Файл: Сырьевая база и подготовка материалов к металлургическому переделу.doc
ВУЗ: Не указан
Категория: Не указан
Дисциплина: Не указана
Добавлен: 17.03.2024
Просмотров: 372
Скачиваний: 0
СОДЕРЖАНИЕ
3.1 Разжижители и шлакообразующие материалы.................................93
4.1 Цель и методы подготовки шихты.....................................................99
6.2 Обезвоживание концентратов.........................................................156
6.3 Обжиг железных руд........................................................................157
8.2 Производство кокса...........................................................................174
8.10 Качество металлургического кокса................................................202
3.1 Разжижители и шлакообразующие материалы
Шлакообразующие смеси и брикеты
4.1 Цель и методы подготовки шихты
Таблица 6.1 – Сравнительные характеристики различных сепараторов
6.2 Обезвоживание концентратов
ПОНЯТИЯ ОДНОРОДНОСТИ И УСРЕДНЕННОСТИ
Рисунок 7.1 – Усреднительный склад
Рисунок 7.2 – Устройство саморазгружающейся тележки
Таблица 8.2 – Структура запасов углей Донбасса
Таблица 8.8 – Коксуемость углей Донецкого бассейна
Рисунок 8.4 – Схема процесса коксования шихты в камере коксовой печи
Рисунок 8.5 – Поперечный разрез коксовой батареи
8.10 Качество металлургического кокса
Рисунок 8.7 – Барабаны для механического испытания кокса
Таблица 8.11 – Ситовый состав некоторых коксов
В сложившейся ситуации наиболее целесообразным является следующее: четко разграничить понятия однородности и усредненности, а в качестве общепринятой и единой методики определения количественной оценки этих характеристик принять как наиболее разумную и научно обоснованную методику, автором которой является Русаков П.Г., разработавший теорию процессов усреднения и закономерностей формирования колебаний состава материалов.
Суть ее сводится к следующему. Однородность материала определяется дисперсией состава материала на уровне элементарных порций от куска к куску и не зависит от взаимного расположения кусков, то есть не меняется в ходе усреднения. Понятие элементарной порции отождествляется с порцией, сохраняющейся при перемешивании как единое целое, не разрушающейся на более мелкие порции и не подвергающейся вторжению постороннего материала. Для кусковатых материалов (железная руда, агломерат, окатыши) такой порцией является кусок средних размеров, для мелкозернистых материалов (концентрат, пыле-угольное топливо) – отдельное зерно. Для удобства понятие КУСОК используют как синоним понятия элементарная порция, вне зависимости от действительной крупности материала.
Усредненность материала – синоним перемешанности, перетасованности, хаотичности взаимного расположения его кусков. Чем беспорядочнее относительно друг друга располагаются куски разного состава, тем выше усредненность материала. Усредненность не зависит от того, велика или мала разница состава куска материала, то есть не зависит от однородности материала.
Количественной характеристикой усредненности является автокорреляционная функция (АКФ) колебаний состава материала: чем хаотичнее расположены куски в массиве, тем слабее корреляция их состава и тем меньше АКФ, а чем меньше размеры скоплений близких по составу кусков, тем меньше интервалы (протяженность) корреляции.
Дисперсия (и среднеквадратичное отклонение – СКО) разовых анализов материала определяется тремя факторами: однородностью материала (СКО от куска к куску), его усредненностью (АКФ) и технологией опробования (величина опробуемых массивов, число частных проб в каждой разовой пробе и массе проб). Чем выше усредненность материала, тем сильнее влияние технологии опробования. Поэтому без указания технологии опробования материала численные значения СКО его анализов лишены определенности, а их сопоставление – содержательности.
Подводя итог вышеизложенным рассуждениям, необходимо во избежание дальнейших разночтений и для обеспечения сравнимости результатов отдельных определений неоднородности смеси различных по своим химическим и физическим свойствам материалов, способов и закономерностей процессов их смешивания и усреднения, во всех случаях руководствоваться следующими принципами:
-
Четко разграничить понятия однородности и усредненности смеси.
-
Неоднородность смеси однозначно определяется дисперсией ее состава на уровне элементарных порций от куска к куску и зависит от исходной неоднородности смешиваемых материалов и расхода этих материалов при объединении в смесь:
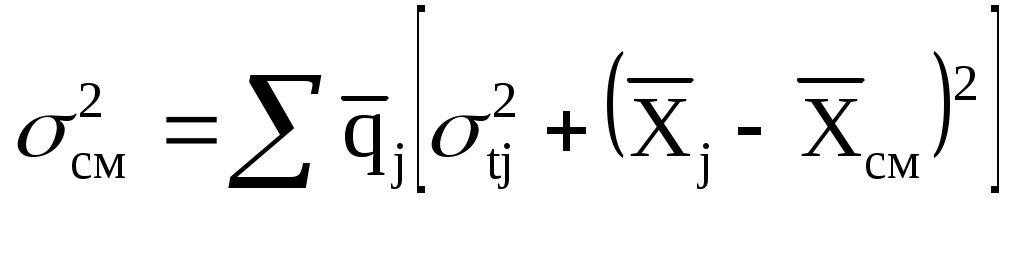
где N – дисперсия состава от куска к куску смеси и входящих в нее j-х материалов;
Хсм, Хj – среднее содержание контролируемого компонента в смеси и в j-ом материале;
qj – относительная доля j-го материала в смеси.
