Файл: Контрольная работа по дисциплине Специальные методы соединения материалов Технология и оборудование сварки взрывом. Область применения.docx
ВУЗ: Не указан
Категория: Не указан
Дисциплина: Не указана
Добавлен: 16.10.2024
Просмотров: 17
Скачиваний: 0
ВНИМАНИЕ! Если данный файл нарушает Ваши авторские права, то обязательно сообщите нам.
Взрывные технологии широко используют для закрепления труб в трубных дисках различного теплообменного оборудования тепловых и атомных электростанций, химического и нефтеперерабатывающего оборудования (рис. 8 в).
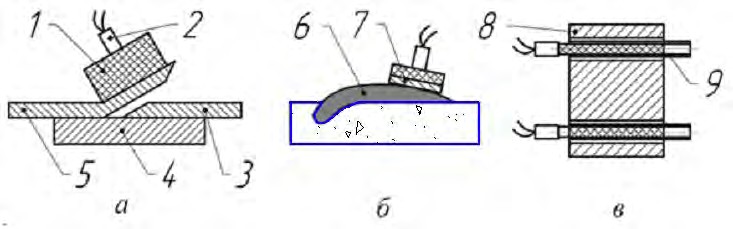
Рисунок 8 — Схемы конструкционной сварки: а – соединение в стык; б – плакирование криволинейных поверхностей; в – соединения труб и трубных дисков; 1 – заряд ВВ; 2 – детонатор; 3, 5 – листовые заготовки; 4 – подложка; 6 – лопасть гидротурбины; 7 – плакирующая заготовка; 8 – трубная плита; 9 – трубные заготовки
Преимущества и недостатки
У любого метода обработки есть положительные и отрицательные моменты. Сварка взрывом не исключение. К достоинствам относят:
-
Стремительность процесса. Стоит вспомнить, что соединение заготовок происходит за какие-то доли секунды. Именно скорость обработки часто становится основным фактором при выборе сварки взрывом. -
Сплавление разнородных металлов. Другие способы сварки исключают возможность качественной сварки материалов с разными физико-химическими характеристиками. -
Плакирование. Данным термином называют придание определенных свойств путем покрытия верхнего слоя слоем другого металла. -
Экономичность. Цельные детали успешно заменяют плакированными, что существенно снижает затраты на заготовки. -
Дешевизна. Технология сварки взрывом включает в себя затраты только на взрывчатое вещество и детонатор. Другого оборудования не требуется. -
Универсальность. Создание изделий сложной формы, заготовок для ковки и штамповки, деталей со множеством изгибов.
Помимо положительных моментов существуют и отрицательные. Среди основных недостатков стоит отметить:
-
низкий уровень управляемости процессом, мощную взрывную волну сложно контролировать; -
необходимость соответствующей квалификации для допуска к работе; -
взрывать можно только в специальных защитных камерах или на оборудованных полигонах; -
длительная подготовка, для расчета типа взрывчатого вещества и его закладки требуется много времени; -
низкая автоматизация, сильная зависимость от человеческого фактора, увы, автоматизировать такую сварку пока не смогли.
Несмотря на преобладание положительных моментов, пренебрегать техникой безопасности нежелательно.
Техника безопасности
При работе со взрывчатыми веществами необходимо тщательно соблюдать технику безопасности, ориентируясь в основном, на меры противопожарной безопасности. Тем не менее риск вредного воздействия на работников и на окружающих очень велик, не стоит забывать о низком проценте управляемости взрывной волны. По этим (и не только) причинам рекомендуется придерживаться следующих ограничений:
-
На полигоне. Это масштабный кусок земли для подобных опасных испытаний. Оборудовать полигон для сварки взрывом обязательно вдали от жилого массива. -
На площадке. Сам процесс должен осуществляться на предварительно подготовленной рабочей площадке, углубленное место с песчаной «подушкой». Чем толще «подушка», тем сильнее она гасит взрывную волну, но предел толщины 1 метр. -
В защитных камерах. На производстве чаще всего встречается небольшой заряд 15-20 кг. Для взрыва используют отдельном пустое помещение со стенами из бетона или кирпича, толщиной 25 см и более. Целостность оболочки камеры не должна быть нарушена или деформирована. -
Индивидуальная защита. Применение средств индивидуальной защиты просто неотъемлемая часть техники безопасности при сварке.
