ВУЗ: Не указан
Категория: Не указан
Дисциплина: Не указана
Добавлен: 16.03.2024
Просмотров: 89
Скачиваний: 0
ВНИМАНИЕ! Если данный файл нарушает Ваши авторские права, то обязательно сообщите нам.
СОДЕРЖАНИЕ
2 (173-180) обусловила ее применение (а также титаната бария) для изготовления твердых диэлектриков в производстве конденсаторов, радиоаппаратуры, высокочастотных печей.
Мощность заводов по производству диоксида титана в капиталистических странах составила в 1985 г. 2770 тыс.т.
Области применения циркония
Цирконий, его сплавы и соединения используют в различных областях техники: атомной энергетике, электронике, пиротехнике, машиностроении, производстве сталей и сплавов с цветными металлами, огнеупоров, керамики и эмалей, в литейном производстве.
Атомная энергетика. Цирконий, очищенный от примеси гафния, обладает низким сечением захвата тепловых нейтронов, тугоплавкостью, антикоррозионной стойкостью и хорошими механическими свойствами. Это привлекло к нему внимание в начале 50-х годов как к ценному конструкционному материалу для изготовления защитных оболочек урановых тепловыделяющих элементов, труб, в которых циркулирует теплопередающая жидкость, и других конструктивных элементов ядерных реакторов.
Для улучшения свойств циркония его легируют добавками олова (1,4-1,6%); железа (0,1-0,15%), хрома (0,08 -0,12%), никеля (0,04-0,06%).
Электроника. В этой области используют способность циркония поглощать газы (служить геттером) для поддержания высокого вакуума в электронном приборе. С этой целью порошок циркония наносят на поверхность анодов, сеток и других деталей. Циркониевую фольгу применяют в качестве фильтра в рентгеновских трубках с молибденовыми антикатодами.
Пиротехника и производствобоеприпасов. Порошки циркония, имеющие низкую температуру воспламенения и высокую скорость сгорания, применяют в качестве воспламенителя в смесях капсулей-детонаторов, а также в смесях для фотовспышки. В смеси с окислителями [В(NO)3)2, КClO3] порошки циркония образуют бездымный порох.
Машиностроение. В связи с расширением производства ковкого циркония и сплавов на его основе привлечено внимание к его использованию в химическом машиностроении как кислотостойкого материала (детали центрифуг, насосы, конденсаторы, испарители и др.), в общем машиностроении (поршни, шатуны, тяги и др.) И турбостроении (лопасти турбин и другие детали).
Стали и сплавы с цветными металлами. Цирконий - эффективный раскислитель и деазотизатор сталей. Кроме того, он ценный легирующий элемент вводимый в некоторые сорта броневых и орудийных сталей, коррозионностойких и жаропрочных сталей. Для введения в стали используют ферросиликоцирконий (40-45 % Zг, 20-24 % Si, остальное железо). Цирконий входит в состав ряда сплавов на основе цветных металлов.
Цирконием легируют медь (0,1-5 % Zr) для улучшения прочностных характеристик. Получили распространение сплавы магния, легированные цирконием для придания им мелкозернистой структуры. Цирконий добавляют в свинцовистые бронзы, что предотвращает сегрегацию свинца в сплаве. Высокой прочностью и электропроводностью обладают меднокадмиевые сплавы, содержащие 0,35 % Zr.
В последние годы разработаны сверхпроводящие сплавы, содержащие цирконий. В частности, сплав 75 % Nb- 25 % Zr используют для изготовления электромагнитов с высоким напряжением магнитного поля.
Производство огнеупоров, фарфора, эмалей и стекла. В этих областях используют более половины общего потребления циркония. В качестве огнеупора применяют минерал циркон ZrSiО4и диоксид циркония. Последний обычно стабилизируют добавками оксидов кальция, магния или иттрия, исключающих растрескивание изделий при нагревании вследствие стабилизации высокотемпературной кубической модификации. Из диоксида циркония и циркона изготовляют кирпич для металлургических печей, тигли и другие изделия.
Диоксид циркония и его минералы вводят в состав электротехнического фарфора для линий электропередач, высокочастотных установок и запальных свечей двигателей внутреннего сгорания. Их вводят также в состав эмалей (для придания им белого цвета и кислотостойкости) и в состав некоторых сортов стекла (повышается устойчивость стекла против действия растворов щелочей).
Литейное производство. В этой области используют значительную долю цирконовых концентратов для присыпки литейных форм с целью получения хорошей поверхности отливок.
Прочие области применения. Среди других областей следует упомянуть применение ZrО2 в синтезе пьезокерамических материалов (цирконотитанаты свинца и др.) и I для полировки оптического стекла; применение ZrО2 или смеси ZrО2-V2О3 в качестве твердого электролита в высокотемпературных топливных элементах (1000 °С и выше); использование двойных сульфатов циркония в качестве дубителя в сожевенной промышленности; тетрахлорида и оксихлорида циркония для приготовления катализаторов, используемых в синтезе органических соединений.
