Файл: Отчет по учебной практике уп. 04 Учебная практика пм. 04 Выполнение работ по профессии слесарьремонтник.docx
Добавлен: 18.03.2024
Просмотров: 96
Скачиваний: 6
ВНИМАНИЕ! Если данный файл нарушает Ваши авторские права, то обязательно сообщите нам.
точно соответствовать очертаниям детали; – отверстия под кондукторные втулки должны быть строго перпендикулярны плоскости, в которой они расточены; – упоры, определяющие положение детали в приспособлении, должны находиться в одной плоскости или на одной горизонтальной линии; – винтовые, клиновые, рычажные и эксцентриковые зажимы должны плотно удерживать обрабатываемую деталь в рабочем положении.
Все поступающие на сборку детали должны быть очищены и промыты в керосине или в бензине. Необработанные поверхности литых и кованых деталей очищаются, грунтуются и окрашиваются масляной краской.
Слесарно-пригоночные работы связаны с опиливанием фасонных поверхностей, образованием на них необходимых канавок и удалением излишков металла в местах, не поддающихся станочной обработке. Базовые и направляющие поверхности слесарь-инструментальщик обрабатывает шабрением. На небольших поверхностях при этом снимается слой металла толщиной до 0,05 мм, а на больших — до 0,1 мм.
Детали, требующие герметичных соединений и подвижных беззазорных посадок, притирают или доводят. На притирку плоских поверхностей оставляют припуск 0,03…0,05 мм, а на доводку отверстий — 0,01…0,02 мм. Закаленные детали приспособлений — копиры, установы, опоры и др. — шлифуют, используя ручные механизированные инструменты, притупляют на них острые углы, делая закругления радиусом 0,5… 1 мм или снимая фаски шириной 0,5… 1 мм под углом 45°.
Сборку универсальных и специальных приспособлений начинают с установки базовой детали (чаще корпуса) и подгонки в ней поверхностей, которые соединяются с поверхностями других деталей.
Способ установки базовых деталей приспособления относительно контрольно-сборочной плиты зависит от формы установочной поверхности и размеров детали. Базовая деталь в виде корпуса устанавливается на плиту основанием. Такая установка дает возможность обрабатывать поверхности, параллельные основанию корпуса. В тех случаях, когда поверхность базовой детали перпендикулярна контрольно-сборочной плите, ее устанавливают на домкратиках или клиньях, размещенных в трех точках. Базовую деталь выверяют по контрольному цилиндру или угольнику. Если у детали установочные поверхности имеют форму тел вращения (с хвостовиком), то их закрепляют в кантующуюся V-образную призму. Базовые детали с центровыми отверстиями устанавливают в центровых бабках. При закреплении базовой детали рекомендуется применять магнитные угольники, призмы, синусные устройства и универсальные поворотные столы координатно-расточных станков.
Сборку приспособлений целесообразно разделять на узловую и общую, что значительно сокращает длительность их изготовления.
Рис. 1. Контрольная плита и кантующийся кубик.
Места расположения контрольных штифтов выбирают так, чтобы отверстия для них были сквозные, а не глухие, иначе при разборке приспособлений выбить штифт будет трудно. Если сквозное отверстие получить невозможно, то ставят конические штифты.
Для неподвижных соединений деталей и узлов, работающих на сжатие и сдвиг, вместо механического крепления целесообразно применять склеивание.
С целью повышения точности часто осуществляют совместную обработку нескольких деталей после их сборки. Например, для получения строгой соосности отверстий в нескольких деталях их обработка ведется с одной установки; для лучшего выравнивания установочных поверхностей опор их часто шлифуют совместно после окончательной установки на корпусе приспособления.
Установка кондукторных втулок. Как отмечалось выше, кондукторные втулки поступают на сборку в готовом виде после механической и термической обработки.
Внутренний и наружный диаметры отверстий кондукторных втулок должны быть строго концентричны. Для обеспечения надежной посадки наружный диаметр втулок делается на 0,01—0,012 мм больше диаметра отверстий в плите. Для лучшей запрессовки наружные поверхности втулок покрывают купоросом или смазывают машинным маслом. Легкими ударами молотка втулки слегка заколачивают в отверстия, а затем винтовым или рычажщим прессом полностью запрессовывают в плиту.
