Файл: 1 техника безопасности при работе на токарных станках.docx
ВУЗ: Не указан
Категория: Не указан
Дисциплина: Не указана
Добавлен: 12.04.2024
Просмотров: 68
Скачиваний: 0
ВНИМАНИЕ! Если данный файл нарушает Ваши авторские права, то обязательно сообщите нам.
, которое должно:
- обеспечивать достаточную свободную площадь (как минимум двукратно превышающую габаритную площадь станка);
- иметь негорючее покрытие стен и потолка;
- иметь твёрдый, ровный пол (для исключения усиления вибраций и возникновения резонанса при работе оборудования) с возможностью надёжного закрепления оборудования, в том числе устанавливаемого на подпорный фундамент;
- обеспечивать негорючее покрытие пола;
- обеспечивать достаточную освещённость рабочей области и контрольно-измерительных приборов (в их числе — ПК, если он используется для управления фрезерным станком);
- обеспечивать возможность подключения к инженерным сетям (электрическим, гидравлическим, пневматическим и пр.) с параметрами, соответствующими требованиям оборудования.
Прежде чем включать фрезерный станок необходимо убедиться в его общей исправности, визуально проверить наличие (правильное подключение/закрепление) всех элементов, а также их корректное расположение — они должны находиться в исходной позиции. Необходимо проверить наличие/качество смазки (прежде всего — на направляющих инструментального портала, а также других узлах трения).
Следует обеспечить наличие режущего инструмента, необходимого для предстоящего технологического процесса, а также убедиться в нормальном состоянии фрез. Крепление фрезы в патроне шпинделя осуществляется следующим образом:
- фреза нужного типа вставляется в цангу соответствующего диаметра;
- цанга вставляется в цанговый патрон;
- патрон закрепляется в «конусе» шпинделя поджатием гайки (рекомендуется использовать инструмент из комплекта поставки станка!).
Для извлечения фрезы вышеуказанная последовательность повторяется в обратном порядке. Ряд шпинделей имеют механизм «выброса» — для облегчения извлечения фрезы из цанги, гайку шпинделя следует выкручивать до упора.
До момента включения станка необходимо убедиться в свободном вращении шпинделя (проверив его от руки). Эту операцию можно проводить только при нахождении инструментального портала в крайнем верхнем положении — во избежание повреждения фрезы при контакте с конструктивными элементами станка. Также следует проверить систему охлаждения шпинделя и её вспомогательные агрегаты (воздушный, водяной насосы, состояние фильтров). При водяном охлаждении — проконтролировать наличие/уровень жидкости.
Необходимо подготовить требуемое количество материалов (заготовок), подходящих для обработки на данном станке (прежде всего, по твёрдости материала и по габаритным размерам). Следует внимательно проверять надёжность закрепления материалов на рабочем столе.
По окончании подготовительных операций необходимо запустить станок без нагрузки («вхолостую») и проверить работоспособность/свободное движение его агрегатов. В некоторых системах ЧПУ предусмотрена функция самотестирования — перед началом обработки рекомендуется запускать её.
К работе на оборудовании должны допускаться лица, прошедшие соответствующее обучение и инструктаж. Оператору станка необходимо чётко представлять технологический процесс и последовательность операций по обработке заготовок, а также возможности фрезерного оборудования (для этого необходимо также иметь всю документацию станка в непосредственной близости к рабочему месту).
Персоналу следует работать в плотно облегающей одежде из материала, податливого на разрыв (для снижения риска «затягивания» одежды вращающимися частями станка). При работе на оборудовании оператору следует использовать средства индивидуальной защиты (перчатки, очки, амортизирующая нескользящая обувь, наушники, респиратор). Все модели фрезерных станков оборудованы легкодоступной и хорошо заметной кнопкой аварийного останова. При возникновении посторонних стуков, шумов, неправильного поведения станка в процессе работы следует немедленно остановить работу!
