Файл: Учебное пособие (практикум) Сыктывкар 2006 Содержание Введение 3 Возникновение и развитие теории логистики 4.doc
ВУЗ: Не указан
Категория: Не указан
Дисциплина: Не указана
Добавлен: 11.04.2024
Просмотров: 73
Скачиваний: 0
ВНИМАНИЕ! Если данный файл нарушает Ваши авторские права, то обязательно сообщите нам.
(или запасы буферные) выделяются из производственных запасов при необходимости дополнительной их подготовки перед использованием в производстве (сушка леса, например). Подготовительные запасы товарных средств производства формируются в случае необходимости подготовить материальные ресурсы к отпуску потребителям.
Гарантийные запасы (или запасы страховые) предназначены для непрерывного снабжения потребителя, в случае непредвиденных обстоятельств:
В отличие от текущих запасов размер гарантийных запасов — величина постоянная. При нормальных условиях работы эти запасы неприкосновенны.
Сезонные запасы образуются при сезонном характере производства продуктов, их потребления или транспортировки. Сезонные запасы должны обеспечить нормальную работу организации во время сезонного перерыва в производстве, потреблении или в транспортировке продукции.
Переходящие запасы — это остатки материальных ресурсов на конец отчетного периода Они предназначаются для обеспечения непрерывности производства и потребления в отчетном и, следующем за отчетным, периоде, до очередной поставки.
Классификация по времени позволяет выделить различные количественные уровни запасов.
Максимальный желательный запас определяет уровень запаса, экономически целесообразный в данной системе управления запасами. Этот уровень может превышаться. В различных системах управления, максимальный желательный запас используется, как ориентир, при расчете объема заказа.
Пороговый уровень запаса используется для определения момента времени выдачи очередного заказа.
Текущий запас соответствует уровню запаса в любой момент учета. Он может совпасть с максимальным желательным уровнем, пороговым уровнем или гарантийным запасом.
Гарантийный запас (или запас страховой) аналогичен гарантийному запасу в классификации по исполняемой запасом функции и предназначен для непрерывного снабжения потребителя в случае непредвиденных обстоятельств.
Неликвидные запасы — длительно неиспользуемые производственные и товарные запасы Они образуются вследствие ухудшения качества товаров во время хранения, а также морального износа. Это единственный вид запаса, который не соответствует определенным выше критериям.
Управление запасами сырья и материалов
Процесс закупочной деятельности предприятия неразрывно связан с процессом хранения приобретаемых материальных ценностей, до того как они будут израсходованы на производство. Наличие запасов сырья, материалов, комплектующих изделий и прочих ресурсов связано с необходимостью бесперебойного и ритмичного обеспечения производственных подразделений материальными ресурсами. Несвоевременные поставки могут пагубно отразиться на выполнении производственной программы и привести к нарушению сроков выполнения заказов или абсолютной невозможности их выполнения.
В то же время создание и хранение запасов сопряжено с большими затратами. Общая сумма затрат, связанных со снабженческо-заготовительной деятельностью, составляет обычно до 25% стоимости самих запасов.
Управление запасами – это функциональная деятельность, цель которой – довести общую сумму ежегодных затрат на содержание запасов до минимума при условии удовлетворительного обслуживания клиентов.
Схема управления материальными запасами.
Техника управления запасами включает определение следующих показателей:
Суммарный цикл заказа – это продолжительность страхового цикла и цикла поставки. Суммарный цикл заказа определяет нижний предел количества имеющихся на складе и заказанных товаров.
Расчет оптимального размера заказа и определение момента его размещения
Оптимальный размер заказа определяется теми затратами, на которые оказывают влияние количество хранящихся запасов или количество сделанных заказов. Если большее количество единиц заказывается одновременно, меньше заказов потребуется сделать за год, т.е. уменьшиться стоимость выполнения заказа. В то же время, когда делается меньше заказов, нужно иметь большой средний запас, что ведет к увеличению стоимости хранения запасов. Цель управления заключается в том, чтобы снизить стоимость хранения больших запасов по сравнению со стоимостью размещения большого количества заказов. Оптимальный размер заказа – это такое заказанное количество, при котором стоимость всего объема заказов и хранения запасов будет минимальной.
В теории управления запасами разработаны две основные системы управления, которые решают поставленные задачи, соответствуя цели непрерывного обеспечения потребителя материальными ресурсами:
1) система управления запасами с фиксированным размером заказа;
2) система управления запасами с фиксированным интервалом времени между заказами.