Перпендикулярность стенок отверстий запрессованных втулок относительно плоскости плиты проверяется с помощью калибра, вставляемого в отверстие втулки, и лекального угольника. Расстояние между центрами отверстий контролируется круглыми калибрами и концевыми мерами, при этом неправильно установленные втулки выпрессовывают и устанавливают в приспособлении.
Контроль после сборки. После сборки контролируют точность приспособлений тремя способами: непосредственным измерением тех размеров, от которых зависит точность их работы; пробной обработкой нескольких заготовок с последующим контролем их точности универсальными измерительными средствами; изготовлением эталонов.
Первый способ контроля трудоемок и может выполняться высококвалифицированными контролерами. Например, расстояние между осями кондукторных втулок проверяют с помощью калибров или плиток-клиньев. Эти размеры определяют с помощью микрометра, штангенциркуля или микрометрического штихмаса.
Можно использовать координатный метод измерения на инструментальном или универсальном микроскопе с окулярной головкой двойного изображения.
Рис. 2. Контроль расстояния между осями втулок.
Примеры проверки радиального биения деталей приспособлений с помощью индикаторов приведены на рис. 3. Биение наружных поверхностей относительно оси центров проверяют в центрах, а наружных поверхностей втулки относительно внутренней — на оправке в центрах или на консольно закрепленной оправке. Биение поверхностей А и В вала относительно поверхности Б определяют на призме, внутренней поверхности выточки валика относительно наружной его поверхности — на роликах, а взаимное биение двух отверстий втулки — на оправке.
Рис. 3. Примеры проверки радиального биения деталей.
Углы между плоскостями и осями отверстий проверяют с помощью нормальных или специальных угольников. Нормальным угольником (90°) можно также измерить угол между плоскостью и осью двух соосных отверстий одинакового диаметра. Для этого на поверочную плиту ставят домкраты, а на них— проверяемую деталь, С помощью микронного индикатора, закрепленного на стойке, плоскость устанавливают параллельно плоскости поверочной плиты. Затем в отверстие вставляют специальный контрольный валик и угольником проверяют угол.
Схема контроля перпендикулярности осей двух отверстий представлена на рис. 4. Изменение показаний индикатора при повороте валика на 180° соответствует отклонению от перпендикулярности осей отверстия на длине.
Рис. 4. Контроль углов между плоскостями, а осями отверстий.
Проверка параллельности плоскостей направляющих, а также оси отверстия и этих плоскостей осуществляется индикатором на стойке или индикаторным нутромером. Порядок проверки следующий. На поверочную плиту ставят домкраты, а на них — проверяемую деталь и затем выравнивают плоскость параллельно плоскости поверочной плиты. С помощью индикатора проверяют параллельность плоскости поверочной плиты и
параллельность оси контрольного валика, вставленного в отверстие, плоскостям. В отдельных случаях можно применять контрольные валики совместно со втулками.
Приспособления должны подвергаться периодическим осмотрам и проверкам работниками ОТК, в условиях серийного производства приспособления периодически снимают со станков и сдают на склад для хранения. Это время должно использоваться для их осмотра и проверки на точность, В массовом производстве приспособления проверяют на станке. В этом случае наиболее удобен способ контроля по эталонам. На крупных машиностроительных предприятиях периодическая проверка приспособлений осуществляется группой работников ОТК, и результаты ее фиксируются в картотеке. По данным проверки выявляют необходимость в профилактическом и текущем ремонтах приспособлений.
Пример сборки фрезерного приспособления. В качестве конкретного примера рассмотрим сборку приспособления для фрезерования двух плоскостей детали.
Рис. 4. Сборка фрезерного приспособления.
Обрабатываемую деталь устанавливают наклонно в приспособлении и закрепляют прихватами. Для установки приспособления на столе станка без выверки служат две направляющие шпонки, которые закрепляются в пазе на опорной плоскости корпуса. Выступающая часть шпонки заходит в Т-образный паз стола станка. Ширина паза под шпонку в корпусе приспособления выполняется обычно с допуском HI.
