ВУЗ: Не указан
Категория: Не указан
Дисциплина: Не указана
Добавлен: 16.03.2024
Просмотров: 88
Скачиваний: 0
ВНИМАНИЕ! Если данный файл нарушает Ваши авторские права, то обязательно сообщите нам.
СОДЕРЖАНИЕ
Рисунок 41 Шахтный хлоратор непрерывного действия:
1-водоохлаждаемый конус; 2 - фурма; 3 -хлорный коллектор; 4 - корпус хлоратора; 5 -волдохлаждаемый свод; 6 - бункер; 7 - золотниковый питатель; 8 - редуктор; 9 - электродвигатель; 10 - сборник огарка; 11 - разгрузочный шнек.
В печах подобного типа можно хлорировать шлаки с низким суммарным содержанием СаО и МgО (не выше 4-5 %). При (более высоком содержании образующиеся жидкие хлориды CaCl2 и МgС12 приводят к слипанию брикетов и нарушению схода шихты вдоль шахты печи.
Расход хлора составляет 0,85-0,9 т на 1 т тетрахлорида титана, что выше теоретического расхода (
0,75 т хлора) вследствие затрат хлора на хлорирование соединений примесей. В хлоратор подается анодный газ магниевых электролизеров, содержащий
85-90 % хлора или испаренный хлор из цистерн с жидким хлором.
При температурах 900-1000 °С хлорирование брикетов протекает во внешне диффузионной области, т.е. скорость процесса определяется скоростью подачи хлора. Энергия активации процесса хлорирования
12-16 кДж/моль ТiO2. Брикет приведенного выше размера полно хлорируется за 3-3,5 ч.
При принятых режимах хлорирования процесс протекает за счет теплоты реакций. При расходе хлора
400 кг/(м2 • ч) высота реакционной зоны, в пределах которой концентрация хлора изменяется примерно от начальной вблизи фурм практически до нуля (у верхней границы зоны), равна 0,8-1,0 м.
Удельная производительность шахтных хлораторов непрерывного действия при температурах хлорирования 900-1000 °С равна 1,8-2 т ТiС14 на 1 м3 объема хлоратора.
Повышение единичной мощности шахтного хлоратора путем увеличения его диаметра нецелесообразно, так как возрастает неравномерность схода шихты (центральная часть брикета перемещается быстрей периферийной) и неоднородность температурного поля по его сечению (у стен температура выше вследствие неравномерности распределения хлора).
Отношение по массе СО:СО2 в парогазовой смеси, выходящей из хлоратора, колеблется (в зависимости от режима) от 5:1 до 2:1.
Рисунок 42 Хлоратор для хлорирования в солевом расплаве:
Недостаток хлорирования брикетированной шихты - высокие затраты на приготовление брикетов, что повышает 10-15 % себестоимость хлорида; взрывоопасность отходящих газов, в которых преобладает СО.
1 - газоход; 2 - свод; 3 -графитовый электрод; 4 -стальные трубы для отвода тепла; 5 - кожух хлоратора; 6 -шамотная футеровка; 7 - бункер с шихтой; 8 - шнековый питатель; 9 - перегородка для создания циркуляции расплава; 10 - фурма; 11,12 - донные графитовые электроды; 13 -нижний слив расплава
Хлорирование в солевом расплаве. Этот способ разработан в СНГ. Хлорирование шлака проводится в ванне из расплава хлоридов щелочных и щелочно-земельных металлов, куда подают компоненты шихты (измельченные шлак и кокс) и хлор. В качестве расплава используют отработанный электролит магниевых электролизеров, имеющий следующий примерный состав, %: КС1 72-76; NаС1 14-16, МgС12 4-6. Шихта подается шнеком на поверхность расплава, хлор поступает в нижнюю часть хлоратора через фурмы и газораспределительную решетку (рис. 42). При удельном расходе хлора 40-60 м3/ч на 1 м3 расплава обеспечивается хорошее перемешивание его барботирующим хлором. В расплаве поддерживают концентрацию ТiO2 2-3 %, углерода 7-9 %. При высоте расплава 3-3,2 м хлор успевает полностью прореагировать в объеме расплава, лишь незначительная часть его уходит с отходящимися газами.
Необходимая температура расплава (800 - 850 oС) поддерживается за счет тепла экзотермических реакций. Избыточное тепло отводится с помощью установленных в стенке хлоратора кессонов из графитовых плит, в которые вмонтированы стальные трубы, куда подается вода.
В процессе хлорирования в расплаве накапливаются нелетучие хлориды (MgCl2, СаС12, а также FeCl2 и FeCl3 в форме комплексов KFeCl3 и KFeCl4 и др.). Периодически часть расплава выпускают и в хлоратор заливают свежий расплав. Отработанный расплав содержит, %: KCl 30 - 40, NaCl 2 - 5, MgCl2 25 - 35, FeCl2 + FeCl3 + MnCl2 10 - 20, SiO2 3 - 6, CaCl2 2 - 4, С 7 - 9, TiO2 0,5 - 1. В отличие от хлорирования брикетированных шихт в хлораторах с расплавом в составе парогазовой смеси преобладает СO2 [объемное соотношение СO2: СО = (10÷20):1], что объясняется неблагоприятными условиями для взаимодействия СO2 с частицами углерода.
Механизм (стадии) хлорирования диоксида титана в сложной системе, содержащей газовую, жидкую и две твердые фазы (TiO2 и кокс), недостаточно изучен.
Очевидно, что с поверхностью частиц кокса и TiO2, находящихся в расплаве, могут вступать во взаимодействие только растворенные в расплаве хлор, СO2 и СО, так как при хорошем смачивании кокса расплавом его поверхность экранирована жидкой средой от непосредственного контакта с пузырьками газа.
Растворимость хлора, СО и СO2 в расплавах KCl - NaCl - MgCl2 при 800 - 900 oС равна примерно 0,04, 0,02 и 1,5 г/л соответственно. Растворимость TiO2 не превышает 0,05 г/л.
Согласно одной из предложенных схем растворенный хлор хемосорбируется на поверхности частиц углеродистого материала с образованием активного (атомарного) хлора, переносимого через расплав к поверхности оксида, где при участии растворенного СО протекает реакция:
ТiO2 + 4С1акт + 2СО = ТiС14 + 2СО2.
Далее СО2 частично взаимодействует с углеродом с образованием СО. Эта схема объясняет наблюдаемое повышение скорости хлорирования с увеличением удельной поверхности кокса и преобладание СО2 над СО в газовой фазе.
Присутствие хлоридов железа в расплаве повышает скорость хлорирования. Это объясняется хлорирующим действием FеС13, легко отщепляющего активный хлор. Как указано выше, хлориды железа находятся в расплаве в форме комплексов
и
. Поэтому хлорирование ТiO2 с участием хлоридов железа можно представить суммарными реакциями:
+ 2С12 =
; (4.13)
+ ТiO2 + 2СО = ТiС14 +
+ 2СО2. (4.14)
Таким образом, хлориды железа выполняют роль переносчиков хлора.
Поскольку хлориды железа хорошо растворимы в расплаве, концентрация хлорирующего агента будет зависеть от содержания в нем железа. Так, достаточно содержания 1 % FeCl3 в расплаве для существенного увеличения скорости процесса. При нормальной работе хлоратора (без проскока хлора) в расплаве устанавливается отношение FeCl2 : FeCl3 = 20 + 200 (по массе), причем концентрация FeCl2 находится в пределах 15 - 20 %, a FeCl3 0,1 - 1,0 %.
Вследствие образования комплексов большая часть железа (а также алюминия, образующего комплекс КA1Cl4) остается в солевом расплаве.
Основные преимущества хлорирования в солевом расплаве по сравнению с хлорированием брикетов следующие: исключены сложные операции подготовки брикетов, что снижает себестоимость хлорида. Возможно хлорирование шлаков с повышенным содержанием СаО и МgО. Быстрый тепло- и массообмен в расплаве обеспечивает высокую скорость хлорирования и возможность отвода избыточного тепла. Преобладание СО2 над СО в составе газов резко снижает их взрывоопасность.
К недостаткам хлорирования в расплаве следует отнести периодический вывод отработанного расплава (до 200 кг на 1 т ТiС14), с которым теряется часть титана. Хлориды -вредные производственные сбросы. Важная задача - их использование или регенерация с возвратом в процесс.
Пылеулавливание и конденсация хлоридов
Парогазовая смесь, выходящая из хлораторов, имеет сложный состав. Она содержит газы (СО, СО2, СОС12, N2, НС1, С12), низкокипящие хлориды - в нормальных условиях жидкости (ТiС14, SiС14,VОС13 и др.); низкокипящие хлориды - в нормальных условиях твердые (FеС13, А1С13); высококипящие хлориды СаС12, МgС12, FеС12, а также КС1, NаС1 (при хлорировании в расплаве). Высококипящие хлориды механически увлекаются парогазовым потоком в виде тумана.
На рис. 43 приведена распространенная схема пылеулавливания и конденсации. Она состоит из пылевых камер (кулеров) для улавливания твердых хлоридов; рукавного фильтра с рукавами из стеклоткани для дополнительной очистки парогазовой смеси от твердых частиц; двух оросительных конденсаторов (конденсаторов смешения) для жидких хлоридов (ТiС14, SiС14), орошаемых охлажденным тетрахлоридом титана; во втором конденсаторе тетрахлорид, поступающий на орошение, охлаждается до -10 С. Далее газы проходят санитарный скруббер, орошаемый известковым молоком, для улавливания небольших количеств хлора, фосгена, хлористого водорода и выбрасываются в атмосферу. В кулерах газы охлаждаются с 500-600 до 140-180 °С омывающим трубы воздухом. В нижней разгрузочной части кулеров поддерживается постоянная температура (120-130 °С) органическим теплоносителем, циркулирующим в рубашке разгрузочного корыта. Термостатирование рукавного фильтра (140-160 °С) также осуществляется жидким теплоносителем.
РBс.43. Схема раздельной конденсационной системы (пунктиром показан путь циркуляции теплоносителя):
1 - пылевые камеры (кулера); 2 — сборник твердых хлоридов; 5 - рукавный фильтр; 4 – оросительные конденсаторы; 5 - водяной холодильник; 6 - погружной насос; 7 - холодильник, охлаждаемый рассолом до -10 С (раствор СаС12)
Для снятия с рукавов из стеклоткани уловленной пыли производится их отдувка парами тетрахлорида титана.
В связи с осложненностью эксплуатации фильтров с рукавами из стеклоткани на некоторых предприятиях они заменены солевым расплавом NаС1 + КС1. (см. рис. 25). Расплав циркулирует с помощью аэролифтного устройства. Принцип работы солевого фильтра рассмотрен в гл. 2.
Извлечение титана из шлака в жидкий технический тетрахлорид составляет 92-93 %.
Очистка технического тетрахлорида титана
Содержание примесей в техническом ТiС14 колеблется примерно в следующих пределах, % (по массе): Si 0,01-0,3; А1 0,01-0,1; Fе 0,01-0,02; V 0,01-0,3; ТiOС12 0,04-0,5; СОС12 0,005-0,15; С1 0,003-0,08; S 0,01-0,08.
Кроме перечисленных, в хлориде титана часто содержатся примеси хлоридов ниобия, тантала, хрома и примеси органических соединений, например ацетилхлориды (СС13СОС1, СН2ClОСl), гексахлорбензол С6С16 и др.
Хлорид титана очищают от большинства примесей ректификацией, основанной на различии температур кипения хлоридов. Однако ректификации предшествует очистка от примеси ванадия.
Очистка от ванадия. Ванадия содержится в ТiС14 в составе оксихлорида VОС13. Отделение его от ТiС14 ректификацией затруднительно вследствие близости точек кипения ТiС14 и VОС13 (136 и 127 °С соответственно). Все известные методы очистки от ванадия основаны на восстановлении VОС13 до малорастворимого в тетрахлориде титана VОС12. На заводах в качестве восстановителей применяют медные или алюминиевые порошки.
Восстановление медным порошком протекает через стадию
образования СuТlС14:
Сu + ТiС14 = СuТiС14; (4.15)
СuТiС14 + VОС13 = VОС12 + CuС1 + ТiС14. (4.16)
Получаемые медно-ванадиевые осадки содержат, % Тi 6-8; V 4-6; С1
45, остальное - кислород и примеси других элементов. Разработаны схемы извлечения из осадков ванадия и меди.
Вследствие высокой стоимости медного порошка стали применять для восстановления VОС13 порошок алюминия. Последний реагирует с ТiС14 с образованием ТiС13, который затем восстанавливает VОС13:
3 ТiС14 + А1 = 3 ТiС13 + А1С13; (4.17)
ТiС13 + VОС13 = VОС12 +Т1С14. (4.18)
Кроме того, протекает реакция:
ТiOС12 + А1С13 = А1ОСl↓ + Т1С14. (4.19)
Осадок, содержащий VОС12, ТiC13, А1С13, направляется на извлечение ванадия. На некоторых зарубежных заводах для очистки от ванадия применяют восстановление сероводородом или органическими веществами (углеводороды, жирные кислоты и др.).
Очистка ректификацией. Очистку хлорида титана ректификацией проводят в колоннах из нержавеющей стали с дырчатыми тарелками (или тарелками с щелевидными прорезями) в две стадии (рис. 44). На первой стадии отделяют тетрахлорид титана от примеси кремния (температура кипения S1С14 58 °С) и других летучих примесей (СС14, СS2, SОС12 и др.), поддерживая в верхней части колонны температуру паров 132-135 °С и избыточное давление 0,66-4 кПа. Температура в кубе колонны 140-150 °С.
Рисунок 44 Схема установки для очистки тетрахлорида титана ректификацией:
1- напорный бак с ТЛС14; 2 - подогреватель; 3 - ректификационная колонна для отделения низкокипящих хлоридов; 4 - кубы-испарители с электронагревателями 5 (в патроне); 6 - дефлегматоры; 7 - регулирующий клапан; 8 - насос; 9 - кубы-испарители с открытыми нагревателями; 10,11 - ректификационная колонна для дистилляции Т1С14; 12 - распределительный клапан; 13 - сборник очищенного Т1С14
Неконденсируемые газы (СО2, С12, N2, СОС12) выводят из дефлегматора через гидрозатвор в систему очистки газов.
