Добавлен: 25.04.2024
Просмотров: 305
Скачиваний: 1
ВНИМАНИЕ! Если данный файл нарушает Ваши авторские права, то обязательно сообщите нам.
СОДЕРЖАНИЕ
1.1. Характеристика целевого продукта
1.1.2 Химические свойства и применение
1.1.3 Способы получения серной кислоты
1.1.4 Применение серной кислоты
1.2 Характеристика исходного сырья и материалов
1.4 Описание технологического процесса
2. МАТЕРИАЛЬНЫЙ И ТЕПЛОВОЙ БАЛАНС ПЕЧИ ДЛЯ ОБЖИГА ЖЕЛЕЗНОГО КОЛЧЕДАНА
2.1. Расчет материального баланса печи для обжига КС-450
I — получение обжигового газа: 1 — обжиг колчедана, 2 — охлаждение газа в котле-утилизаторе, 3 — общая очистка газа, 4 — специальная очистка газа; II — контактирование: 5 — подогрев газа в теплообменнике, 6 — контактирование; III — абсорбция: 7 — абсорбция сксида серы (VI) и образование серной кислоты.
Рисунок 1.3 - Функциональная схема производства серной кислоты по методу «двойное контактирование - двойная абсорбция»
Производство серной кислоты из сульфидов металлов существенно сложнее. Технологическая схема производства серной кислоты из железного колчедана с использованием принципа двойного контактирования ДК—ДА показана на рисунке 1.4.
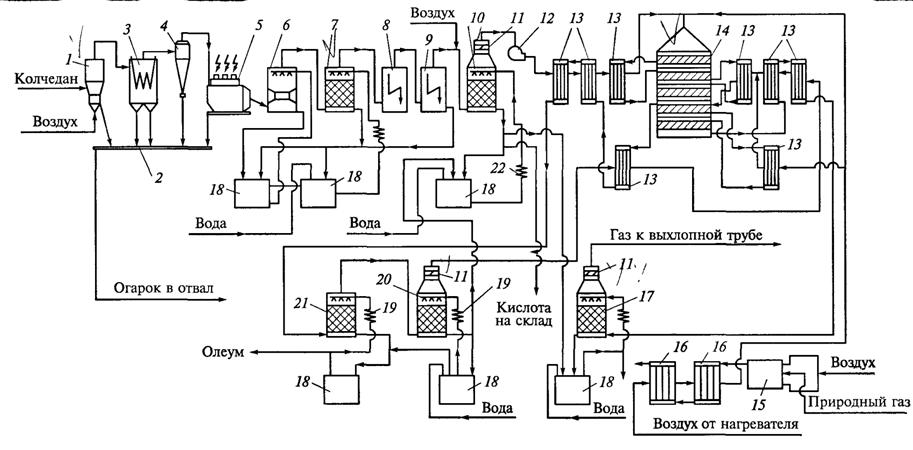
1 — печь;
2 — система гидроудаления огарка;
3 — котел-утилизатор;
4 — циклон с пересыпным уст.;
5 — сухой электрофильтр;
6 — полая промывная башня;
7 — насадочная промывная башня;
8, 9 — мокрые электрофильтры;
10 — сушильная башня;
11— фильтр-брызгоуловитель;
12 — турбогазодувка;
13 — теплообменники контактного узла;
14 — контактный аппарат;
15 — пусковой подогреватель;
16 — теплообменник;
17 — второй моногидратный абсорбер;
18 — сборник кислоты;
19 — холодильник;
20 — первый моногидратный абсорбер;
21 — олеумный абсорбер;
22 — холодильник воздушного охлаждения кислоты
Рисунок 1.4 - Технологическая схема производства серной кислоты из колчедана по способу ДК—ДА
Колчедан через дозатор подают в печь 1 кипящего слоя. Полученный запыленный обжиговый газ, содержащий 13% SO2 и имеющий на выходе из печи температуру около 700°С, подают сначала в котел-утилизатор 3, а затем на стадию сухой очистки от огарковой пыли (в циклоны 4 и в сухой электрофильтр 5). В котле-утилизаторе 3 происходит охлаждение газа с одновременным получением энергетического водяного пара (давление 4 мПа и температура 450 °С), который может быть использован как в самой установке для компенсации затрат энергии на работу компрессоров и насосов, так и в других цехах завода.
В очистном отделении, состоящем из двух промывных башен 6 и 7, двух пар мокрых электрофильтров 8 и 9 и сушильной башни 10, происходит очистка газа от соединений мышьяка, селена, фтора и его осушка.