Для настройки на размер фрезы устанавливают на эталонной детали, которую закрепляют в приспособлении. Затем стол станка подводят к фрезам так, чтобы они коснулись обрабатываемых поверхностей, и закрепляют в этом положении.
Слесарь-инструментальщик получает на сборку окончательно обработанные корпус приспособления, шпонки с винтами, детали прихвата (шпильку, гайку, шайбу и пружину, планку прихвата) и упорный штифт, а также эталонную деталь, проверенную и маркированную ОТК.
Сборка приспособления начинается с зачистки шпоночного паза и пригонки к нему шпонок. Затем на-шпонках размечают отверстия для винтов и сверлят их одновременно в шпонках и в корпусе, после чего нарезают резьбу в отверстиях корпуса и рассверливают сквозные отверстия в шпонках.
После этого в приспособлении устанавливают эталонную деталь и ставят на место планку прихвата, чтобы убедиться в ее горизонтальном положении. Если планка перекошена, слесарь-инструментальщик опиливает ее правый или левый конец, чтобы она заняла горизонтальное положение. Затем в корпусе размечают отверстие для шпильки, сверлят и нарезают его, ввертывают наглухо шпильку, ставят на место все детали прихвата и шпонки. На этом заканчивается предварительная сборка приспособления.
Следующий этап сборки — проверка приспособления на точность — производится на контрольной плите с точными, строго параллельными пазами. Эталонную деталь закрепляют в приспособлении, которое ставят на плиту и прижимают шпонками к стенке ее паза. Рядом с приспособлением ставят индикаторную стойку с двумя индикаторами (можно поставить один индикатор и придавать ему последовательно I и II положения). Передвигая вдоль паза прижатую к нему уступом стойку с индикаторами, проверяют параллельность паза шпонкам. Обнаруженные ошибки устраняют повторным шлифованием гнезда.
После этого проверяют прилегание эталонной детали к стенкам гнезда: при укладке (без прижима прихватом) она не должна качаться в гнезде. Если это даст положительный результат, то ставят на место упорный штифт, отверстие под который было просверлено и развернуто ранее.
Готовое приспособление сдают на контроль, который заключается в обработке нескольких заготовок на станке. Если результаты работы приспособления удовлетворительные, его окрашивают, клеймят и сдают в кладовую.
Более сложные задачи приходится решать при сборке кондукторов, особенно таких, у которых отверстия расположены в нескольких плоскостях. Здесь очень большое значение имеет составление плана пригоночных и сборочных работ, а также проверка приспособления на всех этапах сборки. Особенно важна проверка в тех случаях, когда нужная точность обработки не может быть обеспечена на станках и получается в процессе сборки.
Все поступающие на сборку детали должны быть очищены и промыты в керосине или в бензине. Необработанные поверхности литых и кованых деталей очищаются, грунтуются и окрашиваются масляной краской.
Слесарно-пригоночные работы связаны с опиливанием фасонных поверхностей, образованием на них необходимых канавок и удалением излишков металла в местах, не поддающихся станочной обработке. Базовые и направляющие поверхности слесарь-инструментальщик обрабатывает шабрением. На небольших поверхностях при этом снимается слой металла толщиной до 0,05 мм, а на больших — до 0,1 мм.
Детали, требующие герметичных соединений и подвижных беззазорных посадок, притирают или доводят. На притирку плоских поверхностей оставляют припуск 0,03…0,05 мм, а на доводку отверстий — 0,01…0,02 мм. Закаленные детали приспособлений — копиры, установы, опоры и др. — шлифуют, используя ручные механизированные инструменты, притупляют на них острые углы, делая закругления радиусом 0,5… 1 мм или снимая фаски шириной 0,5… 1 мм под углом 45°.
Сборку универсальных и специальных приспособлений начинают с установки базовой детали (чаще корпуса) и подгонки в ней поверхностей, которые соединяются с поверхностями других деталей.