Прежде всего, следует отключить электропитание станка. Тщательно очистить рабочий стол от стружки и пыли при помощи специальной щётки (обычно прилагаемой к станку в комплекте поставки). Также необходимо удалить стружку, остатки заготовок и прочий мусор с пола — вокруг и вблизи станка. Необходимо всегда убирать готовые изделия, инструмент и другие рабочие материалы после завершения обработки. Регулярно (не реже одного раза в неделю) следует производить очистку потолка и стен помещения от пыли при помощи промышленного пылесоса. Не допускается размещение (складирование) остатков стружки в производственном помещении и вблизи оборудования!
После очистки станка необходимо проверить состояние смазочного слоя в узлах трения. Ни в коем случае нельзя допускать накопление пыли на смазанных деталях — в этом случае смазку необходимо заменять. При эксплуатации станка с водяным охлаждением (а также системой СОЖ) после завершения работы необходимо проверять свободную проходимость водяных магистралей и в случае необходимости — продувать их.
Следует помнить, что обязательное соблюдение всех рекомендация по технике безопасности, поддержание порядка в производственном помещении и содержание оборудования в чистоте позволят избежать риска возникновения нештатных ситуаций и обеспечить длительную бесперебойную эксплуатацию фрезерного оборудования
Фрезерный станок — это станок для обработки металлических и других деталей вращающейся фрезой при поступательном перемещении заготовки.
На фрезерных станках можно обрабатывать плоские и фасонные поверхности с прямыми и винтовыми образующими. Резание осуществляется фрезой — многолезвийным инструментом, у которого зубья расположены на поверхности тела вращения или на торце.
Ввиду многообразия работ, выполняемых фрезерованием, весьма разнообразные и типы фрез (рис. 1). Наиболее распространенными являются цилиндрические фрезы(рис. 1, a), применяемые для обработки поверхностей; дисковые (рис. 1, б) для изготовления пазов, уступов; концевые фрезы (рис. 1, в), используемые для обработки пазов, уступов, фасонных поверхностей; торцовые фрезы (рис. 1, г) для обработки поверхностей, уступов, пазов; фасонные фрезы (рис. 1, д) для изготовления фасонных поверхностей. Стрелками на рисунках показаны направления движения, сообщаемые фрезе и заготовке в процессе резания.
Для того чтобы получить фрезерованием на детали требуемую поверхность, необходимо сообщить инструменту и заготовке вполне определенные движения, согласованные друг с другом. Эти движения в станках разделяют на основные и вспомогательные.
К основным движениям относят главное движение, называемое еще движением резания, и движение подачи.
Во фрезерных станках главное движение (вращательное) совершает фреза, а движение подачи может выполнять либо заготовка, либо фреза.
Вспомогательные движения необходимы в станке для подготовки процесса резания. К вспомогательным движениям относятся движения, связанные с настройкой и наладкой станка, его управлением, закреплением и освобождением детали и инструмента, подводом инструмента к обрабатываемым поверхностям и его отводом; движения приборов для автоматического контроля размеров и т. д..
Вспомогательные движения можно выполнять на станках как автоматически, так и вручную. На станках-автоматах все вспомогательные движения в определенной последовательности выполняются автоматически.
Каждая модель станка имеет цифровое или буквенно-цифровое обозначение — шифр (например, 6P12, 6Р82, 6Р82Ш, 6610 и т. д), по которому можно составить подробную характеристику станка. Шифр содержит три или четыре цифры, из которых первая обозначает, к какой группе станков относится станок, вторая— к какому типу, третья или третья и четвертая цифры характеризуют один из важнейших параметров станка или обрабатываемой заготовки. Буква, стоящая после первой цифры, означает, что данная модель станка модернизирована (или поколение). Буква в конце цифрового шифра показывает, что на базе основной модели станка выполнен станок с небольшими изменениями. Эти станки являются модификациями основной базовой модели.
