Файл: Курсовой проект по дисциплине Технологическое оборудование.docx
ВУЗ: Не указан
Категория: Не указан
Дисциплина: Не указана
Добавлен: 26.04.2024
Просмотров: 45
Скачиваний: 0
ВНИМАНИЕ! Если данный файл нарушает Ваши авторские права, то обязательно сообщите нам.
СОДЕРЖАНИЕ
1.2 Аппаратурное оформление узла
2.1 Описание технологической схемы и оборудования блока
3 Проектировочный расчет теплообменного аппарата
3.4 Разработка эскиза теплообменного аппарата
3.5 Сводная таблица по результатам расчетов теплообменного аппарата
4.1 Расчет на прочность элементов теплообменного аппарата
4.2 Подбор штуцера (вход продукта в кожух теплообменника)
12 – крышка подшипника; 13 – прокладка; 14 – масленка; 15 – прокладка; 16 – гайка рабочего колеса; 17 – шайба; 18 – пробка; 19 – набивка сальниковая; 20 – втулка
защитная; 21 – прокладка; 22 – крышка сальника; 23 – отбойник; 24 – вал;
25 – шпонка
Рисунок 1.3 – Разрез насоса
По величине подачи можно выделить насосы малой (до 100 м3/ч), средней (от 100 до 1000 м3/ч) и большой (свыше 1000 м3/ч) подачи. На рисунке 4 показана схема работы центробежного насоса и его основные элементы.
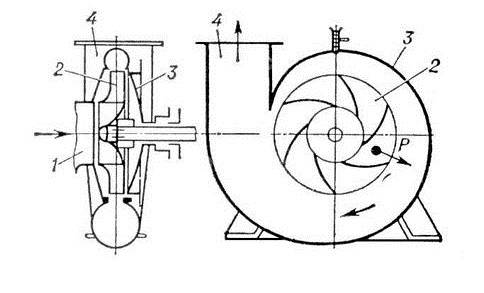
1 – подвод, 2 – концевое уплотнение, 3 – рабочее колесо,4 – отвод
Рисунок 1.4 – Схема работы центробежного насоса и его основные элементы
Принцип работы центробежного насоса состоит в следующем. Жидкость из подводящего трубопровода или непосредственно из резервуара по подводу 1 поступает к рабочему колесу 3, которое вращается приводом насоса. Попадая во вращающиеся каналы рабочего колеса, жидкость получает приращение энергии, в результате чего возрастают ее давление и скорость. Попадая в отвод, жидкость отводится от рабочего колеса, и в расширяющихся каналах (диффузоре) поток замедляется, в результате чего давление жидкости повышается. Из диффузора жидкость подается в напорный трубопровод и поступает в систему. Вал насоса на выходе из корпуса уплотнен концевым уплотнением 2 [8].
1.2.4 Емкостное оборудование
Для хранения нефти, газа и нефтепродуктов на нефтеперерабатывающих заводах применяется большое число емкостей, сосредотачиваемых в резервуарных парках.
В зависимости от назначения хранимого продукта отличают сырьевые, промежуточные и товарные резервуарные парки. Сырьевые и товарные парки сооружают обособленно, вдали от технологических установок, промышленных и бытовых зданий. Парк резервуаров промежуточных продуктов размещают вблизи тех установок, в которых эти продукты используются.
В большинстве случаев сырая нефть хранится в крупных подземных или полуподземных железобетонных резервуарах с внутренней металлической облицовкой и без нее. В таких же резервуарах хранят готовые светлые нефтепродукты. Основные преимущества подземных железобетонных резервуаров состоят в экономии металла, в уменьшении потерь сырья вследствие испарения легких фракций от действия солнечных лучей, а также в противопожарных и маскировочных свойствах.
Металлические емкости, как правило, расположены над землей, что обеспечивает простоту их эксплуатации.
Число и объем устанавливаемых емкостей определяют с учетом суточной производительности завода по сырью и по каждому продукту, числа одновременно хранимых нефтепродуктов, а также норм продолжительности хранения сырья и нефтепродуктов [8].
Дли экономии производственных площадей, материала, трудовых затрат при монтаже и эксплуатации проектируют возможно меньшее число емкостей за счет увеличения объема каждой емкости. Размеры выбранных емкостей должны быть согласованы с соответствующими нормалями, в которых указаны полный и полезный объемы, внутренний диаметр, максимальные рабочие давления и температура, максимальная высота налива и другие данные.
