ВУЗ: Не указан
Категория: Не указан
Дисциплина: Не указана
Добавлен: 28.03.2024
Просмотров: 103
Скачиваний: 0
ВНИМАНИЕ! Если данный файл нарушает Ваши авторские права, то обязательно сообщите нам.
Собранную муфту заполняют маслом до уровня уплотнений. Во время работы зубчатые зацепления находятся в масляной ванне.
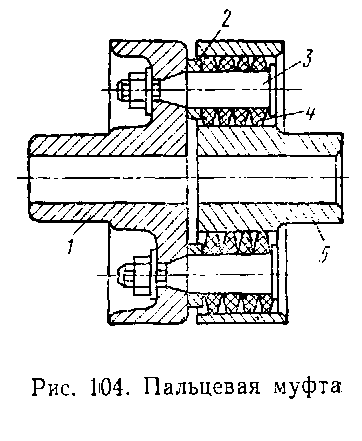
Пальцевые муфты (рис. 104) относят к типу упруго-демпфирующих соединений, допускающих небольшие продольные, поперечные и- угловые смещения одного вала относительно другого и обеспечивающих смягчение толчков и крутильных колебаний, а также некоторую компенсацию монтажных неточностей и биений соединяемых валов.
Упругими элементами пальцевой муфты, через которые осуществляется связь между полумуфтами / и 5, служат резиновые кольца 4. Резиновые кольца размещены на стальных пальцах 3, укрепленных в полумуфте 1. Жесткость резиновых колец на каждом пальце можно регулировать изменением толщины стальных колец 2.
Полумуфты изготовляют из чугунного или стального литья, а также из стальных поковок. Полумуфты крепятся на валах обычно легкой прессовкой или глухой посадкой на призматических шпонках или шлицах.
Кроме зубчатых и пальцевых соединительных муфт применяют также кулачковые и фрикционные. С помощью кулачковых муфт осуществляется постоянное соединение валов. Фрикционные муфты позволяют проводить плавное безударное соединение и разъединение валов привода и компрессора на ходу. Включение и выключение фрикционных муфт может быть ручным и автоматическим.
Ременные передачи применяют на параллельных валах в тех случаях, когда надо изменить частоту вращения, крутящий момент и направление вращения. В приводах насосных и компрессорных установок используют плоскоременные и клиноремен-ные передачи.
Промышленность выпускает следующие плоские приводные ремни: прорезиненные, кожаные, текстильные.
Выбор материала ремня зависит от внешней среды (пыль, пары, щелочи, кислоты и т. п.), характера нагрузок (постоянные, переменные, ударные), скорости движения ремня, передаваемой мощности и конструктивных особенностей ременной передачи.
Ремни надевают на шкивы, один из них укреплен на валу привода, второй — на валу компрессора или насоса. Материалом для
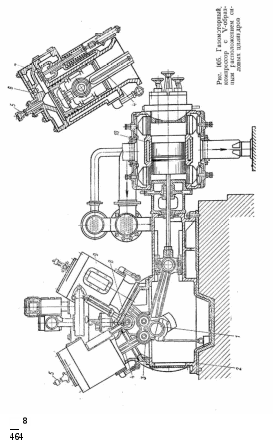
шкивов служат чугун, кованая сталь и пластмассы. Шкивы бывают сплошные, разъемные и сварные.
В клиноременной передаче за счет клиновой формы канавки на шкиве сила сцепления ремня со шкивом больше, чем в плоскоременной передаче. Поэтому клиноременная передача при одинаковых условиях более компактна, чем плоскоременная.
Клиновые ремни изготовляют двух конструкций: кордтканевые и кордшнуровые. Кордшнуровые ремни используют при малых диаметрах шкивов и повышенных скоростях движения ремня. В остальных случаях используют кордтканевые ремни. Число ремней в передаче обычно составляет 8—12, а в некоторых случаях до 16— 18. В ремнях применяют угол клина 40°. Для хорошего прилегания ремня к канавке шкива угол канавки (желоба) делают меньше, чем угол клина недеформированного ремня.
Редукторы служат для изменения частоты вращения и крутящего момента в передачах движения от двигателей к компрессорам и насосам, если валы расположены параллельно или под углом друг к другу, или скрещиваются в пространстве.
Различают следующие виды зубчатых редукторов:
по типу передачи — цилиндрические, конические, червячные {цилиндрические и глобоидные) и смешанные;
по расположению зубчатых колес — горизонтального и вертикального типов;
по числу ступеней — одно-, двух-, трех- и многоступенчатые.