3. В процессе перемешивания (усреднения) неоднородность смеси не изменяется, равно, как не меняется и величина дисперсии ее состава от куска к куску.
Неоднородность может меняться в случае, если по ходу смешивания происходит дополнительное дробление или истирание материалов (например, при перегрузках), либо если меняется соотношение компонентов смеси (например, варьирование расхода материала при дозированной их подаче в поток смеси).
-
Усредненность смеси (тщательность, степень ее перемешанности) исчерпывающим образом характеризуется автокорреляционной функцией (АКФ) колебаний состава: она позволяет не только количественно оценить степень перемешанности (упорядоченности взаимного расположения кусков), но и проследить закономерности изменения колеблемости состава смеси в процессе усреднения. -
Дисперсия состава смеси при усреднении по результатам опробования зависит от исходной неоднородности и от усредненности
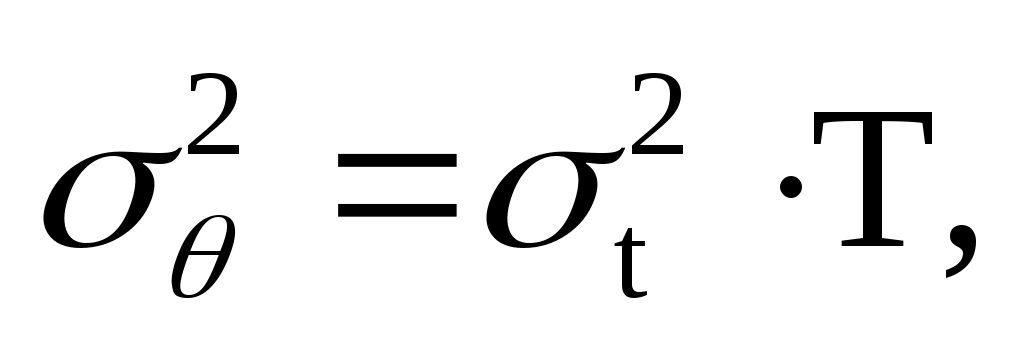
где
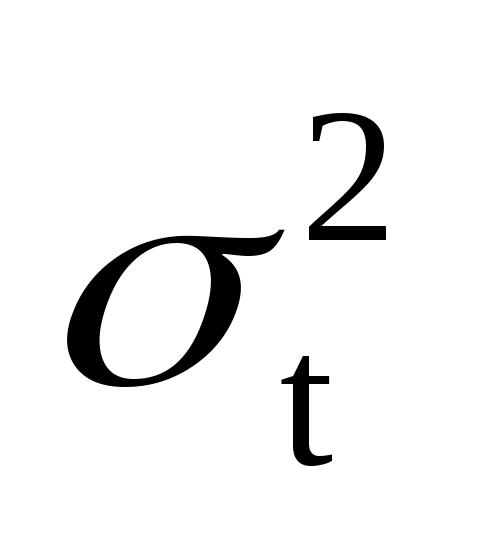
Т – обобщенная характеристика усредненности, которая определяется видом и величиной АКФ.
