Файл: Курсовой проект по дисциплине Технологическое оборудование.docx
ВУЗ: Не указан
Категория: Не указан
Дисциплина: Не указана
Добавлен: 26.04.2024
Просмотров: 56
Скачиваний: 0
ВНИМАНИЕ! Если данный файл нарушает Ваши авторские права, то обязательно сообщите нам.
СОДЕРЖАНИЕ
1.2 Аппаратурное оформление узла
2.1 Описание технологической схемы и оборудования блока
3 Проектировочный расчет теплообменного аппарата
3.4 Разработка эскиза теплообменного аппарата
3.5 Сводная таблица по результатам расчетов теплообменного аппарата
4.1 Расчет на прочность элементов теплообменного аппарата
4.2 Подбор штуцера (вход продукта в кожух теплообменника)
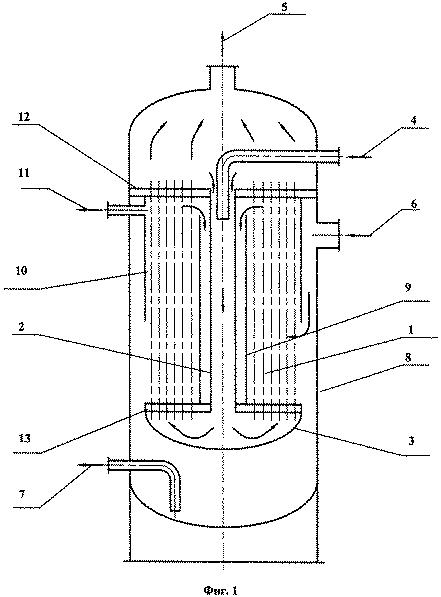
Рисунок 1.6 – Схема разработанного кожухотрубного теплообменника
2 Технологический раздел
2.1 Описание технологической схемы и оборудования блока
Сырье подается для нагрева продуктами реакции в теплообменник Т-2.
Гидрогенизат отдает свое тепло в ребойлере Т-3 для нагрева низа колонны К-1, и направляется для охлаждения в воздушный холодильник АВО-101/1,2 далее в сепаратор С-102, где происходит отделение ВСГ от гидрогенизата. ВСГ возвращается, в систему циркуляции, а нестабильный гидрогенизат направляется в стабилизационную колонну К-1. Часть ВСГ, смешиваясь с ВСГ риформинга, поступает на прием циркуляционного компрессора, а затем в тройник смешения с сырьем перед входом в теплообменник Т-2.
Гидрогенизат из сепаратора С-102, пройдя теплообменник Т-2, поступает в среднюю часть колонны К, на верх которой подается орошение из газосепаратора. Сверху колонны К-1 удаляется легкая часть сырья вместе с летучими продуктами реакции, которая, пройдя воздущный конденсатор-холодильник АВО-101/1,2 собирается в газосепараторе, из верхней части которого сухой газ сбрасывается на факел, а вода из нижней части по мере ее накопления - в закрытую канализационную систему. Стабильный гидрогенизат с низа колонны К-1 через ребойлер Т-3 поступает в систему каталитического риформинга.
Технологическая схема узла с колонной представлена на рисунке 1.1
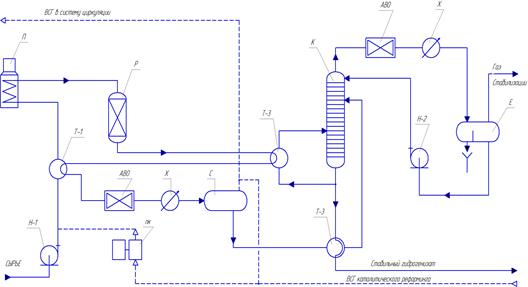
Рисунок 1.1 – Технологическая схема узла с колонной
3 Проектировочный расчет теплообменного аппарата
3.1 Обоснование и выбор исходных данных для расчета теплообменного аппарата
При проектировочном расчете определяется тип теплообменного аппарата и его выбор по каталогу. Чтобы произвести расчет требуются исходные данные.
В качестве исходных данных служат сведения о потоках в трубном и межтрубном пространствах, которые представлены в таблице 3.1.
Таблица 3.1 – Исходные данные для расчета теплообменника
Трубное пространство | Межтрубное пространство | |||||||
tвх1, С | tвых1, С | G1, кг/с | Среда | tвх2, С | tвых2, С | G2, кг/с | Среда | |
136 | 186 | 25 | гидрогенизат | 280 | 195 | 14,54 | гидрогенизат |
Исходными данными для расчета теплообменного аппарата являются температуры теплоносителей и их расходы, причем достаточно знать расход только одного теплоносителя, а второй определится на основании уравнения теплового баланса (3.1):

где Q1 – количество тепла, переданное горячим теплоносителем, Дж;
Q2 – количество тепла, полученное холодным теплоносителем, Дж;
η –коэффициент, учитывающий потери в окружающую среду.
136 оС гидрогенизат 186 оС