Рисунок 24 1- консоль, 2- салазки, 3-стол, 4- защитный щиток, 5- шпиндель,
6- фрезерная бабка, 7- ползун, 8- станина, 9- кожух , 10-шкаф
По принятой в СССР классификации все металлорежущие станки делят на девять групп. Фрезерные станки относятся к шестой группе. В свою очередь, каждая группа станков делится на типы.
(Прим. СМ)
Типы станков фрезерной группы:
1 – вертикально-фрезерные консольные;
2 – фрезерные станки непрерывного действия;
3 – свободная группа;
4 – копировально и гравировально-фрезерные;
5 – вертикальные бесконсольные;
6 – продольно-фрезерные,
7 – широкоуниверсальные консольные,
8 – горизонтальные консольные,
9 – разные.
Расшифровка фрезерного станка 6Р12
Рассмотрим, например, обозначение станка 6Р12. Это фрезерный станок (цифра 6) , модернизированный (буква Р), вертикально-фрезерный (цифра 1), типоразмер станка № 2 (цифра 2).
(Прим. СМ) В СССР производство консольно-фрезерных станков осуществлялось согласно пяти типоразмеров: № 0; № 1; № 2; № 3 и № 4, причем для каждого типоразмера выпускалась полная гамма станков — горизонтальные, универсальные и вертикальные. Каждый станок одной размерной гаммы имел в шифре одинаковое обозначение, совпадающее с номером типоразмера и оснащался фрезерным столом с одинаковыми размерами рабочей поверхности.
В табл. 1 представлены значения размеров рабочей поверхности стола консольно-фрезерных станков взависимости от типоразмера, а также список оборудования относящегося к определенному типоразмеру.
- обеспечивать достаточную свободную площадь (как минимум двукратно превышающую габаритную площадь станка);
- иметь негорючее покрытие стен и потолка;
- иметь твёрдый, ровный пол (для исключения усиления вибраций и возникновения резонанса при работе оборудования) с возможностью надёжного закрепления оборудования, в том числе устанавливаемого на подпорный фундамент;
- обеспечивать негорючее покрытие пола;
- обеспечивать достаточную освещённость рабочей области и контрольно-измерительных приборов (в их числе — ПК, если он используется для управления фрезерным станком);
- обеспечивать возможность подключения к инженерным сетям (электрическим, гидравлическим, пневматическим и пр.) с параметрами, соответствующими требованиям оборудования.
Прежде чем включать фрезерный станок необходимо убедиться в его общей исправности, визуально проверить наличие (правильное подключение/закрепление) всех элементов, а также их корректное расположение — они должны находиться в исходной позиции. Необходимо проверить наличие/качество смазки (прежде всего — на направляющих инструментального портала, а также других узлах трения).
Следует обеспечить наличие режущего инструмента, необходимого для предстоящего технологического процесса, а также убедиться в нормальном состоянии фрез. Крепление фрезы в патроне шпинделя осуществляется следующим образом:
- фреза нужного типа вставляется в цангу соответствующего диаметра;
- цанга вставляется в цанговый патрон;
- патрон закрепляется в «конусе» шпинделя поджатием гайки (рекомендуется использовать инструмент из комплекта поставки станка!).
Для извлечения фрезы вышеуказанная последовательность повторяется в обратном порядке. Ряд шпинделей имеют механизм «выброса» — для облегчения извлечения фрезы из цанги, гайку шпинделя следует выкручивать до упора.
До момента включения станка необходимо убедиться в свободном вращении шпинделя (проверив его от руки). Эту операцию можно проводить только при нахождении инструментального портала в крайнем верхнем положении — во избежание повреждения фрезы при контакте с конструктивными элементами станка. Также следует проверить систему охлаждения шпинделя и её вспомогательные агрегаты (воздушный, водяной насосы, состояние фильтров). При водяном охлаждении — проконтролировать наличие/уровень жидкости.