В плохо усредненном материале параметр Т близок к единице, и дисперсия смеси
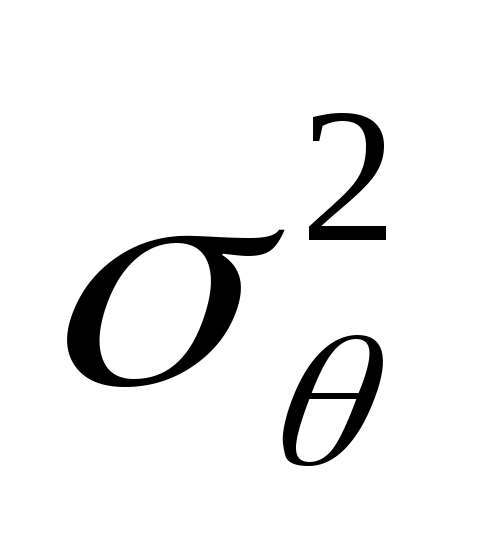
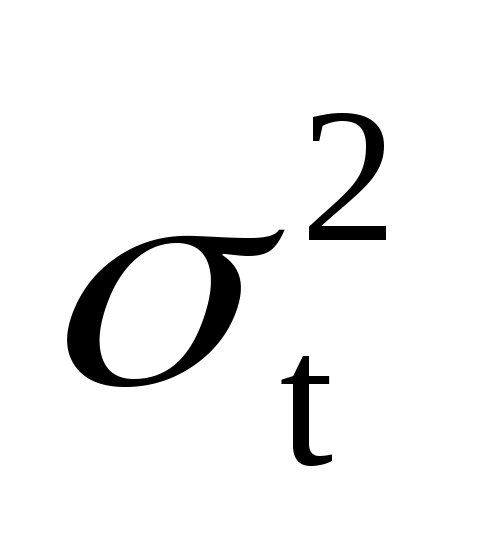
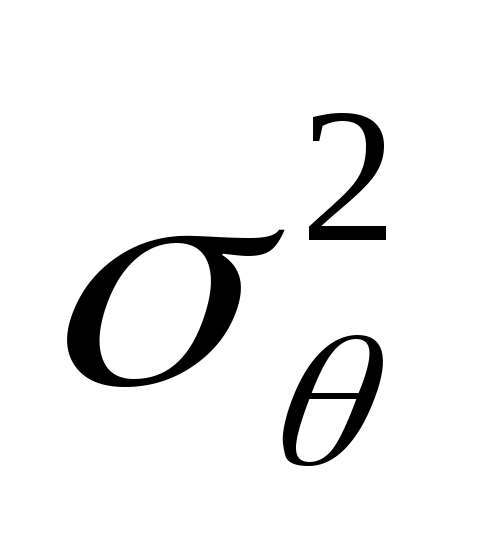
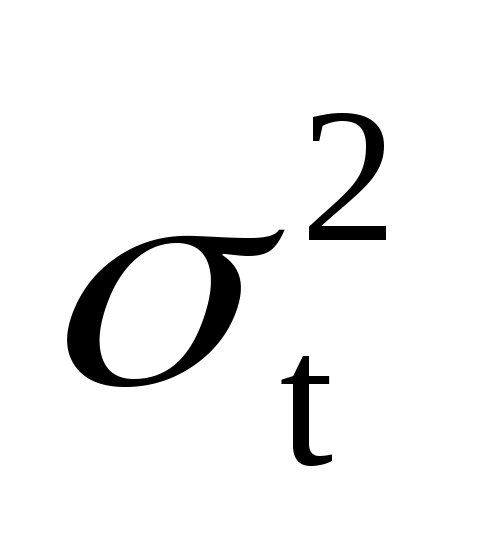
Практически усреднение производят следующим образом. Штабель формируют из большого числа (до 1000) тонких горизонтальных слоев материала (рис. 7.1)
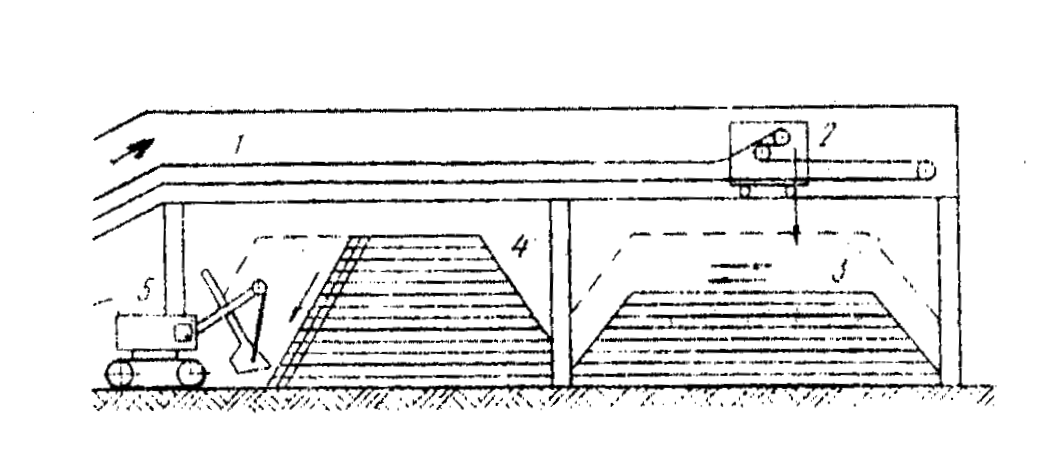
1- подающий конвейер; 2 – саморазгружающаяся тележка; 3 – формируемый штабель; 4 – штабель под разгрузкой; 5 – экскаватор
Рисунок 7.1 – Усреднительный склад
При этом предполагается, что состав каждого отдельного слоя по длине штабеля остается постоянным. Забор материала производят с торца штабеля, одновременно захватывая все слои по высоте. В результате химический состав каждого объема забранного материала практически одинаков.
