Файл: 1 техника безопасности при работе на токарных станках.docx
ВУЗ: Не указан
Категория: Не указан
Дисциплина: Не указана
Добавлен: 12.04.2024
Просмотров: 65
Скачиваний: 0
ВНИМАНИЕ! Если данный файл нарушает Ваши авторские права, то обязательно сообщите нам.
Растачивание
Растачивание – металлообработка отверстий, диаметр которых превышает диаметр существующих сверл, зенкеров. Данный способ обработки также используется, если отверстия имеют неравномерный припуск. Применяются расточные резцы для сквозных или глубоких отверстий.
Обработка заготовок на токарных станках в зависимости от типа операции и металла (сплава) заготовки осуществляется как с использованием СОЖ, так и «на сухую». Припуски при подборе инструмента выбирают исходя из табличных данных. После завершения операций с отверстиями проводится инструментальный контроль качества. При несоответствии показателей по точности, шероховатости заготовки подлежат дальнейшей металлообработке или выбраковываются
10 ОБТОЧКА НАРУЖНЫХ И РАСТАЧИВАНИЕ ВНУТРЕННИХ ПОВЕРХНОСТЕЙ
Обтачивание наружных цилиндрических поверхностей выполняют проходными резцами с продольной подачей, гладкие валы, — при установке заготовки в центрах.
Центровые отверстия обрабатывают на токарных, револьверных, сверлильных и двусторонних центровальных станках. Для центрования применяют типовые наборы инструмента — комбинированные центровочные сверла, а также спиральные сверла и конические зенковки.
Центровые отверстия являются, как правило, установочными базами, и поэтому от точности их исполнения зависит и точность обработки остальных поверхностей заготовки.
В полые заготовки после подрезки торца и обработки отверстия с двух сторон вводят пробки или оправки с зацентрованными отверстиями или на кромке отверстия снимают конические фаски, используемые в качестве технологических баз с последующим удалением их при отделочной обработке.
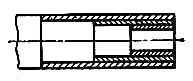
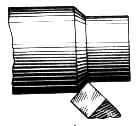
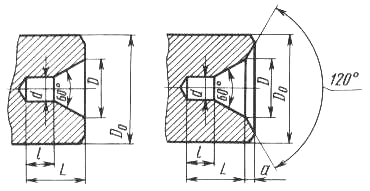
Рисунок 7 а-схемы обработки, б-разновидности центровочных отверстий.
Ступенчатые валы обтачивают по схемам деления припуска на части или деления длины заготовки на части. В первом случае обрабатывают заготовки с меньшей глубиной резания, однако общий путь резца получается большим и резко возрастает
То.
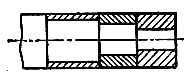
Рисунок 8 обработка заготовки с большой глубиной резания
Во втором случае припуск с каждой ступени срезается сразу за счет обработки заготовки с большой глубиной резания. При этом Т0 уменьшается, но требуется большая мощность привода станка.
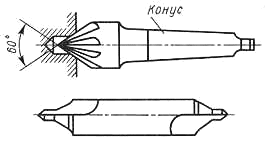
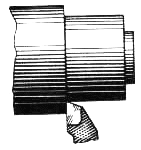
Рисунок 9 упорные проходные резцы
Нежесткие валы рекомендуется обрабатывать упорными проходными резцами, с главным углом в плане j = 90°. При обработке заготовок валов такими резцами радиальная составляющая силы резания Ру = 0, что снижает деформацию заготовок.
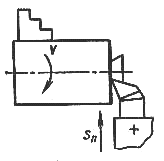
Рисунок 10 схема подрезания торцов
Подрезание торцов заготовки выполняют перед обтачиванием наружных поверхностей. Торцы подрезают подрезными резцами с поперечной подачей к центру или от центра заготовки. При подрезании от центра к периферии поверхность торца получается менее шероховатой.