Необходимо подготовить требуемое количество материалов (заготовок), подходящих для обработки на данном станке (прежде всего, по твёрдости материала и по габаритным размерам). Следует внимательно проверять надёжность закрепления материалов на рабочем столе.
По окончании подготовительных операций необходимо запустить станок без нагрузки («вхолостую») и проверить работоспособность/свободное движение его агрегатов. В некоторых системах ЧПУ предусмотрена функция самотестирования — перед началом обработки рекомендуется запускать её.
В процессе фрезерования
К работе на оборудовании должны допускаться лица, прошедшие соответствующее обучение и инструктаж. Оператору станка необходимо чётко представлять технологический процесс и последовательность операций по обработке заготовок, а также возможности фрезерного оборудования (для этого необходимо также иметь всю документацию станка в непосредственной близости к рабочему месту).
Персоналу следует работать в плотно облегающей одежде из материала, податливого на разрыв (для снижения риска «затягивания» одежды вращающимися частями станка). При работе на оборудовании оператору следует использовать средства индивидуальной защиты (перчатки, очки, амортизирующая нескользящая обувь, наушники, респиратор). Все модели фрезерных станков оборудованы легкодоступной и хорошо заметной кнопкой аварийного останова. При возникновении посторонних стуков, шумов, неправильного поведения станка в процессе работы следует немедленно остановить работу!
После окончания работы
Прежде всего, следует отключить электропитание станка. Тщательно очистить рабочий стол от стружки и пыли при помощи специальной щётки (обычно прилагаемой к станку в комплекте поставки). Также необходимо удалить стружку, остатки заготовок и прочий мусор с пола — вокруг и вблизи станка. Необходимо всегда убирать готовые изделия, инструмент и другие рабочие материалы после завершения обработки. Регулярно (не реже одного раза в неделю) следует производить очистку потолка и стен помещения от пыли при помощи промышленного пылесоса. Не допускается размещение (складирование) остатков стружки в производственном помещении и вблизи оборудования!
После очистки станка необходимо проверить состояние смазочного слоя в узлах трения. Ни в коем случае нельзя допускать накопление пыли на смазанных деталях — в этом случае смазку необходимо заменять. При эксплуатации станка с водяным охлаждением (а также системой СОЖ) после завершения работы необходимо проверять свободную проходимость водяных магистралей и в случае необходимости — продувать их.
Следует помнить, что обязательное соблюдение всех рекомендация по технике безопасности, поддержание порядка в производственном помещении и содержание оборудования в чистоте позволят избежать риска возникновения нештатных ситуаций и обеспечить длительную бесперебойную эксплуатацию фрезерного оборудования
Назначение фрезерных станков и основные типы фрез
Фрезерный станок — это станок для обработки металлических и других деталей вращающейся фрезой при поступательном перемещении заготовки.
На фрезерных станках можно обрабатывать плоские и фасонные поверхности с прямыми и винтовыми образующими. Резание осуществляется фрезой — многолезвийным инструментом, у которого зубья расположены на поверхности тела вращения или на торце.
Ввиду многообразия работ, выполняемых фрезерованием, весьма разнообразные и типы фрез (рис. 1). Наиболее распространенными являются цилиндрические фрезы(рис. 1, a), применяемые для обработки поверхностей; дисковые (рис. 1, б) для изготовления пазов, уступов; концевые фрезы (рис. 1, в), используемые для обработки пазов, уступов, фасонных поверхностей; торцовые фрезы (рис. 1, г) для обработки поверхностей, уступов, пазов; фасонные фрезы (рис. 1, д) для изготовления фасонных поверхностей. Стрелками на рисунках показаны направления движения, сообщаемые фрезе и заготовке в процессе резания.
Для того чтобы получить фрезерованием на детали требуемую поверхность, необходимо сообщить инструменту и заготовке вполне определенные движения, согласованные друг с другом. Эти движения в станках разделяют на основные и вспомогательные.
К основным движениям относят главное движение, называемое еще движением резания, и движение подачи.
