Файл: Контрольная работа должна включать Титульный лист Лист задания Содержание Анализ технических требований.docx
ВУЗ: Не указан
Категория: Не указан
Дисциплина: Не указана
Добавлен: 04.05.2024
Просмотров: 26
Скачиваний: 0
ВНИМАНИЕ! Если данный файл нарушает Ваши авторские права, то обязательно сообщите нам.
Обоснование выбора баз
При выборе технологических баз необходимо соблюдать ряд принципов.
-
Выбирать такую схему базирования, которая обеспечит наименьшую погрешность установки. -
Соблюдать принцип совмещения баз – совмещать конструкторскую, технологическую и измерительную базы. -
Стремиться к соблюдению принципа постоянства баз – на различных операциях механообработки использовать одни и те же базы (поверхности) обрабатываемой детали.
Кроме этого необходимо помнить, что нельзя использовать дважды (и более) в качестве баз «черные» (необработанные) поверхности заготовки. При этом в случае использования в качестве баз «черных» поверхностей, приоритет отдается тем поверхностям, которые после изготовления детали остаются не обработанными. Поэтому на первой операции всегда идет подготовка технологических баз под последующую обработку.
Изначально будут обрабатываться поверхности 13…17. В качестве базы примем необработанную поверхность заготовки (рисунок 1).
Для дальнейшей обработки необходимо обработать торец 2 и просверлить центровое отверстие (рисунок 3), которое будет использоваться в качестве базовой поверхности на последующих операциях.
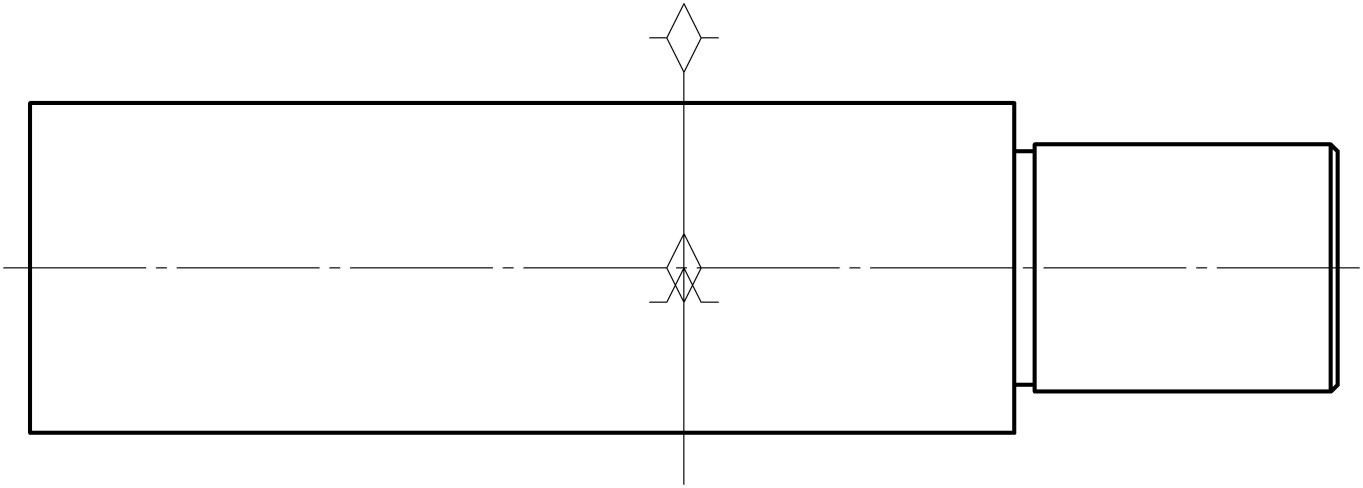
Рисунок 2
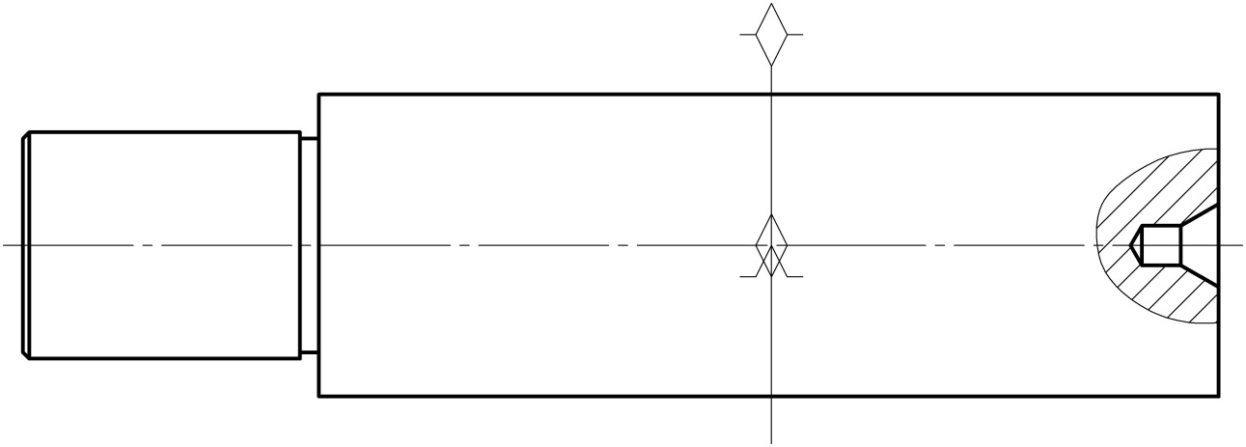
Рисунок 3
Для обработки всех остальных поверхностей (кроме шпоночного паза, отверстий) примем поверхность 15 и центровое отверстие.
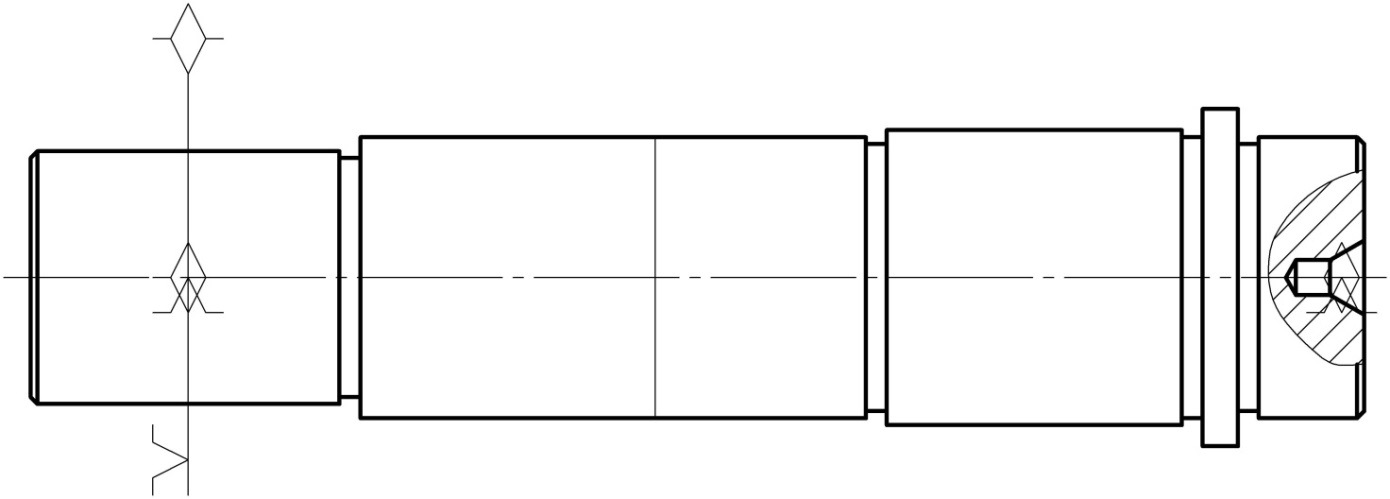
Рисунок 4
Для окончательной обработки поверхности 15 в качестве базы примем поверхности 3 и 12.
