Файл: Отчет по производственной практике (технологическая).docx
Добавлен: 18.03.2024
Просмотров: 59
Скачиваний: 0
ВНИМАНИЕ! Если данный файл нарушает Ваши авторские права, то обязательно сообщите нам.
Дренирование вести, ориентируясь на температуру газов по Т6.110, отходящий из емкостей Е-601 в факельный коллектор, регулируя расходы сбрасываемых сред, не допуская понижения темпераруты ниже минус 30 ˚С. По окончанию сброса давления из оборудования блока, продувочные вентили закрыть. При ведении процесса, количество и степень открытия продувочных вентилей соотносить со скоростью сброса давления из системы не более 0,1 МПа в минуту. Окончание сброса давления контролировать по показаниям датчика давления на соответствующих участках: P4.226. P4.227, P4.229, P4.234, P4.237, P4.238, P4.241/1‚2, Р4.243/1‚2.
Отогрев и сушка колонны К-401.
Полный отогрев холодных аппаратов и трубопроводов производится только при подготовке к ремонту, в период полной остановки установки, согласно этапам, описанным в инструкции по эксплуатации блока предварительного охлаждения (БПО). Из оборудования БP, отогреву подвергается колонна К-401, в которую на орошение приходит жидкостный поток с температурой минус 100°C.
При производстве операций по обслуживанию колонны в момент разогрева, необходимо соблюдать особую осторожность, обслуживающему персоналу на установке находиться в касках‚ так как возможно падение ледяных глыб в моменты оттаивания «снежной шубы» и льда с крышек люков, фланцевых соединений. запорной арматуры, трубопроводов. Опасные участки предполагаемого падения льда. оградить предупреждающими надписями.
Отогрев производится осушенным исходным газом. отобранным на выходе из фильтров блока осушки и очистки. Отогрев аппаратуры можно считать законченным при достижении температуры газа на выходе из колонны 15-20°С и содержании влаги в отработанном греющем газе, выходящем по пути отбензиненного газа, не выше. чем точка росы исходного газа, т.е. минус 60°С при атмосферном давлении. Контроль качества, отработанного отогревного газа. ведётся по результатам анализов газа, отобранного в точке Q1.602 из линии сухого отбензиненного газа в магистраль потребителю. К отогреву колонны можно приступать только после выдержки в течение 6-8 часов от момента ее остановки.
Скорость поднятия температуры для разогрева не должна превышать
50°C за 1 час. Отогрев проводить не менее 3-х часов, начиная со времени достижения в верхней части сепаратора С-302 положительной температуры отогревного потока.
Дренирование следует производит через 30-40 минут после начала
отогрева далее в течение всего времени отогрева. Во всех случаях дренирование накопившейся воды производится через дренажные устройства в низких точках колонны и трубопроводов. При необходимости проведения дренирования в атмосферу, данные операции производить только в присутствии ответственного. По окончании дренирования продувочные вентили закрыть. В случае обнаружения остаточного давления, сбросить его кратковременным открытием ближайшего продувочного вентиля из соответствующей системы.
Перед началом отогрева‚ по показаниям КИП, необходимо убедиться в
отсутствии рабочей среды в колонне и закрытии арматуры, отсекающей узел
колонны от другого оборудования установки.
Произвести приём газа из БПО в колонну К-401, для чего открыть следующую арматуру: вентили В414, 3403, клапаны В70‚ B42 - по пути следования отогревного газа через отогреваемые аппараты. Контроль скорости подъёма давления в колонне не более 0,1 МПа в минуту вести по соответствующим датчикам давления до достижения давления 1.7 МПа
Отрегулировать поступающий поток отогревного газа в колонну, открытием ручной арматуры на байпасе регулирующих клапанов, или перейти на автоматическую работу клапана PY4.251.
Скорость повышения температуры не должна быть более 10 ˚С в час.
По окончании отогрева колонны и трубопроводов обвязки необходимо
закрыть используемую арматуру и сбросить давление из отогреваемого узла,
через продувочную арматуру.
Система ПАЗ (противоаварийная защита).
Для снижения энергетического потенциала установки и, следовательно, обеспечения минимального уровня взрывоопасности установка разделена быстродействующей отсечной арматурой (скорость срабатывания не более 12
секунд) системы ПАЗ (противоаварийной защиты). Это сводит к минимуму возможность натекания взрывоопасных смесей к разгерметизированному участку Разделение на блоки системы ПАЗ определено давлением рабочих сред.