Первая полая промывная башня 6 работает в испарительном режиме: циркулирующая кислота охлаждает газ, при этом теплота затрачивается на испарение воды из кислоты, поступающей на орошение. Концентрацию орошающей кислоты в первой башне, равную 40-50% H2SO4, поддерживают постоянной путем разбавления 10-15%-ной кислотой из второй промывной башни 7. Кислота из второй башни поступает в сборник 18 и после охлаждения возвращается на орошение.
После второй промывной башни газ проходит последовательно две пары мокрых электрофильтров 8 и 9, затем насадочную сушильную башню 10, орошаемую 93-94%-ной серной кислотой при температуре 28-30°С. Кислота циркулирует между сушильной башней 10 и сборником 18,часть кислоты отводится как готовая продукция на склад. Для поддержания постоянной концентрации H2SO4 в сборник кислоты 18 вводят 98-99%-ную кислоту из моногидратных абсорберов 17 и 20. Для поддержания постоянной температуры на стадии осушки циркулирующую кислоту охлаждают в холодильнике воздушного охлаждения 22. Перед сушильной башней обжиговый газ разбавляют воздухом для снижения в нем концентрации SO2 до 9 % и увеличения избытка кислорода в соответствии с оптимальными условиями окисления диоксида серы.
После сушильной башни обжиговый газ проходит через фильтр-брызгоуловитель 11 и поступает в турбогазодувку 12. В теплообменниках 13газ нагревается за счет теплоты продуктов реакции до температуры зажигания катализатора (420-440°С) и поступает на первый слой контактного аппарата, где происходит окисление 74% SO2 с одновременным повышением температуры до 600°С. После охлаждения до 465°С газ поступает на второй слой контактного аппарата, где степень превращения достигает 86%, а температура газа возрастает до 514ºС. После охлаждения до температуры 450ºС газ поступает на третий слой контактного аппарата, где степень превращения SO2 увеличивается до 94-94,5 %, а температура повышается до 470°С.
Затем в соответствии с требованиями метода ДК—ДА реакционный газ охлаждают в теплообменниках от 13 до 100°С и направляют на абсорбцию первой ступени: сначала в олеумный абсорбер 21, затем в моногидратный абсорбер 20. После моногидратного абсорбера и фильтра-брызгоуловителя газ вновь нагревают до температуры 430°С и подают на четвертый слой катализатора. Концентрация SO2 в газе составляет теперь 0,75-0,85 %. В четвертом слое происходит окисление остаточного SO2 с конверсией ≈ 80 %,сопровождающееся повышением температуры до 449°С. Реакционную смесь вновь охлаждают до температуры 409°С и направляют на последний (пятый) слой контактного аппарата. Общая степень превращения после пяти стадий контактирования составляет 99,9%.
Газовую смесь после охлаждения направляют в моногидратный абсорбер второй ступени абсорбции 17. Непоглощенный газ, состоящий в основном из воздуха, пропускают через фильтр 11 для выделения брызг и тумана и выбрасывают в атмосферу через выхлопную трубу. Производительность установки составляет до 1500 т/сут по моногидрату. Расход на 1 т моногидрата: колчедана 0,82 т, воды 50 м3, электроэнергии 82 кВт -ч.
Способ получения серной кислоты из сероводорода, так называемый мокрый катализ (разработчики И.А.Ададуров, Д. Гернст, 1931 г.), состоит в том, что смесь оксида серы (IV) и паров воды, полученная сжиганием сероводорода в потоке воздуха, подается в контактный аппарат без разделения, где оксид серы (IV) окисляется при твердом ванадиевом катализаторе до оксида серы (VI). Затем, газовая смесь охлаждается в конденсаторе, где пары образующейся серной кислоты превращаются в жидкий продукт. Таким образом, в отличие от способов производства серной кислоты из колчедана и серы в процессе мокрого катализа отсутствует специальная стадия абсорбции оксида серы (VI) и весь процесс включает только три последовательных стадии:
1) сжигание сероводорода с образованием смеси оксида серы (IV) и паров воды эквимолекулярного состава (1:1):
H2S + 1,5О2 → SO2 + Н2О – 519 кДж
2) окисление оксида серы (IV) до оксида серы (VI) с сохранением эквимолекулярное™ состава смеси оксида серы (VI) и паров воды (1:1):
SO2 + 0,5О2 ↔ SO3 - 96 кДж
3) конденсация паров и образование серной кислоты:
SО3 + Н2О↔H2SО4 - 92 кДж.
Таким образом, процесс мокрого катализа описывается суммарным уравнением
H2S + 2О2 → H2SO4 -707 кДж.
