Файл: Задание курсовой нормирование точности гладких соединений.docx
ВУЗ: Не указан
Категория: Не указан
Дисциплина: Не указана
Добавлен: 08.02.2024
Просмотров: 26
Скачиваний: 0
ВНИМАНИЕ! Если данный файл нарушает Ваши авторские права, то обязательно сообщите нам.
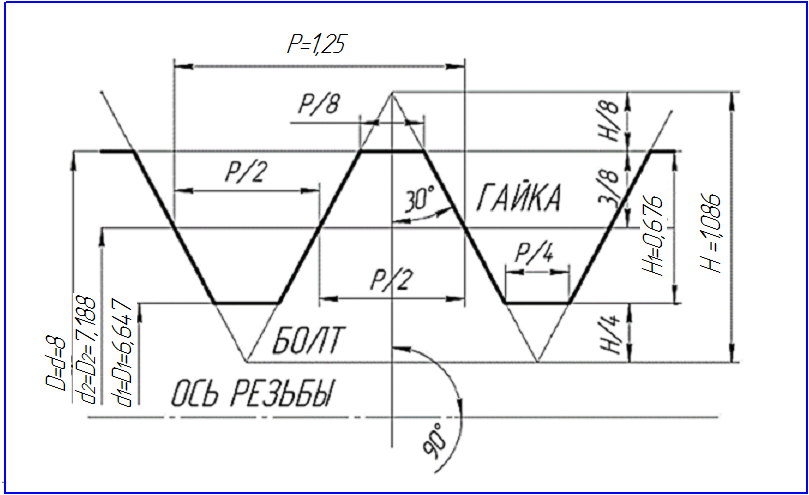
Рис. 3.1 - Профиль резьбы по ГОСТ 9150 – 2002.
2. Посадка с зазором рассчитывается по ГОСТ 16093-2004. «Основные нормы взаимозаменяемости. Резьба метрическая. Допуски. Посадки с зазором».
Резьба имеет нормальную длину свинчивания и средний класс точности, выбираем предпочтительные поля допусков: резьба болта – 6g; резьба гайки –6Н.
Поле допуска для болта (наружная резьба) М8 – 6gопределим по таблице А.1 ГОСТ 16093-2004, поле допуска для гайки (внутренняя резьба) М8 – 6Hопределим по таблице А.2 для номинальных диаметров свыше 5,6 до 11,2 мм.
Таблица 3.3
Значения отклонений и допусков резьбового соединения.
Номинальный размер, мм | Обозначение поля допуска | Величина допуска Т, мкм | ES, мкм | Наибольший предельный размер, мм | EI, мкм | Наименьший предельный размер, мм |
d = 8 | 6g | 212 | -28 | 7,972 | -240 | 7,760 |
d2 = 7,188 | 6g | 118 | -28 | 7,160 | -146 | 7,042 |
d1 = 6,647 | - | - | -28 | 6,619 | - | - |
D = 8 | - | - | - | - | 0 | 8,000 |
D2 = 7,188 | 6H | 160 | +160 | 7,348 | 0 | 7,188 |
D1 = 6,647 | 6H | 265 | +265 | 6,912 | 0 | 6,647 |
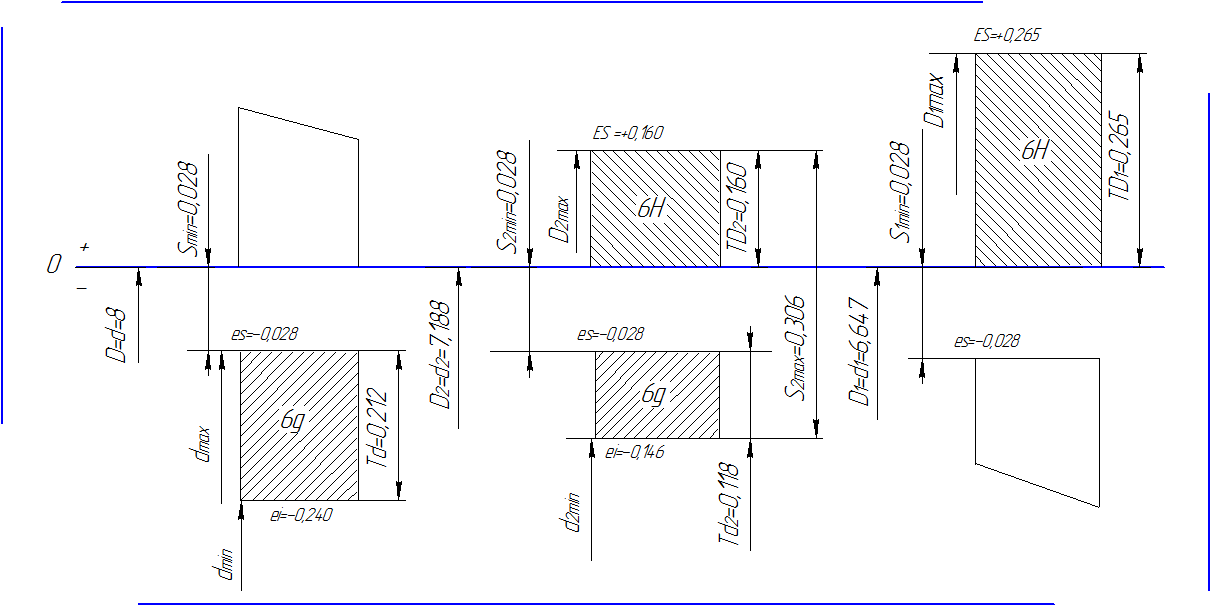
Рис. 3.2 - Расположение полей допусков по профилю резьбы болта и гайки.
3. Расчет приведенного среднего диаметра резьбы болта и заключение о годности резьбы.
Приведенный диаметр: d2пр = d2изм + (fp + fα)
Погрешность наклона боковой стороны половины профиля угла:
∆α/2 = (|∆α/2|пр + |∆α/2|лев)/2 = (|+10| + |-5|)/2 = 7,5 мин
Диаметр компенсация погрешностей половины угла профиля:
fα = 0,36·Р · ∆α/2 = 0,36·1,25·7,5 = 3,375