Кубовый остаток, содержащий ТiС14 и примеси высококипящих хлоридов и оксихлоридов (в частности, ТiOС12), поступает во вторую колонну, в верхней части которой поддерживают температуру 134-136 °С (точка кипения ТiС14), в нижней - 137-138 °С. Отбираемый дистиллят - чистый четыреххлористый титан. Примеси высококипящих хлоридов (ТiOС12, FеС13, А1С13, NbС15 и др.) остаются в кубовом остатке.
Очищенный тетрахлорид титана содержит примеси в количествах, близких к пределу чувствительности спектрального анализа (10-3-10-5 %). Извлечение титана из технического в очищенный тетрахлорид титана равно
96 %.
Производство диоксида титана
Сернокислотный способ
Основное количество выпускаемого диоксида титана из ильменитового концентрата (или титановых шлаков) получают сернокислотным способом, который включает следующие стадии:
-
разложение концентрата серной кислотой;
-
очистку растворов от железа;
-
гидролитическое выделение метатитановой кислоты из сернокислотного раствора;
-
прокаливание осадка с получением диоксида титана.
Этот способ обеспечивает высокое извлечение титана в готовый продукт, причем в технологии практически используют один реагент - серную кислоту.
Разложение концентрата. Разложение ведут концентрированной Н2SО4 (92-94 %) или олеумом в стальных реакторах. Вследствие экзотермичности процесса после нагревания кислоты с измельченным концентратом до 125-135°С реакция проходит интенсивно с саморазогревом до 180-200°С и заканчивается за 5-10 мин. Получающаяся полусухая масса ("плав") содержит оксосульфат титана (IV) (ТiOSО4 • Н2О), FеSО4) избыточную Н2SО4. Плав выщелачивают водой.
Очистка растворов от железа.
Растворы содержат 110-120 г/л ТiO2 (в составе ТiOSО4),
сульфаты железа SеSО4 и Fе2(SО4)3 и 200-240 г/л активной Н2S04.
Для очистки от основной массы железа восстанавливают Fе3+ до Fе2+ железной стружкой, а затем проводят кристаллизацию железного купороса FеSО4-7 Н2О, охлаждая растворы до -5 °С. В результате кристаллизации содержание железа растворе понижается до
20г/л.
Железный купорос - полезный побочный продукт, используемый в сельском хозяйстве как инсектофунгицид.
Осаждение метатитановой кислоты. Из растворов, содержащих оксосульфат титана, гидролитическим разложением выделяют метатитановую кислоту (гидратированный диоксид титана):
ТiОSO4 + 2 Н2О =ТiO2 • Н2О + Н2S04. (4.20)
Следует учитывать, что в действительности продукт гидролиза переменного состава, содержит, кроме ТiО2 и Н2О, значительные количества SО3.
Используют два способа проведения гидролиза: способ введения зародышей и способ разбавления.
При способе введения зародышей в раствор добавляют отдельно приготовленные зародыши в форме коллоидного раствора гидроксида титана в количестве
1 % от содержания ТiO
Рисунок 41 Шахтный хлоратор непрерывного действия:
1-водоохлаждаемый конус; 2 - фурма; 3 -хлорный коллектор; 4 - корпус хлоратора; 5 -волдохлаждаемый свод; 6 - бункер; 7 - золотниковый питатель; 8 - редуктор; 9 - электродвигатель; 10 - сборник огарка; 11 - разгрузочный шнек.
В печах подобного типа можно хлорировать шлаки с низким суммарным содержанием СаО и МgО (не выше 4-5 %). При (более высоком содержании образующиеся жидкие хлориды CaCl2 и МgС12 приводят к слипанию брикетов и нарушению схода шихты вдоль шахты печи.
Расход хлора составляет 0,85-0,9 т на 1 т тетрахлорида титана, что выше теоретического расхода (
0,75 т хлора) вследствие затрат хлора на хлорирование соединений примесей. В хлоратор подается анодный газ магниевых электролизеров, содержащий
85-90 % хлора или испаренный хлор из цистерн с жидким хлором.
При температурах 900-1000 °С хлорирование брикетов протекает во внешне диффузионной области, т.е. скорость процесса определяется скоростью подачи хлора. Энергия активации процесса хлорирования
12-16 кДж/моль ТiO2. Брикет приведенного выше размера полно хлорируется за 3-3,5 ч.
При принятых режимах хлорирования процесс протекает за счет теплоты реакций. При расходе хлора
400 кг/(м2 • ч) высота реакционной зоны, в пределах которой концентрация хлора изменяется примерно от начальной вблизи фурм практически до нуля (у верхней границы зоны), равна 0,8-1,0 м.
Удельная производительность шахтных хлораторов непрерывного действия при температурах хлорирования 900-1000 °С равна 1,8-2 т ТiС14 на 1 м3 объема хлоратора.
Повышение единичной мощности шахтного хлоратора путем увеличения его диаметра нецелесообразно, так как возрастает неравномерность схода шихты (центральная часть брикета перемещается быстрей периферийной) и неоднородность температурного поля по его сечению (у стен температура выше вследствие неравномерности распределения хлора).
Отношение по массе СО:СО2 в парогазовой смеси, выходящей из хлоратора, колеблется (в зависимости от режима) от 5:1 до 2:1.
Рисунок 42 Хлоратор для хлорирования в солевом расплаве:
Недостаток хлорирования брикетированной шихты - высокие затраты на приготовление брикетов, что повышает 10-15 % себестоимость хлорида; взрывоопасность отходящих газов, в которых преобладает СО.
1 - газоход; 2 - свод; 3 -графитовый электрод; 4 -стальные трубы для отвода тепла; 5 - кожух хлоратора; 6 -шамотная футеровка; 7 - бункер с шихтой; 8 - шнековый питатель; 9 - перегородка для создания циркуляции расплава; 10 - фурма; 11,12 - донные графитовые электроды; 13 -нижний слив расплава
Хлорирование в солевом расплаве. Этот способ разработан в СНГ. Хлорирование шлака проводится в ванне из расплава хлоридов щелочных и щелочно-земельных металлов, куда подают компоненты шихты (измельченные шлак и кокс) и хлор. В качестве расплава используют отработанный электролит магниевых электролизеров, имеющий следующий примерный состав, %: КС1 72-76; NаС1 14-16, МgС12 4-6. Шихта подается шнеком на поверхность расплава, хлор поступает в нижнюю часть хлоратора через фурмы и газораспределительную решетку (рис. 42). При удельном расходе хлора 40-60 м3/ч на 1 м3 расплава обеспечивается хорошее перемешивание его барботирующим хлором. В расплаве поддерживают концентрацию ТiO2 2-3 %, углерода 7-9 %. При высоте расплава 3-3,2 м хлор успевает полностью прореагировать в объеме расплава, лишь незначительная часть его уходит с отходящимися газами.
Необходимая температура расплава (800 - 850 oС) поддерживается за счет тепла экзотермических реакций. Избыточное тепло отводится с помощью установленных в стенке хлоратора кессонов из графитовых плит, в которые вмонтированы стальные трубы, куда подается вода.
В процессе хлорирования в расплаве накапливаются нелетучие хлориды (MgCl2, СаС12, а также FeCl2 и FeCl3 в форме комплексов KFeCl3 и KFeCl4 и др.). Периодически часть расплава выпускают и в хлоратор заливают свежий расплав. Отработанный расплав содержит, %: KCl 30 - 40, NaCl 2 - 5, MgCl2 25 - 35, FeCl2 + FeCl3 + MnCl2 10 - 20, SiO2 3 - 6, CaCl2 2 - 4, С 7 - 9, TiO2 0,5 - 1. В отличие от хлорирования брикетированных шихт в хлораторах с расплавом в составе парогазовой смеси преобладает СO2 [объемное соотношение СO2: СО = (10÷20):1], что объясняется неблагоприятными условиями для взаимодействия СO2 с частицами углерода.
Механизм (стадии) хлорирования диоксида титана в сложной системе, содержащей газовую, жидкую и две твердые фазы (TiO2 и кокс), недостаточно изучен.
Очевидно, что с поверхностью частиц кокса и TiO2, находящихся в расплаве, могут вступать во взаимодействие только растворенные в расплаве хлор, СO2 и СО, так как при хорошем смачивании кокса расплавом его поверхность экранирована жидкой средой от непосредственного контакта с пузырьками газа.
Растворимость хлора, СО и СO2 в расплавах KCl - NaCl - MgCl2 при 800 - 900 oС равна примерно 0,04, 0,02 и 1,5 г/л соответственно. Растворимость TiO2 не превышает 0,05 г/л.
Согласно одной из предложенных схем растворенный хлор хемосорбируется на поверхности частиц углеродистого материала с образованием активного (атомарного) хлора, переносимого через расплав к поверхности оксида, где при участии растворенного СО протекает реакция:
ТiO2 + 4С1акт + 2СО = ТiС14 + 2СО2.
Далее СО2 частично взаимодействует с углеродом с образованием СО. Эта схема объясняет наблюдаемое повышение скорости хлорирования с увеличением удельной поверхности кокса и преобладание СО2 над СО в газовой фазе.
Присутствие хлоридов железа в расплаве повышает скорость хлорирования. Это объясняется хлорирующим действием FеС13, легко отщепляющего активный хлор. Как указано выше, хлориды железа находятся в расплаве в форме комплексов
и
. Поэтому хлорирование ТiO2 с участием хлоридов железа можно представить суммарными реакциями:
+ 2С12 =
; (4.13)
+ ТiO2 + 2СО = ТiС14 +
+ 2СО2. (4.14)
Таким образом, хлориды железа выполняют роль переносчиков хлора.
Поскольку хлориды железа хорошо растворимы в расплаве, концентрация хлорирующего агента будет зависеть от содержания в нем железа. Так, достаточно содержания 1 % FeCl3 в расплаве для существенного увеличения скорости процесса. При нормальной работе хлоратора (без проскока хлора) в расплаве устанавливается отношение FeCl2 : FeCl3 = 20 + 200 (по массе), причем концентрация FeCl2 находится в пределах 15 - 20 %, a FeCl3 0,1 - 1,0 %.
Вследствие образования комплексов большая часть железа (а также алюминия, образующего комплекс КA1Cl4) остается в солевом расплаве.
Основные преимущества хлорирования в солевом расплаве по сравнению с хлорированием брикетов следующие: исключены сложные операции подготовки брикетов, что снижает себестоимость хлорида. Возможно хлорирование шлаков с повышенным содержанием СаО и МgО. Быстрый тепло- и массообмен в расплаве обеспечивает высокую скорость хлорирования и возможность отвода избыточного тепла. Преобладание СО2 над СО в составе газов резко снижает их взрывоопасность.
К недостаткам хлорирования в расплаве следует отнести периодический вывод отработанного расплава (до 200 кг на 1 т ТiС14), с которым теряется часть титана. Хлориды -вредные производственные сбросы. Важная задача - их использование или регенерация с возвратом в процесс.
Пылеулавливание и конденсация хлоридов
Парогазовая смесь, выходящая из хлораторов, имеет сложный состав. Она содержит газы (СО, СО2, СОС12, N2, НС1, С12), низкокипящие хлориды - в нормальных условиях жидкости (ТiС14, SiС14,VОС13 и др.); низкокипящие хлориды - в нормальных условиях твердые (FеС13, А1С13); высококипящие хлориды СаС12, МgС12, FеС12, а также КС1, NаС1 (при хлорировании в расплаве). Высококипящие хлориды механически увлекаются парогазовым потоком в виде тумана.
На рис. 43 приведена распространенная схема пылеулавливания и конденсации. Она состоит из пылевых камер (кулеров) для улавливания твердых хлоридов; рукавного фильтра с рукавами из стеклоткани для дополнительной очистки парогазовой смеси от твердых частиц; двух оросительных конденсаторов (конденсаторов смешения) для жидких хлоридов (ТiС14, SiС14), орошаемых охлажденным тетрахлоридом титана; во втором конденсаторе тетрахлорид, поступающий на орошение, охлаждается до -10 С. Далее газы проходят санитарный скруббер, орошаемый известковым молоком, для улавливания небольших количеств хлора, фосгена, хлористого водорода и выбрасываются в атмосферу. В кулерах газы охлаждаются с 500-600 до 140-180 °С омывающим трубы воздухом. В нижней разгрузочной части кулеров поддерживается постоянная температура (120-130 °С) органическим теплоносителем, циркулирующим в рубашке разгрузочного корыта. Термостатирование рукавного фильтра (140-160 °С) также осуществляется жидким теплоносителем.
РBс.43. Схема раздельной конденсационной системы (пунктиром показан путь циркуляции теплоносителя):
1 - пылевые камеры (кулера); 2 — сборник твердых хлоридов; 5 - рукавный фильтр; 4 – оросительные конденсаторы; 5 - водяной холодильник; 6 - погружной насос; 7 - холодильник, охлаждаемый рассолом до -10 С (раствор СаС12)
Для снятия с рукавов из стеклоткани уловленной пыли производится их отдувка парами тетрахлорида титана.
В связи с осложненностью эксплуатации фильтров с рукавами из стеклоткани на некоторых предприятиях они заменены солевым расплавом NаС1 + КС1. (см. рис. 25). Расплав циркулирует с помощью аэролифтного устройства. Принцип работы солевого фильтра рассмотрен в гл. 2.
Извлечение титана из шлака в жидкий технический тетрахлорид составляет 92-93 %.
Очистка технического тетрахлорида титана
Содержание примесей в техническом ТiС14 колеблется примерно в следующих пределах, % (по массе): Si 0,01-0,3; А1 0,01-0,1; Fе 0,01-0,02; V 0,01-0,3; ТiOС12 0,04-0,5; СОС12 0,005-0,15; С1 0,003-0,08; S 0,01-0,08.