В качестве сырья при производстве серной кислоты по методу мокрого катализа используют высококонцентрированный сероводородный газ (объемная доля сероводорода до 90%), являющийся отходом некоторых производств. Так как газ при выделении подвергается промывке, то не нуждается в особой стадии очистки, а продукты его сжигания не содержат вредных примесей и также не требуют очистки. Это наряду с отсутствием в технологической схеме стадии абсорбции существенно упрощает процесс производства.
Технологическая схема производства серной кислоты из сероводорода (рис. 1.5) включает в себя следующие операции:
-
сжигание сероводородного газа при большом избытке воздуха для исключения перегрева вследствие выделения большого количества теплоты; -
охлаждение газопаровой смеси от 1000 до 400ºС в котле-утилизаторе; -
разбавление газопаровой смеси воздухом до оптимального для контактирования состава; -
контактирование в контактных аппаратах, термостатируемых введением воздуха между слоями катализатора; -
охлаждение конвертированного газа в башнях, орошаемых серной кислотой, с образованием продукционной серной кислоты и сернокислотного тумана, улавливаемого в электрофильтрах.
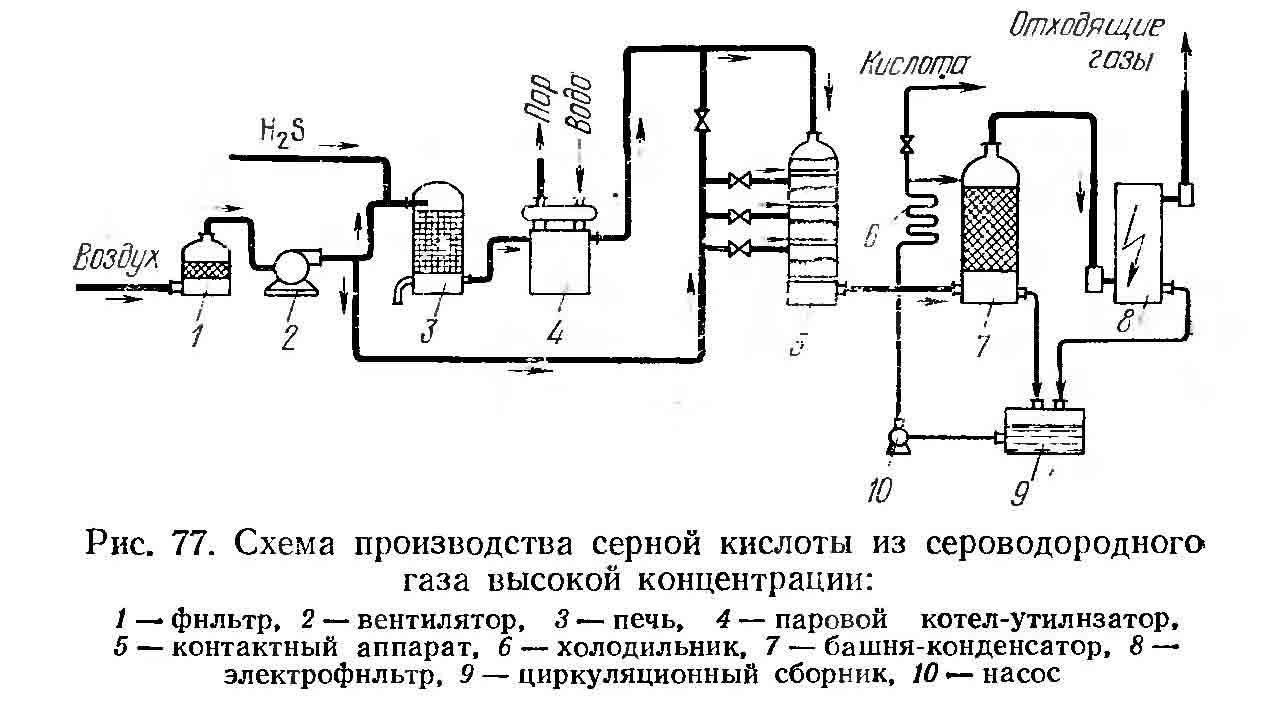
1 — фильтр; 2 — вентилятор; 3 — печь; 4 — паровой котел-утилизатор; 5 — контактный аппарат; 6 — холодильник; 7 — башня–конденсатор; 8 —электрофильтр; 9 — циркуляционный сборник; 10 — насос.
Рисунок 1.5 - Схема производства серной кислоты из сероводородного
газа высокой концентрации
Теоретически, при абсолютно сухих сероводородном газе и воздухе, должна образоваться 100%-ная серная кислота. На практике вследствие присутствия в воздухе паров воды концентрация получаемой кислоты не превышает 96 %, при пересчете на сероводород — 97 %. Производительность существующих установок, работающих по способу мокрого катализа, достигает 300 т/сут по моногидрату серной кислоты.