Процесс усреднения стараются производить на всех этапах переработки руды начиная от карьера и кончая бункерами доменного цеха.
Наилучшие результаты получаются при усреднении на специальных складах, сооружаемых обычно на обогатительных фабриках или фабриках окускования. Для загрузки-формирования штабелей почти повсеместно применяют саморазгружающиеся тележки (рис. 7.2).
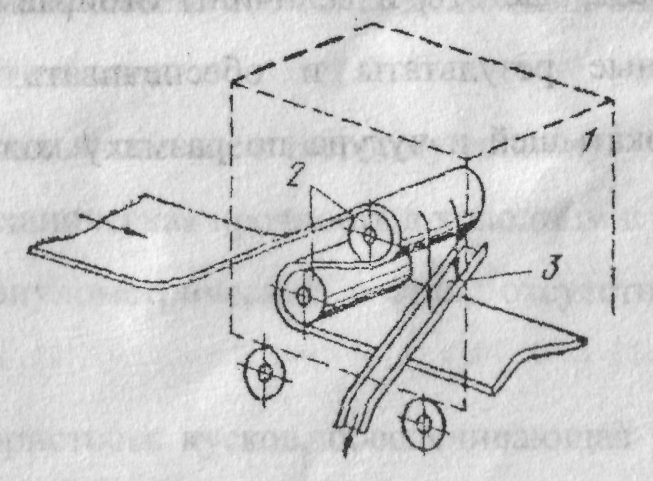
Рисунок 7.2 – Устройство саморазгружающейся тележки
Такая тележка представляет собой раму 1 на четырех роликах, на которой установлены два свободно вращающихся барабана 2. Лента конвейера, огибая эти барабаны, делает петлю. Между барабанами укреплен один или два наклонных лотка 3. Материал, движущийся по конвейеру, падая с верхнего барабана, по наклонному лотку ссыпается вниз. Такая конструкция тележки позволяет ей перемещаться вдоль работающего конвейера, разгружая с него материал в любом нужном месте. Как правило, саморазгружающиеся тележки работают в челночном автоматическом режиме, реверс производится от конечных выключателей.
Забор материала из штабеля осуществляют различными устройствами и способами. На рисунке 7.1 представлен усреднительный склад, где забор материала производится экскаватором. Экскаватор забирает руду только с низу штабеля. Смешивание происходит в момент ссыпания материала по торцевой поверхности штабеля.
Для осуществления хорошего усреднения на каждом складе должно быть два штабеля одного и того же материала, один из которых формируется, а другой вырабатывается. Чем больше емкость склада, тем лучше результаты по усреднению можно получить. Однако площадь больших складов значительна и для их сооружения требуются значительные капитальные затраты. Вполне удовлетворительные результаты усреднения получаются на складах емкостью 70-100 тыс. т.
К сожалению на горнообогатительных фабриках и металлургических комбинатах Украины нет ни одного усреднительного склада, который бы отвечал современным требованиям к усреднению материалов. Складирование и усреднение материалов происходит на рудных дворах, оборудованных вагоноопрокидывателями и рудногрейферными перегружателями, которые не приспособлены и не предназначены производить усреднение материалов.
Однако глубокое теоретическое изучение вопросов усреднения на рудных дворах, бункерах аглофабрик и горнообогатительных комбинатов, изучение влияния режима возврата, частоты и величины отбираемых проб позволяют получать положительные результаты и обеспечивать удовлетворительное качество агломерата, окатышей и чугуна по размаху колебаний химического состава.
8 ТОПЛИВО
В черной металлургии в качестве теплоносителей и восстановителей применяются различные виды топлива: твердое (кокс), жидкое (мазут), газообразное (природный, коксовый, доменный и др. газы).
8.1 Твердое топливо
Твердое топливо применяется в основном в доменном производстве, как теплоноситель – для достижения высоких температур (до 2100оС), восстановитель и разрыхлитель столба шихты материалов для обеспечения высокой ее газопроницаемости.
В современных доменных печах на выплавку 1 т чугуна затрачивается 400-600 кг кокса, то есть приблизительно половина массы конечного продукта плавки. Стоимость кокса составляет 40-60 % себестоимости чугуна, то есть около половины всех затрат на материалы. Поэтому даже незначительное снижение расхода кокса или замена его более дешевыми видами топлива являются экономически эффективными.
Требования, предъявляемые к твердому топливу:
-
Высокая механическая прочность в холодном и разогретом состоянии. -
Ровный гранулометрический состав, отсутствие мелких пылеватых фракций. -
Высокая пористость кусков, обеспечивающая интенсивное горение в горне доменной печи. -
Высокая теплотворная способность. -
Низкое содержание вредных примесей. -
Низкое содержание золы, которая, переходя в шлак, увеличивает его количество и расход топлива на его нагрев. -
Низкое содержание летучих веществ. -
Невысокая стоимость.