При срабатывании системы ПАЗ производится отсечение БР с целью
изолирования его энергетического потенциала. в также производится эвакуация основных объёмов жидкости из ёмкостного оборудования. При этом в блоке происходит:
- остановка насоса Н-401/1,2;
- остановка насоса Н-403/1‚2;
- закрытие клапана B42 и отсечение колонны K-401 от остального оборудования по линии отбензиненного газа;
- закрытие клапанов В31 и B32 и прекращение подачи питания в колонну К-401;
- закрытие клапана B70 и прекращение подачи орошения в колонну K-
401;
- открытие клапанов В43/1 и В4З/2 до снижения уровня L4.501 B кубе
колонны К-401 и кипятильнике T-401 до минимально допустимого значения;
- закрытие клапанов B71, B45, B48 и В47 и отсечение колонны К-402 от
оборудования блока по входу питания и выходу готовой продукции;
- открытие клапанов B44 и B46 до снижения уровня L4.502 в кубе колонны К-402 и кипятильнике Т-402 до минимально допустимого значения;
- открытие клапана B73 до снижения значения уровня по L4.503 в Е—401 до минимально допустимого значения;
- открытие клапана B72 до снижения значения уровня по L4.504 в Е-403 до минимально допустимого значения.
При срабатывании системы ПАЗ помимо рассечения установки на блоки производится эвакуация жидких продуктов - углеводородов C3 — C6 из обрудования узлов колонн K-401 и К-402‚ в подземную емкость Е-602. Остатки жидкости из оборудования блока сбрасывается на факел через дренажную ёмкость Е-601, соответствующим открытием дренажных задвижек.
Дальнейшие действия производится согласно контрактной обстановке и причине аварийной остановки.
5
19
. Основные требования к определению сроков замены и ремонта оборудования установки
На установке капитальные ремонты проводятся для всей установки в целом. «Положение о системе технического обслуживания и ремонта технологического оборудования и аппаратов объектов сбора, транспорта и переработки нефтяного газа». Основанием для остановки на ремонт является приказ по ПАО «Сургутнефтегаз» и Управлению.
Подготовку к капитальному ремонту оборудования проводят по следующим этапам:
- остановка оборудования;
- отогрев;
- вытеснение из оборудования и трубопроводов нефтяного газа азотом;
- установка заглушек согласно схеме, утверждаемой техническим руководителем предприятия при подготовке к каждому ремонту.
При проведении подготовительных операций к ремонту следует соблюдать инструкцию по охране труда ИОТВ-35 «По охране труда при остановке, подготовке к ремонту и пуску после ремонта УПГ-3».
При подготовке к ремонту и во время проведения ремонтных работ должны соблюдаться следующие правила безопасности:
- во время работы рабочие должны пользоваться установленной для данной профессии и выполняемой работы спецодеждой, спецобувью, касками и другими средствами индивидуальной защиты. Работать без средств индивидуальной защиты запрещается;
- во время работы руководствоваться инструкциями согласно плана-программы инструктажей;
- каждый работающий, приступив к работе, обязан строго соблюдать сам и требовать от своих подчиненных выполнения действующих правил, норм и инструкций по безопасным приемам работы;
- места, где жизни и здоровью работающего персонала может грозить опасность (неисправности, места возможного падения наледей с оборудования и трубопроводов, места сброса продувочного газа в атмосферу и др.) должны быть ограждены, вывешены таблички, предупреждающие об опасности, при необходимости выставляются наблюдатели из числа персонала установки;
- нахождение посторонних лиц на территории установки, где происходит подготовка к ремонту или ремонт, непосредственно не связанных с выполняемыми работами, запрещается;
- в период подготовки к ремонту и во время проведения ремонтных работ во взрывоопасных помещениях должна работать приточно-вытяжная вентиляция;
- ремонтируемое оборудование, эксплуатируемое при высоких температурах, должно быть охлаждено до температуры +30°С, а при отрицательных температурах отогрето до температуры окружающей среды;
- не допускается розлив взрывопожароопасных жидкостей на территории ремонтируемой установки;
При вытеснении газа из аппаратов и трубопроводов в атмосферу организовать контроль загазованности территории. Особое внимание обратить на направление ветра, на оборудование, где имеется открытый огонь (печи установок УКПГ-1,2) и на помещения, где установлено не взрывозащищенное оборудование (ЦПУ, ЗРУ). При обнаружении загазованности вблизи указанных объектов или при угрозе загазованности в связи с изменением направления ветра, вытеснение газа немедленно прекратить, сообщить о случившемся инженеру I категории ЦПГ-2, руководству цеха. По результатам продувки произвести отбор анализов на содержание углеводородов по блокам с составлением справки на основании плана проведения подготовительных и ремонтных работ на технологическом оборудовании установки. При отсутствии взрывной концентрации установить заглушки, согласно утвержденной схеме.