Диаметральная компенсация погрешностей по шагу:
fp = 1,732·∆Рn = 1,732 ·18 = 31,176

d2пр = 7,12 +(0,003 + 0,031) = 7,154 мм
Условия годности резьбы по среднему диаметру для болта:
Условие прочности: d2изм


Условие свинчиваемости: d2пр


Оба условия выполнено, следовательно, болт годен.
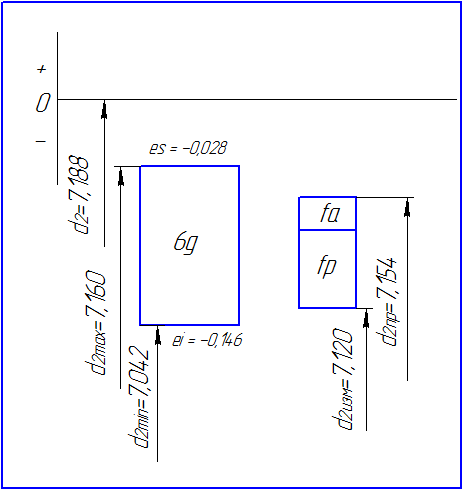
Рис. 3.3. Схема расположения полей допусков по среднему диаметру болта.
3.2. Нормирование точности шпоночных соединений
Таблица 3.4
Карта исходных данных шпоночного соединения
Наименования исходных данных | Значения исходных данных |
Диаметр соединения, d мм | 45 |
Ширина и высота шпонки (ГОСТ 23360), bxh, мм | 14×9 |
Шпонка: | Для передачи крутящего момента |
Тип производства: | серийное |
Количество шпонок в соединении: | одна |
Определение размеров соединения с призматической шпонкой
Найдем размеры шпоночного соединения по ГОСТ 23360-78 [1, табл. 3.1].
d = 45 мм - диаметр вала;
b = 14 мм - ширина шпонки;
h = 9 мм - высота шпонки;
Smin= 0,40 мм - фаска;
S1 max = 0,40 мм - радиус закругления r или фаска;
l = 36…160 мм - интервал длин шпонки;
t1 = 5,5+0.2 мм - глубина шпоночного паза с отклонением на валу;
t2 = 3,8+0.2 мм - глубина шпоночного паза с отклонением во втулке.
Выбор посадок шпонки в пазы вала и втулки
Предельные отклонения шпонки:
− на ширину шпонки b = 14h9(-0,043)
− на высоту шпонки h = 9h11(-0,090)
− на длину шпонки l = 50h14(-0,620)
− на длину паза под шпонку на валу L = 56H15(+1,2)
Посадка шпонки в паз вала производится по системе вала.
Выбор посадок шпонки в пазы вала и втулки зависят от типа производства и назначения шпонки. В данном соединении шпонка не направляющая, служит для передачи крутящего момента, соединение плотное, производство – серийное.
Принимаем по [1, табл. 3.2]:
- паз вала – 14P9