Соблюдение обозначенных рекомендаций снизит вероятность возникновения нестандартных ситуаций во время процесса, который имеет, в свою очередь, некоторые особенности.
Особенности
Процесс сварки взрывом включает в себя два этапа: кропотливую подготовку и молниеносную сварку. Рассмотрим подробнее каждый этап.
Повысить качество сварного соединения и обеспечить его прочность поможет предварительная обработка деталей. Для правильной подготовки необходимо:
-
Выпрямить поверхность свариваемых изделий, максимальная кривизна должна быть 2 мм/м². -
Обезжирить места соединения, удалить с них оксидную пленку, протереть от окалины и прочих примесей. -
Достичь необходимой шероховатости. Для этого иногда допустимо использование абразивных материалов.
После подготовительных манипуляций взрывчатое вещество аккуратно и равномерно распределяют по поверхности, в зависимости от способа сварки.
По всем параметрам подготовительный этап занимает намного больше времени, чем сам процесс. Да, все происходит за несколько микросекунд: ударная волна серьезной мощности с силой ударяет движимый слой о неподвижный, формируя сварное соединение.
Собираясь проводить сварку взрывом стоит помнить, что воздействие взрывной волны на некоторые металлы ухудшает и разрушает их структуру. Вследствие этого в самом слабом по прочности месте сварного соединения возникает диффузия, которая негативно сказывается на результате.
Контроль качества швов
Для контроля сварных соединений, полученных путем сварки взрывом, проверяются три параметра:
-
Плотность шва проверяют ультразвуковым методом. Для важных швов применяют проверку рентгеноскопией. -
Прочность выявляют при помощи срез части шва или его разрыва. -
Пластичность исследуют путем различных изгибов, прогибов и кручений сварного соединения.
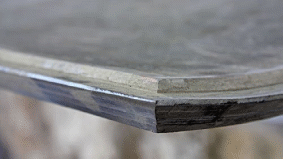
Рисунок 9 – Сварной шов, образовавшийся в результате операции.
При возникновении сомнений в ровности результата, полученное изделие проверяют на деформацию. Для этого понадобится любой измерительный прибор, например линейка.
Новые технологии обработки металлов завоевывают позиции, но остаются не полностью рассмотренными. Поэтому, несмотря на кажущуюся простоту процесса, необходимо предварительно изучить все нюансы и особенности техники безопасности.
Подготовка к работе
Способы сварки взрывом.
Для проведения работ потребуется:
-
опорный фундамент для закрепления неподвижной детали; -
детали, которые требуют сварки; -
взрывчатое вещество; -
детонатор; -
соблюдение определенного расстояния относительно свариваемых деталей; -
соблюдение определенного угла установки относительно свариваемых деталей.
-
прокладка для установки между деталями; -
органический растворитель; -
шлифующий элемент.
Массивные детали (прокатные листы, металлические основания композитов) располагают на уплотненном гравии или песке без дополнительной фиксации, а небольшие детали, требующие высокой точности соединения, закрепляются на толстом бетонном или металлическом основании специальными монтажными болтами. Болты вставляются в наружные ушки детали, которые отрезаются после завершения процесса сварки.
Прокладка между плоскими деталями, которые нужно сварить, поддерживает между ними расстояние в 2-8 мм, необходимое для разгона плакирующей детали. Прокладка изготавливается из обеззоленного картона или углеродного клатрата (для высокоточной сварки) – данные материалы сгорают в момент сваривания с выделением углекислого газа практически без образования копоти и золы, которые могут уменьшить прочность соединения.
В зависимости от требуемой задачи, отличается и процесс подготовки к нему. Это может быть сварка:
-
крупногабаритных деталей; -
многослойных соединений и волокнистых армированных материалов; -
цилиндрических деталей.