Кроме перечисленных, в хлориде титана часто содержатся примеси хлоридов ниобия, тантала, хрома и примеси органических соединений, например ацетилхлориды (СС13СОС1, СН2ClОСl), гексахлорбензол С6С16 и др.
Хлорид титана очищают от большинства примесей ректификацией, основанной на различии температур кипения хлоридов. Однако ректификации предшествует очистка от примеси ванадия.
Очистка от ванадия. Ванадия содержится в ТiС14 в составе оксихлорида VОС13. Отделение его от ТiС14 ректификацией затруднительно вследствие близости точек кипения ТiС14 и VОС13 (136 и 127 °С соответственно). Все известные методы очистки от ванадия основаны на восстановлении VОС13 до малорастворимого в тетрахлориде титана VОС12. На заводах в качестве восстановителей применяют медные или алюминиевые порошки.
Восстановление медным порошком протекает через стадию
образования СuТlС14:
Сu + ТiС14 = СuТiС14; (4.15)
СuТiС14 + VОС13 = VОС12 + CuС1 + ТiС14. (4.16)
Получаемые медно-ванадиевые осадки содержат, % Тi 6-8; V 4-6; С1
45, остальное - кислород и примеси других элементов. Разработаны схемы извлечения из осадков ванадия и меди.
Вследствие высокой стоимости медного порошка стали применять для восстановления VОС13 порошок алюминия. Последний реагирует с ТiС14 с образованием ТiС13, который затем восстанавливает VОС13:
3 ТiС14 + А1 = 3 ТiС13 + А1С13; (4.17)
ТiС13 + VОС13 = VОС12 +Т1С14. (4.18)
Кроме того, протекает реакция:
ТiOС12 + А1С13 = А1ОСl↓ + Т1С14. (4.19)
Осадок, содержащий VОС12, ТiC13, А1С13, направляется на извлечение ванадия. На некоторых зарубежных заводах для очистки от ванадия применяют восстановление сероводородом или органическими веществами (углеводороды, жирные кислоты и др.).
Очистка ректификацией. Очистку хлорида титана ректификацией проводят в колоннах из нержавеющей стали с дырчатыми тарелками (или тарелками с щелевидными прорезями) в две стадии (рис. 44). На первой стадии отделяют тетрахлорид титана от примеси кремния (температура кипения S1С14 58 °С) и других летучих примесей (СС14, СS2, SОС12 и др.), поддерживая в верхней части колонны температуру паров 132-135 °С и избыточное давление 0,66-4 кПа. Температура в кубе колонны 140-150 °С.
Рисунок 44 Схема установки для очистки тетрахлорида титана ректификацией:
1- напорный бак с ТЛС14; 2 - подогреватель; 3 - ректификационная колонна для отделения низкокипящих хлоридов; 4 - кубы-испарители с электронагревателями 5 (в патроне); 6 - дефлегматоры; 7 - регулирующий клапан; 8 - насос; 9 - кубы-испарители с открытыми нагревателями; 10,11 - ректификационная колонна для дистилляции Т1С14; 12 - распределительный клапан; 13 - сборник очищенного Т1С14
Неконденсируемые газы (СО2, С12, N2, СОС12) выводят из дефлегматора через гидрозатвор в систему очистки газов.
Кубовый остаток, содержащий ТiС14 и примеси высококипящих хлоридов и оксихлоридов (в частности, ТiOС12), поступает во вторую колонну, в верхней части которой поддерживают температуру 134-136 °С (точка кипения ТiС14), в нижней - 137-138 °С. Отбираемый дистиллят - чистый четыреххлористый титан. Примеси высококипящих хлоридов (ТiOС12, FеС13, А1С13, NbС15 и др.) остаются в кубовом остатке.
Очищенный тетрахлорид титана содержит примеси в количествах, близких к пределу чувствительности спектрального анализа (10-3-10-5 %). Извлечение титана из технического в очищенный тетрахлорид титана равно
96 %.
Рисунок 41 Шахтный хлоратор непрерывного действия:
1-водоохлаждаемый конус; 2 - фурма; 3 -хлорный коллектор; 4 - корпус хлоратора; 5 -волдохлаждаемый свод; 6 - бункер; 7 - золотниковый питатель; 8 - редуктор; 9 - электродвигатель; 10 - сборник огарка; 11 - разгрузочный шнек.
В печах подобного типа можно хлорировать шлаки с низким суммарным содержанием СаО и МgО (не выше 4-5 %). При (более высоком содержании образующиеся жидкие хлориды CaCl2 и МgС12 приводят к слипанию брикетов и нарушению схода шихты вдоль шахты печи.
Расход хлора составляет 0,85-0,9 т на 1 т тетрахлорида титана, что выше теоретического расхода (
0,75 т хлора) вследствие затрат хлора на хлорирование соединений примесей. В хлоратор подается анодный газ магниевых электролизеров, содержащий
85-90 % хлора или испаренный хлор из цистерн с жидким хлором.
При температурах 900-1000 °С хлорирование брикетов протекает во внешне диффузионной области, т.е. скорость процесса определяется скоростью подачи хлора. Энергия активации процесса хлорирования
12-16 кДж/моль ТiO2. Брикет приведенного выше размера полно хлорируется за 3-3,5 ч.
При принятых режимах хлорирования процесс протекает за счет теплоты реакций. При расходе хлора
400 кг/(м2 • ч) высота реакционной зоны, в пределах которой концентрация хлора изменяется примерно от начальной вблизи фурм практически до нуля (у верхней границы зоны), равна 0,8-1,0 м.
Рисунок 41 Шахтный хлоратор непрерывного действия:
1-водоохлаждаемый конус; 2 - фурма; 3 -хлорный коллектор; 4 - корпус хлоратора; 5 -волдохлаждаемый свод; 6 - бункер; 7 - золотниковый питатель; 8 - редуктор; 9 - электродвигатель; 10 - сборник огарка; 11 - разгрузочный шнек.
В печах подобного типа можно хлорировать шлаки с низким суммарным содержанием СаО и МgО (не выше 4-5 %). При (более высоком содержании образующиеся жидкие хлориды CaCl2 и МgС12 приводят к слипанию брикетов и нарушению схода шихты вдоль шахты печи.
Расход хлора составляет 0,85-0,9 т на 1 т тетрахлорида титана, что выше теоретического расхода (
0,75 т хлора) вследствие затрат хлора на хлорирование соединений примесей. В хлоратор подается анодный газ магниевых электролизеров, содержащий
85-90 % хлора или испаренный хлор из цистерн с жидким хлором.Рисунок 41 Шахтный хлоратор непрерывного действия:
1-водоохлаждаемый конус; 2 - фурма; 3 -хлорный коллектор; 4 - корпус хлоратора; 5 -волдохлаждаемый свод; 6 - бункер; 7 - золотниковый питатель; 8 - редуктор; 9 - электродвигатель; 10 - сборник огарка; 11 - разгрузочный шнек.
В печах подобного типа можно хлорировать шлаки с низким суммарным содержанием СаО и МgО (не выше 4-5 %). При (более высоком содержании образующиеся жидкие хлориды CaCl2 и МgС12 приводят к слипанию брикетов и нарушению схода шихты вдоль шахты печи.
Расход хлора составляет 0,85-0,9 т на 1 т тетрахлорида титана, что выше теоретического расхода (
При температурах 900-1000 °С хлорирование брикетов протекает во внешне диффузионной области, т.е. скорость процесса определяется скоростью подачи хлора. Энергия активации процесса хлорирования
Удельная производительность шахтных хлораторов непрерывного действия при температурах хлорирования 900-1000 °С равна 1,8-2 т ТiС14 на 1 м3 объема хлоратора.
Повышение единичной мощности шахтного хлоратора путем увеличения его диаметра нецелесообразно, так как возрастает неравномерность схода шихты (центральная часть брикета перемещается быстрей периферийной) и неоднородность температурного поля по его сечению (у стен температура выше вследствие неравномерности распределения хлора).
Отношение по массе СО:СО2 в парогазовой смеси, выходящей из хлоратора, колеблется (в зависимости от режима) от 5:1 до 2:1.

Рисунок 42 Хлоратор для хлорирования в солевом расплаве:
Недостаток хлорирования брикетированной шихты - высокие затраты на приготовление брикетов, что повышает 10-15 % себестоимость хлорида; взрывоопасность отходящих газов, в которых преобладает СО.
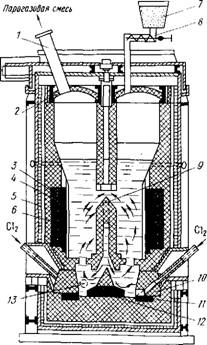
1 - газоход; 2 - свод; 3 -графитовый электрод; 4 -стальные трубы для отвода тепла; 5 - кожух хлоратора; 6 -шамотная футеровка; 7 - бункер с шихтой; 8 - шнековый питатель; 9 - перегородка для создания циркуляции расплава; 10 - фурма; 11,12 - донные графитовые электроды; 13 -нижний слив расплава
Хлорирование в солевом расплаве. Этот способ разработан в СНГ. Хлорирование шлака проводится в ванне из расплава хлоридов щелочных и щелочно-земельных металлов, куда подают компоненты шихты (измельченные шлак и кокс) и хлор. В качестве расплава используют отработанный электролит магниевых электролизеров, имеющий следующий примерный состав, %: КС1 72-76; NаС1 14-16, МgС12 4-6. Шихта подается шнеком на поверхность расплава, хлор поступает в нижнюю часть хлоратора через фурмы и газораспределительную решетку (рис. 42). При удельном расходе хлора 40-60 м3/ч на 1 м3 расплава обеспечивается хорошее перемешивание его барботирующим хлором. В расплаве поддерживают концентрацию ТiO2 2-3 %, углерода 7-9 %. При высоте расплава 3-3,2 м хлор успевает полностью прореагировать в объеме расплава, лишь незначительная часть его уходит с отходящимися газами.
Необходимая температура расплава (800 - 850 oС) поддерживается за счет тепла экзотермических реакций. Избыточное тепло отводится с помощью установленных в стенке хлоратора кессонов из графитовых плит, в которые вмонтированы стальные трубы, куда подается вода.
В процессе хлорирования в расплаве накапливаются нелетучие хлориды (MgCl2, СаС12, а также FeCl2 и FeCl3 в форме комплексов KFeCl3 и KFeCl4 и др.). Периодически часть расплава выпускают и в хлоратор заливают свежий расплав. Отработанный расплав содержит, %: KCl 30 - 40, NaCl 2 - 5, MgCl2 25 - 35, FeCl2 + FeCl3 + MnCl2 10 - 20, SiO2 3 - 6, CaCl2 2 - 4, С 7 - 9, TiO2 0,5 - 1. В отличие от хлорирования брикетированных шихт в хлораторах с расплавом в составе парогазовой смеси преобладает СO2 [объемное соотношение СO2: СО = (10÷20):1], что объясняется неблагоприятными условиями для взаимодействия СO2 с частицами углерода.
Механизм (стадии) хлорирования диоксида титана в сложной системе, содержащей газовую, жидкую и две твердые фазы (TiO2 и кокс), недостаточно изучен.
Очевидно, что с поверхностью частиц кокса и TiO2, находящихся в расплаве, могут вступать во взаимодействие только растворенные в расплаве хлор, СO2 и СО, так как при хорошем смачивании кокса расплавом его поверхность экранирована жидкой средой от непосредственного контакта с пузырьками газа.
Растворимость хлора, СО и СO2 в расплавах KCl - NaCl - MgCl2 при 800 - 900 oС равна примерно 0,04, 0,02 и 1,5 г/л соответственно. Растворимость TiO2 не превышает 0,05 г/л.
Согласно одной из предложенных схем растворенный хлор хемосорбируется на поверхности частиц углеродистого материала с образованием активного (атомарного) хлора, переносимого через расплав к поверхности оксида, где при участии растворенного СО протекает реакция:
ТiO2 + 4С1акт + 2СО = ТiС14 + 2СО2.
Далее СО2 частично взаимодействует с углеродом с образованием СО. Эта схема объясняет наблюдаемое повышение скорости хлорирования с увеличением удельной поверхности кокса и преобладание СО2 над СО в газовой фазе.
Присутствие хлоридов железа в расплаве повышает скорость хлорирования. Это объясняется хлорирующим действием FеС13, легко отщепляющего активный хлор. Как указано выше, хлориды железа находятся в расплаве в форме комплексов






Таким образом, хлориды железа выполняют роль переносчиков хлора.
Поскольку хлориды железа хорошо растворимы в расплаве, концентрация хлорирующего агента будет зависеть от содержания в нем железа. Так, достаточно содержания 1 % FeCl3 в расплаве для существенного увеличения скорости процесса. При нормальной работе хлоратора (без проскока хлора) в расплаве устанавливается отношение FeCl2 : FeCl3 = 20 + 200 (по массе), причем концентрация FeCl2 находится в пределах 15 - 20 %, a FeCl3 0,1 - 1,0 %.
Вследствие образования комплексов большая часть железа (а также алюминия, образующего комплекс КA1Cl4) остается в солевом расплаве.
Основные преимущества хлорирования в солевом расплаве по сравнению с хлорированием брикетов следующие: исключены сложные операции подготовки брикетов, что снижает себестоимость хлорида. Возможно хлорирование шлаков с повышенным содержанием СаО и МgО. Быстрый тепло- и массообмен в расплаве обеспечивает высокую скорость хлорирования и возможность отвода избыточного тепла. Преобладание СО2 над СО в составе газов резко снижает их взрывоопасность.
К недостаткам хлорирования в расплаве следует отнести периодический вывод отработанного расплава (до 200 кг на 1 т ТiС14), с которым теряется часть титана. Хлориды -вредные производственные сбросы. Важная задача - их использование или регенерация с возвратом в процесс.
