Файл: "Проектирование участка механического цеха на базе прерывнопоточной линии в условиях крупносерийного и массового производства".docx
ВУЗ: Не указан
Категория: Не указан
Дисциплина: Не указана
Добавлен: 27.04.2024
Просмотров: 49
Скачиваний: 0
ВНИМАНИЕ! Если данный файл нарушает Ваши авторские права, то обязательно сообщите нам.
Вспомогательные рабочие заняты обслуживанием оборудования, поэтому у них оплата труда по повременно-премиальной системе в зависимости от количества проработанного времени.
Основной фонд заработной платы (Фо) рассчитывается по формуле
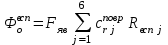
где споврr j - часовая тарифная ставка рабочего-повременщика 2-й группы тарифных ставок соответствующего j-го разряда, руб./ч.
cповрrj=cповr 1Kтар i
где сповr1j - часовая тарифная ставка рабочего-повременщика 1-го разряда, руб./ч.
Величина Ктар j берется из табл.3.
Rвcп j - количество вспомогательных рабочих j-го разряда, чел.
Дополнительный фонд заработной платы вспомогательных рабочих-повременщиков (Фдоп) включает компенсационные выплаты и премиальное вознаграждение за своевременное и качественное обслуживание оборудования. По данным предприятия Тульского региона размер дополнительной заработной платы колеблется от (40...50) % от суммы основного фонда, т.е.
Фвспдоп = (0.4...0.5) Фо.
Таким образом, общий фонд заработной платы вспомогательных рабочих равен Фвспобщ = Фо + Фдоп.
Фонд начислений на социальное обеспечение (Фс.о) для вспомогательных рабочих определяются подобно основным производственным рабочим, т.е.
Фвспс.о = 0.385Фобщ.
7.4. Расчет потребного количества ИТР, служащих, младшего обслуживающего персонала (МОП)
В качестве ИТР принимаем сменного мастера, из расчета один сменный мастер не менее на 25 рабочих, т.е. на каждую смену по мастеру. Рекомендации по определению количества ИТР даются также в [4,9].
В качестве служащего выбирается нормировщик или учетчик-нарядчик из норматива: один нормировщик - на 40 рабочих-сдельщиков; один учетчик-нарядчик - на 75 рабочих-сдельщиков.
Принимаем одного учетчика-нарядчика.
По рекомендации [1,4,9] количества МОП определяется из расчета (2...3)% от сумму количества основных и вспомогательных производственных рабочих.
Rмоп = (0.02...0.03)(Rосн + Rвсп
).
7.4.1. Определение фонда заработной платы ИТР, служащих и МОП
Основной фонд заработной платы рассчитывается единообразно по формуле (на примере ИТР)
Фитро = ДитрокqКн.рRитр
где Дитрок - должностной месячный оклад (ставка), руб./мес;
q - количество месяцев в году;
Кн.р - коэффициент, учитывающий невыходы на работу по болезни. Рекомендуется [1,4] принимать Кн.р = 0.97;
Rитр - количество ИТР, чел.
Дополнительный фонд составляет 50 % от основного фонда зарплаты.
Фитрдоп = 0.57Фо.
Таким образом, общий фонд заработной платы (Фитробщ) будет равен
Фитробщ = Фитро + Фитрдоп.
Фонд начислений на социальное обеспечение Фитрс.о находится аналогично рабочим: Фитрс.о = 0.385 Фитробщ.
Подобным образом рассчитывается фонд заработной платы служащих и МОП, только дополнительный фонд у служащих составляет 40%, а у МОП - 30%.
8. Расчет потребного количества режущего и мерительного инструмента
8.1. Расчет режущего инструмента
Для i-й операции ведется по формуле [12]:

где Nвып - годовая программа, шт;
Тмаш i - норма машинного времени на i-ю операцию, мин;
Куб i - коэффициент убыли инструмента на i-й операции. Выбирается по [3,12,13];
Тизн i - расчетное время до полного износа инструмента на i-й операции, ч. Принимается по [3,12,13].
Для рассматриваемого в курсовой работе примера расчетные данные сводятся в табл.7.
Таблица 7
Ведомость расчета количества режущего инструмента
Наименование операции | Наименование инструмента | Тмаш, мин | Тизн, ч | Куб | Ареж i, шт |
1.Центрирование | Сверло ![]() | 0.73 | 11 | 1.10 | 246 |
2.Черновое точение шейки | Резец проходной 12*20 | 1.12 | 19 | 1.15 | 230 |
3.Черновое обтачивание | Резец проходной 12*20 | 2.16 | 19 | 1.15 | 447 |
4.Сверление отверстия | Сверло ![]() | 1.32 | 11 | 1.10 | 447 |
5.Черновая обработка цилиндрической поверхности | Резец 16*24 | 3.95 | 9 | 1.15 | 1710 |
6.Чистовая обработка цилиндрической поверхности | Резец 16*24 | 1.93 | 18 | 1.15 | 417 |
7.Шлифование | Шлиф.круг ![]() | 0.42 | 43 | 1.10 | 37 |
8.Нарезание резьбы | Гребенки дисковые | 0.92 | 61 | 1.05 | 54 |
Примечание: если Куб выбирается по [3], то к выбранному значению необходимо прибавить единицу, т.е. (Куб+1).
8.2. Расчет мерительного инструмента
Определяется на i-й операции по формуле [12]:

где аi - число промеров данным инструментом при изготовлении одной детали на i-й операции;
Кизн i - износостойкость мерительных инструментов до полного износа на i-й операции. Выбирается по [12].