Примерное распределение циркония по областям потребления следующее, %: литейное производство 42, огнеупоры 30, керамика 12, абразивы 4, металл, сплавы и другое применение 12.
Области применения гафния
Промышленное производство гафния возникло в 1950-1951 гг. Вследствие высокого сечения захвата тепловых нейтронов (115 • 10-24 см2) металл и его соединения (HfО2, НfB2) используют в регулирующих и защитных устройствах ядерных реакторов. Вторая перспективная область -производство тугоплавких и жаропрочных материалов. Так, перспективно использование карбида гафния (температура плавления 3890 °С), а также твердого раствора 25 % НfС + 75 % ТаС (tпл = 4200 °С). Высокой жаропрочностью отличаются сплавы гафния с другими тугоплавкими металлами (танталом, ниобием, вольфрамом).
Намечается использование гафния в электровакуумной технике (катоды накаливания радиоламп и газоразрядных трубок) и для изготовления нитей накаливания электроламп.
Примерные масштабы мирового производства гафния в 1985 г. 100 т.
2 м от выгрузки. Хлорирование проводят при 950-1000 °С.
Мощность заводов по производству диоксида титана в капиталистических странах составила в 1985 г. 2770 тыс.т.
Области применения циркония
Цирконий, его сплавы и соединения используют в различных областях техники: атомной энергетике, электронике, пиротехнике, машиностроении, производстве сталей и сплавов с цветными металлами, огнеупоров, керамики и эмалей, в литейном производстве.
Атомная энергетика. Цирконий, очищенный от примеси гафния, обладает низким сечением захвата тепловых нейтронов, тугоплавкостью, антикоррозионной стойкостью и хорошими механическими свойствами. Это привлекло к нему внимание в начале 50-х годов как к ценному конструкционному материалу для изготовления защитных оболочек урановых тепловыделяющих элементов, труб, в которых циркулирует теплопередающая жидкость, и других конструктивных элементов ядерных реакторов.
Для улучшения свойств циркония его легируют добавками олова (1,4-1,6%); железа (0,1-0,15%), хрома (0,08 -0,12%), никеля (0,04-0,06%).
Электроника. В этой области используют способность циркония поглощать газы (служить геттером) для поддержания высокого вакуума в электронном приборе. С этой целью порошок циркония наносят на поверхность анодов, сеток и других деталей. Циркониевую фольгу применяют в качестве фильтра в рентгеновских трубках с молибденовыми антикатодами.
Пиротехника и производствобоеприпасов. Порошки циркония, имеющие низкую температуру воспламенения и высокую скорость сгорания, применяют в качестве воспламенителя в смесях капсулей-детонаторов, а также в смесях для фотовспышки. В смеси с окислителями [В(NO)3)2, КClO3] порошки циркония образуют бездымный порох.
Машиностроение. В связи с расширением производства ковкого циркония и сплавов на его основе привлечено внимание к его использованию в химическом машиностроении как кислотостойкого материала (детали центрифуг, насосы, конденсаторы, испарители и др.), в общем машиностроении (поршни, шатуны, тяги и др.) И турбостроении (лопасти турбин и другие детали).
Стали и сплавы с цветными металлами. Цирконий - эффективный раскислитель и деазотизатор сталей. Кроме того, он ценный легирующий элемент вводимый в некоторые сорта броневых и орудийных сталей, коррозионностойких и жаропрочных сталей. Для введения в стали используют ферросиликоцирконий (40-45 % Zг, 20-24 % Si, остальное железо). Цирконий входит в состав ряда сплавов на основе цветных металлов.
Цирконием легируют медь (0,1-5 % Zr) для улучшения прочностных характеристик. Получили распространение сплавы магния, легированные цирконием для придания им мелкозернистой структуры. Цирконий добавляют в свинцовистые бронзы, что предотвращает сегрегацию свинца в сплаве. Высокой прочностью и электропроводностью обладают меднокадмиевые сплавы, содержащие 0,35 % Zr.
В последние годы разработаны сверхпроводящие сплавы, содержащие цирконий. В частности, сплав 75 % Nb- 25 % Zr используют для изготовления электромагнитов с высоким напряжением магнитного поля.
Производство огнеупоров, фарфора, эмалей и стекла. В этих областях используют более половины общего потребления циркония. В качестве огнеупора применяют минерал циркон ZrSiО4и диоксид циркония. Последний обычно стабилизируют добавками оксидов кальция, магния или иттрия, исключающих растрескивание изделий при нагревании вследствие стабилизации высокотемпературной кубической модификации. Из диоксида циркония и циркона изготовляют кирпич для металлургических печей, тигли и другие изделия.
Диоксид циркония и его минералы вводят в состав электротехнического фарфора для линий электропередач, высокочастотных установок и запальных свечей двигателей внутреннего сгорания. Их вводят также в состав эмалей (для придания им белого цвета и кислотостойкости) и в состав некоторых сортов стекла (повышается устойчивость стекла против действия растворов щелочей).