Пылеулавливание и конденсация хлоридов
Парогазовая смесь, выходящая из хлораторов, имеет сложный состав. Она содержит газы (СО, СО2, СОС12, N2, НС1, С12), низкокипящие хлориды - в нормальных условиях жидкости (ТiС14, SiС14,VОС13 и др.); низкокипящие хлориды - в нормальных условиях твердые (FеС13, А1С13); высококипящие хлориды СаС12, МgС12, FеС12, а также КС1, NаС1 (при хлорировании в расплаве). Высококипящие хлориды механически увлекаются парогазовым потоком в виде тумана.
На рис. 43 приведена распространенная схема пылеулавливания и конденсации. Она состоит из пылевых камер (кулеров) для улавливания твердых хлоридов; рукавного фильтра с рукавами из стеклоткани для дополнительной очистки парогазовой смеси от твердых частиц; двух оросительных конденсаторов (конденсаторов смешения) для жидких хлоридов (ТiС14, SiС14), орошаемых охлажденным тетрахлоридом титана; во втором конденсаторе тетрахлорид, поступающий на орошение, охлаждается до -10 С. Далее газы проходят санитарный скруббер, орошаемый известковым молоком, для улавливания небольших количеств хлора, фосгена, хлористого водорода и выбрасываются в атмосферу. В кулерах газы охлаждаются с 500-600 до 140-180 °С омывающим трубы воздухом. В нижней разгрузочной части кулеров поддерживается постоянная температура (120-130 °С) органическим теплоносителем, циркулирующим в рубашке разгрузочного корыта. Термостатирование рукавного фильтра (140-160 °С) также осуществляется жидким теплоносителем.
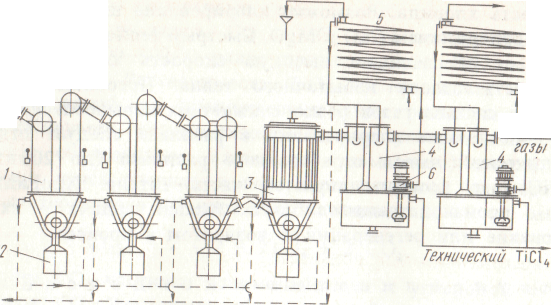
РBс.43. Схема раздельной конденсационной системы (пунктиром показан путь циркуляции теплоносителя):
1 - пылевые камеры (кулера); 2 — сборник твердых хлоридов; 5 - рукавный фильтр; 4 – оросительные конденсаторы; 5 - водяной холодильник; 6 - погружной насос; 7 - холодильник, охлаждаемый рассолом до -10 С (раствор СаС12)
Для снятия с рукавов из стеклоткани уловленной пыли производится их отдувка парами тетрахлорида титана.
В связи с осложненностью эксплуатации фильтров с рукавами из стеклоткани на некоторых предприятиях они заменены солевым расплавом NаС1 + КС1. (см. рис. 25). Расплав циркулирует с помощью аэролифтного устройства. Принцип работы солевого фильтра рассмотрен в гл. 2.
Извлечение титана из шлака в жидкий технический тетрахлорид составляет 92-93 %.
Очистка технического тетрахлорида титана
Содержание примесей в техническом ТiС14 колеблется примерно в следующих пределах, % (по массе): Si 0,01-0,3; А1 0,01-0,1; Fе 0,01-0,02; V 0,01-0,3; ТiOС12 0,04-0,5; СОС12 0,005-0,15; С1 0,003-0,08; S 0,01-0,08.
Кроме перечисленных, в хлориде титана часто содержатся примеси хлоридов ниобия, тантала, хрома и примеси органических соединений, например ацетилхлориды (СС13СОС1, СН2ClОСl), гексахлорбензол С6С16 и др.
Хлорид титана очищают от большинства примесей ректификацией, основанной на различии температур кипения хлоридов. Однако ректификации предшествует очистка от примеси ванадия.
Очистка от ванадия. Ванадия содержится в ТiС14 в составе оксихлорида VОС13. Отделение его от ТiС14 ректификацией затруднительно вследствие близости точек кипения ТiС14 и VОС13 (136 и 127 °С соответственно). Все известные методы очистки от ванадия основаны на восстановлении VОС13 до малорастворимого в тетрахлориде титана VОС12. На заводах в качестве восстановителей применяют медные или алюминиевые порошки.
Восстановление медным порошком протекает через стадию
образования СuТlС14:
Сu + ТiС14 = СuТiС14; (4.15)
СuТiС14 + VОС13 = VОС12 + CuС1 + ТiС14. (4.16)
Получаемые медно-ванадиевые осадки содержат, % Тi 6-8; V 4-6; С1
Производство диоксида титана
Сернокислотный способ
Основное количество выпускаемого диоксида титана из ильменитового концентрата (или титановых шлаков) получают сернокислотным способом, который включает следующие стадии:
-
разложение концентрата серной кислотой; -
очистку растворов от железа; -
гидролитическое выделение метатитановой кислоты из сернокислотного раствора; -
прокаливание осадка с получением диоксида титана.
Этот способ обеспечивает высокое извлечение титана в готовый продукт, причем в технологии практически используют один реагент - серную кислоту.
Разложение концентрата. Разложение ведут концентрированной Н2SО4 (92-94 %) или олеумом в стальных реакторах. Вследствие экзотермичности процесса после нагревания кислоты с измельченным концентратом до 125-135°С реакция проходит интенсивно с саморазогревом до 180-200°С и заканчивается за 5-10 мин. Получающаяся полусухая масса ("плав") содержит оксосульфат титана (IV) (ТiOSО4 • Н2О), FеSО4) избыточную Н2SО4. Плав выщелачивают водой.
Очистка растворов от железа.
Растворы содержат 110-120 г/л ТiO2 (в составе ТiOSО4),
сульфаты железа SеSО4 и Fе2(SО4)3 и 200-240 г/л активной Н2S04.
Для очистки от основной массы железа восстанавливают Fе3+ до Fе2+ железной стружкой, а затем проводят кристаллизацию железного купороса FеSО4-7 Н2О, охлаждая растворы до -5 °С. В результате кристаллизации содержание железа растворе понижается до
2. После нагревания до кипения в осадок выпадает 95-96% ТiO2.
В случае применения способа разбавления исходные растворы концентрируют выпариванием до содержания 240 -260 г/л ТiO2 и затем нагретый раствор по определенному режиму разбавляют, вливая в воду. При разбавлении раствора возникают зародыши - центры кристаллизации, а затем образуется осадок метатитановой кислоты.
Прокаливание метатитановой кислоты. Отфильтрованные и промытые осадки метатитановой кислоты прокаливают в барабанных печах, футерованных высокоглиноземистым кирпичом, при максимальной температуре 850-1000 °С (в зависимости от назначения ТiO2). Помимо воды при прокаливании удаляется содержащийся в осадках SО3.
Способ "сжигания" тетрахлорида титана.
В последние годы получает все большее развитие производство диоксида титана из тетрахлорида титана методом "сжигания", который основан на реакции:
ТiС14 + О2 = ТiO2 + 2 С12,
Δ

Эта реакция при 900-1000 °С протекает с достаточной скоростью. Получаемый хлор возвращают на хлорирование титанового сырья.
Известно несколько вариантов проведения процесса "сжигания". Рассмотрим два из них.
-
Реакцию проводят в камере, в которой установлена
форсунка, куда поступают кислород и пары тетрахлорида титана, предварительно нагретые до 1000-1100 °С. На выходе из форсунки пары ТiС14 реагируют с кислородом с образованием желто-зеленого пламени. Поток газа уносит частицы
диоксида титана в пылевую камеру и рукавные фильтры. От
ходящие газы, содержащие 80-85 % хлора, пригодны для использования в производстве ТiС14.
Основное затруднение при использовании способа состоит в необходимости предварительного нагрева реагирующих компонентов до 1000-1100 °С.
-
Применение плазмы в качестве источника тепла - наиболее перспективный метод. Целесообразно использовать высокочастотную плазменную горелку с факелом кислородной плазмы. В факел, имеющий температуру 6000-10000 °С, вводят пары тетрахлорида титана, которые при столь высокой
температуре быстро реагируют с кислородом с образованием
тонкодисперсного диоксида титана рутильной модификации.
Основные преимущества технологии получения диоксида титана из тетрахлорида титана по способу "сжигания" в сравнении с сернокислотным способом:
-
технологическая схема проще, капитальные затраты в
среднем в 1,5 раза ниже; -
схема замкнута (хлор утилизируется), тогда как в
сернокислотной схеме затруднительна утилизация гидролизной серной кислоты; -
диоксид титана более высокой чистоты, а качество
получаемого из него пигмента выше, чем получаемого сернокислотным способом.
- 1 2 3 4 5
ПРОИЗВОДСТВО ХИМИЧЕСКИХ СОЕДИНЕНИЙ ЦИРКОНИЯ И ГАФНИЯ
Циркониевые минералы, руды и рудные концентраты
Содержание циркония в земной коре относительно высокое - 0,025 % (по массе). По распространенности он превосходит медь, цинк, олово, никель и свинец. Известно около 20 минералов циркония. Они концентрируются главным образом в гранитных и щелочных (нефелин-сиенитовых) пегматитах. Основными промышленными источниками в настоящее время служат минералы бедделеит и циркон. Сырьем могут служить также минералы эвдиалит и эвколит, но они значительно бедней по содержанию циркония.
Бадделеит. По составу представляет собой почти чистый диоксид циркония. В наиболее чистых образцах до 98 % ZrО2. Обычно содержит примесь гафния (до нескольких процентов), изредка уран (до 1 %) и торий (до 0,2 %). Месторождения редки. Плотность минерала 5,5-6. Наиболее крупное месторождение найдено в Бразилии.
Основные методы обогащения руд - гравитационные. Для отделения минералов железа и ильменита используют электромагнитное обогащение.
Циркон - ортосиликат циркония ZrSiО4 (67,2 % ZrО2, 32,8 % SiО2). Это наиболее распространенный минерал циркония. Концентрируется главным образом в пегматитах гранитной и особенно щелочной магмы. Часто встречается в россыпях, образующихся при разрушении коренных пород. Циркон большей частью имеет коричневый цвет, плотность минерала 4,4-4.7 г/см3, твердость 7,5 по минералогической шкале. Минерал обычно содержит гафний (0,5-4 %). Основные запасы циркона сосредоточены в прибрежно-морских россыпях. Здесь циркон накапливается вместе с ильменитом, рутилом, монацитом и рядом других минералов.
Руды, содержащие циркон, обогащают гравитационными методами в сочетании с магнитной и электростатической сепарациями.
Выпускаемые цирконовые концентраты первого сорта должны содержать не менее 65% ZrО2. В них лимитируется содержание следующих примесей, % (не 6oлее): FeO 0,1; TiО2 0,4; A12O3 2,0; СаО и MgO 0,1; P2O5 0,15. Концентраты второго сорта должны содержать не менее 60% ZrО2, примеси не лимитируются.
Наиболее крупные месторождения циркона за рубежом расположены в Австралии, Индии, Бразилии, ЮАР, США. В СНГ циркон найден на Урале, Украине и в других районах страны.
Эвдиалит и эвколит. Состав эвдиалита может быть выражен общей эмпирической формулой: (Nа, Са)6 Zr [Si 6О18][ОН,С1]2.
Эвколит - разновидность эвдиалита, содержащего ионы Fе2+. Химический состав эвдиалита, %: Nа2О 11,6-17,3; ZrO2 12-14,5; FеО 3,1-7,1; SiO2 47,2-51,2; С1 0,7-1,6. Цвет минерала - розовый или малиновый. Минерал легко разлагается кислотами.
Эвдиалит и эвколит встречаются в магматических щелочных породах (нефелиновых сиенитах). Известны месторождения в СССР (на Кольском полуострове), Португалии, Гренландии, Трансваале, Бразилии и других странах.
В капиталистических странах в 1986г. было добыто 830 тыс.т цирконовых концентратов, в том числе в Австралии - 470, ЮАР - 150, США - 85.
Продукты переработки цирконовых концентратов
Цирконовые концентраты служат исходным материалом для производства ферросиликоциркония, ферроциркония и химических соединений циркония: диоксида циркония, фтороцирконата калия и тетрахлорида циркония, а также соединений гафния.
Ферросиликоцирконий непосредственно выплавляют из цирконовых концентратов. Технический диоксид циркония служит исходным материалом для получения ферроциркония и используется в производстве огнеупоров и керамики. Диоксид циркония высокой чистоты применяют для производства высококачественных огнеупорных изделий и порошкообразного циркония. Фтороцирконат калия и тетрахлорид циркония используют главным образом для производства металлического циркония. Ниже рассмотрены основные способы производства соединений циркония.
Производство диоксида циркония
Разложение концентрата
Циркон практически не разлагается соляной, серной и азотной кислотами. Для его разложения с целью перевода циркония в раствор используют большей частью спекание (или сплавление) с содой или спекание с карбонатом кальция (мелом). Образующиеся цирконаты натрия или кальция растворяются в кислотах, из раствора затем выделяют гид-роксид или основные соли циркония. Последние термически разлагают, получая диоксид циркония.
Разложение циркона спеканием с карбонатом натрия. При 1100-1200 °С сода реагирует с цирконом с образованием метацирконата и ортосиликата натрия:
ZrSiO4 + 3Na2CO3= Na2ZrO3+Na4SiO4+2CO2. (4.23)
Процесс можно проводить в барабанных печах непрерывного действия, питая печь гранулированной шихтой (размер гранул 5-10 мм). Грануляцию проводят на чашевом грануляторе при увлажнении шихты. Измельченный спек первоначально выщелачивают водой для извлечения в раствор большей части ортосиликата натрия. Осадки после водного выщелачивания обрабатывают соляной или серной кислотой. В первом случае получают солянокислый раствор, содержащий основной хлорид цирконила ZrОС12, во втором случае - растворы, содержащие основной сульфат циркония Zr(ОН)2SО4. При кислотной обработке образуется кремниевая кислота, для коагуляции которой в пульпу добавляют флокулянт полиакриламид. Осадки отделяют от цирконийсодержащих растворов фильтрацией.