Вывод технологической установки из ремонта состоит из следующих этапов:
- подписание приказа по управлению;
- подписание акта приёмки в эксплуатацию;
- снятие заглушек, установленных на период ремонта установки;
- вытеснение азотом воздуха из оборудования и трубопроводов;
- опрессовка оборудования и трубопроводов азотом;
- прием объекта комиссией ПАО «Сургутнефтегаз»;
- прием сырьевого газа на установку.
По окончании выполнения ремонтных работ необходимо привести в порядок территорию установки: вывезти мусор, использованные молекулярные сита, убрать посторонние материалы и предметы, не задействованное в рабочем процессе оборудование, спецтехнику.
С территории установки удалить работников сторонних организаций и вспомогательных цехов, принимавших участие в проведении ремонтных работ.
Проверить фланцевые соединения технологических трубопроводов, аппаратов, оборудования, состояние запорно-регулирующей арматуры. Демонтировать заглушки, установленные на время ремонтных работ, согласно утвержденной схеме.
Произвести вытеснение воздуха из аппаратов и трубопроводов установки. Вытеснение воздуха производится инертным газом – азотом. Если факельная система заполнена углеводородным газом, продувка производится со сбросом вытесняемой среды на свечу (в атмосферу). Последующее вытеснение инертного газа углеводородным газом также производится на свечу. Продувка производится вытеснением основного количества воздуха при давлении азота 0,035 МПа. Схемы и последовательность продувки азотом представлены в разделе 6.1. данного регламента и в инструкции по охране труда ИОТВ-35 «По охране труда при остановке, подготовке к ремонту и пуску после ремонта УПГ-3».
Вытеснение воздуха из оборудования и трубопроводов производится последовательно по потокам, в конце каждого потока отбирается анализ на содержание кислорода в вытесняемой среде. Содержание кислорода должно быть не более 1% об. При большем содержании кислорода проводится повторная продувка и повторное определение содержания кислорода.
После вытеснения основного количества воздуха из оборудования и трубопроводов производится опрессовка азотом давлением 0,4 МПа. При выявлении неплотностей, утечек производится их устранение с отглушением участка, на котором обнаружены утечки, и повторнаяопрессовка данного участка. Составляется акт о продувке системы. Пуск установки производится согласно инструкции по охране труда ИОТВ-35 «По охране труда при остановке, подготовке к ремонту и пуску после ремонта УПГ-3».
Заключение
В результате прохождения производственной практики была изучена установка переработки газа №3 входящей в состав структурного подразделения Управление по переработке газа ПАО «Сургутнефтегаз». УПГ-3 производительностью 4,28 млрд. м3 в предназначена для для переработки поступающего попутного нефтяного газа с извлечением из него широкой фракции легких углеводородов, получения сухого отбензиненного газа, пропана технического, пропан-бутана технического и бензина газового стабильного.
После прохождения практики были также получены практические навыки управления производственным процессом, в области эксплуатации и ремонта технологического оборудования.
Список использованных источников
1. Бойко Е. В., Химия нефти и топлив / Е.В. Бойко. – Ульяновск: УлГТУ, 2007. – 60 с. – Текст: непосредственный.
2. Ахметов С. А., Технология и оборудование процессов переработки нефти и газа / С.А. Ахметов. – Санкт-Петербург: Недра, 2006. – 868 с. – Текст: непосредственный.
3. Скобло А. И., Процессы и аппараты нефтегазопереработки и нефтехимии / А.И. Скобло. – Москва: Недра, 2000. – 677 с. – Текст: непосредственный.
4. Лутошкин Г. С., Сбор и подготовка нефти, газа и воды / Г.С. Лутошкин. – Москва: Недра, 1974, –184 с. – Текст : непосредственный.