- паз втулки –14P9

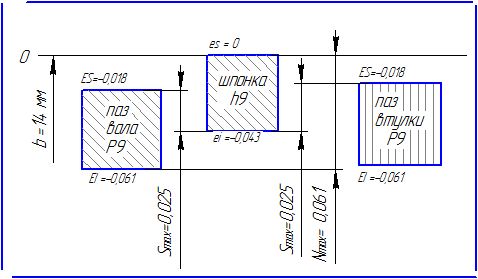
Рис. 3.4 - Схема расположения полей допусков по ширине шпонки.
Предельные зазоры и натяги в соединении:
Шпонка-паз вала, шпонка-паз втулки:
Smax = Bmax – bmin = 13,982 – 13,957 = 0,025 мм
Nmax = bmax – Bmin = 14,000 –13,939 = 0,061 мм
Расчет допусков взаимного расположения шпоночного паза
Допуски параллельности равны 0,5 Т9, а допуски симметричности 2 Т9.
Рассчитываем и округляем до стандартных значений [1, табл. 2.9 и 2.10], указываем на эскизах вала и втулки. Tпарал= 0,5 · 43 = 21,5 мкм; по номинальной длине шпоночного паза, ближайший допуск – 20 мкм. Тсимм = 2·43 = 86 мкм, по номинальному диаметру ближайшим допуском будет 80 мкм. Допуск симметричности зависимый, так как производство серийное
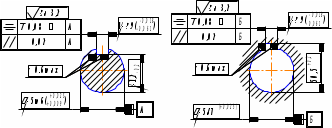
а) б)
Рис. 3.5 - Поперечные сечения: а- вала; б-втулки

а) б)
Рис. 3.6 - Шпоночное соединение:
а – поперечное сечение (1 – втулка; 2 – шпонка; 3 - вал); б – сечение шпонки
3.3 Нормирование точности шлицевых соединений.
Таблица 3.5
Карта исходных данных шлицевого соединения
Наименования исходных данных | Значения исходных данных |
z×d×D , мм | 16×52×60 |
Соединение работает: с реверсом или с вращением в одну сторону | С реверсом |
Соединение вдоль оси: подвижное или неподвижное | подвижное |
Шлицы в отверстии втулки: закалены или не закалены | закалены |
Определить параметры шлицевого соединения
z = 16 - количество шлицев;
d = 52 мм - внутренний диаметр шлицев;
D = 60 мм - наружный диаметр шлицев;
b = 5 мм - ширина шлицев;
c = 0,5+0,3 мм - фаска;
r = 0,5 мм - радиус закруглений.
Шлицевое соединение 16×56×65 относится к тяжелой серии ГОСТ 1139 [1, табл. 3.3].
Выбор вида центрирования, назначение посадок
В зависимости от условий работы механизма (с реверсом) и закалки шлиц выбираем вид центрирования шлицевого соединения и назначаем посадки по ГОСТ 1139-80 [1, табл. 3.4]. Выбираем центрирование по внутреннему диаметру. Назначаем посадки на элементы шлицевого соединения:
- по внутреннему диаметру d:
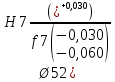
- по внешнему диаметру D:

- по ширине b:

Таким образом, условная комплексная запись шлицевого соединения будет иметь вид:
d – 16 х 52