Расчетные данные для рассматриваемого примера сводим в табл.8.
Таблица 8
Ведомость потребности в мерительном инструменте на годовую программу
Наименование операции | Наименование инструмента | Кизн | а | Амер i, шт |
1.Центрирование | Пробка | 20.8 | 2 | 20 |
2.Черновое точение шейки | Скоба 40.5 | 84.6 | 1 | 3 |
3.Черновое обтачивание | Скоба 31.0 | 84.6 | 1 | 3 |
4.Сверление отверстия | Пробка ![]() | 20.8 | 1 | 10 |
5.Черновая обработка цилиндрической поверхности | Скоба 20.5 | 84.6 | 2 | 5 |
6.Чистовая обработка цилиндрической поверхности | Скоба 30.5 | 84.6 | 2 | 5 |
7.Шлифование | Скоба 49 | 84.6 | 1 | 3 |
8.Нарезание резьбы | Резьб.кольцо М 20*1.5 | 5.5 | 1 | 37 |
Примечание: количество мерительного инструмента можно рассчитать по [13], но в этом случае расчетная формула (20) имеет другой вид.
9. Разработка планировки участка
Планировка участка представляет собой план расположения технологического оборудования, подъемно-транспортных средств и рабочих мест. Планировка поточных линий изображается в виде прямых (односторонних и двухсторонних) линий. Наиболее часто встречаются прямые линии, у которых станки располагаются по одну сторону (односторонние) и по обе стороны от него (двухсторонние). В массовом и крупносерийном производстве станки располагаются в порядке следования технологических операций с указанием на них номера операции и минимально допустимых расстояний между ними [2,3]. Не допускается при этом возвратнопоступательных движений обрабатываемой детали. Контуры станков вычерчиваются по крайним выступающим частям. Каждый тип станка должен иметь свое графическое изображение, которое берется в [2,3] или прилож.1. Планировка выполняется в масштабе 1:100 (как исключение в курсовой работе допускается 1:50). На ней необходимо предусмотреть места для размещения межоперационных оборотных заделов (если
их скопление у станка достаточно велико и площадь их складирования может быть изображена в принятом масштабе планировки) и рабочего столика (тумбочки) станочника. При размещении оборудования следует руководствоваться нормативными размерами промежутков между станками в продольном и поперечном направлениях, от стен и колонн зданий [2,3,14].
При проектировании механических цехов рекомендуется применять стандартную сетку колонн здания: 6*12, 12*12 и реже 12*18 м. Станки на поточной линии могут располагаться поперек, вдоль пролета и под углом (25...45) к нему. Под углом рекомендуется располагать следующие типы станков: револьверные, протяжные, продольно-фрезерные, продольно-шлифовальные, продольно-строгательные. Место рабочего у станка обозначается на планировке кружком диаметром 5 мм (в масштабе 1:100). Половина этого кружка закрашивается, причем светлая часть его должна быть обращена к станку. Ширина рабочей зоны между выступающей частью станков, расположенных на фронтальной линии и транспортным конвейером должна составлять 800 мм.
Если участок расположен вдоль пролета цеха и по ширине он не занимает весь пролет, то на планировке от крайней выступающей точки станка на расстоянии 800 мм проводят волнистую линию, которая условно считается границей проектируемого участка и служит для определения производственной площади, занимаемой этим участком.
Производственная площадь участка определяется по формуле
Sуч = L H, м2 (21)
где L - длина участка на планировке с учетом масштаба, м;
Н - ширина участка, м.
На планировке условно, размером 1.5*2 м, показываются рабочие места вспомогательных рабочих: слесарей, электриков и наладчиков, которые располагаются у стены (колон) или других свободных местах участка. Рабочее место контролера изображается тем же размером, но в конце поточной линии после последней по технологии операции. Кроме этого, в начале поточной линии показывают место заготовок, а в конце - место готовых деталей.
10. Выбор подъемно-транспортных средств [2,3]
К транспортным средствам, применяемым для межоперационной транспортировки деталей на поточной линии относятся конвейеры различных типов. Приводные конвейеры наиболее полно отвечают требованиям поточного производства. На участках механической обработки деталей наибольшее распространение получили ленточные, пластинчатые, подвесные цепные конвейеры и рольганги [3]. Ленточные и пластинчатые конвейеры обычно используются при транспортировке деталей меньше 10 кг, а подвесные цепные конвейеры и рольганги - при весе детали более 10 кг.
Ленточные конвейеры имеют в качестве тягового органа прорезиненную ленту, на которой (иногда) закрепляются специальные гнезда для деталей. Наибольшее распространение получили ленточные конвейеры с шириной ленты от 200 до 600 мм. Рабочая скорость конвейера колеблется от 5 до 20 м/мин [2].
Пластинчатые конвейеры также имеют широкое применение. Ширина их настила колеблется от 400 до 800 мм, а рабочая скорость от 1 до 5 м/мин.
На участках механической обработки деталей наибольшее распространение получили подвесные цепные конвейеры, представляющие собой замкнутое тяговое устройство в виде цепи, несущей подвески для грузов. Такие конвейеры используются не только для передачи деталей от одного рабочего места к другому, но и для транспортировки обработанных деталей в другие цехи и участки. Рабочая скорость такого конвейера колеблется от 0.1 до 1 м/мин.
Для того, чтобы выбрать нужный вид конвейера необходимо по планировке определить минимальный шаг между двумя смежными подвесками (lmin).
Для этого на планировке, выполненной в масштабе, нужно найти минимальное расстояние по осям смежных станков на поточной линии.