Система с фиксированным размером заказа
Основополагающий параметр системы – размер заказа. Он строго зафиксирован и не меняется ни при каких условиях работы системы.
Критерием оптимизации является минимум совокупных затрат на хранение запасов и повторение заказа. Данный критерий учитывает три фактора:
Оптимальный размер заказа по критерию минимизации совокупных затрат на хранение запаса и повторение заказа рассчитывается по формуле (критерий Уилсона):
, где
Q – количество единиц заказа
D – общая потребность единиц материала на период
О – стоимость выполнения одного заказа
H – стоимость хранения единицы запаса.
Исходные данные для расчета параметров системы:
Система с фиксированным интервалом времени между заказами
В системе с фиксированным интервалом времени между заказами, заказы делаются в строго определенные моменты времени, которые отстоят друг от друга на равные интервалы.
Определить интервал времени между заказами можно с учетом оптимального размера заказа. Расчет интервала времени между заказами производится следующим образом:
, где
N – количество рабочих дней в году, дни;
S – потребность в заказываемом продукте, шт.;
OP3 – оптимальный размер заказа, шт.
Полученный с помощью приведенной формулы интервал времени может быть скорректирован на основе экспертных оценок.
Исходные данные для расчета параметров системы следующие:
Преимущества и недостатки основных систем управления запасами
Сравнение основных систем управления запасами.
При значительных колебаниях спроса основные системы управления запасами не в состоянии обеспечить бесперебойное снабжение потребителя без значительного завышения объема запасов. При наличии систематических сбоев в поставке и потреблении основные системы управления запасами становятся неэффективными. Для таких случаев проектируются иные системы управления запасами.
Наиболее распространенные системы управления запасами, основанные на сочетании параметров основных систем:
Система с установленной периодичностью пополнения запасов до постоянного уровня
В данной системе, как и в системе с фиксированным интервалом времени между заказами, входным параметром является период времени между затратами. В отличие от основной системы, она ориентирована на работу при значительных колебаниях потребления. Чтобы предотвратить завышение объемов запасов, содержащихся на складе, или их дефицит, заказы производятся не только в установленные моменты времени, но и при достижении запасом порогового уровня. Таким образом, рассматриваемая система включает в себя элемент системы с фиксированным интервалом времени между заказами (установленную периодичность оформления заказа) и элемент системы с фиксированным размером заказа (отслеживание порогового уровня запасов).
Система «минимум – максимум»
Эта система, как и система с установленной периодичностью пополнения запасов до постоянного уровня, содержит в себе элементы основных систем управления запасами. В ней используется постоянный интервал времени между заказами. Система «минимум – максимум» ориентирована на ситуацию, когда затраты на учет запасов и издержки на оформление заказа настолько значительны, что становятся соизмеримы с потерями от дефицита запасов. Поэтому в рассматриваемой системе заказы, производятся не через каждый заданный интервал времени, а только при условии, что запасы на складе в этот момент оказались равными или меньше установленного минимального уровня. В случае выдачи размер рассчитывается так, чтобы поставка пополнила запасы до максимального желательного уровня. Данная система работает лишь с двумя уровнями запасов – минимальным и максимальным.
Система «Канбан»
Логистическая система "Канбан", обеспечивающая предприятие материалами "с колес", относится к "вытягивающей" разновидности системы "точно в срок", при которой размер партии поставки, скорость и сроки поставки определяет не поставщик, а потребитель материалов, с параллельным движением специальных карточек "Канбан" в которых содержится вся необходимая информация. Так, автомобильная фирма "Тойота" снабжает производство материалами "с колес" по следующей схеме (рис). Для перемещения материалов от поставщика используется три грузовых автомобиля с контейнерами. Один из них находится в движении, другой у поставщика под погрузкой, третий у заказчика под выгрузкой. Ежедневно к 8 часам утра водитель автомашины доставляет поставщику порожние контейнеры вмес
Гарантийные запасы (или запасы страховые) предназначены для непрерывного снабжения потребителя, в случае непредвиденных обстоятельств:
-
отклонения в периодичности и в величине партий поставок от запланированных, -
изменения интенсивности потребления, -
задержки поставок в пути.
В отличие от текущих запасов размер гарантийных запасов — величина постоянная. При нормальных условиях работы эти запасы неприкосновенны.
Сезонные запасы образуются при сезонном характере производства продуктов, их потребления или транспортировки. Сезонные запасы должны обеспечить нормальную работу организации во время сезонного перерыва в производстве, потреблении или в транспортировке продукции.