Литейное производство. В этой области используют значительную долю цирконовых концентратов для присыпки литейных форм с целью получения хорошей поверхности отливок.
Прочие области применения. Среди других областей следует упомянуть применение ZrО2 в синтезе пьезокерамических материалов (цирконотитанаты свинца и др.) и I для полировки оптического стекла; применение ZrО2 или смеси ZrО2-V2О3 в качестве твердого электролита в высокотемпературных топливных элементах (1000 °С и выше); использование двойных сульфатов циркония в качестве дубителя в сожевенной промышленности; тетрахлорида и оксихлорида циркония для приготовления катализаторов, используемых в синтезе органических соединений.
Примерное распределение циркония по областям потребления следующее, %: литейное производство 42, огнеупоры 30, керамика 12, абразивы 4, металл, сплавы и другое применение 12.
Области применения гафния
Промышленное производство гафния возникло в 1950-1951 гг. Вследствие высокого сечения захвата тепловых нейтронов (115 • 10-24 см2) металл и его соединения (HfО2, НfB2) используют в регулирующих и защитных устройствах ядерных реакторов. Вторая перспективная область -производство тугоплавких и жаропрочных материалов. Так, перспективно использование карбида гафния (температура плавления 3890 °С), а также твердого раствора 25 % НfС + 75 % ТаС (tпл = 4200 °С). Высокой жаропрочностью отличаются сплавы гафния с другими тугоплавкими металлами (танталом, ниобием, вольфрамом).
Намечается использование гафния в электровакуумной технике (катоды накаливания радиоламп и газоразрядных трубок) и для изготовления нитей накаливания электроламп.
Примерные масштабы мирового производства гафния в 1985 г. 100 т.
- 1 2 3 4 5
ПРОИЗВОДСТВО ХИМИЧЕСКИХ СОЕДИНЕНИЙ ТИТАНА
Титановые минералы, руды и рудные концентраты
В ряду распространенности элементов титан занимает де вятое место, содержание его в земной коре 0,61 % (по массе). Титан встречается во всех изверженных и осадочных породах, а также в почве, торфе, каменном угле, растениях, крови, костях животных.
Титан встречается в земной коре в виде диоксида, титанатов и сложных комплексных титанониобатов и силикатов,
Известно около 70 минералов титана, наибольшее промышленное значение имеют рутил, ильменит, перовскит и сфен, являющиеся собственно титановыми минералами.
Рутил - природный диоксид титана (другие модификации -анатаз и брукит). Обычно содержит примесь оксида железа (II) FеО. Плотность 4,18-4,28 г/см3. Цвет большей частью красно-коричневый. Крупные месторождения редки. Рутиловые концентраты содержат 90-95 % ТiO2.
Ильменит - титанат железа FеО-ТiO2 наиболее распространенный минерал титана. Впервые найден на Урале в Ильменских горах. Минерал бурого или буро-черного цвета. Плотность 4,56-5,21 г/см3. При длительном выветривании ильменит переходит в аризонит (Fe2O3∙3TiO2) и лейкоксен (TiO2∙nH2O). Это объясняет более высокое содержание TiO2 в некоторых ильменитах, чем это соответствует формуле (52,66 %).
Часто ильменит находится в тесной связи с магнетитом. Такие руды называют титаномагнетитами.
Ильменит добывают преимущественно из речных и прибрежно-морских россыпей. Эксплуатируемые россыпи содержат от единиц до нескольких десятков килограммов ильменита на 1 м3 песков. Пески часто бывают комплексным сырьем. Так, пески Самотканского месторождения на Украине содержат рутил, ильменит, циркон, а также минералы алюминия - дистен.
* По структуре титанаты относятся к типу смешанных оксидов.
Al2O3·SiO2 и ставролит Fe(OH)2·2AlSiO5.
Крупные россыпи ильменитовых песков найдены в Индии, Австралии, Индонезии, Африке, Южной Америке, США и России.
Важный источник ильменита - титаномагнетитовые месторождения. Крупнейшие из них известны в Канаде, России, Скандинавии, Бразилии.
Перовскит - титанат кальция СаО • ТiO2 (58,7 % ТiO2). Часто содержит примеси ниобия, иттрия, марганца, магния. Плотность 3,95-4,04 г/см3. Цвет черный, красно-бурый.
Крупные месторождения найдены в СССР на Кольском полуострове. В перспективе может стать важным источником получения титана.
Сфен или титанит — титаносиликат кальция CaO-TiO2-SiO2 (38,8% TiO2). Цвет желтый, плотность 3,4-3,56 г/см3. Месторождения найдены во многих районах СССР, известны в США, Канаде и Мадагаскаре. Может служить титановым сырьем при комплексной добыче с другими рудами (апатитом и нефелином).
При обогащении ильменитовых песков вначале гравитационными методами извлекают тяжелые минералы (магнетит, ильменит, рутил, циркон и др.), получая так называемые черные шлихи. Для разделения шлихов используют электромагнитные и электростатические методы. Если магнитную проницаемость железа принять за 100, то для магнетита она равна 40,2, для ильменита 24,7, для рутила 0,4, для силикатов меньше 0,2. Изменяя напряженность магнитного поля, отделяют магнетит от ильменита, а последний от рутила.