Разложение циркона спекании с карбонатом кальция. Процесс основан на взаимодействии циркона с СаСО3:
ZrSiO4 + 3СаСО3 = СаZrО3 + Са2SiO4 + 3 СО2. (4.24)
Эта реакция протекает с достаточной скоростью лишь при 1400-1500 °С. Однако добавки в шихту небольшого количества хлорида кальция (
5 % от массы цирконового концентрата) позволяют снизить температуру спекания до 1100-1200 °С. Ускорение процесса в присутствии малых добавок СаС12 объясняется, вероятно, частичным образованием жидкой фазы (температура плавления СаС12 774 °С), а также увеличением структурных дефектов в кристаллах компонентов шихты под действием хлористого
кальция.
Рис.45. Технологическая схема переработки цирконового концентрата по способу спекания с карбонатом кальция
Шихту, содержащую измельченный цирконовый концентрат, мел и хлорид кальция, нагревают во вращающихся барабанных печах при 1100-1200 °С в течение 4-5 ч, степень разложения достигает 97-98 %.
Обработку спеков соляной кислотой ведут в две стадии. Первоначально при обработке на холоду 5-10 %-ной соляной кислотой растворяется избыточный оксид кальция и разлагается ортосиликат кальция. Образующаяся колоидная кремниевая кислота удаляется вместе с раствором. Нерастворившийся остаток, содержащий цирконат кальция, выщелачивают 25-30 %-ной НС1 при нагревании до 70-80 °C, получая растворы, содержащие основной хлорид циркония. Примерно по тем же режимам можно выщелачивать известковые спеки азотной кислотой, получая растворы, содержащие Zr(ОН)2(NО3)2. Преимущества последней состоят в возможноти утилизации азотнокислых маточных растворов после излечения из них циркония и получения азотнокислых солей.
В случае применения серной кислоты можно выщелачивать известковый спек в одну стадию без существенных затруднений в отношении отделения раствора от осадка кремниевой кислоты. Обработку спека проводят раствором 300-400 г/л Н2SО4 при температуре не выше 80-90 °С. В этих условиях осадки содержат гидратированные сульфаты кальция СаSО4 • 2 Н2О и СаSО4 • 0,5 Н2О, что обеспечивает хорошую фильтрацию осадков. С целью снижения потерь циркония сульфатный кек, количество которого велико (
6 т на 1т ZrО2) многократно промывают водой. В некоторых производственных схемах рационально сочетается выщелачивание известковых спеков соляной и серной кислотами, что обспечивает получение различных соединений циркония (рис. 45).
Выделение циркония из растворов и получение ZrО2
Растворы, полученные в результате выщелачивания содовых или известковых спеков, содержат цирконий (100-200 г/л) и примеси железа, титана, алюминия, кремния и др. В промышленной практике применяют четыре способа выделения циркония из растворов:
-
Выделение основного хлорида Zr(ОН)2С12•7 Н2О.
-
Выделение основных сульфатов циркония.
-
Осаждение кристаллогидрата сульфата циркония Zг(S04)2•4 Н20.
-
Кристаллизация сульфато-цирконатов натрия или аммония (дубитель для кожевенной промышленности).
Ниже рассмотрены наиболее распространенные первые два способа.
Выделение основного хлорида. Способ основан на малой растворимости кристаллогидрата Zг(ОН)2С12•7 Н2О в концентрированной соляной кислоте, в то время как в воде и разбавленной НС1 растворимость высокая.
Концентрация HCI, г/л
7,2
135,6
231,5
318
370
Растворимость при 20 °С Zг(ОН)2С12•7 Н2О г/л
567,5
164,9
20,5
10,8
17,8
Растворимость основного хлорида в концентрированной НС1 при 70 °С примерно в 5 раз выше, чем при 20 °С. Выпариванием нельзя достигнуть концентрации НС1 выше
220 г/л, так как образуется азеотропная смесь. Однако в кислоте такой концентрации растворимость Zr(ОН)2С12•7 Н2О невысокая (
25 г/л), что позволяет после охлаждения раствора выделить в кристаллы 70-80 % циркония, содержащегося в растворе. Основной хлорид выделяется в виде крупных кристаллов, имеющих форму тетрагональных призм, легко отделяемых от маточного раствора.
Способ дает возможность получить соединения циркония высокой чистоты, так как большинство примесей остается в солянокислом маточном растворе.
Из основного хлорида легко можно получить другие соединения циркония. Для получения ZгО2 основной хлорид растворяют в воде и осаждают добавлением раствора аммиака гидроксид циркония. Прокаливанием последнего при 600-700 °С получают диоксид с содержанием ZгО2 99,6-99,8 %. Для получения других соединений (нитрата, фторидов) гидроксид растворяют в соответствующей кислоте.
Выделение основных сульфатов. Малорастворимые основные сульфаты, состав которых можно выразить общей формулой х ZгО2• у SО3•z Н2О (х>у), выделяются из растворов при рН = 2+3 и мольном отношении SО3:ZгО2 в исходном растворе в пределах 0,55-0,9.
При нейтрализации сернокислого раствора, содержащего значительный избыток кислоты, содой или аммиаком, гидролитическое выделение основного сульфата циркония не происходит. Это объясняется тем, что в таких растворах цирконий находится в составе прочных анионов [ZгО(SО4)2]2-, образующих с катионами натрия и аммония хорошо растворимые соли. Гидролиз наступает лишь в случае вывода части ионов
из растворов, например добавлением ВаС12 или СаС12, что усложняет технологию.
Значительно проще гидролитическое выделение основных сульфатов из солянокислых или азотнокислых растворов, так как в этом случае в раствор вводится дозированное количество сульфат-ионов (добавляют Н2SО4 или Ка2SО4).
Для осаждения основного сульфата в солянокислый раствор, содержащий 40-60 г/л циркония, добавляют Н2SО4 (0,5-0,7 моля на 1 моль ZгО2), нейтрализацией и разбавлением доводят кислотность до 1-1,5 г/л по НС1, а затем нагревают раствор до 70-80 °С. В осадок выделяется 97-98 % циркония, его состав примерно соответствует формуле 2ZгО2-SО3-5 Н2О.
Осадок основного сульфата после промывки, фильтрации и сушки прокаливают для удаления SО3 при 850-900 С в муфельных печах, футерованных высокоглиноземистым огнеупором. Получаемый технический диоксид циркония содержит 97-98 % ZгО2. Основные примеси следующие, %: ТiO2 0,25-0,5; SO2 0,2-0,5; Fе2О3 0,05-0,15; СаО 0,2-0,5; SО3 0,3-0,4.
Получение фтороцирконата калия
Наиболее просто фтороцирконат калия можно получить из цирконового концентрата по технологии, разработанной Н.П.Сажиным и Е.А.Пепеляевой. Способ основан на реакции, протекающей при нагревании циркона с фторосиликатом калия:
ZrSO4 + К2SiF6 = К2ZrF6 + 2 SiO2.
Рuс.46. Диаграмма состояния системы
О Ю 20 30 40 50 60 70
КF %(мол.) ZrF4
Как видно из диаграммы состояния системы КF-ZrF4 (рис.46), выше 600 °С К22гР6 разлагается с образованием К3ZrF7 и расплава, содержащего КF и ZrF4:
2 К2ZrF6 = К3ZrF7 + КF + ZrF4.
Поэтому продукт спекания, помимо К2ZrF6, может содержать некоторое количество К3ZrF7.
Полно циркон разлагается в интервале 650—700 С при условии введения в шихту хлористого калия, подавляющего диссоциацию К2SiF6 с образованием летучего SiF4.
При температурах спекания в шихте в результате взаимодействия компонентов образуется жидкая фаза, что способствует быстрому протеканию процесса. Получающийся в результате разложения спек выщелачивают водой. Из раствора затем кристаллизуют К2ZrF6.
Шихту, состоящую из измельченного циркона, фторосиликата калия (взятого с избытком
50 % от стехиометрического количества) и КС1 (10-40 % от массы циркона) спекают в барабанной печи. Спек состоит из слегка оплавленных гранул размером 0,5-10 мм. Его измельчают и выщелачивают подкисленной водой (1 % НС1) при соотношении Т:Ж = 1:7 и температуре 85 С.
Это позволяет охлаждением раствора до 15 С выкристаллизовать 80-90 % циркония
Из маточного раствора осаждают аммиачной водой гидроксид циркония, который возвращают в шихту для спекания.
Кристаллы К2ZrF6 имеют следующий состав, %: (Zr+Нf) 31,9-32; К 27,2-27,6; F 39,9-40,05; Fе 0,045; Тi 0,042; 81 0,07; С1 0,007; Hf 1,5-2,5 (по отношению к цирконию).
Гафний от циркония можно отделить дробной кристаллизацией соли.
Получение тетрахлорида циркония
Тетрахлорид циркония получают хлорированием трех продуктов: цирконового концентрата, карбида (карбонитрида) циркония, предварительно полученного из концентрата, и диоксида циркония. ,
Хлорирование цирконового концентрата. Цирконовый концентрат в смеси с углеродистым материалом хлорируется с
достаточной для практических целей скоростью при
900-1000 °С. Основные реакции процесса:
2ZrSiО4 + 4 С12 + 2 С = ZгС14 + SiС14 + 2 СО2;
CO2 + C= 2 CO
Теплоты реакции
125кДж недостаточно для самопроизвольного протекания процесса, необходим постоянный подвод тепла. Хлорирование проводят в шахтных хлораторах непрерывного действия, куда загружается брикетированная шихта. При содержании в брикетах 25-30 % углерода брикеты при температуре хлорирования обладают достаточной электропроводностью, что позволяет нагревать шихту с помощью графитовых электродов, вмонтированных в стенках хлоратора. Для прохождения тока через горячую шихту требуется напряжение
25В. Выгружаемый из печи остаток неполно прохлорированных брикетов возвращается на шихтовку.
Система улавливания состоит из пылевых камер для улавливания ZгС14 и оросительных конденсаторов (орошение охлажденным до -10 С ТiС14) для конденсации SiС14. Смесь жидких ТiС14 + SiС14 затем разделяют ректификацией. Состав технического тетрахлорида циркония следующий, %: Zг 33-36; С1 58-60; Fе 0,2-0,8; А1 1-1,6; Тi 0,05-0,1; Si « 0,01. Технический хлорид очищают возгонкой.
Тетрахлорид кремния используют для получения кремния и в производстве кремнийорганических соединений.
Хлорирование карбонитрида циркония. В этом технологическом варианте циркон первоначально восстанавливают углеродом при 1900-2000 С с образованием карбида циркония по основной реакции:
ZгSiO4 + 4 С = ZгС + SiO↑ + 3 СО.
Большая часть кремния при этом удаляется в виде монооксида 8Ю, давление пара которого при 1900-2000 С близко к ОД МПа. Поскольку восстановление ведут в присутствии азота воздуха, практически получают карбонитрид -твердый раствор ZгС-ZгN.
Таким образом, в результате восстановления отделяют большую часть кремния (95-96 %) и получают продукт с высоким содержанием циркония, который хлорируется с высокой скоростью.
Восстановление можно проводить в электродуговой печи или, как показали исследования, в печи кипящего слоя с непрерывным питанием ее гранулированной шихтой. Кипящий слой создается потоком азота. Примерный состав карбонитрида, получаемого в печи КС, %: Zг 70-73; Si 2-4; С 6-8; Fе 0,26; Тi 3-5; N 0,6.
Карбонитрид хлорируется с высокой скоростью, начиная с 400 С, причем выделяемого тепла достаточно для самопроизвольного протекания процесса даже в хлораторах небольшого размера. Реакции хлорирования:
ZгС + 2 С12 = ZгС14 + С + 846 кДж;
ZrN + 2 С12 = ZгС14 + 1/2 N2 + 670 кДж.
На одном из предприятий США хлорирование карбонитрида, полученного в результате карбидизации в электродуговой печи, проводили в шахтной печи, схема которой дана на рис. 47.
Шахта печи диаметром 1,0 м и высотой
2,5 м футерована динасовым кирпичом. Хлор поступает в печь через дырчатую графитовую плиту, на которую загружают слой кускового кокса. Процесс начинается с разогрева коксовой постели нагретым воздухом. Затем на нагретую постель загружают карбонитрид и впускают хлор. Интенсивное хлорирование начинается при 400 С и далее продолжается за счет теплоты реакции.
ПРОИЗВОДСТВО ХИМИЧЕСКИХ СОЕДИНЕНИЙ ЦИРКОНИЯ И ГАФНИЯ
Циркониевые минералы, руды и рудные концентраты
Содержание циркония в земной коре относительно высокое - 0,025 % (по массе). По распространенности он превосходит медь, цинк, олово, никель и свинец. Известно около 20 минералов циркония. Они концентрируются главным образом в гранитных и щелочных (нефелин-сиенитовых) пегматитах. Основными промышленными источниками в настоящее время служат минералы бедделеит и циркон. Сырьем могут служить также минералы эвдиалит и эвколит, но они значительно бедней по содержанию циркония.
Бадделеит. По составу представляет собой почти чистый диоксид циркония. В наиболее чистых образцах до 98 % ZrО2. Обычно содержит примесь гафния (до нескольких процентов), изредка уран (до 1 %) и торий (до 0,2 %). Месторождения редки. Плотность минерала 5,5-6. Наиболее крупное месторождение найдено в Бразилии.
Основные методы обогащения руд - гравитационные. Для отделения минералов железа и ильменита используют электромагнитное обогащение.
Циркон - ортосиликат циркония ZrSiО4 (67,2 % ZrО2, 32,8 % SiО2). Это наиболее распространенный минерал циркония. Концентрируется главным образом в пегматитах гранитной и особенно щелочной магмы. Часто встречается в россыпях, образующихся при разрушении коренных пород. Циркон большей частью имеет коричневый цвет, плотность минерала 4,4-4.7 г/см3, твердость 7,5 по минералогической шкале. Минерал обычно содержит гафний (0,5-4 %). Основные запасы циркона сосредоточены в прибрежно-морских россыпях. Здесь циркон накапливается вместе с ильменитом, рутилом, монацитом и рядом других минералов.