Цилиндрические зубчатые редукторы получили наиболее широкое применение благодаря простоте изготовления, надежности, долговечности и широкому диапазону передаваемых мощностей и передаточных чисел. В редукторах используют цилиндрические зубчатые колеса с прямыми, косыми и шевронными зубьями. Наиболее часто применяют редукторы с шевронными зубьями.
Конические и червячные редукторы предназначены для передачи малых и средних мощностей. Глобоидные червячные редукторы имеют высокий КПД.
§ 86. Газомоторные компрессоры и газотурбинные установки
Газомоторные компрессоры. Газомоторный компрессор представляет собой агрегат, состоящий из компрессорных цилиндров и газового двигателя внутреннего сгорания, соединенных общим коленчатым валом и рамой. В газовом двигателе используют в качестве топлива природный, светильный, генераторный или доменный газ.
Большие газовые двигатели чаще всего выполняют четырехтактными. Цилиндры такого газового двигателя могут быть расположены по отношению к цилиндрам компрессора последовательно— по одной оси, параллельно — в два ряда: ряд силовых цилиндров и параллельно ему ряд компрессорных цилиндров. В последнее время наиболее распространены газомоторные компрессоры с горизонтальным расположением компрессорных цилиндров и V-образным или вертикальным расположением цилиндров четырехтактного или двухтактного двигателя. В агрегатах с двухтактными силовыми цилиндрами на каждый компрессорный цилиндр приходится один силовой, с четырехтактными силовыми цилиндрами— два.
Мощность и частоту вращения газовых двигателей регулируют по качественной схеме, при которой количество воздуха, поступающего в силовой цилиндр, остается неизменным, изменяется только количество поступающего газа. Для такого регулирования на двигателях обычно установлены центробежные регуляторы.
Производительность компрессора регулируют изменением частоты вращения вала двигателя.
Газомоторные компрессоры имеют от одного до десяти цилиндров двигателя. На рис. 105 изображен газомоторный компрессор с четырехтактными силовыми цилиндрами 9, расположенными V-об-разно, и с компрессорными цилиндрами 10 двойного действия — горизонтально. Шатуны 4 силовых цилиндров пальцами 3 непосредственно соединены с шатунами компрессорных цилиндров 10, благодаря чему достигается компактность агрегата. Клапаны 7 находятся вне цилиндров, в специальных клапанных полостях. В головке цилиндра расположены пусковой клапан 5 и запальная свеча 6. Коленчатый вал 1 агрегата уложен в станине 2. Распределительный валик 8, частота вращения которого в два раза меньше частоты вращения коленчатого вала, имеет кулачки соответствующего профиля. Под действием этих кулачков в нужный момент поднимается тот или другой клапан соответствующего цилиндра, пропуская в него рабочую смесь или выпуская выхлопные газы.
Газовую смесь подготовляют в системе питания, состоящей из чувствительного регулятора давления, емкости для топливного газа, смесительного клапана и центробежного регулятора частоты вращения. Центробежный регулятор, воздействуя на смесительный клапан, автоматически регулирует качество смеси. Количество подаваемой смеси регулируют вручную.
Агрегат оснащен тремя смазочными системами. Цилиндры двигателя, подшипники распределительного вала и направляющие крейцкопфов смазывают маслом, разбрызгиваемым коленчатым валом из картера. Остальные сборочные единицы механизма движения — с помощью шестеренных насосов по циркуляционной системе. Лубрикатор подает смазку в цилиндры и сальники компрессора.
Газотурбинные установки. Для привода центробежных компрессоров часто применяют газовые турбины. Это особенно удобно, когда компрессорная установка предназначена для нагнетания природного газа, который используют в качестве дешевого топлива для газовой турбины. В установку помимо центробежных нагнетателей входят также центробежные компрессоры, обслуживающие газовую турбину, и электрогенераторы, используемые для получения электроэнергии.
Например, газотурбинная установка ГТ-700-4, предназначенная для нагнетания природного газа, состоит из газовой турбины, осевого компрессора, нагнетателя, редуктора, генератора и камеры сгорания.