Переходящие запасы — это остатки материальных ресурсов на конец отчетного периода Они предназначаются для обеспечения непрерывности производства и потребления в отчетном и, следующем за отчетным, периоде, до очередной поставки.
Классификация по времени позволяет выделить различные количественные уровни запасов.
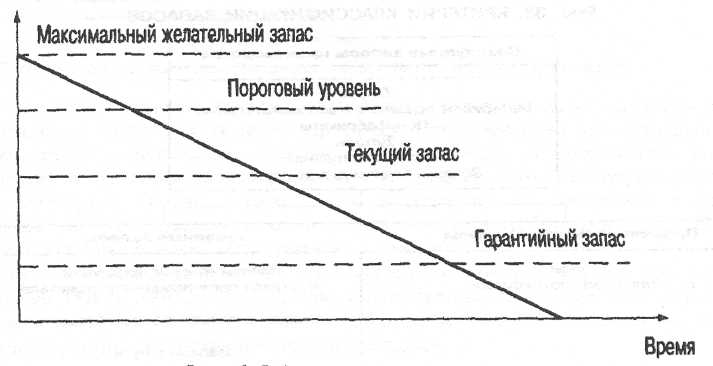
Максимальный желательный запас определяет уровень запаса, экономически целесообразный в данной системе управления запасами. Этот уровень может превышаться. В различных системах управления, максимальный желательный запас используется, как ориентир, при расчете объема заказа.
Пороговый уровень запаса используется для определения момента времени выдачи очередного заказа.
Текущий запас соответствует уровню запаса в любой момент учета. Он может совпасть с максимальным желательным уровнем, пороговым уровнем или гарантийным запасом.
Гарантийный запас (или запас страховой) аналогичен гарантийному запасу в классификации по исполняемой запасом функции и предназначен для непрерывного снабжения потребителя в случае непредвиденных обстоятельств.
Неликвидные запасы — длительно неиспользуемые производственные и товарные запасы Они образуются вследствие ухудшения качества товаров во время хранения, а также морального износа. Это единственный вид запаса, который не соответствует определенным выше критериям.
Управление запасами сырья и материалов
Процесс закупочной деятельности предприятия неразрывно связан с процессом хранения приобретаемых материальных ценностей, до того как они будут израсходованы на производство. Наличие запасов сырья, материалов, комплектующих изделий и прочих ресурсов связано с необходимостью бесперебойного и ритмичного обеспечения производственных подразделений материальными ресурсами. Несвоевременные поставки могут пагубно отразиться на выполнении производственной программы и привести к нарушению сроков выполнения заказов или абсолютной невозможности их выполнения.
В то же время создание и хранение запасов сопряжено с большими затратами. Общая сумма затрат, связанных со снабженческо-заготовительной деятельностью, составляет обычно до 25% стоимости самих запасов.
Управление запасами – это функциональная деятельность, цель которой – довести общую сумму ежегодных затрат на содержание запасов до минимума при условии удовлетворительного обслуживания клиентов.
Схема управления материальными запасами.
-
Определение задач и целей управления запасами
-
П
Плановое управление
оиск путей поддержания оптимального запаса -
Сбор данных о нормированных и фактических запасах
-
Выбор вариантов действий
-
Принятие решений
-
С
Процедуры контроля и регулирования
равнение фактических запасов с оптимальным уровнем -
Процедуры заявок, поставок и отпуска материалов
-
Сравнение фактических запасов с уровнем заказа
Техника управления запасами включает определение следующих показателей:
-
продолжительность страховых циклов -
продолжительность циклов поставки -
размер заказываемых партий -
суммарный цикл заказа
Суммарный цикл заказа – это продолжительность страхового цикла и цикла поставки. Суммарный цикл заказа определяет нижний предел количества имеющихся на складе и заказанных товаров.
Расчет оптимального размера заказа и определение момента его размещения
Оптимальный размер заказа определяется теми затратами, на которые оказывают влияние количество хранящихся запасов или количество сделанных заказов. Если большее количество единиц заказывается одновременно, меньше заказов потребуется сделать за год, т.е. уменьшиться стоимость выполнения заказа. В то же время, когда делается меньше заказов, нужно иметь большой средний запас, что ведет к увеличению стоимости хранения запасов. Цель управления заключается в том, чтобы снизить стоимость хранения больших запасов по сравнению со стоимостью размещения большого количества заказов. Оптимальный размер заказа – это такое заказанное количество, при котором стоимость всего объема заказов и хранения запасов будет минимальной.