Таблица 6. Примерный состав титановых концентратов, выпускаемых в СССР
Концентрат
Состав концентрата, % (по массе)
TiO2
FeO
Fe2O3
SiO2
Ai2O3
Cr2O3
MgO
CaO
V2O5
Уральский
44,0
31,4
16,9
1,8
2,5
-
2,8
1,3
-
Иршинский
48,7
45,9
-
3,9
0,5
-
1,3
1,1
-
Самотканский
(аризонитовый)
60,3
-
25,3
1,2
2,0
1,4
0,9
0,2
-
Рутиловый
93,2
1,8
-
2,0
1,1
0,3
-
0,2
0,11
При обогащении титаномагнетитовых руд с крупной вкрапленностью ильменита также используют магнитную сепарацию. Некоторые титаномагнетиты не поддаются механическому обогащению. В этом случае применяют металлургическое обогащение - плавку в электропечах с получением чугуна и богатого титаном шлака. Из ильменитовых концентратов выплавляют шлаки с содержанием 75-85 % TiO2. Кроме того, из них в результате химического обогащения получают синтетический рутил с содержанием 90-97 % TiO2.
В табл.6 приведен примерный состав титановых концентратов, выпускаемых в СССР.
Продукты переработки титановых концентратов
Из титановых концентратов непосредственно получают три вида продуктов: тетрахлорид титана, диоксид титана и ферротитан.
Рисунок 39 Общая схема производства тетрахлормда титана и диоксида титана из кльменитового концентрата.
Тетрахлорид титана - основное исходное соединение для производства металлического титана. Для этой цели получают хлорид высокой чистоты, представляющий собой бесцветную (или слегка окрашенную в желтый цвет) жидкость. Диоксид титана выпускают различной степени чистоты: пигментный, содержащий 94-98,5 % TiO2; повышенной чистоты (не ниже 99,5 % TiO2) для производства твердых сплавов и металлического титана; для приготовления лигатур с никелем, медью, алюминием с содержанием TiO2 не ниже 99 %; для обмазки сварочных электродов с содержанием не ниже 97,5 % TiO2.
Ферротитан выплавляют из ильменитовых концентратов алюминотермическим способом. Сплавы содержат 25-30 % Тi; 5-8 % А1; 3-4 % Si; остальное - железо.
Ниже рассмотрены промышленные способы производства те-трахлорида титана и диоксида титана из основного сырья -ильменитовых концентратов.
На рис. 39 приведена общая схема переработки ильменитового концентрата. Видно, что хлорид титана производят хлорированием титанового шлака или "синтетического рутила", получаемых из концентрата. Диоксид титана производят двумя способами - сернокислотным или "сжиганием" тетрахлорида титана.
Выплавка титанового шлака из ильменита
Высокое содержание железа (40-48 % FеО + Fе2О3) затрудняет получение хлорида титана из ильменита. При прямом хлорировании концентрата на образование хлорида железа затрачивается много хлора, регенерация которого—из хлорного железа затруднительна.
Для отеделения железа проводят восстановительную плавку ильменита с получением чугуна и титанового шлака (80-87 % TiO2). Разделение титана и железа в этом процессе основано на большом различии сродства к кислороду у железа и титана.
Восстановительную плавку ведут в трехфазных электродуговых печах, подобных применяемым в производстве ферросплавов, мощностью 5-20 МВт (рис. 40). Ванна печи футерована магнезитовыми огнеупорами. Для защиты футеровки стен от быстрого разъедания шлаком на них предварительно наращивают гарниссаж — слой застывшего тугоплавкого шлака.
Рисунок 40. Схема электродуговой печи мощностью 5 МВт для выплавки титановых шлаков:
1 - кожух; 2 - футеровка (магнезитовый кирпич); 3 - электроды; 4 - токопод-водящие щеки; 5 - водоохлаждаемый свод; 6 - вентиляционная труба; 7 - бункера с шихтой; 8 - система подвески и перепуска электродов; 9 - труботечки для подачи шихты; 10 - гарниссаж; 11 - шлак; 12 - летка; 13 – чугун
Для защиты подины от разъедания на ней постоянно поддерживают высокий слой чугуна (
0,5 м). Внутренние размеры плавильного пространства печи: диаметр 4,55м, глубина ванны 2,175м.
Охлаждаемый свод печи - съемный. Герметизация печи осуществляется с помощью песочного затвора между оа нием свода и кожухом печи. Через отверстия в своде ванну вводят закрепленные в электрододержателях три графитированных электрода (диаметром 0,5м), связанные с системой их перепуска. Перепуск электродов приводится в действие по мере их выгорания при отключенной печи высоту примерно 100-150 мм.