Руды, содержащие циркон, обогащают гравитационными методами в сочетании с магнитной и электростатической сепарациями.
Выпускаемые цирконовые концентраты первого сорта должны содержать не менее 65% ZrО2. В них лимитируется содержание следующих примесей, % (не 6oлее): FeO 0,1; TiО2 0,4; A12O3 2,0; СаО и MgO 0,1; P2O5 0,15. Концентраты второго сорта должны содержать не менее 60% ZrО2, примеси не лимитируются.
Наиболее крупные месторождения циркона за рубежом расположены в Австралии, Индии, Бразилии, ЮАР, США. В СНГ циркон найден на Урале, Украине и в других районах страны.
Эвдиалит и эвколит. Состав эвдиалита может быть выражен общей эмпирической формулой: (Nа, Са)6 Zr [Si 6О18][ОН,С1]2.
Эвколит - разновидность эвдиалита, содержащего ионы Fе2+. Химический состав эвдиалита, %: Nа2О 11,6-17,3; ZrO2 12-14,5; FеО 3,1-7,1; SiO2 47,2-51,2; С1 0,7-1,6. Цвет минерала - розовый или малиновый. Минерал легко разлагается кислотами.
Эвдиалит и эвколит встречаются в магматических щелочных породах (нефелиновых сиенитах). Известны месторождения в СССР (на Кольском полуострове), Португалии, Гренландии, Трансваале, Бразилии и других странах.
В капиталистических странах в 1986г. было добыто 830 тыс.т цирконовых концентратов, в том числе в Австралии - 470, ЮАР - 150, США - 85.
Продукты переработки цирконовых концентратов
Цирконовые концентраты служат исходным материалом для производства ферросиликоциркония, ферроциркония и химических соединений циркония: диоксида циркония, фтороцирконата калия и тетрахлорида циркония, а также соединений гафния.
Ферросиликоцирконий непосредственно выплавляют из цирконовых концентратов. Технический диоксид циркония служит исходным материалом для получения ферроциркония и используется в производстве огнеупоров и керамики. Диоксид циркония высокой чистоты применяют для производства высококачественных огнеупорных изделий и порошкообразного циркония. Фтороцирконат калия и тетрахлорид циркония используют главным образом для производства металлического циркония. Ниже рассмотрены основные способы производства соединений циркония.
Производство диоксида циркония
Разложение концентрата
Циркон практически не разлагается соляной, серной и азотной кислотами. Для его разложения с целью перевода циркония в раствор используют большей частью спекание (или сплавление) с содой или спекание с карбонатом кальция (мелом). Образующиеся цирконаты натрия или кальция растворяются в кислотах, из раствора затем выделяют гид-роксид или основные соли циркония. Последние термически разлагают, получая диоксид циркония.
Разложение циркона спеканием с карбонатом натрия. При 1100-1200 °С сода реагирует с цирконом с образованием метацирконата и ортосиликата натрия:
ZrSiO4 + 3Na2CO3= Na2ZrO3+Na4SiO4+2CO2. (4.23)
Процесс можно проводить в барабанных печах непрерывного действия, питая печь гранулированной шихтой (размер гранул 5-10 мм). Грануляцию проводят на чашевом грануляторе при увлажнении шихты. Измельченный спек первоначально выщелачивают водой для извлечения в раствор большей части ортосиликата натрия. Осадки после водного выщелачивания обрабатывают соляной или серной кислотой. В первом случае получают солянокислый раствор, содержащий основной хлорид цирконила ZrОС12, во втором случае - растворы, содержащие основной сульфат циркония Zr(ОН)2SО4. При кислотной обработке образуется кремниевая кислота, для коагуляции которой в пульпу добавляют флокулянт полиакриламид. Осадки отделяют от цирконийсодержащих растворов фильтрацией.
Разложение циркона спекании с карбонатом кальция. Процесс основан на взаимодействии циркона с СаСО3:
ZrSiO4 + 3СаСО3 = СаZrО3 + Са2SiO4 + 3 СО2. (4.24)
Эта реакция протекает с достаточной скоростью лишь при 1400-1500 °С. Однако добавки в шихту небольшого количества хлорида кальция (
5 % от массы цирконового концентрата) позволяют снизить температуру спекания до 1100-1200 °С. Ускорение процесса в присутствии малых добавок СаС12 объясняется, вероятно, частичным образованием жидкой фазы (температура плавления СаС12 774 °С), а также увеличением структурных дефектов в кристаллах компонентов шихты под действием хлористого
кальция.
Рис.45. Технологическая схема переработки цирконового концентрата по способу спекания с карбонатом кальция
Шихту, содержащую измельченный цирконовый концентрат, мел и хлорид кальция, нагревают во вращающихся барабанных печах при 1100-1200 °С в течение 4-5 ч, степень разложения достигает 97-98 %.
Обработку спеков соляной кислотой ведут в две стадии. Первоначально при обработке на холоду 5-10 %-ной соляной кислотой растворяется избыточный оксид кальция и разлагается ортосиликат кальция. Образующаяся колоидная кремниевая кислота удаляется вместе с раствором. Нерастворившийся остаток, содержащий цирконат кальция, выщелачивают 25-30 %-ной НС1 при нагревании до 70-80 °C, получая растворы, содержащие основной хлорид циркония. Примерно по тем же режимам можно выщелачивать известковые спеки азотной кислотой, получая растворы, содержащие Zr(ОН)2(NО3)2. Преимущества последней состоят в возможноти утилизации азотнокислых маточных растворов после излечения из них циркония и получения азотнокислых солей.
В случае применения серной кислоты можно выщелачивать известковый спек в одну стадию без существенных затруднений в отношении отделения раствора от осадка кремниевой кислоты. Обработку спека проводят раствором 300-400 г/л Н2SО4 при температуре не выше 80-90 °С. В этих условиях осадки содержат гидратированные сульфаты кальция СаSО4 • 2 Н2О и СаSО4 • 0,5 Н2О, что обеспечивает хорошую фильтрацию осадков. С целью снижения потерь циркония сульфатный кек, количество которого велико (
6 т на 1т ZrО2) многократно промывают водой. В некоторых производственных схемах рационально сочетается выщелачивание известковых спеков соляной и серной кислотами, что обспечивает получение различных соединений циркония (рис. 45).
Выделение циркония из растворов и получение ZrО2
Растворы, полученные в результате выщелачивания содовых или известковых спеков, содержат цирконий (100-200 г/л) и примеси железа, титана, алюминия, кремния и др. В промышленной практике применяют четыре способа выделения циркония из растворов:
-
Выделение основного хлорида Zr(ОН)2С12•7 Н2О.
-
Выделение основных сульфатов циркония.
-
Осаждение кристаллогидрата сульфата циркония Zг(S04)2•4 Н20.
-
Кристаллизация сульфато-цирконатов натрия или аммония (дубитель для кожевенной промышленности).
Ниже рассмотрены наиболее распространенные первые два способа.
Выделение основного хлорида. Способ основан на малой растворимости кристаллогидрата Zг(ОН)2С12•7 Н2О в концентрированной соляной кислоте, в то время как в воде и разбавленной НС1 растворимость высокая.
Концентрация HCI, г/л
7,2
135,6
231,5
318
370
Растворимость при 20 °С Zг(ОН)2С12•7 Н2О г/л
567,5
164,9
20,5
10,8
17,8
Растворимость основного хлорида в концентрированной НС1 при 70 °С примерно в 5 раз выше, чем при 20 °С. Выпариванием нельзя достигнуть концентрации НС1 выше
220 г/л, так как образуется азеотропная смесь. Однако в кислоте такой концентрации растворимость Zr(ОН)2С12•7 Н2О невысокая (
25 г/л), что позволяет после охлаждения раствора выделить в кристаллы 70-80 % циркония, содержащегося в растворе. Основной хлорид выделяется в виде крупных кристаллов, имеющих форму тетрагональных призм, легко отделяемых от маточного раствора.
Способ дает возможность получить соединения циркония высокой чистоты, так как большинство примесей остается в солянокислом маточном растворе.
Из основного хлорида легко можно получить другие соединения циркония. Для получения ZгО2 основной хлорид растворяют в воде и осаждают добавлением раствора аммиака гидроксид циркония. Прокаливанием последнего при 600-700 °С получают диоксид с содержанием ZгО2 99,6-99,8 %. Для получения других соединений (нитрата, фторидов) гидроксид растворяют в соответствующей кислоте.
Выделение основных сульфатов. Малорастворимые основные сульфаты, состав которых можно выразить общей формулой х ZгО2• у SО3•z Н2О (х>у), выделяются из растворов при рН = 2+3 и мольном отношении SО3:ZгО2 в исходном растворе в пределах 0,55-0,9.
При нейтрализации сернокислого раствора, содержащего значительный избыток кислоты, содой или аммиаком, гидролитическое выделение основного сульфата циркония не происходит. Это объясняется тем, что в таких растворах цирконий находится в составе прочных анионов [ZгО(SО4)2]2-, образующих с катионами натрия и аммония хорошо растворимые соли. Гидролиз наступает лишь в случае вывода части ионов
из растворов, например добавлением ВаС12 или СаС12, что усложняет технологию.
Значительно проще гидролитическое выделение основных сульфатов из солянокислых или азотнокислых растворов, так как в этом случае в раствор вводится дозированное количество сульфат-ионов (добавляют Н2SО4 или Ка2SО4).
Для осаждения основного сульфата в солянокислый раствор, содержащий 40-60 г/л циркония, добавляют Н2SО4 (0,5-0,7 моля на 1 моль ZгО2), нейтрализацией и разбавлением доводят кислотность до 1-1,5 г/л по НС1, а затем нагревают раствор до 70-80 °С. В осадок выделяется 97-98 % циркония, его состав примерно соответствует формуле 2ZгО2-SО3-5 Н2О.
Осадок основного сульфата после промывки, фильтрации и сушки прокаливают для удаления SО3 при 850-900 С в муфельных печах, футерованных высокоглиноземистым огнеупором. Получаемый технический диоксид циркония содержит 97-98 % ZгО2. Основные примеси следующие, %: ТiO2 0,25-0,5; SO2 0,2-0,5; Fе2О3 0,05-0,15; СаО 0,2-0,5; SО3 0,3-0,4.
Получение фтороцирконата калия
Наиболее просто фтороцирконат калия можно получить из цирконового концентрата по технологии, разработанной Н.П.Сажиным и Е.А.Пепеляевой. Способ основан на реакции, протекающей при нагревании циркона с фторосиликатом калия:
ZrSO4 + К2SiF6 = К2ZrF6 + 2 SiO2.
Рuс.46. Диаграмма состояния системы
О Ю 20 30 40 50 60 70
КF %(мол.) ZrF4
Как видно из диаграммы состояния системы КF-ZrF4 (рис.46), выше 600 °С К22гР6 разлагается с образованием К3ZrF7 и расплава, содержащего КF и ZrF4:
2 К2ZrF6 = К3ZrF7 + КF + ZrF4.
Поэтому продукт спекания, помимо К2ZrF6, может содержать некоторое количество К3ZrF7.
Полно циркон разлагается в интервале 650—700 С при условии введения в шихту хлористого калия, подавляющего диссоциацию К2SiF6 с образованием летучего SiF4.
При температурах спекания в шихте в результате взаимодействия компонентов образуется жидкая фаза, что способствует быстрому протеканию процесса. Получающийся в результате разложения спек выщелачивают водой. Из раствора затем кристаллизуют К2ZrF6.
Шихту, состоящую из измельченного циркона, фторосиликата калия (взятого с избытком
50 % от стехиометрического количества) и КС1 (10-40 % от массы циркона) спекают в барабанной печи. Спек состоит из слегка оплавленных гранул размером 0,5-10 мм. Его измельчают и выщелачивают подкисленной водой (1 % НС1) при соотношении Т:Ж = 1:7 и температуре 85 С.
Это позволяет охлаждением раствора до 15 С выкристаллизовать 80-90 % циркония
Из маточного раствора осаждают аммиачной водой гидроксид циркония, который возвращают в шихту для спекания.
Кристаллы К2ZrF6 имеют следующий состав, %: (Zr+Нf) 31,9-32; К 27,2-27,6; F 39,9-40,05; Fе 0,045; Тi 0,042; 81 0,07; С1 0,007; Hf 1,5-2,5 (по отношению к цирконию).
Гафний от циркония можно отделить дробной кристаллизацией соли.
Получение тетрахлорида циркония
Тетрахлорид циркония получают хлорированием трех продуктов: цирконового концентрата, карбида (карбонитрида) циркония, предварительно полученного из концентрата, и диоксида циркония. ,
Хлорирование цирконового концентрата. Цирконовый концентрат в смеси с углеродистым материалом хлорируется с
достаточной для практических целей скоростью при
900-1000 °С. Основные реакции процесса:
2ZrSiО4 + 4 С12 + 2 С = ZгС14 + SiС14 + 2 СО2;
CO2 + C= 2 CO
Теплоты реакции
125кДж недостаточно для самопроизвольного протекания процесса, необходим постоянный подвод тепла. Хлорирование проводят в шахтных хлораторах непрерывного действия, куда загружается брикетированная шихта. При содержании в брикетах 25-30 % углерода брикеты при температуре хлорирования обладают достаточной электропроводностью, что позволяет нагревать шихту с помощью графитовых электродов, вмонтированных в стенках хлоратора. Для прохождения тока через горячую шихту требуется напряжение
ПРОИЗВОДСТВО ХИМИЧЕСКИХ СОЕДИНЕНИЙ ЦИРКОНИЯ И ГАФНИЯ
Циркониевые минералы, руды и рудные концентраты
Содержание циркония в земной коре относительно высокое - 0,025 % (по массе). По распространенности он превосходит медь, цинк, олово, никель и свинец. Известно около 20 минералов циркония. Они концентрируются главным образом в гранитных и щелочных (нефелин-сиенитовых) пегматитах. Основными промышленными источниками в настоящее время служат минералы бедделеит и циркон. Сырьем могут служить также минералы эвдиалит и эвколит, но они значительно бедней по содержанию циркония.