Относительно требуемых целей отличается технологический процесс, прочность и некоторые физические характеристики полученных соединений. Но для использования какого-либо процесса нужно изучать конкретный способ и его особенности более детально.
Основной принцип одинаков для любого из перечисленных воздействий – отличаются только величины, используемые в процессе.
Зафиксированную деталь устанавливают на массивную плиту. После подрыва плита всегда разрушается. Металлическая плита выносит несколько подрывов, но все равно ее приходится восстанавливать после каждого применения.
Наиболее рациональны опоры из легко восстанавливаемых материалов, таковыми себя хорошо зарекомендовал песок и дробь.
Ударяемую деталь устанавливают под углом от 3 до 10 градусов к закрепленной детали и с определенным зазором, составляющим от 2 до 10 миллиметров. На поверхность ускоряемой детали равномерно укладывается взрывчатое вещество.
Важно, чтобы взрывчатое вещество нанесено было именно равномерно по всей поверхности детали, чтобы избежать возможных изгибов или смещений.
Использовать в качестве взрывчатого вещества можно гексоген, аммонал, тол, ил другие доступные вещества.
Устанавливаем детонатор. Очень важно правильно установить и использовать детонирующие вещества. Для более точной установки заряда используются специальные контейнеры для взрывчатых веществ. Чаще всего они изготавливаются из плотного картона. Выглядит контейнер как открытая сверху коробка с дном, в котором делают отверстие для плотного прилегания к необходимой детали.
Для получения желаемого результата требуется максимально эффективно инициировать заряд. К главному заряду, которому придаются формы изделия, прикрепляется детонирующий. В зависимости от необходимых объемов работ изменяется форма и размеры вспомогательного взрывателя.
После активации взрывчатого вещества образующаяся взрывная волна растекается со скоростью от 2000 до 8000 метров в секунду. Темпы распространения зависят от химического состава и физического состояния используемого материала.
Взрывная волна воздействует на изделие
, расположенное под зарядом, и передает ему львиную долю своей энергии и тем самым ускоряет его до необходимой скорости. Высокоскоростное приближение движущейся детали к неподвижной развивает в месте контакта сильное давление. Под его воздействием происходит неравномерное сжатие с наиболее подходящими условиями для процесса сварки.
Возможные трудности
-
Взрывная волна может стать причиной разброса осколков железобетонной «подушки». -
Качественное соединение возможно при соблюдении технологии. -
Заряд должен обеспечить необходимую скорость деформации, чтобы не произошли диффузные изменения в области шва. -
Одна из поверхностей должна быть плотно закреплена. При одновременном движении деталей прочность соединения значительно снижается. -
При работе на установках необходимо контролировать скорость метания разрядов. -
Нет математической модели процесса, поэтому все расчеты приблизительны. Сам процесс – экспериментальный.
Список литературы
-
Беляев В. И., Ковалевский В. И., Смирнов Г. В., Чекан В. А. Высокоскоростная деформация металлов. — Минск: Наука и техника, 1976. — 224 с. -
Захаренко И. Д. Сварка металлов взрывом. — Минск: Наука и техника, 1990. — 206 с. -
Конон Ю. А., Первухин Л. Б., Чудновский А. Д. Сварка взрывом / Под ред. В. М. Кудинова. — М.: Машиностроение, 1987. — 216 с. -
Карпентер С. Сварка металлов взрывом. — Минск: Беларусь, 1976. — 43 с. -
Кривенцов А. Н. Проектирование и изготовление сваркой взрывом ВКМ. — Волгоград: Изд. РПК «Политехник», 2005. — 184 с. -
Крупин А. В., Соловьев В. Я., Попов Г. С. Обработка металлов взрывом. — М.: Металлургия, 1991. — 495 с. -
Кудинов В. М., Коротеев А. Я. Сварка взрывом в металлургии. — М.: Металлургия, 1978. — 168 с. -
Лысак В. И., Кузьмин С. В. Сварка взрывом. — М.: Машиностроение-1, 2005. — 544 с