Способ установки базовых деталей приспособления относительно контрольно-сборочной плиты зависит от формы установочной поверхности и размеров детали. Базовая деталь в виде корпуса устанавливается на плиту основанием. Такая установка дает возможность обрабатывать поверхности, параллельные основанию корпуса. В тех случаях, когда поверхность базовой детали перпендикулярна контрольно-сборочной плите, ее устанавливают на домкратиках или клиньях, размещенных в трех точках. Базовую деталь выверяют по контрольному цилиндру или угольнику. Если у детали установочные поверхности имеют форму тел вращения (с хвостовиком), то их закрепляют в кантующуюся V-образную призму. Базовые детали с центровыми отверстиями устанавливают в центровых бабках. При закреплении базовой детали рекомендуется применять магнитные угольники, призмы, синусные устройства и универсальные поворотные столы координатно-расточных станков.
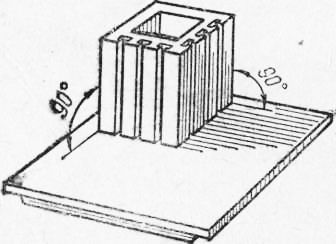
Рис. 1. Контрольная плита и кантующийся кубик.
Места расположения контрольных штифтов выбирают так, чтобы отверстия для них были сквозные, а не глухие, иначе при разборке приспособлений выбить штифт будет трудно. Если сквозное отверстие получить невозможно, то ставят конические штифты.
Для неподвижных соединений деталей и узлов, работающих на сжатие и сдвиг, вместо механического крепления целесообразно применять склеивание.
С целью повышения точности часто осуществляют совместную обработку нескольких деталей после их сборки. Например, для получения строгой соосности отверстий в нескольких деталях их обработка ведется с одной установки; для лучшего выравнивания установочных поверхностей опор их часто шлифуют совместно после окончательной установки на корпусе приспособления.
Установка кондукторных втулок. Как отмечалось выше, кондукторные втулки поступают на сборку в готовом виде после механической и термической обработки.
Внутренний и наружный диаметры отверстий кондукторных втулок должны быть строго концентричны. Для обеспечения надежной посадки наружный диаметр втулок делается на 0,01—0,012 мм больше диаметра отверстий в плите. Для лучшей запрессовки наружные поверхности втулок покрывают купоросом или смазывают машинным маслом. Легкими ударами молотка втулки слегка заколачивают в отверстия, а затем винтовым или рычажщим прессом полностью запрессовывают в плиту.
Перпендикулярность стенок отверстий запрессованных втулок относительно плоскости плиты проверяется с помощью калибра, вставляемого в отверстие втулки, и лекального угольника. Расстояние между центрами отверстий контролируется круглыми калибрами и концевыми мерами, при этом неправильно установленные втулки выпрессовывают и устанавливают в приспособлении.
Контроль после сборки. После сборки контролируют точность приспособлений тремя способами: непосредственным измерением тех размеров, от которых зависит точность их работы; пробной обработкой нескольких заготовок с последующим контролем их точности универсальными измерительными средствами; изготовлением эталонов.
Первый способ контроля трудоемок и может выполняться высококвалифицированными контролерами. Например, расстояние между осями кондукторных втулок проверяют с помощью калибров или плиток-клиньев. Эти размеры определяют с помощью микрометра, штангенциркуля или микрометрического штихмаса.
Можно использовать координатный метод измерения на инструментальном или универсальном микроскопе с окулярной головкой двойного изображения.
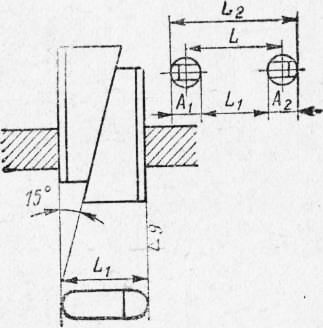
Рис. 2. Контроль расстояния между осями втулок.
Примеры проверки радиального биения деталей приспособлений с помощью индикаторов приведены на рис. 3. Биение наружных поверхностей относительно оси центров проверяют в центрах, а наружных поверхностей втулки относительно внутренней — на оправке в центрах или на консольно закрепленной оправке. Биение поверхностей А и В вала относительно поверхности Б определяют на призме, внутренней поверхности выточки валика относительно наружной его поверхности — на роликах, а взаимное биение двух отверстий втулки — на оправке.