В теории управления запасами разработаны две основные системы управления, которые решают поставленные задачи, соответствуя цели непрерывного обеспечения потребителя материальными ресурсами:
1) система управления запасами с фиксированным размером заказа;
2) система управления запасами с фиксированным интервалом времени между заказами.
Система с фиксированным размером заказа
Основополагающий параметр системы – размер заказа. Он строго зафиксирован и не меняется ни при каких условиях работы системы.
Критерием оптимизации является минимум совокупных затрат на хранение запасов и повторение заказа. Данный критерий учитывает три фактора:
-
используемая площадь складских помещений; -
издержки на хранение запасов; -
стоимость оформления заказа.
Оптимальный размер заказа по критерию минимизации совокупных затрат на хранение запаса и повторение заказа рассчитывается по формуле (критерий Уилсона):
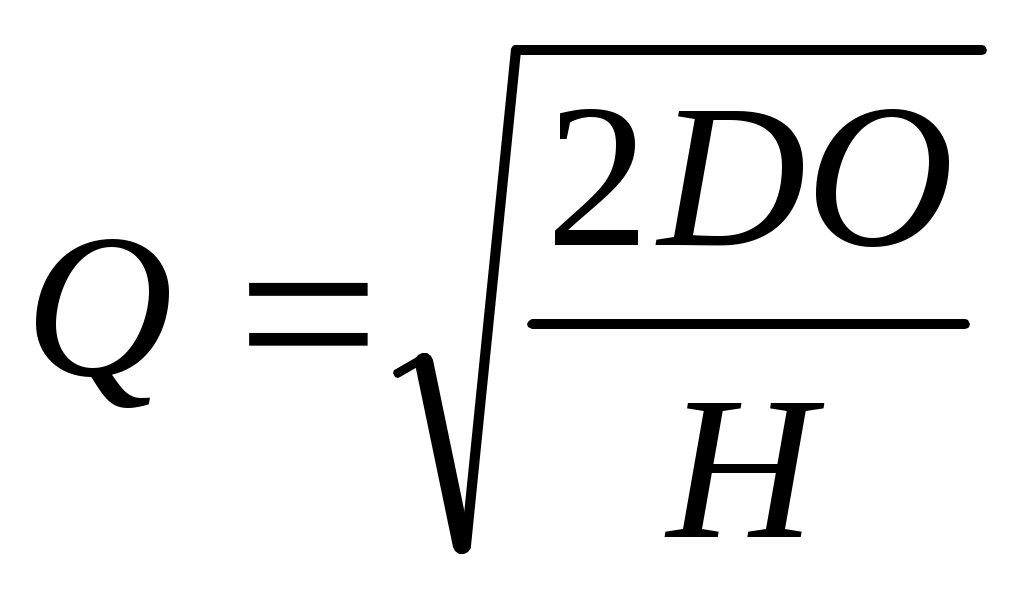
Q – количество единиц заказа
D – общая потребность единиц материала на период
О – стоимость выполнения одного заказа
H – стоимость хранения единицы запаса.
Исходные данные для расчета параметров системы:
-
потребность в заказываемом продукте, шт; -
оптимальный размер заказа, шт.; -
время поставки, дни; -
возможная задержка поставки, дни.
Система с фиксированным интервалом времени между заказами
В системе с фиксированным интервалом времени между заказами, заказы делаются в строго определенные моменты времени, которые отстоят друг от друга на равные интервалы.
Определить интервал времени между заказами можно с учетом оптимального размера заказа. Расчет интервала времени между заказами производится следующим образом:
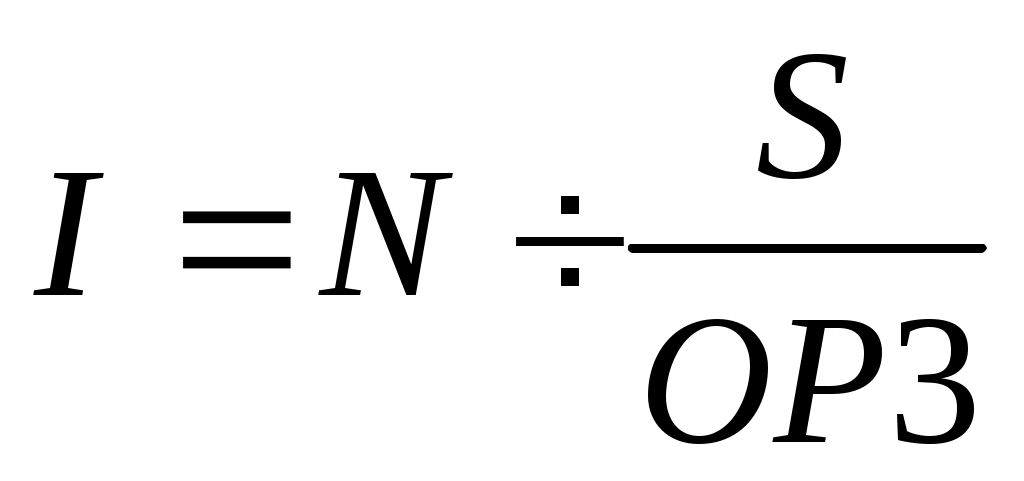
N – количество рабочих дней в году, дни;
S – потребность в заказываемом продукте, шт.;
OP3 – оптимальный размер заказа, шт.