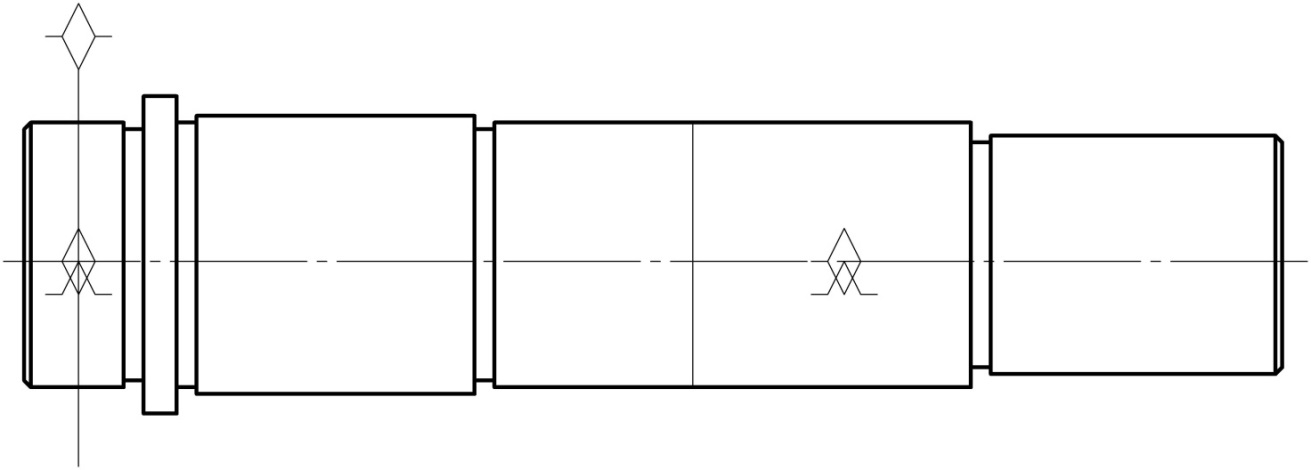
Рисунок 5
Для обработки шпоночного паза и отверстий в качестве баз примем поверхности 3, 5, 11.
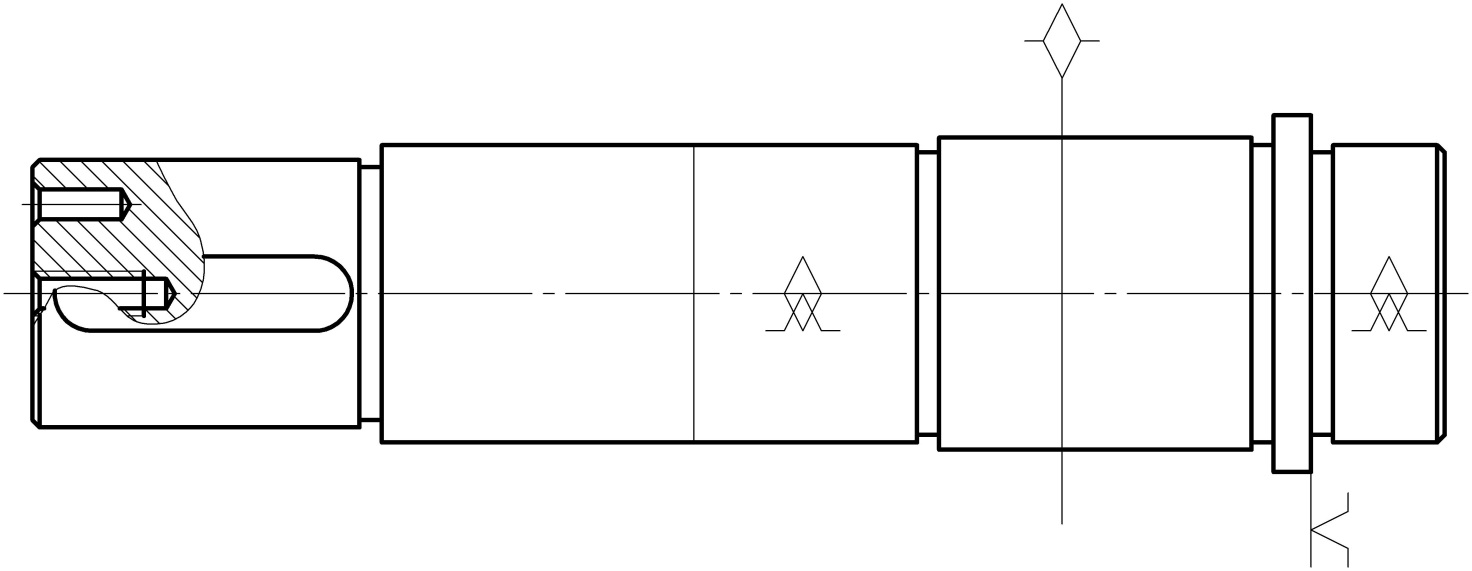
Рисунок 6
-
Разработка и обоснование маршрутного единичного перспективного технологического процесса
Обоснование маршрута обработки заготовки выполняется на основании сопоставления различных вариантов последовательности выполнения операций и схем установки заготовки.
Так как практически невозможно (за редким исключением) полностью обработать заготовку на одном станке, то возникает необходимость дифференциации обработки на ряд операций. Поэтому при построении маршрута необходимо синтезировать обработку по группам оборудования (токарная, фрезерная, сверлильная, шлифовальная и др.), разделяя обработку на черновую, чистовую и отделочную. Причиной дифференциации технологического процесса являются, также, чередование видов механической обработки и прерывание её другими видами воздействия на заготовку – термообработка, старение, нанесение различных видов покрытия, технический межоперационный контроль и т.д.
Составим маршрутный технологический процесс с учётом того, что тип производства серийный; заготовка – круглый прокат обычной точности.
Таблица 4 – Маршрутный технологический процесс
№ операции | Наименование | Содержание операции |
005 | Заготовительная | Отрезка заготовки на необходимую длину. |
010 | Токарная | Обработка поверхностей 2, 13…17, сверление центрового отверстия |
015 | Токарная с ЧПУ | Обработка остальных поверхностей, кроме паза и отверстий |