1.4 Описание технологического процесса
Процесс получения серной кислоты в данном случае осуществляется контактным способом. Контактный способ производства – самый распространенный, и он выполняет следующие задачи:
Получается продукт, удовлетворяющий потребности максимального количества потребителей. Во время производства сокращается вред для окружающей среды.
При контактном способе в качестве сырья используются такие вещества:
-
пирит (серный колчедан); -
сера; -
оксид ванадия (это вещество вызывает роль катализатора); -
сероводород; -
сульфиды различных металлов.
Последовательность процессов следующая:
1. Сжигание серы. При получении обжигового газа путем сжигания серы отпадает необходимость очистки от примесей. Стадия подготовки будет включать лишь осушку газа и утилизацию кислоты. При сжигании серы протекает необратимая экзотермическая реакция (с выделением очень большого количества теплоты):
S + O2 = SO2
Расплавленная жидкая сера, подаваемая на сжигание, испаряется (кипит) при температуре 444,6°С. Теплота испарения составляет 288 кДж/кг. Как видно из приведенных данных, теплоты реакции горения серы вполне достаточно для испарения исходного сырья, поэтому взаимодействие серы и кислорода происходит в газовой фазе (гомогенная реакция). Сжигание серы в промышленности проводят следующим образом. Серу предварительно расплавляют (для этого можно использовать водяной пар, полученный при утилизации теплоты основной реакции горения серы). Так как температура плавления серы сравнительно низка, то путем отстаивания и последующей фильтрации от серы легко отделить механические примеси, не перешедшие в жидкую фазу, и получить исходное сырье достаточной степени чистоты. Для сжигания расплавленной серы используют два типа печей - форсуночные и циклонные. В них необходимо предусмотреть распыление жидкой серы для ее быстрого испарения и обеспечения надежного контакта с воздухом во всех частях аппарата. Из печи обжиговый газ поступает в котел-утилизатор и далее в последующие аппараты. Концентрация диоксида серы в обжиговом газе зависит от соотношения серы и воздуха, подаваемых на сжигание. Обычно при сжигании серы получают обжиговый газ, содержащий 13 - 14% SO
2.
2. Контактное окисление SO2 в SO3. Реакция окисления диоксида серы характеризуется очень высоким значением энергии активации и поэтому практическое ее осуществление возможно лишь в присутствии катализатора. В промышленности основным катализатором окисления SO2 является катализатор на основе оксида ванадия V2O5 (ванадиевая контактная масса). Скорость реакции повышается с ростом концентрации кислорода, поэтому процесс в промышленности проводят при его избытке. Так как реакция окисления SO2 относится к типу экзотермических, температурный режим ее проведения должен приближаться к линии оптимальных температур.
SO2 + 0,5 O2 = SO3
Чаще всего в промышленности используют полочные контактные аппараты с наружным теплообменом. Схема теплообмена предполагает максимальное использование теплоты реакции для подогрева исходного газа и одновременное охлаждение газа между полками. Одна из важнейших задач, стоящих перед сернокислотной промышленностью, - увеличение степени превращения диоксида серы и снижение его выбросов в атмосферу. Эта задача может быть решена несколькими методами.
3. Абсорбция триоксида серы. Последней стадией процесса производства серной кислоты контактным способом является абсорбция триоксида серы из газовой смеси и превращение его в серную кислоту.
nSO3 + H2O = H2SO4 + (n-1)SO3 + Q
-
если n >1, то получается олеум (раствор SO3 в H2SO4); -
если n =1, то получается моногидрат (98,3% H2SO4); -
если n <1, то получается разбавленная серная кислота.
При выборе абсорбента и условий проведения стадии абсорбции необходимо обеспечить почти 100%-ное извлечение SO3 из газовой фазы. Оптимальным абсорбентом является 98,3%-ная серная кислота (техническое название - моногидрат), соответствующая азеотропному составу. Действительно, над этой кислотой практически нет ни паров воды, ни паров SO
3. Протекающий при этом процесс можно условно описать уравнением реакции:
SO3 + nH2SO4 + H2O = (n+1)H2SO4
Использование в качестве поглотителя менее концентрированной серной кислоты может привести к образованию сернокислотного тумана. На рисунке 1.6 наглядно изображена технологическая схема производства серной кислоты.
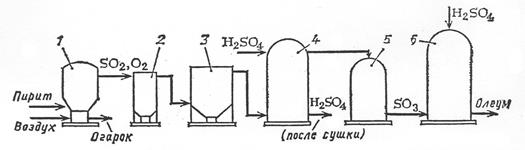
1– печь для обжига; 2,3 – пылеулавливатели; 4 – осушительная башня; 5– контактный аппарат; 6 – поглотительная башня.