ВУЗ: Не указан
Категория: Не указан
Дисциплина: Не указана
Добавлен: 09.02.2024
Просмотров: 8
Скачиваний: 0
ВНИМАНИЕ! Если данный файл нарушает Ваши авторские права, то обязательно сообщите нам.
Для стабилизации газового конденсата используются 3 метода:
1. Ступенчатое выветривание (сепарация, дегазация);
2. Ректификация в стабилизационных колоннах;
3. Комбинирование сепарации и ректификации.
1. Технология стабилизации конденсата дегазацией
Стабилизация газового конденсата дегазацией или сепарацией основана на снижении растворимости низкокипящих углеводородов в конденсатах при повышении температуры и понижении давления. Обычно такая технология процесса стабилизации применяется на месторождениях, имеющих низкий конденсатный фактор.
2. Технология стабилизации конденсата ректификацией
Сбор и утилизация газов дегазации конденсата связаны с большими энергетическими затратами, поэтому при больших объемах перерабатываемого конденсата применяют стабилизацию с использованием ректификационных колонн.
Она имеет ряд преимуществ, в частности, энергия нестабильного конденсата рационально используется, полученный стабильный конденсат отличается низким давлением насыщенных паров и др.
Ректификационная стабилизация газового конденсата проводится чаще всего в 2-х или 3-х колоннах, что дает возможность, кроме газов стабилизации и стабильного конденсата, получить пропан-бутановую фракцию (или пропан и бутан).
3. Комбинирование сепарации и ректификации
На современных установках обычно применяют комбинирование процессов сепарации и ректификации, что позволяет повысить технологическую гибкость процесса и уменьшить энергозатраты. стабилизация конденсат дегазация ректификация
Принципиальная схема типовой установки стабилизации конденсата с использованием 2х ректификационных колонн включает дегазацию конденсата в сепараторе, разделение отсепарированной жидкости из сепаратора на 2 потока.
Один из них нагревается в теплообменнике и поступает в питательную секцию абсорбционно-отпарной колонны (АОК); другой в качестве орошения подается на верхнюю тарелку АОК.
Используются сепаратор; теплообменник; АОК;трубчатые печи; стабилизатор; конденсатор-холодильник нестабильный конденсат; стабильный конденсат; газы стабилизации; ШФЛУ;
Технологический режим в АОК следующий: давление 1,9-2,5 МПа; температура вверху 15-20°С, внизу - 170-180°С.
Ректификатом АОК является фракция, состоящая в основном из метана и этана, остатком - деэтанизированный конденсат.
Обычно газ сепарации из сепаратора объединяют с верхним продуктом АОК и после дожатия направляют в магистральный газопровод (МГП).
Деэтанизированный конденсат из АОК направляют в стабилизатор, работающий по схеме полной ректификационной колонны.
С верха стабилизатора отбирают пропан-бутановую фракцию (ПБФ) или широкую фракцию легких углеводородов (ШФЛУ) , а из куба колонны отводят стабильный конденсат .Давление в стабилизаторе составляет 1,0-1,6 МПа.
Для подвода тепла в кубы колонн используют трубчатые печи.
На усовершенствованных установках стабилизации конденсата для повышения технологической гибкости и возможности переработки облегченного по фракционному составу конденсата из-за истощения месторождения газ сепарации из сепаратора 1 нагревают и подают в куб АОК как отдувочный газ.
Использование газа сепарации в качестве отдувочного позволяет в нижней части АОК снизить парциальное давление компонентов С3+, вследствие чего снижаются необходимое паровое число и количество тепла, подводимого в трубчатой печи.
Схема установки стабилизации конденсата с подачей отдувочного газа включает сепаратор; рекуперативные теплообменники; АОК; трубчатые печи; стабилизатор; конденсатор-холодильник
Во время стабилизации конденсата с с подачей отдувочного газа согласно техпроцесса происходит преобразование: сырой конденсат- стабильный конденсат- газы стабилизации- ШФЛУ.