5. Мановян А. К., Технология первичной переработки нефти и природного газа / А.К. Мановян. – Москва : Химия, 2001. – 586 с. – Текст: непосредственный
6. Сыркин А. М., Основы химии нефти и газа / А.М. Сыркин, Э.М. Мовсумзаде. – Уфа: УГНТУ, 2002. – 109 с. – Текст: непосредственный
Приложение А
Принципиальная технологическая схема УПГ-3
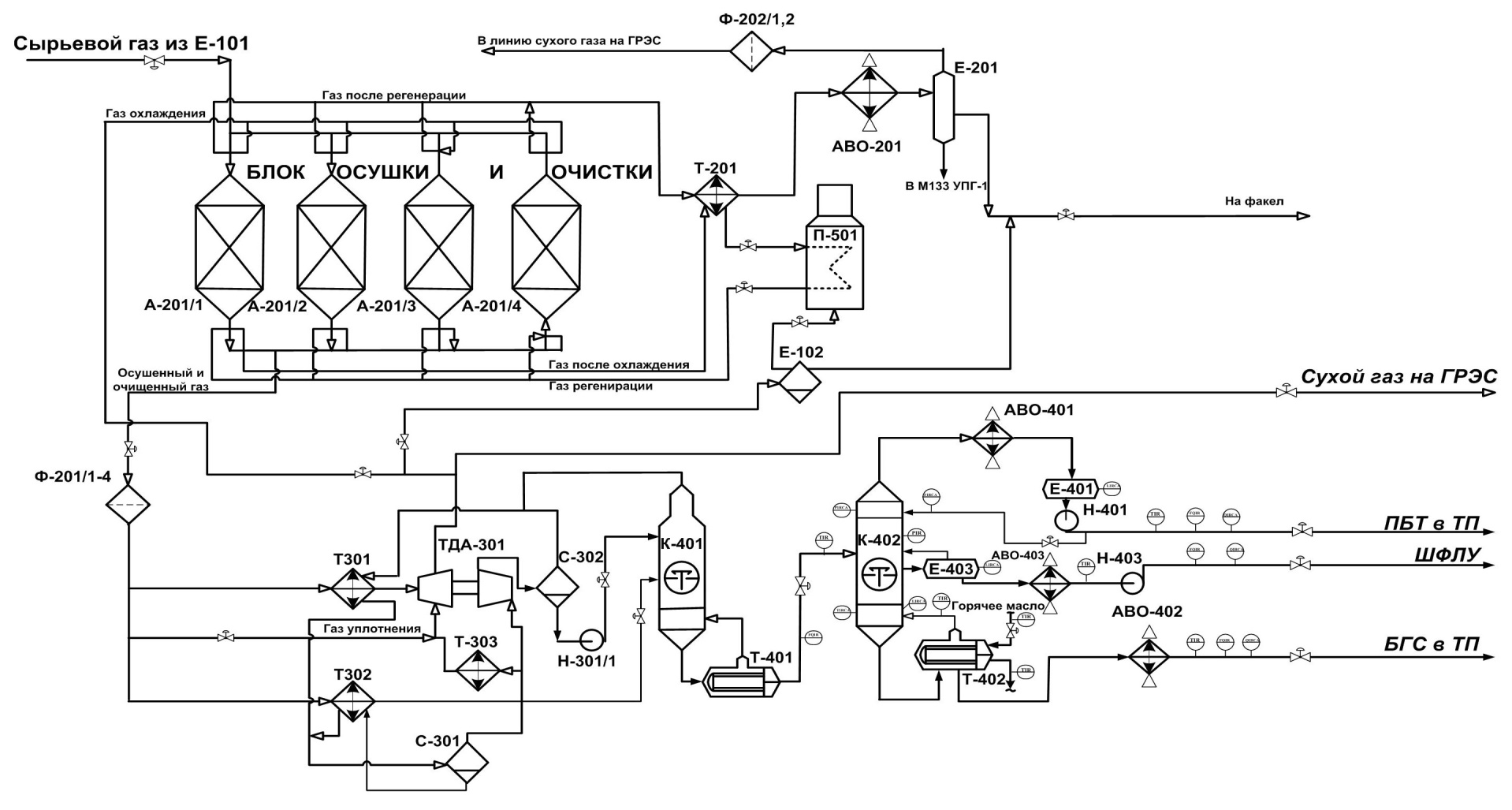