195 оС гидрогенизат 280 оС
Физико-химические характеристики для амина при средних температурах, которые определяются следующим образом
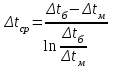
где Δtб и Δtм – соответственно большая и меньшая разность температур между горячим и холодным теплоносителями в процессе теплообмена, С, а если отношение

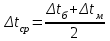
Подставив, получаем следующие значения
Δtб =280 - 186 =94С,
Δtм =195- 136=59 С,
- для межтрубного пространства
Тср=(136+186)/2=161 С,
- для трубного пространства
Тср=(280+195)/2=237С.
Таким образом
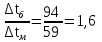


По средним температурам определяем физико-химические свойства сред с учетом расчетного давления и сводим в таблицу 3.2.
Распишем уравнение (3.1)

Подставляем исходные данные и определяем неизвестное значение


Вносим полученное значение в таблицу 3.2.
Физико-химические свойства сред рассчитаны и приведены в таблице 3.2.
Таблица 3.2 – Физико-химические характеристики сред при средней температуре
Параметр | (трубное пространство) | (межтрубное пространство) |
Фазовое состояние | Жидкость | Жидкость |
Средняя температура, С | 161 | 237 |
Рабочее давление, МПа | 2 | 1,4 |
Плотность, ρ кг/м3. | 675,6 | 650,5 |
Вязкость динамическая, μ Па·с | 0,28·10-3 | 0,26·10-3 |
Вязкость кинематическая, ν м2/с. | 0,41·10-6 | 0.39·10-6 |
Удельная теплоемкость, Ср Дж/(кг·К). | 4320 | 4150 |
Коэффициент теплопроводности, λ Вт/(м·К). | 0,13 | 0,16 |
3.2 Определение поверхности нагрева и предварительный выбор типа теплообменного аппарата по каталогу
Данный теплообменник служит для подогрева сырья в колонну Е-404.
Поверхность теплообменника определяется по формуле
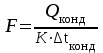
где К – коэффициент теплопередачи, Вт/(м2·К);
Qконд – количество передаваемого тепла, Вт.
Для предварительного выбора теплообменника принимаем К= 250 Вт/м2∙К.
Количество тепла, выделенное теплоносителем, должно быть равно количеству тепла, полученному теплым теплоносителем, т.е.
Q1=Q2. (3.6)
Но так как мы не можем получить идеальную систему без потерь, как тепловых (расход тепла в атмосферу), так и утечек, то величины тепловых потоков различаются на значение коэффициента полезного действия (КПД), его принимают равным η = 0,95. Поэтому (2.6) примет вид
Q2=η∙Q1. (3.7)
Тепловой поток в аппарате вычисляется по формуле
Q1=G1∙Cp1∙Δt, (3.8)
где G1 = 25 кг/с – расход теплоносителя;
Ср 1= 4320 Дж/( кг∙°С) - удельная теплоемкость;
Δt – разность температур на входе и выходе в трубном пространстве, определяется по (3.9), °С
Δt=tвых–tвх. (3.9)
Величины температурных перепадов на концах аппарата Δtб и Δtм:
Δtб =94 °C;
Δtм =59 °C;
Δtср =76,5°C.
Тепловой поток по (2.8) равен
Q1=25∙4320∙(186-136)= 5400000 Вт.
Площадь поверхности теплообмена аппарата рассчитывается по (2.5)
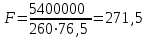
Произведем выбор теплообменника по каталогу.
Основными исходными данными при выборе аппарата является поверхность теплообмена, равная 271,5 м2, температуры теплоносителей на входе и выходе в трубное и межтрубное пространство, а также наименование теплообменивающихся сред.
По рабочему давлению и максимальной температуре определим условное давление Pу мтр =2,5 МПа и Pу тр =2,5 МПа.
В данном случае рассматриваем кожухотрубчатые теплообменные аппараты. Учитывая, что средний перепад температур на концах теплообменного аппарата 76,5°С – выбираем теплообменный аппарат с U- образными трубками.
Данным условиям соответствует теплообменник типа ТУ с поверхностью теплообмена 274,5 м2.
Теплообменный аппарат типа ТУ имеет следующие размеры:
- Dв = 800 мм – внутренний диаметр кожуха;
- dн × Sтр= 20 × 2 мм – наружный диаметр и толщина стенок трубок;
- lт = 6000 мм – длина трубок;
- поверхность теплообмена при длине прямого участка труб F=274,5 м2;
- площадь проходного сечения одного хода по трубам fтр=0,0703 м2;
- площадь проходного сечения по межтрубному пространству fмтр=0,088 м2.
Условное обозначение:
800ТУ-2,5-М1/20Г-2-6-У-И по ТУ 3612-023-00220302-01.
3.3 Уточненный расчет поверхности теплообмена и окончательный
выбор типа теплообменного аппарата
При уточненном расчете определяется общий коэффициент теплопередачи К, который определяется по следующему выражению
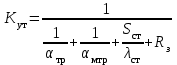
где αтр и αмтр– коэффициенты теплоотдачи на внутренней и наружной поверхностях трубок;
Sст и λст – толщина стенки и теплопроводность материала. В расчетах принимаем