26. Назовите преимущества и недостатки стабилизации газовых конденсатов в ректификационных колоннах перед другими способами стабилизации?
Основные преимущества схем дегазации - это простота технологии, низкие металло- и энергоемкость процесса.
Основной недостаток - это нечеткое разделение углеводородов, одни из которых являются целевыми для газов стабилизации, а другие - для стабильного газового конденсата.
При ступенчатой дегазации газа давление на последующей ступени всегда меньше давления на предыдущей.
27. Дайте определения понятию «синтез-газ», и опишите основные методы его получения?
Синтез-газ (водяной газ, генераторный газ) — преимущественно смесь монооксида углерода и водорода. В промышленности получают паровой конверсией метана, парциальным окислением метана, плазменной газификацией отходов и сырья, газификацией угля. Соотношение компонентов зависит также от метода и условий газификации углей.
В промышленности получают паровой конверсией метана, парциальным окислением метана, плазменной газификацией отходов и сырья, газификацией угля. В зависимости от способа получения соотношение CO:Н
2 варьируется от 1:1 до 1:3.
28. Получение синтез-газа паровой конверсии метана.
Соотношение компонентов в синтез-газе колеблется в широком диапазоне, поскольку зависит как от применяемого сырья, так и от вида конверсии — водяным паром или кислородом:
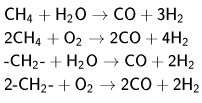
29. Получение синтез-газа парциальным окислением метана.
Основная реакция:
СН4 + ½ О2 ↔ 2Н2 + СО
Побочная реакция:
СО + 1/2О2 ↔ СО2
Побочная реакция:
Н2 + 1/2О2 ↔ Н2О
Условия: катализатор, 1200-1500 0С, 3-4 МПа, недостаток О2, соотношения Н2/СО = 2.
30. Получение синтез-газа углекислотной конверсией метана.
Основная реакция:
СО2 + СН4 ↔ 2Н2 + 2СО2
Отношение Н2/СО в полученном ситез-газе равно 1.
31. Получение синтез-газа газификацией угля.
Процесс основан на взаимодействии угля с водяным паром:
С + Н2О ↔ Н2 + СО
32. Опишите процесс получения жидких углеводородов синтезом Фишера-Тропша.
Первая стадия процесса Фишера—Тропша состояла в получении синтез-газа из твёрдых углеводородов (обычно каменного угля):

Для этого сквозь слой раскалённого каменного угля продували перегретый водяной пар. Продуктом являлся так называемый водяной газ — смесь монооксида углерода (угарного газа) и водорода. Далее процесс Фишера—Тропша описывается следующим химическим уравнением:
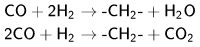
Смесь монооксида углерода и водорода называется синтез-газ, или сингаз, а также применяется термин «водяной газ».
Смесь получаемых углеводородов очищают для получения целевого продукта — синтетического бензина. Получение более тяжёлых видов топлива методом Фишера—Тропша экономически невыгодно из-за быстрого отравления катализатора.
Углекислый газ и монооксид углерода образуются при частичном окислении угля и древесного топлива. Польза от этого процесса преимущественно в его роли в производстве жидких углеводородов или водорода из твёрдого сырья, такого как уголь или твёрдые углеродсодержащие отходы различных видов.
Неокислительный пиролиз твёрдого органического сырья производит сингаз, который может быть напрямую использован в качестве топлива, без преобразования по процессу Фишера—Тропша.
Если требуется жидкое вещество, похожее на нефтяное топливо, смазочные масла или парафин, может быть применён процесс Фишера—Тропша. Если требуется увеличить выход водорода, то водяной пар берут с избытком, что сдвигает равновесие реакции, в результате чего образуются только углекислый газ и водород.
Таким образом получают жидкое топливо из смеси газов.
33. В чем суть технологий GTL и CTL?
GTL (англ. Gas-to-liquids — газ в жидкость) (рус. Газожидкостная конверсия. ГЖК)— процесс преобразования природного газа в высококачественные, не содержащие серу моторные топлива и, при необходимости, другие, более тяжёлые, углеводородные продукты. Упреждающее развитие подобных технологий поможет с меньшими потерями преодолеть снижение добычи невозобновляемой традиционной нефти (так называемый пик нефти).