Плавку ведут с закрытым колошником, т.е. с дугами, закрытыми шихтой (электроды глубоко погружены в шихту). Шихту (концентрат в смеси с коксом) из бункеров по труботечкам загружают возле электродов и между ними. Плавку ведут на порошковой или брикетированной шихте. Применяют также комбинированную шихту из смеси брикетов и порошковой шихты.
При восстановлении ильменита в различных температурных интервалах протекают следующие реакции:
примерно до 1240 °С:
FеО • ТiO2 + С = Fе + ТiO2 + СО,
3 ТiO2 + С = Тi3O5 + СО;
при 1270-1400 °С (4.1)
2 Тi3O5 + С = 3 Тi2O3 + СО;
при 1400-1600 °С
Тi2O3 + С = 2 ТiO + СО.
В процессе плавки образуются сложные соединения, кристаллизующиеся при затвердевании шлака. Главное из них аносовит, в основе которого промежуточный оксид Тi3O5.
Состав аносовита можно представить общей формулой:
m[(Mg, Fe, Ті)O • 2TiO2 ]• n[(Al, Fe, Ті)2O3 • TiO2].
В аносовите титан находится в состояниях окисления Ті4+, Ті3+, Ті2+. Кроме аносовита, а также некоторых других сложных соединений в шлаках может присутствовать оксикарбонитрид Ti (C,O,N), который представляет собой твердые растворы ТіС, ТіО и TiN, обладающие однотипной кристаллической решеткой. Оксикарбонитрид образуется при температурах выше 1600 °С.
Низшие оксиды и особенно оксикарбонитрид повышают температуру плавления и вязкость шлаков. Эти параметры можно снизить добавками флюсов (CaO, MgO, А12O3). Однако стремятся проводить бесфлюсовую плавку для получения более богатых по TiO2 шлаков. Режим плавки включает загрузку шихты, набор электронагрузки до максимума, получение первичного шлака, его доводку, отстой и перегрев, выпуск шлака и чугуна. Количество углерода в шихте рассчитывают так, чтобы получать шлак с содержанием 3-5 % FeO.
Продукты плавки (чугун и шлак) обычно выпускают вместе через одну летку в общую изложницу. Температура шлака на выпуске 1570-1650 °С. После расслаивания и затвердевания чугун и шлак разделяют.
Расход электроэнергии при плавке в закрытых печах равен 1900 кВт • ч/т шлака.
Примерный состав шлаков, %: ТiO2 82-87; FеО 3-6,5; SiO2 2,8-5,6; СаО 0,3-1,2; А12О3 2-6; МgО 2-5,6; МnО 1-1,5; V2О5 0,15; Сг2О3 0,2-1,7. Выплавить шлаки с содержанием FеО ниже 3 % трудно без добавок флюсов вследствие их тугоплавкости, обусловленной присутствием оксикарбида. При достаточном содержании FеО оксикарбид взаимодействует с ним по реакции:
ТiC • ТiO + 3 FеО = Тi2O3 + 3 Fе + СО.
Характерная особенность блока титанового шлака состоит в том, что он рассыпается в процессе охлаждения на воздухе; это объясняется окислением низших оксидов с образованием рутила. Данное явление облегчает переработку блока.
Производство тетрахлорида титана
Физико-химические основы процесса
Диоксид титана реагирует с хлором по эндотермической реакции:
ТiO2 + 2 С12 = ТiС14 + O2; ∆H°1000 к = 192 кДж,
∆G°1000к = 127,5 кДж. (4.2)
Даже при 800-1000 °С эта реакция протекает в незначительной степени вследствие малой величины константы равновесия:
Так как
, а суммарное давление газов
, то
Отсюда
Определенное из этого уравнения равновесное парциальное давление ТіСl4 для реакции (4.2) равно 47,8 Па, что отвечает объемной концентрации 0,05 %. Из этого следует, что реакция протекает в малой степени.
С достаточными для практических целей скоростью и выходом продукта при температурах 700-900 °С хлорирование диоксида титана протекает в присутствии углерода. В этом случае хлорирование TiO2 описывается суммарной реакцией:
ТiO2 + С + 2 С12 = ТiС14 + СО2. (4.3)
Реакция (4.3) - экзотермическая и протекает с большой убылью энергии Гиббса:
∆H°1000 к = - 218 кДж; ∆G°1000к = - 273 кДж
Константа равновесия реакции (3.3) при 1000 К:
Кроме реакции (4.3) для расчета состава равновесной газовой фазы необходимо учитывать реакцию газификации углерода и реакцию образования фосгена:
; (4.4)
(4.5)
Равновесный состав газовой фазы можно определить, решив систему из пяти уравнений. Из них три - (4.3), (4.4) и (4.5) - выражают условия равновесия. Другие два уравнения вытекают из материального баланса и равенства общего давления 0,1 МПа:
;
. (4.6)
В табл. 7 приведены результаты расчета состава равновесной газовой фазы.