Во фрезерных станках главное движение (вращательное) совершает фреза, а движение подачи может выполнять либо заготовка, либо фреза.
Вспомогательные движения необходимы в станке для подготовки процесса резания. К вспомогательным движениям относятся движения, связанные с настройкой и наладкой станка, его управлением, закреплением и освобождением детали и инструмента, подводом инструмента к обрабатываемым поверхностям и его отводом; движения приборов для автоматического контроля размеров и т. д..
Вспомогательные движения можно выполнять на станках как автоматически, так и вручную. На станках-автоматах все вспомогательные движения в определенной последовательности выполняются автоматически.
Классификация и расшифровка фрезерных станков
Каждая модель станка имеет цифровое или буквенно-цифровое обозначение — шифр (например, 6P12, 6Р82, 6Р82Ш, 6610 и т. д), по которому можно составить подробную характеристику станка. Шифр содержит три или четыре цифры, из которых первая обозначает, к какой группе станков относится станок, вторая— к какому типу, третья или третья и четвертая цифры характеризуют один из важнейших параметров станка или обрабатываемой заготовки. Буква, стоящая после первой цифры, означает, что данная модель станка модернизирована (или поколение). Буква в конце цифрового шифра показывает, что на базе основной модели станка выполнен станок с небольшими изменениями. Эти станки являются модификациями основной базовой модели.
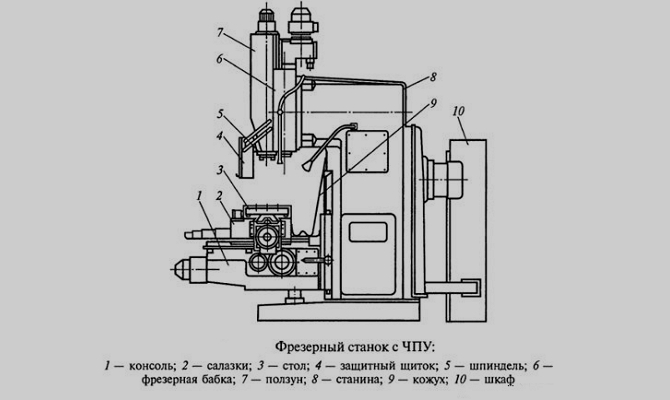
Рисунок 24 1- консоль, 2- салазки, 3-стол, 4- защитный щиток, 5- шпиндель,
6- фрезерная бабка, 7- ползун, 8- станина, 9- кожух , 10-шкаф
По принятой в СССР классификации все металлорежущие станки делят на девять групп. Фрезерные станки относятся к шестой группе. В свою очередь, каждая группа станков делится на типы.
(Прим. СМ)
Типы станков фрезерной группы:
1 – вертикально-фрезерные консольные;
2 – фрезерные станки непрерывного действия;
3 – свободная группа;
4 – копировально и гравировально-фрезерные;
5 – вертикальные бесконсольные;
6 – продольно-фрезерные,
7 – широкоуниверсальные консольные,
8 – горизонтальные консольные,
9 – разные.
Расшифровка фрезерного станка 6Р12
Рассмотрим, например, обозначение станка 6Р12. Это фрезерный станок (цифра 6) , модернизированный (буква Р), вертикально-фрезерный (цифра 1), типоразмер станка № 2 (цифра 2).
(Прим. СМ) В СССР производство консольно-фрезерных станков осуществлялось согласно пяти типоразмеров: № 0; № 1; № 2; № 3 и № 4, причем для каждого типоразмера выпускалась полная гамма станков — горизонтальные, универсальные и вертикальные. Каждый станок одной размерной гаммы имел в шифре одинаковое обозначение, совпадающее с номером типоразмера и оснащался фрезерным столом с одинаковыми размерами рабочей поверхности.
В табл. 1 представлены значения размеров рабочей поверхности стола консольно-фрезерных станков взависимости от типоразмера, а также список оборудования относящегося к определенному типоразмеру.