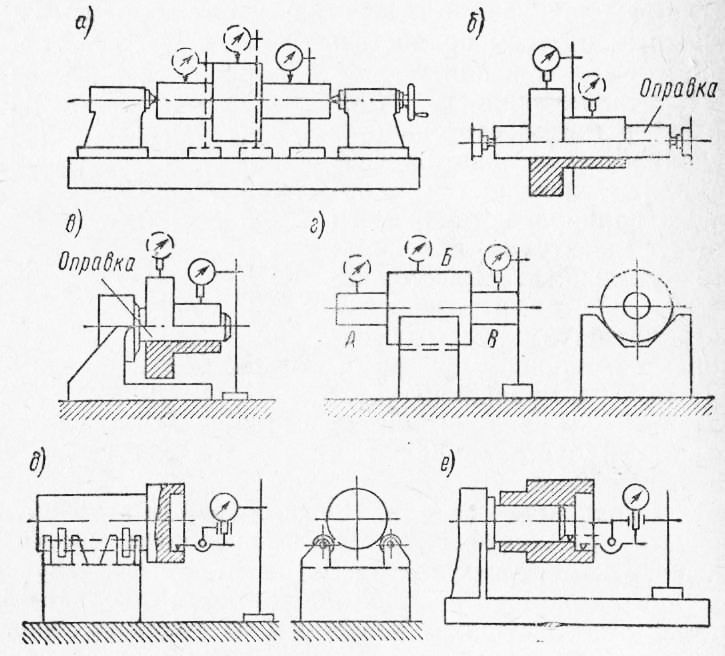
Рис. 3. Примеры проверки радиального биения деталей.
Углы между плоскостями и осями отверстий проверяют с помощью нормальных или специальных угольников. Нормальным угольником (90°) можно также измерить угол между плоскостью и осью двух соосных отверстий одинакового диаметра. Для этого на поверочную плиту ставят домкраты, а на них— проверяемую деталь, С помощью микронного индикатора, закрепленного на стойке, плоскость устанавливают параллельно плоскости поверочной плиты. Затем в отверстие вставляют специальный контрольный валик и угольником проверяют угол.
Схема контроля перпендикулярности осей двух отверстий представлена на рис. 4. Изменение показаний индикатора при повороте валика на 180° соответствует отклонению от перпендикулярности осей отверстия на длине.
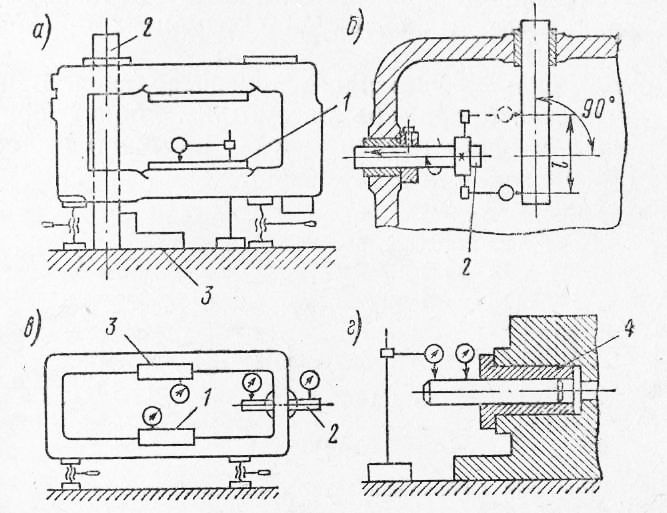
Рис. 4. Контроль углов между плоскостями, а осями отверстий.
Проверка параллельности плоскостей направляющих, а также оси отверстия и этих плоскостей осуществляется индикатором на стойке или индикаторным нутромером. Порядок проверки следующий. На поверочную плиту ставят домкраты, а на них — проверяемую деталь и затем выравнивают плоскость параллельно плоскости поверочной плиты. С помощью индикатора проверяют параллельность плоскости поверочной плиты и
параллельность оси контрольного валика, вставленного в отверстие, плоскостям. В отдельных случаях можно применять контрольные валики совместно со втулками.