020 | Термическая | Обработка поверхностей 2…6 |
025 | Шлифовальная | Окончательная обработка поверхности 15 |
030 | Шлифовальная с ЧПУ | Окончательная обработка поверхностей 3, 5, 9, 11, 12 |
035 | Фрезерно-сверлильная | Обработка паза и отверстий |
040 | Контрольная | Контроль размеров и требования по чертежу детали |
Необходимо определить размеры заготовки.
-
Расчёт длины заготовки.
Припуски на обработку торца [1, с.188]:
на черновую – 1,5 мм;
Длина заготовки: 190 + 1,52 = 193 мм.
Примем длину заготовки L = 193±0,5 мм.
-
Расчёт диаметра проката.
Диаметр проката будем определять по наибольшему диаметру детали Ø48 мм (поверхность 6).
Припуски на точение (на диаметр) [1, с.193]:
черновое – 1,6 мм;
получистовое – 0,45 мм.
Диаметр проката: 48 + 1,6 + 0,45 = 50,05 мм.
Примем размер проката по ГОСТ 2590-2006: Ø

- 1 2 3 4 5 6
Выбор оборудования, приспособлений, режущего и измерительного инструмента
При выборе оборудования учитывают следующие факторы: точность станков; размеры рабочей зоны; производительность; прочность, жесткость и кинематические возможности станков; возможность механизации и автоматизации обработки, простота обслуживания. Выбор оборудования выполняют по паспортным данным станков, ориентируясь на информацию в справочной литературе.
Станок 8В242 – автомат абразивно-отрезной. Станок предназначен для отрезания абразивными кругами с охлаждением и без охлаждения проката черных и цветных металлов различных профилей в заготовительных цехах машиностроительных предприятий.