Полученный с помощью приведенной формулы интервал времени может быть скорректирован на основе экспертных оценок.
Исходные данные для расчета параметров системы следующие:
-
потребность в заказываемом продукте, шт.; -
интервал времени между заказами, дни; -
время доставки, дни; -
возможная задержка, дни.
Преимущества и недостатки основных систем управления запасами
Сравнение основных систем управления запасами.
Система | Преимущества | Недостатки |
С фиксированным размером заказа | Меньший уровень максимального желательного запаса Экономия затрат на содержание запасов на складе за счет сокращения площадей под запасы | Ведение постоянного контроля наличия запасов на складе |
С фиксированным интервалом времени между заказами | Отсутствие постоянного контроля наличия запасов на складе | Высокий уровень максимального желательного запаса Повышение затрат на содержание запасов на сладе за счет увеличения площадей под запасы |
При значительных колебаниях спроса основные системы управления запасами не в состоянии обеспечить бесперебойное снабжение потребителя без значительного завышения объема запасов. При наличии систематических сбоев в поставке и потреблении основные системы управления запасами становятся неэффективными. Для таких случаев проектируются иные системы управления запасами.
Наиболее распространенные системы управления запасами, основанные на сочетании параметров основных систем:
-
система с установленной периодичностью пополнения запасов до постоянного уровня. -
Система «минимум – максимум».
Система с установленной периодичностью пополнения запасов до постоянного уровня
В данной системе, как и в системе с фиксированным интервалом времени между заказами, входным параметром является период времени между затратами. В отличие от основной системы, она ориентирована на работу при значительных колебаниях потребления. Чтобы предотвратить завышение объемов запасов, содержащихся на складе, или их дефицит, заказы производятся не только в установленные моменты времени, но и при достижении запасом порогового уровня. Таким образом, рассматриваемая система включает в себя элемент системы с фиксированным интервалом времени между заказами (установленную периодичность оформления заказа) и элемент системы с фиксированным размером заказа (отслеживание порогового уровня запасов).
Система «минимум – максимум»
Эта система, как и система с установленной периодичностью пополнения запасов до постоянного уровня, содержит в себе элементы основных систем управления запасами. В ней используется постоянный интервал времени между заказами. Система «минимум – максимум» ориентирована на ситуацию, когда затраты на учет запасов и издержки на оформление заказа настолько значительны, что становятся соизмеримы с потерями от дефицита запасов. Поэтому в рассматриваемой системе заказы, производятся не через каждый заданный интервал времени, а только при условии, что запасы на складе в этот момент оказались равными или меньше установленного минимального уровня. В случае выдачи размер рассчитывается так, чтобы поставка пополнила запасы до максимального желательного уровня. Данная система работает лишь с двумя уровнями запасов – минимальным и максимальным.
Система «Канбан»
Логистическая система "Канбан", обеспечивающая предприятие материалами "с колес", относится к "вытягивающей" разновидности системы "точно в срок", при которой размер партии поставки, скорость и сроки поставки определяет не поставщик, а потребитель материалов, с параллельным движением специальных карточек "Канбан" в которых содержится вся необходимая информация. Так, автомобильная фирма "Тойота" снабжает производство материалами "с колес" по следующей схеме (рис). Для перемещения материалов от поставщика используется три грузовых автомобиля с контейнерами. Один из них находится в движении, другой у поставщика под погрузкой, третий у заказчика под выгрузкой. Ежедневно к 8 часам утра водитель автомашины доставляет поставщику порожние контейнеры вмес