Конструкция емкостей определяется множеством факторов, однако основными являются химические и физические свойства, а также давление и температура находящихся в них жидкостей и газов.
Сжиженные газы (пропан, бутан и др.) и легкие фракции бензина хранят в горизонтальных или вертикальных цилиндрических пустотелых аппаратах, устанавливаемых на фундаментах или постаментах. В таких же емкостях, часто называемых монжусами, хранят химически активные вещества; в этом случае внутренние поверхности аппарата покрывают антикоррозионной облицовкой. Емкостное оборудование представлено на рисунке 1.5.
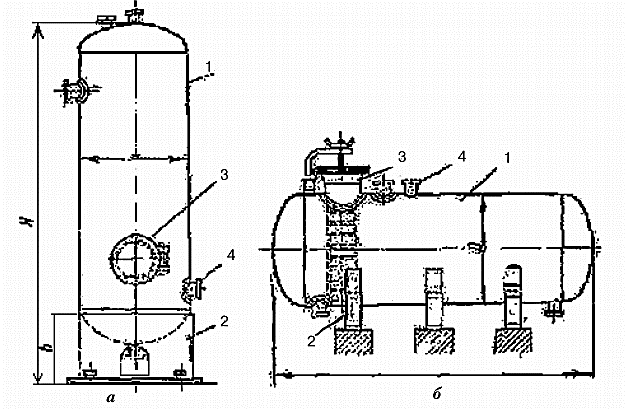
а – вертикальный; б – горизонтальный;
1– корпус; 2 – опора; 3 – люк; 4 – штуцера
Рисунок 1.5 – Емкостное оборудование
Горизонтальные емкости диаметром более 1,4 м внутри у люка снабжают стремянкой для спуска людей. Они должны быть оборудованы также измерительными, регулирующими и предохранительными устройствами, предотвращающими превышение давления, температуры и высоты заполнения выше допустимых значений. Соответствующие лестницы и площадки обеспечивают свободный доступ обслуживающего персонала к арматуре, измерительным, контрольным приборам и предохранительным устройствам. Для предохранения от нагрева солнечными лучами емкости окрашивают снаружи в белый цвет, а в случае необходимости создают теневую защиту [7, 8, 9].
1.3 Патентная проработка
Изобретение [14] относится к нефтеперерабатывающей промышленности и может быть использовано для очистки дизельных фракций. Настоящее изобретение относится к способу гидрообработки дизельного дистиллята путем ректификационной подачи, в котором он разделяется на легкие и тяжелые дизельные фракции. После смешивания тяжелой дизельной фракции с водородсодержащим газом она направляется в верхнюю часть реактора гидрообработки и проходит через слой катализатора из алюминия, никеля, молибдена или алюминия, кобальта и молибдена вместе с теплоносителем при высокой температуре и высоком давлении. Высота слоя катализатора вводит фракцию в реактор гидрообработки в одной или нескольких точках, а точка введения теплоносителя находится между 10 % и 50 % по объему подачи катализатора вдоль подачи.
Техническим результатом является обеспечение необходимой чистоты сырья и контроля температуры в зоне реакции.
Известен способ гидроочистки дизельных фракций путем контактирования сырья и водородсодержащего газа при повышенной температуре и давлении через слой катализатора. В этом случае сырье подается как в верхнюю часть реактора, так и в несколько точек по высоте реактора в слое катализатора. Эта технология позволяет успешно решить проблему удаления избыточного тепла из реакции гидроочистки, поскольку некоторое количество дополнительного сырья, подаваемого по высоте реактора, можно использовать в качестве теплоносителя.
Однако существенным недостатком известного способа является то, что часть сырья (20 % свежего сырья) поступает не на вход реактора, а на высоту 10 %, 20 %, 30 % и 40 % от высоты нанесенного слоя катализатора. 40 %), поэтому степень очистки сырья, как правило, снижается. Что сокращает время контакта между частью сырья и катализатором.
Наиболее близким к заявляемому способу является способ гидроочистки прямогонного дизельного дистиллята [14] или его смеси с вторичным продуктом путем контактирования сырья с водородсодержащим газом (HSG) через гранулированный слой катализатора. Гидрообработку проводят при температуре 340-400 °С, давлении 2,8-5,5 МПа, объемной скорости подачи 3-5 ч-1 и соотношении водородсодержащий газ/сырье 200-500 н.об./об. Одна или три точки по высоте слоя,
загружаемого в каталитический реактор, используются в качестве дополнительного водородсодержащего газа. В этом случае водородсодержащий газ используется в качестве теплоносителя для обеспечения необходимого распределения температуры по всей площади реактора.