Строим схемы расположения полей допусков и рассчитываем предельные значения зазоров и натягов.
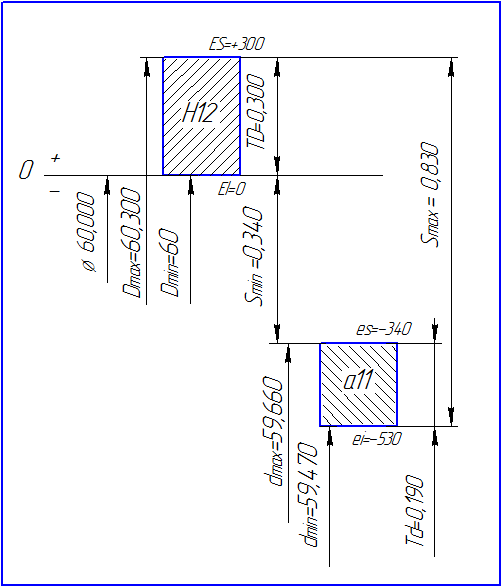
Рис. 3.7 - Схема расположения полей допусков по наружному диаметру D
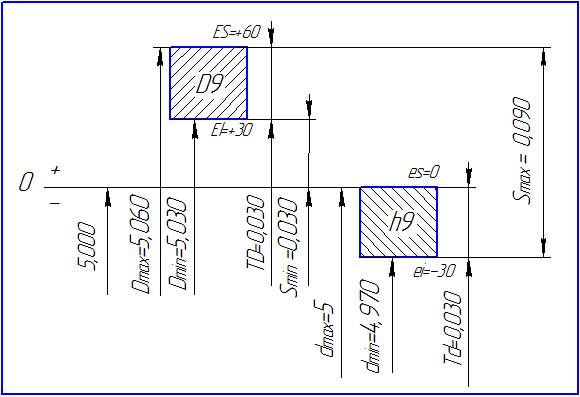
Рис. 3.8 - Схема расположения полей допусков по ширине b
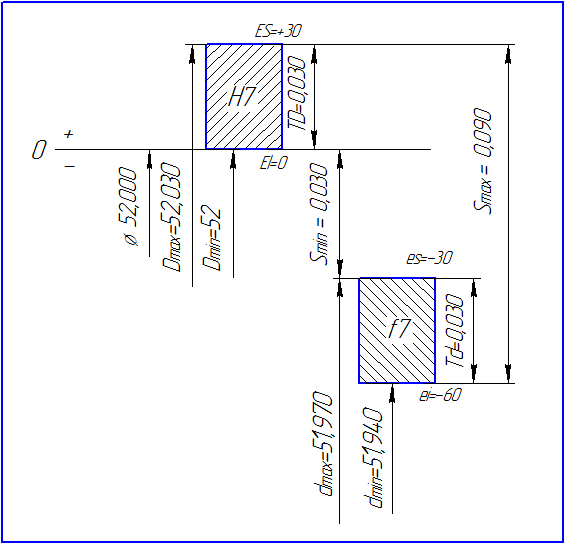
Рис. 3.9 - Схема расположения полей допусков по внутреннему диаметру d
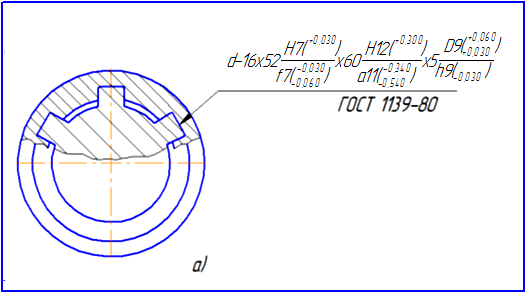
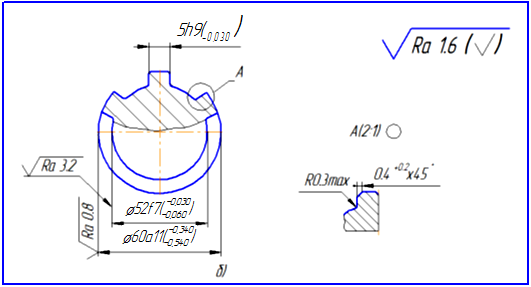
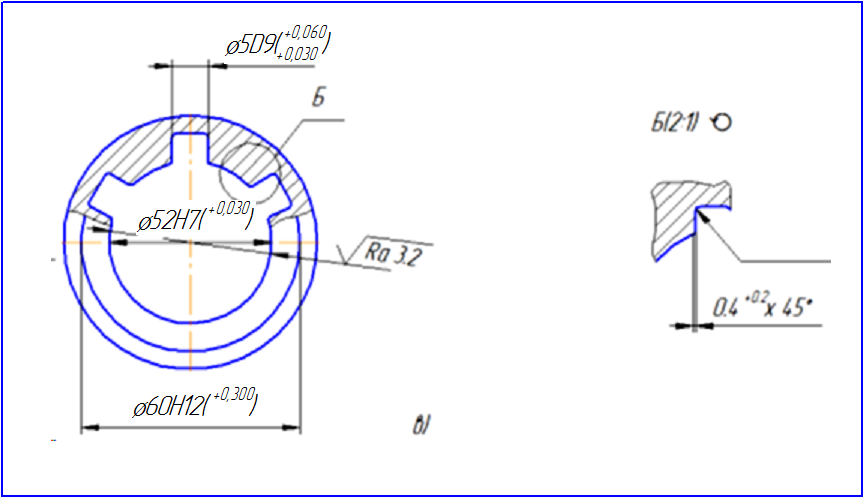
Рис. 3.10 - Поперечное сечение шлицевого соединения:
а - шлицевое соединение в сборке;
б - сечение вала d - 16 x 52f7 x 60a11 x 5h9;
в - сечение втулки d - 16 x 52H7 x 60H12 x 5D9
3.4 Нормирование точности цилиндрических зубчатых передач
Таблица 3.6
Наименования исходных данных | Значения исходных данных |
Вид изделия(автомобиль, пресс, специальный станок) | Шпиндельная группа специального станка |
Номер позиции по чертежу | 2 |
Межосевое расстояние а, мм | 140 |
Модуль зубчатой передачи m, мм | 4 |
Исходный контур | ГОСТ 13755-81 |
Коэффициент смещения исходного контура х | 0 |
Окружная скорость V, м/с | 10 |
Число зубьев z | 35 |
Температура допустимого нагрева зубчатой передачи | t1= +60°C |
Температура допустимого нагрева корпуса | t2= +30°C. |