Таблица 7. Равновесный состав газовой фазы для реакци хлорирования TiO2 в присутствии углерода
t, °С
Парциальное давление, МПа
CO
CO2
TiCl4
Cl2
COCl2
600
0,017
0,0372
0,0457
4,37·10-11
5,63·10-13
700
0,041
0,0193
0,0397
1,13·10-9
4,98·10-12
800
0,0588
0,0059
0,0353
2,41·10-9
6,37·10-11
900
0,0653
0,0015
0,0336
9,93·10-9
1,06·10-10
Можно видеть, что в интервале 600-900 °С равновесное давление хлора малое, что говорит о практической необратимости реакции хлорирования TIO2 в присутствии углерода. Равновесное давление фосгена на 2-3 порядка ниже давления хлора.
Исследования кинетики хлорирования ТiO2 показали, что роль углерода не сводится лишь к связыванию кислорода в СО2 и СО. Молекулы хлора, сорбируясь на поверхности углеродистого материала (угля, кокса), активизируются - переходят в атомарное состояние. Возможно также образование радикалов (
и др.) и хлороуглеродных нестойких комплексов СхС1У. Участие атомарного хлора, радикалов или хлороуглеродных комплексов в реакциях хлорирования ускоряет их протекание.
Ниже приведена возможная схема процесса с участием атомарного хлора:
I стадия - сорбция молекул хлора на угле или коксе с образованием атомарного хлора
[Cl2]адс
2 [С1]адс
2 С1газ; (4.7)
II стадия - хлорирование ТiO2 атомарным хлором при участии СО
ТiO2 + 4 С1 + 2 СО = ТiС14 + 2 СО2; (4.8)
III стадия - реакция газификации (реакция Будуара):
СО2 + С
2 СО. (4.9)
Приведенная схема объясняет различия в скорости хлорирования ТiО2 смесью хлора с СО при отсутствии и наличии угля. Находит также объяснение наблюдаемое резкое различие в соотношении СО/СО2 в газовой фазе в зависимости от условий хлорирования. Когда скорость хлорирования лимитирует стадия газификации состав газовой фазы будет близким составу для реакции хлорирования, т.е. в газовой фазе будет превалировать СО2. Если же скорость процесса лимитируется стадией хлорирования, в составе газовой фазы при 800-900 °С будет преобладать СО в соответствии с равновесием реакции (см. табл. 7).
При одинаковой температуре и крупности частиц скорость хлорирования шлаков выше, чем рутиловых концентратов. Это объясняется тем, что в составе шлаков содержатся низшие оксиды титана, которые активно реагируют с хлором при 300 – 400 °С даже при отсутствии углерода:
2Ti3O5 + 2Cl2 = TiCl4 +5TiO2,
Δ
k= – 431 кДж; (4.10)
2Ti2O3 + 2Cl2 = TiCl4 + 3TiO2,
Δ
k = – 447 кДж; (4.11)
2TiO + 2Cl2 = TiCl4↓ + TiO2,
Δ
k = – 548 кДж (4.12)
Образующийся по реакциям (4.10) – (4.12) активный диоксид титана интенсивней хлорируется в присутствии угля, чем рутил.
В шлаках в тех или иных количествах содержатся кислородные соединения железа, марганца, магния, кальция, алюминия, кремния, ванадия и других элементов. Летучие хлориды образуют Fe, Al, Si, V, Сr, Та, Nb.
По убывающей способности к взаимодействию с хлором оксиды можно расположить в ряд: К2О > Nа2О > СаО > (МпО, FеО, МgО) > ТiO2 > А12О3 > SiO2. Естественно, что оксиды, расположенные в ряду до ТiO2, в процессе хлорирования при 800-900 °С полностью переходят в хлориды, тогда как А12О3 и SiO2 хлорируются лишь частично (однако силикаты и алюмосиликаты хлорируются активно).
Практика хлорирования
В производственной практике применяют три способа хлорирования титансодержащих материалов: хлорирование брикетированной шихты, хлорирование в солевом расплаве и хлорирование в кипящем слое. Ниже рассмотрены первые два способа, используемые на отечественных предприятиях хлорирования титановых шлаков.
Хлорирование брикетировании шихт. В этом варианте брикеты шихты хлорируют в шахтном хлораторе непрерывного действия. Для приготовления брикетов компоненты шихты (измельченные титановый шлак и нефтяной кокс) смешивают, к смеси добавляют связку (сульфитно-целлюлозный щелок, каменноугольный или нефтяной пек). Смесь прессуют на вальцевых прессах в подушкообразные брикеты размером 50x40x35 мм. С целью повышения прочности и удаления летучих составляющих брикеты прокаливают без доступа воздуха при 850-950 °С в прокалочных печах периодического или непрерывного действия. В шихту вводя примерно 20-25 % кокса (при содержании в шлаке 80-85 % ТiO2).
На рис. 41 приведена схема шахтного хлоратора непрерывного действия. Шахта хлоратора (внутренний диаметр 1,8 высота 10 м) футерована динасовым и плотным шамотным кирпичом. Брикеты подаются из бункера через золотниковый питатель, остаток выгружается шнеком или золотниковым устройством. Фурмы подачи хлора расположены на высоте
2 м от выгрузки. Хлорирование проводят при 950-1000 °С.