Недостатком этого способа являются большие энергозатраты на процесс гидрообработки, связанные с дополнительным расходом водородсодержащего газа.
Изобретение [15] относится к способу гидроочистки дизельного топлива и может найти применение в нефтеперерабатывающей промышленности. Настоящее изобретение относится к способу гидроочистки дизельного масла, включающему фракционирование прямогонного дизельного масла для получения дизельного топлива с легкой и тяжелой фракцией, а затем сравнение полученного в двух реакторах в присутствии водородсодержащего газа в двух реакторах. Легкие и тяжелые фракции дизельного масла отдельно каталитически подвергают гидроочистке, чтобы отделить водородсодержащий газ от гидрида и смешать гидрид. Граница между легкой и тяжелой фракциями дизельного топлива определяется путем анализа содержания отдельных органических соединений серы в исходном дизельном топливе. Легкая фракция в основном содержит моноциклический сульфид и тиофен, а тяжелая фракция в основном содержит бициклический тиофен и Ассоциированный сульфид. Допустимая глубина каталитической гидрообработки легких и тяжелых дизельных топлив ограничена оптимальной концентрацией и скоростью обычной реакции гидрогенизации органического компонента серы для каждой фракции, которую легко и сложно гидрировать, так что общее количество двух реакторов Количество катализатора сведено к минимуму.
Технический результат заключается в снижении энергозатрат на подготовку сырья для гидрообработки и формировании оптимальной границы для разделения сырья на легкие и тяжелые фракции при одновременном уменьшении объема катализатора в реакторе.
Изобретение [16] относится к теплотехнике и может быть использовано в энергетической, нефтехимической, пищевой и других отраслях промышленности. Задачей настоящего изобретения является создание элемента кожухотрубного теплообменника, имеющего трубчатые пластины и теплообмен, который характеризуется. Теплообменная трубка после прямого участка короткой технологии выполнена через спиральную проволоку, диаметр
спиральной проволоки и трубный лист, и имеет свои гидравлические характеристики. Расстояние между дугой угла и выходным отверстием, изменение диаметра трубки и комбинация частичного потока для поддержания соотношения I/de и выравнивания трубки от входа до центра оси. Эффект: теплообмен с использованием рекомендуемого теплообменного элемента. Устройство может увеличить относительно высокую мощность (до 20 %) прямой трубы без снижения надежности и обеспечить большую тепловую мощность при том же размере, тем самым увеличивая мощность нагрева, охлаждения и охлаждения. Скорость и сопоставимы по спиральной тепловой мощности.
Изобретение [17] относится к нефтехимической промышленности и теплотехнике. Кожухотрубчный теплообменник включает в себя: корпус, имеющий встроенную в него поверхность теплообмена в форме прямого трубного пучка, имеющего подвижную нижнюю трубную пластину с коллектором, и для введения И насадка для слива газожидкостной охлаждающей жидкости, расположенная на корпусе. Прямой пучок трубок содержит центральную трубку с наружной кольцевой полостью, закрытой снизу. Верхняя часть трубки с прямыми трубками на стороне конденсатора ограничена фартуковой перегородкой с соплом для выпуска неконденсированного газа наружу корпуса устройства.
Технический результат – повышение надежности работы теплообменника.
Жидкость, давление которой близко к атмосферному давлению, поступает в камеру кипения и нагрева через трубу 4 и центральную трубу 2 и заполняет коллектор 3 тепла. Затем под действием веса собственной колонны жидкость распределяется по трубам прямоточного пучка 1 труб и испаряется в них, а при необходимости нагревается до заданной температуры за счет конденсации и охлаждения конденсата, образовавшегося в затрубном пространстве. Пар, используемый для конденсации в затрубном пространстве, подается через сопло 6, а образующийся конденсат и неконденсируемый газ отводятся через сопла 7 и 7 соответственно. 11. Часть потока конденсата заполняет кольцевую полость 9 и, следовательно, исключает внешнюю поверхность центральной трубы 2 из режима конденсации, что, в свою очередь, не позволяет жидкости кипеть в центральной трубе 2 и поддерживает максимальное рабочее давление в устройстве. Накопленный неконденсирующийся газ из камеры конденсации (ограниченный перегородкой 10) выпускается наружу оборудования. На рисунке 1.6 показана схема разработанного кожухотрубного теплообменника.