Файл: Сырьевая база и подготовка материалов к металлургическому переделу.doc
ВУЗ: Не указан
Категория: Не указан
Дисциплина: Не указана
Добавлен: 17.03.2024
Просмотров: 353
Скачиваний: 0
СОДЕРЖАНИЕ
3.1 Разжижители и шлакообразующие материалы.................................93
4.1 Цель и методы подготовки шихты.....................................................99
6.2 Обезвоживание концентратов.........................................................156
6.3 Обжиг железных руд........................................................................157
8.2 Производство кокса...........................................................................174
8.10 Качество металлургического кокса................................................202
3.1 Разжижители и шлакообразующие материалы
Шлакообразующие смеси и брикеты
4.1 Цель и методы подготовки шихты
Таблица 6.1 – Сравнительные характеристики различных сепараторов
6.2 Обезвоживание концентратов
ПОНЯТИЯ ОДНОРОДНОСТИ И УСРЕДНЕННОСТИ
Рисунок 7.1 – Усреднительный склад
Рисунок 7.2 – Устройство саморазгружающейся тележки
Таблица 8.2 – Структура запасов углей Донбасса
Таблица 8.8 – Коксуемость углей Донецкого бассейна
Рисунок 8.4 – Схема процесса коксования шихты в камере коксовой печи
Рисунок 8.5 – Поперечный разрез коксовой батареи
8.10 Качество металлургического кокса
Рисунок 8.7 – Барабаны для механического испытания кокса
Таблица 8.11 – Ситовый состав некоторых коксов
6.1 Магнитное обогащение
Магнитная сепарация является наиболее эффективным методом обогащения железных руд. Она основана на различии магнитных свойств некоторых железосодержащих минералов и минералов пустой породы. Это различие можно проиллюстрировать данными об относительной величине удельной магнитной восприимчивости некоторых минералов (по отношению к чистому железу):
Железо 100,0 Пиролюзит 0,71
Магнетит 40,1 Магнезит 0,52
Ильменит 24,7 Кварц 0,37
Сидерит 1,82 Доломит 0,22
Гематит 1,32 Апатит 0,21
Лимонит 0,84
Магнитной сепарацией обогащаются 70 % железных руд в мире и 90 % – в Украине, и марганцевых руд более 90 % крупностью до 150 мм.
Процесс сепарации разделяют на слабомагнитную и сильномагнитную. Слабомагнитная – с 3,810-5 м3/кг, сильномагнитную – меньше этой величины. Например, удельная магнитная восприимчивость магнетита составляет 9,710-5 м3/кг, а кварца – 0,4710-7 м3/кг.
По характеристике среды процесс сепарации разделяют на мокрую и сухую. Сухой сепарацией разделяют материалы крупностью 3 мм в воздушной среде, более мелкий материал (до 0,2 мм) подвергают мокрой сепарации в водной среде.
Магнитное обогащение осуществляют в аппаратах, называемых магнитными сепараторами.
Виды сепараторов: барабанные, валковые, ленточные, дисковые, роторные и др. Для слабомагнитных – валковые и роторные, сильномагнитные – барабанные.
В основе работы всех сепараторов лежит один принцип: раздробленная до необходимой крупности руда подается тонким слоем в рабочую зону аппарата, где создано магнитное поле. Под действием силы тяжести или динамического напора потока воды частички, не обладающие магнитными свойствами (хвосты) свободно удаляются из этой зоны, в то время как частички, обладающие магнитными свойствами удерживаются в магнитном поле и транспортирующей системой выносятся в другую сторону.
При сухом обогащении руда поступает сверху, а при мокром – в виде пульпы – под барабан. Ее дальнейшее движение определяется типом ванн, которые подразделяются на прямоточные, противоточные, полупротивоточные. Выбор типов ванн определяется крупностью сепарируемого материала.
Фракции 6 – 0 – в прямоточных;
3 – 0 – противоточные ванны;
0,15 – 0 – полупротивоточные с питанием в нижней части барабана.
Для разрушения образующихся флокул полярность периодически меняется. Для увеличения контрастности магнитных веществ применяют термообработку (обжиг) в окислительной, восстановительной или восстановительно-окислительной атмосферах.
Типы магнитных барабанных сепараторов (сухого обогащения) (рис.6.5):
171СЭ, 168СЭ, 189СЭ – 251СЭ.
ПБСВ 63/200 ЭБС 18/170.
Диаметр барабана от 60 до 1000 мм.
Количество барабанов от 1 до 4.
Крупность руды: 50 – 3 – 0 мм.
Частота вращения барабана 25 – 39 мин-1.
Степень извлечения железа – 85 % в прямоточных, 95 % в противоточных и 95-98 % - в полупротивоточных.
Производительность от 20 до 100 т/час.
Типы магнитных сепараторов мокрого обогащения:
167СЭ, 26СБ, 167ПП – СЭ, ПБМ – 4ПА, ПБМ – 4ППА, 209 СЭ, 209П СЭ, 209 ЦП – СЭ, ПБМ – ПП – 120/300.