ПРОИЗВОДСТВО ХИМИЧЕСКИХ СОЕДИНЕНИЙ ТИТАНА
Титановые минералы, руды и рудные концентраты
В ряду распространенности элементов титан занимает де вятое место, содержание его в земной коре 0,61 % (по массе). Титан встречается во всех изверженных и осадочных породах, а также в почве, торфе, каменном угле, растениях, крови, костях животных.
Титан встречается в земной коре в виде диоксида, титанатов и сложных комплексных титанониобатов и силикатов,
Известно около 70 минералов титана, наибольшее промышленное значение имеют рутил, ильменит, перовскит и сфен, являющиеся собственно титановыми минералами.
Рутил - природный диоксид титана (другие модификации -анатаз и брукит). Обычно содержит примесь оксида железа (II) FеО. Плотность 4,18-4,28 г/см3. Цвет большей частью красно-коричневый. Крупные месторождения редки. Рутиловые концентраты содержат 90-95 % ТiO2.
Ильменит - титанат железа FеО-ТiO2 наиболее распространенный минерал титана. Впервые найден на Урале в Ильменских горах. Минерал бурого или буро-черного цвета. Плотность 4,56-5,21 г/см3. При длительном выветривании ильменит переходит в аризонит (Fe2O3∙3TiO2) и лейкоксен (TiO2∙nH2O). Это объясняет более высокое содержание TiO2 в некоторых ильменитах, чем это соответствует формуле (52,66 %).
Часто ильменит находится в тесной связи с магнетитом. Такие руды называют титаномагнетитами.
Ильменит добывают преимущественно из речных и прибрежно-морских россыпей. Эксплуатируемые россыпи содержат от единиц до нескольких десятков килограммов ильменита на 1 м3 песков. Пески часто бывают комплексным сырьем. Так, пески Самотканского месторождения на Украине содержат рутил, ильменит, циркон, а также минералы алюминия - дистен.

* По структуре титанаты относятся к типу смешанных оксидов.
Al2O3·SiO2 и ставролит Fe(OH)2·2AlSiO5.
Крупные россыпи ильменитовых песков найдены в Индии, Австралии, Индонезии, Африке, Южной Америке, США и России.
Важный источник ильменита - титаномагнетитовые месторождения. Крупнейшие из них известны в Канаде, России, Скандинавии, Бразилии.
Перовскит - титанат кальция СаО • ТiO2 (58,7 % ТiO2). Часто содержит примеси ниобия, иттрия, марганца, магния. Плотность 3,95-4,04 г/см3. Цвет черный, красно-бурый.
Крупные месторождения найдены в СССР на Кольском полуострове. В перспективе может стать важным источником получения титана.
Сфен или титанит — титаносиликат кальция CaO-TiO2-SiO2 (38,8% TiO2). Цвет желтый, плотность 3,4-3,56 г/см3. Месторождения найдены во многих районах СССР, известны в США, Канаде и Мадагаскаре. Может служить титановым сырьем при комплексной добыче с другими рудами (апатитом и нефелином).
При обогащении ильменитовых песков вначале гравитационными методами извлекают тяжелые минералы (магнетит, ильменит, рутил, циркон и др.), получая так называемые черные шлихи. Для разделения шлихов используют электромагнитные и электростатические методы. Если магнитную проницаемость железа принять за 100, то для магнетита она равна 40,2, для ильменита 24,7, для рутила 0,4, для силикатов меньше 0,2. Изменяя напряженность магнитного поля, отделяют магнетит от ильменита, а последний от рутила.
Таблица 6. Примерный состав титановых концентратов, выпускаемых в СССР
Концентрат | Состав концентрата, % (по массе) | ||||||||
TiO2 | FeO | Fe2O3 | SiO2 | Ai2O3 | Cr2O3 | MgO | CaO | V2O5 | |
Уральский | 44,0 | 31,4 | 16,9 | 1,8 | 2,5 | - | 2,8 | 1,3 | - |
Иршинский | 48,7 | 45,9 | - | 3,9 | 0,5 | - | 1,3 | 1,1 | - |
Самотканский (аризонитовый) | 60,3 | - | 25,3 | 1,2 | 2,0 | 1,4 | 0,9 | 0,2 | - |
Рутиловый | 93,2 | 1,8 | - | 2,0 | 1,1 | 0,3 | - | 0,2 | 0,11 |
При обогащении титаномагнетитовых руд с крупной вкрапленностью ильменита также используют магнитную сепарацию. Некоторые титаномагнетиты не поддаются механическому обогащению. В этом случае применяют металлургическое обогащение - плавку в электропечах с получением чугуна и богатого титаном шлака. Из ильменитовых концентратов выплавляют шлаки с содержанием 75-85 % TiO2. Кроме того, из них в результате химического обогащения получают синтетический рутил с содержанием 90-97 % TiO2.