Бадделеит. По составу представляет собой почти чистый диоксид циркония. В наиболее чистых образцах до 98 % ZrО2. Обычно содержит примесь гафния (до нескольких процентов), изредка уран (до 1 %) и торий (до 0,2 %). Месторождения редки. Плотность минерала 5,5-6. Наиболее крупное месторождение найдено в Бразилии.
Основные методы обогащения руд - гравитационные. Для отделения минералов железа и ильменита используют электромагнитное обогащение.
Циркон - ортосиликат циркония ZrSiО4 (67,2 % ZrО2, 32,8 % SiО2). Это наиболее распространенный минерал циркония. Концентрируется главным образом в пегматитах гранитной и особенно щелочной магмы. Часто встречается в россыпях, образующихся при разрушении коренных пород. Циркон большей частью имеет коричневый цвет, плотность минерала 4,4-4.7 г/см3, твердость 7,5 по минералогической шкале. Минерал обычно содержит гафний (0,5-4 %). Основные запасы циркона сосредоточены в прибрежно-морских россыпях. Здесь циркон накапливается вместе с ильменитом, рутилом, монацитом и рядом других минералов.
Руды, содержащие циркон, обогащают гравитационными методами в сочетании с магнитной и электростатической сепарациями.
Выпускаемые цирконовые концентраты первого сорта должны содержать не менее 65% ZrО2. В них лимитируется содержание следующих примесей, % (не 6oлее): FeO 0,1; TiО2 0,4; A12O3 2,0; СаО и MgO 0,1; P2O5 0,15. Концентраты второго сорта должны содержать не менее 60% ZrО2, примеси не лимитируются.
Наиболее крупные месторождения циркона за рубежом расположены в Австралии, Индии, Бразилии, ЮАР, США. В СНГ циркон найден на Урале, Украине и в других районах страны.
Эвдиалит и эвколит. Состав эвдиалита может быть выражен общей эмпирической формулой: (Nа, Са)6 Zr [Si 6О18][ОН,С1]2.
Эвколит - разновидность эвдиалита, содержащего ионы Fе2+. Химический состав эвдиалита, %: Nа2О 11,6-17,3; ZrO2 12-14,5; FеО 3,1-7,1; SiO2 47,2-51,2; С1 0,7-1,6. Цвет минерала - розовый или малиновый. Минерал легко разлагается кислотами.
Эвдиалит и эвколит встречаются в магматических щелочных породах (нефелиновых сиенитах). Известны месторождения в СССР (на Кольском полуострове), Португалии, Гренландии, Трансваале, Бразилии и других странах.
В капиталистических странах в 1986г. было добыто 830 тыс.т цирконовых концентратов, в том числе в Австралии - 470, ЮАР - 150, США - 85.
Продукты переработки цирконовых концентратов
Цирконовые концентраты служат исходным материалом для производства ферросиликоциркония, ферроциркония и химических соединений циркония: диоксида циркония, фтороцирконата калия и тетрахлорида циркония, а также соединений гафния.
Ферросиликоцирконий непосредственно выплавляют из цирконовых концентратов. Технический диоксид циркония служит исходным материалом для получения ферроциркония и используется в производстве огнеупоров и керамики. Диоксид циркония высокой чистоты применяют для производства высококачественных огнеупорных изделий и порошкообразного циркония. Фтороцирконат калия и тетрахлорид циркония используют главным образом для производства металлического циркония. Ниже рассмотрены основные способы производства соединений циркония.
Производство диоксида циркония
Разложение концентрата
Циркон практически не разлагается соляной, серной и азотной кислотами. Для его разложения с целью перевода циркония в раствор используют большей частью спекание (или сплавление) с содой или спекание с карбонатом кальция (мелом). Образующиеся цирконаты натрия или кальция растворяются в кислотах, из раствора затем выделяют гид-роксид или основные соли циркония. Последние термически разлагают, получая диоксид циркония.
Разложение циркона спеканием с карбонатом натрия. При 1100-1200 °С сода реагирует с цирконом с образованием метацирконата и ортосиликата натрия:
ZrSiO4 + 3Na2CO3= Na2ZrO3+Na4SiO4+2CO2. (4.23)
Процесс можно проводить в барабанных печах непрерывного действия, питая печь гранулированной шихтой (размер гранул 5-10 мм). Грануляцию проводят на чашевом грануляторе при увлажнении шихты. Измельченный спек первоначально выщелачивают водой для извлечения в раствор большей части ортосиликата натрия. Осадки после водного выщелачивания обрабатывают соляной или серной кислотой. В первом случае получают солянокислый раствор, содержащий основной хлорид цирконила ZrОС12, во втором случае - растворы, содержащие основной сульфат циркония Zr(ОН)2SО4. При кислотной обработке образуется кремниевая кислота, для коагуляции которой в пульпу добавляют флокулянт полиакриламид. Осадки отделяют от цирконийсодержащих растворов фильтрацией.
Разложение циркона спекании с карбонатом кальция. Процесс основан на взаимодействии циркона с СаСО3:
ZrSiO4 + 3СаСО3 = СаZrО3 + Са2SiO4 + 3 СО2. (4.24)
Эта реакция протекает с достаточной скоростью лишь при 1400-1500 °С. Однако добавки в шихту небольшого количества хлорида кальция (
5 % от массы цирконового концентрата) позволяют снизить температуру спекания до 1100-1200 °С. Ускорение процесса в присутствии малых добавок СаС12 объясняется, вероятно, частичным образованием жидкой фазы (температура плавления СаС12 774 °С), а также увеличением структурных дефектов в кристаллах компонентов шихты под действием хлористого
кальция.
Рис.45. Технологическая схема переработки цирконового концентрата по способу спекания с карбонатом кальция
Шихту, содержащую измельченный цирконовый концентрат, мел и хлорид кальция, нагревают во вращающихся барабанных печах при 1100-1200 °С в течение 4-5 ч, степень разложения достигает 97-98 %.
Обработку спеков соляной кислотой ведут в две стадии. Первоначально при обработке на холоду 5-10 %-ной соляной кислотой растворяется избыточный оксид кальция и разлагается ортосиликат кальция. Образующаяся колоидная кремниевая кислота удаляется вместе с раствором. Нерастворившийся остаток, содержащий цирконат кальция, выщелачивают 25-30 %-ной НС1 при нагревании до 70-80 °C, получая растворы, содержащие основной хлорид циркония. Примерно по тем же режимам можно выщелачивать известковые спеки азотной кислотой, получая растворы, содержащие Zr(ОН)2(NО3)2. Преимущества последней состоят в возможноти утилизации азотнокислых маточных растворов после излечения из них циркония и получения азотнокислых солей.
В случае применения серной кислоты можно выщелачивать известковый спек в одну стадию без существенных затруднений в отношении отделения раствора от осадка кремниевой кислоты. Обработку спека проводят раствором 300-400 г/л Н2SО4 при температуре не выше 80-90 °С. В этих условиях осадки содержат гидратированные сульфаты кальция СаSО4 • 2 Н2О и СаSО4 • 0,5 Н2О, что обеспечивает хорошую фильтрацию осадков. С целью снижения потерь циркония сульфатный кек, количество которого велико (
6 т на 1т ZrО2) многократно промывают водой. В некоторых производственных схемах рационально сочетается выщелачивание известковых спеков соляной и серной кислотами, что обспечивает получение различных соединений циркония (рис. 45).
Выделение циркония из растворов и получение ZrО2
Растворы, полученные в результате выщелачивания содовых или известковых спеков, содержат цирконий (100-200 г/л) и примеси железа, титана, алюминия, кремния и др. В промышленной практике применяют четыре способа выделения циркония из растворов:
-
Выделение основного хлорида Zr(ОН)2С12•7 Н2О.
-
Выделение основных сульфатов циркония.
-
Осаждение кристаллогидрата сульфата циркония Zг(S04)2•4 Н20.
-
Кристаллизация сульфато-цирконатов натрия или аммония (дубитель для кожевенной промышленности).
Ниже рассмотрены наиболее распространенные первые два способа.
Выделение основного хлорида. Способ основан на малой растворимости кристаллогидрата Zг(ОН)2С12•7 Н2О в концентрированной соляной кислоте, в то время как в воде и разбавленной НС1 растворимость высокая.
Концентрация HCI, г/л
7,2
135,6
231,5
318
370
Растворимость при 20 °С Zг(ОН)2С12•7 Н2О г/л
567,5
164,9
20,5
10,8
17,8
Растворимость основного хлорида в концентрированной НС1 при 70 °С примерно в 5 раз выше, чем при 20 °С. Выпариванием нельзя достигнуть концентрации НС1 выше
220 г/л, так как образуется азеотропная смесь. Однако в кислоте такой концентрации растворимость Zr(ОН)2С12•7 Н2О невысокая (
25 г/л), что позволяет после охлаждения раствора выделить в кристаллы 70-80 % циркония, содержащегося в растворе. Основной хлорид выделяется в виде крупных кристаллов, имеющих форму тетрагональных призм, легко отделяемых от маточного раствора.
ПРОИЗВОДСТВО ХИМИЧЕСКИХ СОЕДИНЕНИЙ ЦИРКОНИЯ И ГАФНИЯ
Циркониевые минералы, руды и рудные концентраты
Содержание циркония в земной коре относительно высокое - 0,025 % (по массе). По распространенности он превосходит медь, цинк, олово, никель и свинец. Известно около 20 минералов циркония. Они концентрируются главным образом в гранитных и щелочных (нефелин-сиенитовых) пегматитах. Основными промышленными источниками в настоящее время служат минералы бедделеит и циркон. Сырьем могут служить также минералы эвдиалит и эвколит, но они значительно бедней по содержанию циркония.
Бадделеит. По составу представляет собой почти чистый диоксид циркония. В наиболее чистых образцах до 98 % ZrО2. Обычно содержит примесь гафния (до нескольких процентов), изредка уран (до 1 %) и торий (до 0,2 %). Месторождения редки. Плотность минерала 5,5-6. Наиболее крупное месторождение найдено в Бразилии.
Основные методы обогащения руд - гравитационные. Для отделения минералов железа и ильменита используют электромагнитное обогащение.
Циркон - ортосиликат циркония ZrSiО4 (67,2 % ZrО2, 32,8 % SiО2). Это наиболее распространенный минерал циркония. Концентрируется главным образом в пегматитах гранитной и особенно щелочной магмы. Часто встречается в россыпях, образующихся при разрушении коренных пород. Циркон большей частью имеет коричневый цвет, плотность минерала 4,4-4.7 г/см3, твердость 7,5 по минералогической шкале. Минерал обычно содержит гафний (0,5-4 %). Основные запасы циркона сосредоточены в прибрежно-морских россыпях. Здесь циркон накапливается вместе с ильменитом, рутилом, монацитом и рядом других минералов.
Руды, содержащие циркон, обогащают гравитационными методами в сочетании с магнитной и электростатической сепарациями.
Выпускаемые цирконовые концентраты первого сорта должны содержать не менее 65% ZrО2. В них лимитируется содержание следующих примесей, % (не 6oлее): FeO 0,1; TiО2 0,4; A12O3 2,0; СаО и MgO 0,1; P2O5 0,15. Концентраты второго сорта должны содержать не менее 60% ZrО2, примеси не лимитируются.
Наиболее крупные месторождения циркона за рубежом расположены в Австралии, Индии, Бразилии, ЮАР, США. В СНГ циркон найден на Урале, Украине и в других районах страны.
Эвдиалит и эвколит. Состав эвдиалита может быть выражен общей эмпирической формулой: (Nа, Са)6 Zr [Si 6О18][ОН,С1]2.
Эвколит - разновидность эвдиалита, содержащего ионы Fе2+. Химический состав эвдиалита, %: Nа2О 11,6-17,3; ZrO2 12-14,5; FеО 3,1-7,1; SiO2 47,2-51,2; С1 0,7-1,6. Цвет минерала - розовый или малиновый. Минерал легко разлагается кислотами.
Эвдиалит и эвколит встречаются в магматических щелочных породах (нефелиновых сиенитах). Известны месторождения в СССР (на Кольском полуострове), Португалии, Гренландии, Трансваале, Бразилии и других странах.
В капиталистических странах в 1986г. было добыто 830 тыс.т цирконовых концентратов, в том числе в Австралии - 470, ЮАР - 150, США - 85.
Продукты переработки цирконовых концентратов
Цирконовые концентраты служат исходным материалом для производства ферросиликоциркония, ферроциркония и химических соединений циркония: диоксида циркония, фтороцирконата калия и тетрахлорида циркония, а также соединений гафния.
Ферросиликоцирконий непосредственно выплавляют из цирконовых концентратов. Технический диоксид циркония служит исходным материалом для получения ферроциркония и используется в производстве огнеупоров и керамики. Диоксид циркония высокой чистоты применяют для производства высококачественных огнеупорных изделий и порошкообразного циркония. Фтороцирконат калия и тетрахлорид циркония используют главным образом для производства металлического циркония. Ниже рассмотрены основные способы производства соединений циркония.
Производство диоксида циркония
Разложение концентрата
Циркон практически не разлагается соляной, серной и азотной кислотами. Для его разложения с целью перевода циркония в раствор используют большей частью спекание (или сплавление) с содой или спекание с карбонатом кальция (мелом). Образующиеся цирконаты натрия или кальция растворяются в кислотах, из раствора затем выделяют гид-роксид или основные соли циркония. Последние термически разлагают, получая диоксид циркония.