Крупность 2,0-0, чаще 0,2-0.
Тонкоизмельченный материал для магнитного обогащения подвергается предварительному сгущению и обесшламливанию в магнитных конусах или гидросепараторах. Применение их позволило повысить плотность сепарируемого материала, повысить содержание железа на 7-10 %.
Весь материал перед сепараторами подвергается намагничиванию.
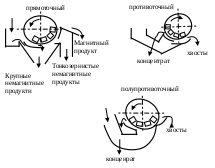
Р
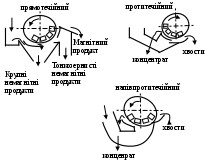
Таблица 6.1 – Сравнительные характеристики различных сепараторов
Произвдительность, т/час.м | Концентрат, % | Хвосты, % | Исходное питание, % | ||||||
выход | Содержа-ние Fe | Извлече-ние Fe | Выход | Содержа-ние Fe | Извлече-ние Fe | Выход | Содержа-ние Fe | Извлече-ние Fe | |
Сепаратор 167А-СЭ с прямоточной ваннойи трехполюсной магнитной системой | |||||||||
30,2 | 96,7 | 56,5 | 99,3 | 3,3 | 11,1 | 0,7 | 100 | 54,9 | 100,0 |
76,3 | 90,6 | 56,4 | 95,0 | 9,4 | 28,6 | 5,0 | 100 | 53,8 | 100,0 |
Сепаратор 26СБ с четырехполюсной системой и противоточной ванной | |||||||||
28,5 | 95,9 | 56,8 | 99,2 | 4,1 | 10,0 | 0,8 | 100,0 | 54,9 | 100,0 |
109,5 | 95,4 | 57,7 | 99,0 | 4,6 | 13,1 | 1,0 | 100,0 | 54,9 | 100,0 |
Чехословацкий сепаратор с противоточной ванной | |||||||||
26,6 | 98,2 | 55,6 | 99,6 | 1,8 | 10,4 | 0,4 | 100,0 | 54,8 | 100,0 |
105,4 | 37,4 | 56,1 | 99,3 | 2,6 | 14,8 | 0,7 | 100,0 | 54,9 | 100,0 |
Кроме сепараторов барабанного типа для сепарации сухих сильно магнитных материалов применяют сепараторы ленточного типа (рис.6.6).
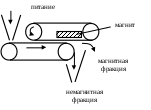
Рисунок 6.6 – Схема сепаратора ленточного типа
Ленточные сепараторы из-за сложности конструкции и низкой эффективности работы широкого применения не нашли.
Технологическая схема фабрик магнитного обогащения железных руд строится таким образом, что руда измельчается в 2-4 стадии, причем после каждой стадии путем магнитной сепарации выводятся зерна пустой породы. Это позволяет избежать больших расходов на измельчение пустой породы.
Практика работы обогатительных фабрик показывает на возможность при годовой переработке 9-10 млн.т кварцитов с содержанием железа – 36-38% получать концентраты с 64-68 % железа при степени извлечения до 85 %.
Развитие магнитного обогащения идет по пути более тонкого измельчения исходной руды и повышения напряженности магнитного поля в сепараторах, что позволяет обогащать слабомагнитные руды.
При обогащении магнетитовых руд используют сепараторы со слабым магнитным полем, а при обогащении гематитовых руд сепараторы должны быть с сильным магнитным полем (400-1000 эрстед и 18000-20000 эрстед). Широко распространены более простые сепараторы со слабым магнитным полем. Все горнообогатительные комбинаты Кривбасса (ГОКи) оснащены барабанными сепараторами со слабым и сильным магнитным полем, где обогащают магнетитовые кварциты.
ГОК для обогащения гематитовых (окисленных) руд строится рядом с Криворожским бассейном – в г. Долинское (Кировоградская обл.). На этом ГОКе (ГОКОРе) не планируется добыча кварцитов. Окисленные (гематитовые) кварциты будут привозить для обогащения на ГОКОРе со старых ГОКов Кривбасса (ЮГОК и НКГОК).
Магнитное обогащение происходит в водной среде. Концентрат получают в виде пульпы – взвесь зерен концентрата в воде. Содержание влаги в пульпе – до 40-60 %. Хвосты примерно с таким же содержанием влаги направляются в отдельные хвостохранилища.
6.2 Обезвоживание концентратов
Для осуществления таких технологических операций, как дозирование, смешивание, окомкование железорудных концентратов, последние должны содержать не более 10 % влаги. В то же время в результате мокрого обогащения (магнитной сепарацией и флотацией) получается пульпа, содержащая твердого вещества всего 20-30 %. Влажность концентрата снижают в два этапа – сгущением и фильтрацией. Если концентрат необходимо транспортировать на дальние расстояния по железной дороге зимой, то его дополнительно сушат.