В табл.6 приведен примерный состав титановых концентратов, выпускаемых в СССР.
Продукты переработки титановых концентратов
Из титановых концентратов непосредственно получают три вида продуктов: тетрахлорид титана, диоксид титана и ферротитан.
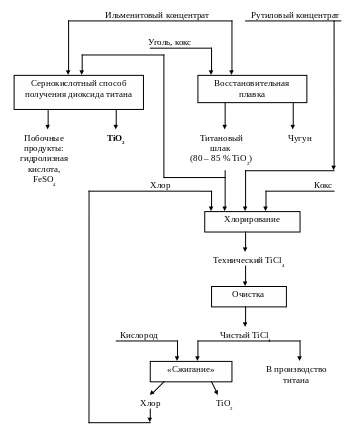
Рисунок 39 Общая схема производства тетрахлормда титана и диоксида титана из кльменитового концентрата.
Тетрахлорид титана - основное исходное соединение для производства металлического титана. Для этой цели получают хлорид высокой чистоты, представляющий собой бесцветную (или слегка окрашенную в желтый цвет) жидкость. Диоксид титана выпускают различной степени чистоты: пигментный, содержащий 94-98,5 % TiO2; повышенной чистоты (не ниже 99,5 % TiO2) для производства твердых сплавов и металлического титана; для приготовления лигатур с никелем, медью, алюминием с содержанием TiO2 не ниже 99 %; для обмазки сварочных электродов с содержанием не ниже 97,5 % TiO2.
Ферротитан выплавляют из ильменитовых концентратов алюминотермическим способом. Сплавы содержат 25-30 % Тi; 5-8 % А1; 3-4 % Si; остальное - железо.
Ниже рассмотрены промышленные способы производства те-трахлорида титана и диоксида титана из основного сырья -ильменитовых концентратов.
На рис. 39 приведена общая схема переработки ильменитового концентрата. Видно, что хлорид титана производят хлорированием титанового шлака или "синтетического рутила", получаемых из концентрата. Диоксид титана производят двумя способами - сернокислотным или "сжиганием" тетрахлорида титана.
Выплавка титанового шлака из ильменита
Высокое содержание железа (40-48 % FеО + Fе2О3) затрудняет получение хлорида титана из ильменита. При прямом хлорировании концентрата на образование хлорида железа затрачивается много хлора, регенерация которого—из хлорного железа затруднительна.
Для отеделения железа проводят восстановительную плавку ильменита с получением чугуна и титанового шлака (80-87 % TiO2). Разделение титана и железа в этом процессе основано на большом различии сродства к кислороду у железа и титана.
Восстановительную плавку ведут в трехфазных электродуговых печах, подобных применяемым в производстве ферросплавов, мощностью 5-20 МВт (рис. 40). Ванна печи футерована магнезитовыми огнеупорами. Для защиты футеровки стен от быстрого разъедания шлаком на них предварительно наращивают гарниссаж — слой застывшего тугоплавкого шлака.
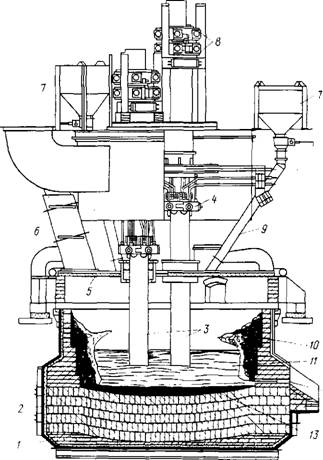
Рисунок 40. Схема электродуговой печи мощностью 5 МВт для выплавки титановых шлаков:
1 - кожух; 2 - футеровка (магнезитовый кирпич); 3 - электроды; 4 - токопод-водящие щеки; 5 - водоохлаждаемый свод; 6 - вентиляционная труба; 7 - бункера с шихтой; 8 - система подвески и перепуска электродов; 9 - труботечки для подачи шихты; 10 - гарниссаж; 11 - шлак; 12 - летка; 13 – чугун
Для защиты подины от разъедания на ней постоянно поддерживают высокий слой чугуна (
t, °С | Парциальное давление, МПа | ||||
CO | CO2 | TiCl4 | Cl2 | COCl2 | |
600 | 0,017 | 0,0372 | 0,0457 | 4,37·10-11 | 5,63·10-13 |
700 | 0,041 | 0,0193 | 0,0397 | 1,13·10-9 | 4,98·10-12 |
800 | 0,0588 | 0,0059 | 0,0353 | 2,41·10-9 | 6,37·10-11 |
900 | 0,0653 | 0,0015 | 0,0336 | 9,93·10-9 | 1,06·10-10 |
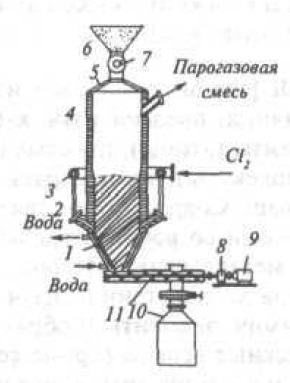