Разложение циркона спеканием с карбонатом натрия. При 1100-1200 °С сода реагирует с цирконом с образованием метацирконата и ортосиликата натрия:
ZrSiO4 + 3Na2CO3= Na2ZrO3+Na4SiO4+2CO2. (4.23)
Процесс можно проводить в барабанных печах непрерывного действия, питая печь гранулированной шихтой (размер гранул 5-10 мм). Грануляцию проводят на чашевом грануляторе при увлажнении шихты. Измельченный спек первоначально выщелачивают водой для извлечения в раствор большей части ортосиликата натрия. Осадки после водного выщелачивания обрабатывают соляной или серной кислотой. В первом случае получают солянокислый раствор, содержащий основной хлорид цирконила ZrОС12, во втором случае - растворы, содержащие основной сульфат циркония Zr(ОН)2SО4. При кислотной обработке образуется кремниевая кислота, для коагуляции которой в пульпу добавляют флокулянт полиакриламид. Осадки отделяют от цирконийсодержащих растворов фильтрацией.
Разложение циркона спекании с карбонатом кальция. Процесс основан на взаимодействии циркона с СаСО3:
ZrSiO4 + 3СаСО3 = СаZrО3 + Са2SiO4 + 3 СО2. (4.24)
Эта реакция протекает с достаточной скоростью лишь при 1400-1500 °С. Однако добавки в шихту небольшого количества хлорида кальция (
5 % от массы цирконового концентрата) позволяют снизить температуру спекания до 1100-1200 °С. Ускорение процесса в присутствии малых добавок СаС12 объясняется, вероятно, частичным образованием жидкой фазы (температура плавления СаС12 774 °С), а также увеличением структурных дефектов в кристаллах компонентов шихты под действием хлористого
кальция.
Рис.45. Технологическая схема переработки цирконового концентрата по способу спекания с карбонатом кальция
Шихту, содержащую измельченный цирконовый концентрат, мел и хлорид кальция, нагревают во вращающихся барабанных печах при 1100-1200 °С в течение 4-5 ч, степень разложения достигает 97-98 %.
Обработку спеков соляной кислотой ведут в две стадии. Первоначально при обработке на холоду 5-10 %-ной соляной кислотой растворяется избыточный оксид кальция и разлагается ортосиликат кальция. Образующаяся колоидная кремниевая кислота удаляется вместе с раствором. Нерастворившийся остаток, содержащий цирконат кальция, выщелачивают 25-30 %-ной НС1 при нагревании до 70-80 °C, получая растворы, содержащие основной хлорид циркония. Примерно по тем же режимам можно выщелачивать известковые спеки азотной кислотой, получая растворы, содержащие Zr(ОН)2(NО3)2. Преимущества последней состоят в возможноти утилизации азотнокислых маточных растворов после излечения из них циркония и получения азотнокислых солей.
В случае применения серной кислоты можно выщелачивать известковый спек в одну стадию без существенных затруднений в отношении отделения раствора от осадка кремниевой кислоты. Обработку спека проводят раствором 300-400 г/л Н2SО4 при температуре не выше 80-90 °С. В этих условиях осадки содержат гидратированные сульфаты кальция СаSО4 • 2 Н2О и СаSО4 • 0,5 Н2О, что обеспечивает хорошую фильтрацию осадков. С целью снижения потерь циркония сульфатный кек, количество которого велико (
6 т на 1т ZrО2) многократно промывают водой. В некоторых производственных схемах рационально сочетается выщелачивание известковых спеков соляной и серной кислотами, что обспечивает получение различных соединений циркония (рис. 45).ПРОИЗВОДСТВО ХИМИЧЕСКИХ СОЕДИНЕНИЙ ЦИРКОНИЯ И ГАФНИЯ
Циркониевые минералы, руды и рудные концентраты
Содержание циркония в земной коре относительно высокое - 0,025 % (по массе). По распространенности он превосходит медь, цинк, олово, никель и свинец. Известно около 20 минералов циркония. Они концентрируются главным образом в гранитных и щелочных (нефелин-сиенитовых) пегматитах. Основными промышленными источниками в настоящее время служат минералы бедделеит и циркон. Сырьем могут служить также минералы эвдиалит и эвколит, но они значительно бедней по содержанию циркония.
Бадделеит. По составу представляет собой почти чистый диоксид циркония. В наиболее чистых образцах до 98 % ZrО2. Обычно содержит примесь гафния (до нескольких процентов), изредка уран (до 1 %) и торий (до 0,2 %). Месторождения редки. Плотность минерала 5,5-6. Наиболее крупное месторождение найдено в Бразилии.
Основные методы обогащения руд - гравитационные. Для отделения минералов железа и ильменита используют электромагнитное обогащение.
Циркон - ортосиликат циркония ZrSiО4 (67,2 % ZrО2, 32,8 % SiО2). Это наиболее распространенный минерал циркония. Концентрируется главным образом в пегматитах гранитной и особенно щелочной магмы. Часто встречается в россыпях, образующихся при разрушении коренных пород. Циркон большей частью имеет коричневый цвет, плотность минерала 4,4-4.7 г/см3, твердость 7,5 по минералогической шкале. Минерал обычно содержит гафний (0,5-4 %). Основные запасы циркона сосредоточены в прибрежно-морских россыпях. Здесь циркон накапливается вместе с ильменитом, рутилом, монацитом и рядом других минералов.
Руды, содержащие циркон, обогащают гравитационными методами в сочетании с магнитной и электростатической сепарациями.
Выпускаемые цирконовые концентраты первого сорта должны содержать не менее 65% ZrО2. В них лимитируется содержание следующих примесей, % (не 6oлее): FeO 0,1; TiО2 0,4; A12O3 2,0; СаО и MgO 0,1; P2O5 0,15. Концентраты второго сорта должны содержать не менее 60% ZrО2, примеси не лимитируются.
Наиболее крупные месторождения циркона за рубежом расположены в Австралии, Индии, Бразилии, ЮАР, США. В СНГ циркон найден на Урале, Украине и в других районах страны.
Эвдиалит и эвколит. Состав эвдиалита может быть выражен общей эмпирической формулой: (Nа, Са)6 Zr [Si 6О18][ОН,С1]2.
Эвколит - разновидность эвдиалита, содержащего ионы Fе2+. Химический состав эвдиалита, %: Nа2О 11,6-17,3; ZrO2 12-14,5; FеО 3,1-7,1; SiO2 47,2-51,2; С1 0,7-1,6. Цвет минерала - розовый или малиновый. Минерал легко разлагается кислотами.
Эвдиалит и эвколит встречаются в магматических щелочных породах (нефелиновых сиенитах). Известны месторождения в СССР (на Кольском полуострове), Португалии, Гренландии, Трансваале, Бразилии и других странах.
В капиталистических странах в 1986г. было добыто 830 тыс.т цирконовых концентратов, в том числе в Австралии - 470, ЮАР - 150, США - 85.
Продукты переработки цирконовых концентратов
Цирконовые концентраты служат исходным материалом для производства ферросиликоциркония, ферроциркония и химических соединений циркония: диоксида циркония, фтороцирконата калия и тетрахлорида циркония, а также соединений гафния.
Ферросиликоцирконий непосредственно выплавляют из цирконовых концентратов. Технический диоксид циркония служит исходным материалом для получения ферроциркония и используется в производстве огнеупоров и керамики. Диоксид циркония высокой чистоты применяют для производства высококачественных огнеупорных изделий и порошкообразного циркония. Фтороцирконат калия и тетрахлорид циркония используют главным образом для производства металлического циркония. Ниже рассмотрены основные способы производства соединений циркония.
Производство диоксида циркония
Разложение концентрата
Циркон практически не разлагается соляной, серной и азотной кислотами. Для его разложения с целью перевода циркония в раствор используют большей частью спекание (или сплавление) с содой или спекание с карбонатом кальция (мелом). Образующиеся цирконаты натрия или кальция растворяются в кислотах, из раствора затем выделяют гид-роксид или основные соли циркония. Последние термически разлагают, получая диоксид циркония.
Разложение циркона спеканием с карбонатом натрия. При 1100-1200 °С сода реагирует с цирконом с образованием метацирконата и ортосиликата натрия:
ZrSiO4 + 3Na2CO3= Na2ZrO3+Na4SiO4+2CO2. (4.23)
Процесс можно проводить в барабанных печах непрерывного действия, питая печь гранулированной шихтой (размер гранул 5-10 мм). Грануляцию проводят на чашевом грануляторе при увлажнении шихты. Измельченный спек первоначально выщелачивают водой для извлечения в раствор большей части ортосиликата натрия. Осадки после водного выщелачивания обрабатывают соляной или серной кислотой. В первом случае получают солянокислый раствор, содержащий основной хлорид цирконила ZrОС12, во втором случае - растворы, содержащие основной сульфат циркония Zr(ОН)2SО4. При кислотной обработке образуется кремниевая кислота, для коагуляции которой в пульпу добавляют флокулянт полиакриламид. Осадки отделяют от цирконийсодержащих растворов фильтрацией.
Разложение циркона спекании с карбонатом кальция. Процесс основан на взаимодействии циркона с СаСО3:
ZrSiO4 + 3СаСО3 = СаZrО3 + Са2SiO4 + 3 СО2. (4.24)
Эта реакция протекает с достаточной скоростью лишь при 1400-1500 °С. Однако добавки в шихту небольшого количества хлорида кальция (
Выделение циркония из растворов и получение ZrО2
Растворы, полученные в результате выщелачивания содовых или известковых спеков, содержат цирконий (100-200 г/л) и примеси железа, титана, алюминия, кремния и др. В промышленной практике применяют четыре способа выделения циркония из растворов:
-
Выделение основного хлорида Zr(ОН)2С12•7 Н2О. -
Выделение основных сульфатов циркония. -
Осаждение кристаллогидрата сульфата циркония Zг(S04)2•4 Н20. -
Кристаллизация сульфато-цирконатов натрия или аммония (дубитель для кожевенной промышленности).
Ниже рассмотрены наиболее распространенные первые два способа.
Выделение основного хлорида. Способ основан на малой растворимости кристаллогидрата Zг(ОН)2С12•7 Н2О в концентрированной соляной кислоте, в то время как в воде и разбавленной НС1 растворимость высокая.
Концентрация HCI, г/л | 7,2 | 135,6 | 231,5 | 318 | 370 |
Растворимость при 20 °С Zг(ОН)2С12•7 Н2О г/л | 567,5 | 164,9 | 20,5 | 10,8 | 17,8 |
Растворимость основного хлорида в концентрированной НС1 при 70 °С примерно в 5 раз выше, чем при 20 °С. Выпариванием нельзя достигнуть концентрации НС1 выше
Способ дает возможность получить соединения циркония высокой чистоты, так как большинство примесей остается в солянокислом маточном растворе.
Из основного хлорида легко можно получить другие соединения циркония. Для получения ZгО2 основной хлорид растворяют в воде и осаждают добавлением раствора аммиака гидроксид циркония. Прокаливанием последнего при 600-700 °С получают диоксид с содержанием ZгО2 99,6-99,8 %. Для получения других соединений (нитрата, фторидов) гидроксид растворяют в соответствующей кислоте.
Выделение основных сульфатов. Малорастворимые основные сульфаты, состав которых можно выразить общей формулой х ZгО2• у SО3•z Н2О (х>у), выделяются из растворов при рН = 2+3 и мольном отношении SО3:ZгО2 в исходном растворе в пределах 0,55-0,9.
При нейтрализации сернокислого раствора, содержащего значительный избыток кислоты, содой или аммиаком, гидролитическое выделение основного сульфата циркония не происходит. Это объясняется тем, что в таких растворах цирконий находится в составе прочных анионов [ZгО(SО4)2]2-, образующих с катионами натрия и аммония хорошо растворимые соли. Гидролиз наступает лишь в случае вывода части ионов

Значительно проще гидролитическое выделение основных сульфатов из солянокислых или азотнокислых растворов, так как в этом случае в раствор вводится дозированное количество сульфат-ионов (добавляют Н2SО4 или Ка2SО4).
Для осаждения основного сульфата в солянокислый раствор, содержащий 40-60 г/л циркония, добавляют Н2SО4 (0,5-0,7 моля на 1 моль ZгО2), нейтрализацией и разбавлением доводят кислотность до 1-1,5 г/л по НС1, а затем нагревают раствор до 70-80 °С. В осадок выделяется 97-98 % циркония, его состав примерно соответствует формуле 2ZгО2-SО3-5 Н2О.
Осадок основного сульфата после промывки, фильтрации и сушки прокаливают для удаления SО3 при 850-900 С в муфельных печах, футерованных высокоглиноземистым огнеупором. Получаемый технический диоксид циркония содержит 97-98 % ZгО2. Основные примеси следующие, %: ТiO2 0,25-0,5; SO2 0,2-0,5; Fе2О3 0,05-0,15; СаО 0,2-0,5; SО3 0,3-0,4.
Получение фтороцирконата калия
Наиболее просто фтороцирконат калия можно получить из цирконового концентрата по технологии, разработанной Н.П.Сажиным и Е.А.Пепеляевой. Способ основан на реакции, протекающей при нагревании циркона с фторосиликатом калия:
ZrSO4 + К2SiF6 = К2ZrF6 + 2 SiO2.
Рuс.46. Диаграмма состояния системы
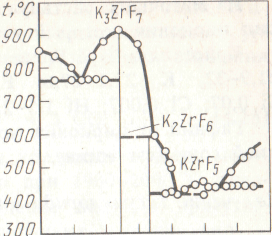
О Ю 20 30 40 50 60 70
КF %(мол.) ZrF4
Как видно из диаграммы состояния системы КF-ZrF4 (рис.46), выше 600 °С К22гР6 разлагается с образованием К3ZrF7 и расплава, содержащего КF и ZrF4:
2 К2ZrF6 = К3ZrF7 + КF + ZrF4.
Поэтому продукт спекания, помимо К2ZrF6, может содержать некоторое количество К3ZrF7.
Полно циркон разлагается в интервале 650—700 С при условии введения в шихту хлористого калия, подавляющего диссоциацию К2SiF6 с образованием летучего SiF4.
При температурах спекания в шихте в результате взаимодействия компонентов образуется жидкая фаза, что способствует быстрому протеканию процесса. Получающийся в результате разложения спек выщелачивают водой. Из раствора затем кристаллизуют К2ZrF6.
Шихту, состоящую из измельченного циркона, фторосиликата калия (взятого с избытком