CTL (англ. Coal to Liquids), ожижение угля — технология получения жидкого топлива из угольного сырья. Позволяет использовать традиционные потребители бензина (например, автотранспорт) в условиях нехватки нефти.
34. Опишите процесс синтеза метанола из синтез-газа.
Реакция синтеза метанола из синтез–газа представляет гетерогенно каталитическую обратимую экзотермическую реакцию, протекающую по уравнению:

35. Назовите основные пути синтеза метанола из метана, минуя синтез-газ.
Процесс проводят при давлениях до 10 МПа и температурах 400-500°С в трубчатых реакторах при относительно низких начальных концентрациях кислорода с последующим охлаждением газожидкостной смеси и отделением жидких продуктов, из которых ректификацией выделяют метанол.
36. Перечислите и охарактеризуйте основные направления использования метанола.
Существуют три основных направления использования метилового спирта: Также из метанола производят: пентаэритрит, необходимое сырье для изготовления пенопласта, лаков, смазочных масел.
37. Получение формальдегида из метанола.
Получение формальдегида предусмотрено методом парофазного окисления – дегидрирования метанола кислородом воздуха на пемзосеребрянном катализаторе, в мягких температурных условиях (550 – 600) 0С, либо жестком режиме (660 – 700) 0С с поглощением формальдегида водой и последующим выделением непрореагировавшего метанола вакуум – ректификацией. Выделенный метанол возвращается в процесс. Процесс ведется при давлении 0,76 атм.
Основная реакция процесса:
2СН3ОН + О2 → 2НСОН + 2Н2О
38. Получение диметилового эфира из метанола.
Процесс протекает при 1700С и в присутствии серной кислоты.
2СН3ОН = С2Н6О + Н2О
39. Охарактеризуйте процесс пиролиза углеводородов.
Пиролиз углеводородного сырья - это термическое разложение органических природных соединений при недостатке воздуха.
Под действием высоких температур (650-900°С) нефтяное и газовое сырье термически разлагают для получения главным образом непредельных (этилена, пропилена) и ароматических углеводородов.
40. Приведите первичные и вторичные реакции, протекающие при пиролизе углеводородов.
Основная первичная реакция – разложение исходного углеводорода с образованием водорода, низших алканов, этилена, пропилена и других олефинов. К вторичным – нежелательным реакциям относятся: дальнейшее разложение образовавшихся олефинов; гидрирование и дегидрирование олефинов с образованием парафинов, диенов, ацетилена и его производных; конденсация отдельных молекул с образованием более высокомолекулярных углеводородов, а также более стабильных структур (ароматических углеводородов, циклодиенов и др.).
41. Приведите основные технологические параметры процесса пиролиза и их взаимосвязь с составом и выходом продуктов пиролиза.
К числу основных параметров, в наибольшей степени влияющих на процесс пиролиза, относятся температура, время пребывания сырья в реакторе и парциальное давление взаимодействующих углеводородов. Применяемые в промышленной практике величины этих важнейших параметров устанавливаются в соответствии с известными зависимостями термодинамики и кинетики реакций углеводородов при пиролизе.
Важнейший параметр процесса – температура – определяет степень превращения исходных веществ по реакциям, протекающим при пиролизе. Температура процесса – фактор, определяющий как степень разложения исходного вещества (степень превращения), так и распределение продуктов пиролиза. С увеличением температуры в результате первичных реакций повышаются выходы низших олефинов, метана и водорода и снижается выход алканов.
42. Каковы функции водяного пара, используемого при пиролизе углеводородов?
Водяной пар играет тройную функцию:
- снижает парциальное давление углеводородов, увеличивая выход целевых продуктов;
- препятствует образованию и отложению кокса и сажи на стенках оборудования;
- обеспечивает высокую скорость движения паро-сырьевой смеси в печи.