Приспособления должны подвергаться периодическим осмотрам и проверкам работниками ОТК, в условиях серийного производства приспособления периодически снимают со станков и сдают на склад для хранения. Это время должно использоваться для их осмотра и проверки на точность, В массовом производстве приспособления проверяют на станке. В этом случае наиболее удобен способ контроля по эталонам. На крупных машиностроительных предприятиях периодическая проверка приспособлений осуществляется группой работников ОТК, и результаты ее фиксируются в картотеке. По данным проверки выявляют необходимость в профилактическом и текущем ремонтах приспособлений.
Пример сборки фрезерного приспособления. В качестве конкретного примера рассмотрим сборку приспособления для фрезерования двух плоскостей детали.
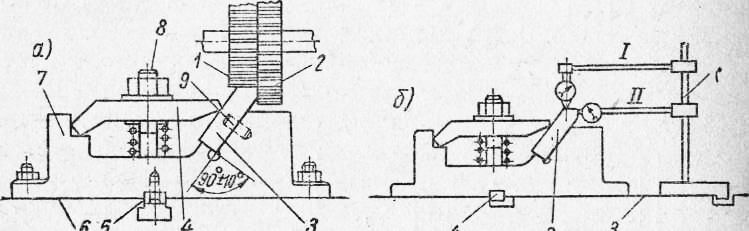
Рис. 4. Сборка фрезерного приспособления.
Обрабатываемую деталь устанавливают наклонно в приспособлении и закрепляют прихватами. Для установки приспособления на столе станка без выверки служат две направляющие шпонки, которые закрепляются в пазе на опорной плоскости корпуса. Выступающая часть шпонки заходит в Т-образный паз стола станка. Ширина паза под шпонку в корпусе приспособления выполняется обычно с допуском HI.
Для настройки на размер фрезы устанавливают на эталонной детали, которую закрепляют в приспособлении. Затем стол станка подводят к фрезам так, чтобы они коснулись обрабатываемых поверхностей, и закрепляют в этом положении.
Слесарь-инструментальщик получает на сборку окончательно обработанные корпус приспособления, шпонки с винтами, детали прихвата (шпильку, гайку, шайбу и пружину, планку прихвата) и упорный штифт, а также эталонную деталь, проверенную и маркированную ОТК.
Сборка приспособления начинается с зачистки шпоночного паза и пригонки к нему шпонок. Затем на-шпонках размечают отверстия для винтов и сверлят их одновременно в шпонках и в корпусе, после чего нарезают резьбу в отверстиях корпуса и рассверливают сквозные отверстия в шпонках.
После этого в приспособлении устанавливают эталонную деталь и ставят на место планку прихвата, чтобы убедиться в ее горизонтальном положении. Если планка перекошена, слесарь-инструментальщик опиливает ее правый или левый конец, чтобы она заняла горизонтальное положение. Затем в корпусе размечают отверстие для шпильки, сверлят и нарезают его, ввертывают наглухо шпильку, ставят на место все детали прихвата и шпонки. На этом заканчивается предварительная сборка приспособления.
Следующий этап сборки — проверка приспособления на точность — производится на контрольной плите с точными, строго параллельными пазами. Эталонную деталь закрепляют в приспособлении, которое ставят на плиту и прижимают шпонками к стенке ее паза. Рядом с приспособлением ставят индикаторную стойку с двумя индикаторами (можно поставить один индикатор и придавать ему последовательно I и II положения). Передвигая вдоль паза прижатую к нему уступом стойку с индикаторами, проверяют параллельность паза шпонкам. Обнаруженные ошибки устраняют повторным шлифованием гнезда.
После этого проверяют прилегание эталонной детали к стенкам гнезда: при укладке (без прижима прихватом) она не должна качаться в гнезде. Если это даст положительный результат, то ставят на место упорный штифт, отверстие под который было просверлено и развернуто ранее.
Готовое приспособление сдают на контроль, который заключается в обработке нескольких заготовок на станке. Если результаты работы приспособления удовлетворительные, его окрашивают, клеймят и сдают в кладовую.
Более сложные задачи приходится решать при сборке кондукторов, особенно таких, у которых отверстия расположены в нескольких плоскостях. Здесь очень большое значение имеет составление плана пригоночных и сборочных работ, а также проверка приспособления на всех этапах сборки. Особенно важна проверка в тех случаях, когда нужная точность обработки не может быть обеспечена на станках и получается в процессе сборки.