Таблица 5 – Технические характеристики станка 8В242
Класс точности станка по ГОСТ 8-82 (Н,П,В,А,С) | Н |
Длина проката, поступающего на разрезку, мм | 1000…6000 |
Наибольший диаметр заготовки, мм | 60 |
Длина отрезаемой заготовки наибольшая, мм | 1000…1600 |
Диаметр диска не более, мм | 400 |
Частота вращения шпинделя, об/мин | при скорости резания 100 м/с 4726 при скорости резания 80 м/с 3820 при скорости резания 50 м/с 2410 |
Мощность, кВт | 30 |
Габариты, мм | 1200_2770_1800 |
Масса, кг | 4500 |
Станок 16Б16 – станок токарно-винторезный, предназначен для выполнения разнообразных токарных работ в центрах или патроне, а также для нарезания метрических, модульных, дюймовых и питчевых резьб. Установка заготовок осуществляется в патроне, а длинных – в центрах.
Таблица 6 – Технические характеристики станка 16Б16
Наибольший диаметр детали обрабатываемой над станиной, мм | 360 |
Наибольший диаметр детали обрабатываемой над суппортом, мм | 180 |
Наибольшая длина обрабатываемой детали, мм | 750 |
Число ступеней частот прямого вращения шпинделя | 21 |
Пределы частот вращения шпинделя Min/Max, об/мин. | 20…2000 |
Пределы продольных подач, мм/об | 0,05...2,8 |
Пределы поперечных подач, мм/об | 0,025...1,4 |
Число ступеней продольных и поперечных подач | 24 |
Мощность, кВт | 7,1 |
Габариты, мм | 2150×1000×1430 |
Масса, кг | 1800 |
Токарный станок с ЧПУ 16А20Ф3 предназначен для токарной обработки деталей типа тел вращения в замкнутом полуавтоматическом цикле. Станок оснащен электромеханическим приводом зажима патрона, перемещения пиноли задней бабки и транспортером стружкоудаления. Область применения станка – мелкосерийное и серийное производство.
Таблица 7 – Технические характеристики станка 16К20Ф3
Диаметр обработки над станиной, мм | 500 |
Диаметр обработки над суппортом, мм | 200 |
Наибольшая длина обработки в центрах, мм | 1000 |
Наибольший поперечный ход суппорта, мм | 210 |
Наибольший продольный ход суппорта, мм | 905 |
Дискретность задания перемещения, мм | 0,001 |
Пределы частот вращения шпинделя, мин-1 | 12,5…2000 |
Количество позиций инструментальной головки | 8 |
Мощность электродвигателя главного движения, кВт | 11 |
Габаритные размеры станка (Д х Ш х В), мм | 3700×2260×1650 |
Масса станка, кг | 4000 |
Станок 3М151 – станок круглошлифовальный. Круглошлифовальный полуавтомат 3М151 предназначен для наружного шлифования цилиндрических и конических поверхностей изделий в условиях единичного, серийного и крупносерийного производства.
Таблица 8 – Технические характеристики станка 3М151
Наибольший диаметр обрабатываемого изделия, мм | 200 |
Наибольшая длина обрабатываемого изделия, мм | 700 |
Диаметр шлифования, min / max, мм | 10…200 |
Наибольшая длина шлифования, мм | 700 |
Шлифовальный круг по ГОСТ 2424-67 | ПП600х80х305 |
Наибольшая высота устанавливаемого круга, мм | 100 |
Частота вращения шпинделя шлифовальной бабки, об/мин | 1590 |
Скорость резания шлифовального круга, м/с | 50 |
Частота вращения изделия (бесступенчатое регулирование) | 50...500 об/мин |
Мощность главного электродвигателя станка, кВт | 10 |
Габаритные размеры станка (длина х ширина х высота), мм | 4605х2450х2170 |
Масса станка с электрооборудованием и охлаждением, кг | 5600 |