Во многих производствах выбрасываемые газы, если они имеют достаточное давление, используют в турбинах, соединенных с центробежными компрессорами. В установках по производству слабой
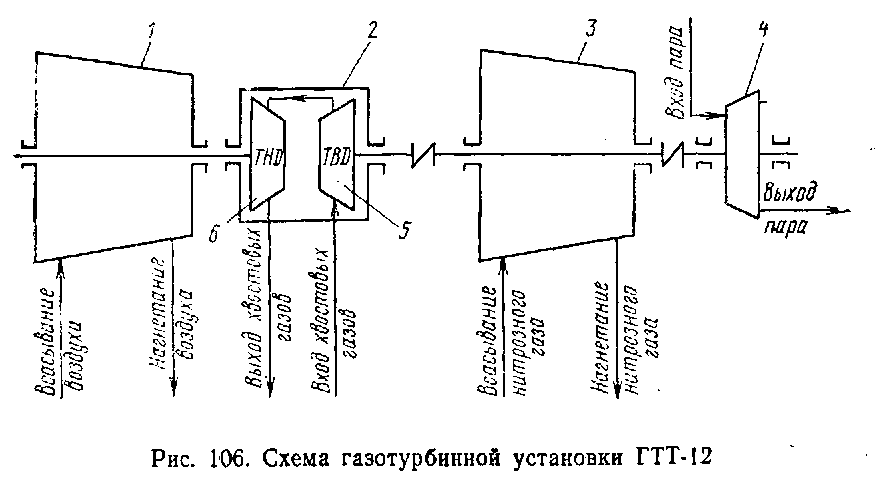
азотной кислоты под повышенным давлением применяют комплексный машинный агрегат ГТТ-12. Агрегат состоит из двух механически несвязанных между собой газовых турбин ГТТ-12 (высокого и низкого давления), осевого воздушного компрессора, нагнетателя нитрозного газа 1150-41-1, пусковой паровой турбины П-2/45, а также смазочной системы, систем регулирования, защиты управления и контроля.
Газовая турбина высокого давления служит для привода нагнетателя нитрозного газа с частотой вращения 5000 мин-1.
Газовую турбину низкого давления с частотой вращения 5200 мин-1 используют для привода осевого воздушного компрессора производительностью 200 000 м3/ч.
Воздух из атмосферы засасывается через фильтры в осевой компрессор / (рис. 106), где сжимается до давления 0,42 МПа и по трубопроводам направляется на смешивание с газообразным аммиаком. Образовавшаяся аммиачно-воздушная смесь в контактных аппаратах на сеточных катализаторах превращается в нитроз-ные газы, которые под давлением около 0,22 МПа поступают в нагнетатель 3. Газы, сжатые в нагнетателе до 1,1 МПа, поступают в абсорбционные колонны для получения слабой азотной кислоты. Хвостовые газы, образовавшиеся в процессе производства кислоты, после колонн направляются в реактор каталитической очистки, где разлагаются на нейтральные элементы. Реакция идет с выделением теплоты.
Горючие газы с температурой около 760°С и давлением 0,95 МПа после реактора поступают в турбину высокого давления 5, а затем проходят турбину низкого давления 6 и выбрасываются в атмосферу. Для запуска агрегата предусмотрена паровая турбина 4.
Турбины высокого и низкого давлений располагают в общем корпусе 2, имеющем внутреннюю тепловую изоляцию. Ротор турбины высокого давления состоит из одновенечного диска, укрепленного на консоли вала.
Вал вращается в двух подшипниках, из которых один — опорный, второй — опорно-упорный. Подшипники смонтированы в одном общем корпусе. Ротор турбины высокого давления и нагнетатель соединяют специальной зубчатой муфтой. Два диска турбины низкого давления укреплены на консоли ротора осевого компрессора с помощью горизонтальных стяжных болтов. Ротор осевого компрессора барабанного типа вращается в двух подшипниках, расположенных в корпусе осевого компрессора. Воздушный осевой компрессор имеет 10 ступеней.
Направляющие лопатки укреплены в чугунном корпусе. Рабочие лопатки крепятся к барабану ласточкиным хвостом.
Вся турбогруппа смонтирована на общей сварной раме, которая одновременно служит и маслобаком.
Масляная система агрегата состоит из главного масляного насоса, пускового и резервного электронасосов, маслобака (рама турбогруппы), маслопроводов с арматурой.
Системы регулирования, управления и защиты агрегата обеспечивают: поддержание заданного давления в нагнетании воздушного компрессора с неравномерностью 5—10% за счет выпуска небольшого количества воздуха в атмосферу; дистанционное управление сборочными единицами агрегата с местного щита в процессе пуска и эксплуатации; защиту агрегата от недопустимых режимов работы путем его аварийной остановки.
Система контроля позволяет измерять основные эксплуатационные параметры.
Контрольные вопросы. 1. Какие приводы используют для насосных и компрессорных установок? 2. Назовите основные сборочные единицы четырехтактного двигателя внутреннего сгорания. 3. По какому признаку классифицируют газовые и паровые турбины? 4. В каких случаях применяют зубчатые редукторы? 5. Какие установки называют газотурбинными? 6. Для чего в газотур» бинную установку включен осевой воздушный компрессор?