Сгущение осуществляют в аппаратах, подобных гидравлическим классификаторам и гидроциклонам. В ходе этой операции удается снизить влажность до 50 % и меньше.
Фильтрация заключается в просасывании воздуха через слой влажного концентрата, помещенного на фильтровальную ткань. Эти агрегаты – вакуумфильтры – оборудуются вакуумнасосами (обычно это водокольцевые насосы), создающие глубокий вакуум – 0,72-0,76 от полного вакуума (540-570 мм.рт.столба). По конструкции вакуумфильтры чаще дисковые, бывают барабанные. Конечное содержание влаги – 9-10 %.
Огневая сушка осуществляется в барабанных сушилках, в рабочем пространстве которых сжигают горючий газ. Содержание влаги после сушки – 2-3 %.
6.3 Обжиг материалов
Обжиг применяется при подготовке сырьевых материалов к доменной плавке и сталеплавильному переделу.
Обжиг может быть окислительным, то-есть проходить в окислительной атмосфере, и восстановительный или магнетизирующий – в восстановительной атмосфере.
Окислительному обжигу можно подвергать бурые железняки, сидеритовые железные и марганцевые руды, все типы известняков с целью обогащения и получения извести.
Реакции обжига следующие:
FeCO3
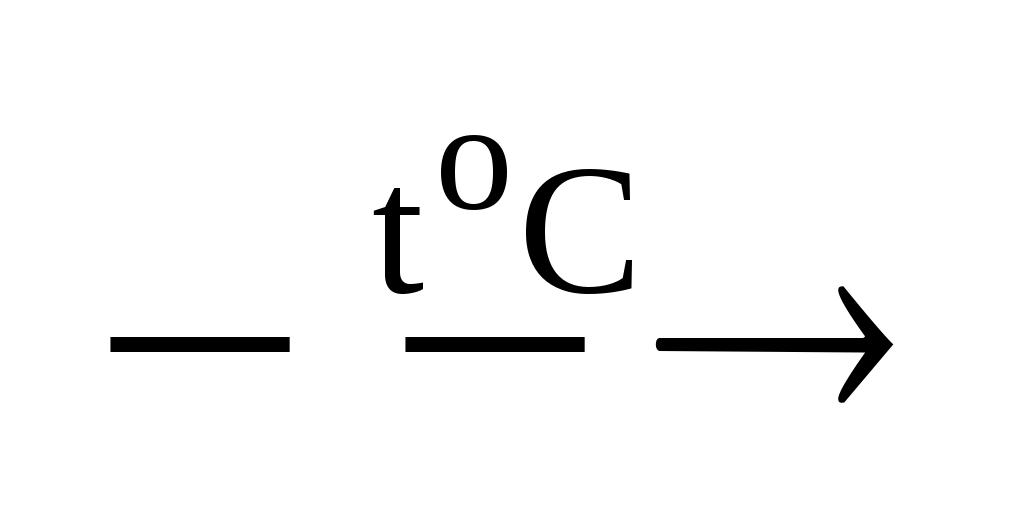
Fe2O3Н2О
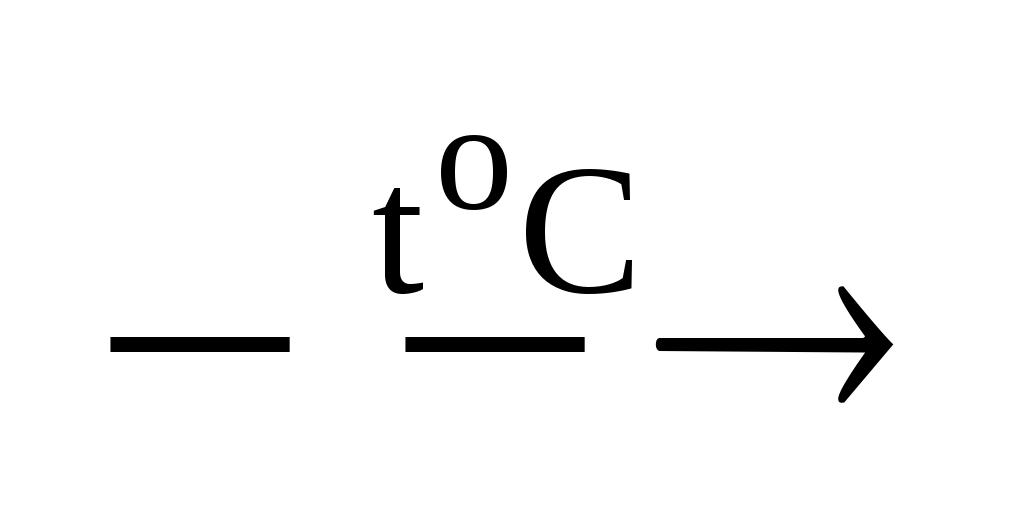
СаCO3 СаO + CO2;
MgCO3 MgO + CO2.
В настоящее время окислительный обжиг железных руд не используется ввиду его дороговизны и по целому ряду других причин.