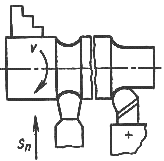
Рисунок 11 схема обтачивания скруглений
Обтачивание скруглений между ступенями валов - галтелей выполняют проходными резцами с закруглением между режущими кромками по соответствующему радиусу с продольной или поперечной подачей.
Точение канавок выполняют с поперечной подачей канавочными или фасонными резцами, у которых длина главной режущей кромки равна ширине протачиваемой канавки. Широкие канавки протачивают теми же резцами сначала с поперечной, а затем с продольной подачей.
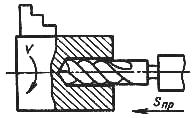
Рисунок 12 схема сверления в заготовке цилиндрического отверстия
Обработку отверстий в валах выполняют соответствующими инструментами, закрепляемыми в пиноли задней бабки. На рисунке слева показана схема сверления в заготовке цилиндрического отверстия.
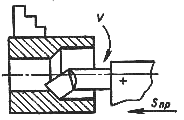
Рисунок 13 схема растачивания внутренних цилиндрических поверхностей
Растачивание внутренних цилиндрических поверхностей выполняют расточными резцами, закрепленными в резцедержателе станка, с продольной подачей.
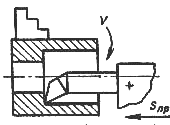
Рисунок 14 растачивание проходными резцами
Гладкие сквозные отверстия растачивают проходными резцами; ступенчатые и глухие — упорными расточными резцами.
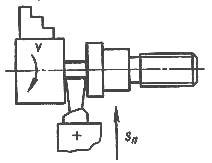
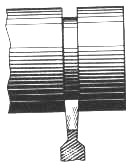
Рисунок 15 отрезание обработанных деталей
Отрезку обработанных деталей выполняют отрезными резцами с поперечной подачей. При отрезке детали резцом с прямой главной режущей кромкой (рисунок слева) разрушается образующаяся шейка и приходится дополнительно подрезать торец готовой детали.
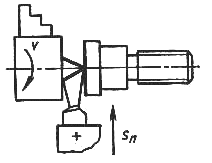
Рисунок 16
При отрезке детали резцом с наклонной режущей кромкой .торец получается чистым.
Обтачивание наружных конических поверхностей заготовок осуществляют на токарно-винторезных станках одним из следующих способов.
1. Широкими токарными резцами.
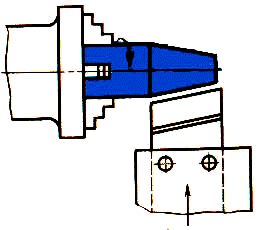
Рисунок 17
Обтачивают короткие конические поверхности с длиной образующей до 30мм токарными проходными резцами. Обтачивают с поперечной или продольной подачей. Этот способ можно использовать при снятии фасок с обработанных цилиндрическихповерхностей.
2. Поворотом каретки верхнего суппорта.
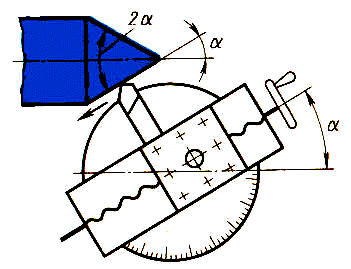
Рисунок 18
При обработке конических поверхностей каретку верхнего суппорта повертывают на угол, равный половине угла при вершине обрабатываемого конуса. Обрабатывают с ручной подачей верхнего суппорта под углом к линии центров станка (a). Таким способом обтачивают конические поверхности, длина образующей которых не превышает величины хода каретки верхнего суппорта. Угол конуса обтачиваемой поверхности любой
3. Смещением корпуса задней бабки в поперечном направлении.
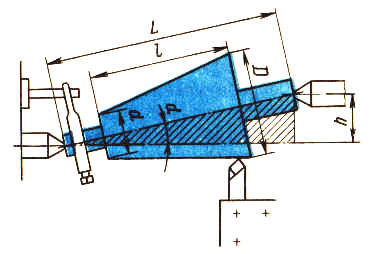
Рисунок 19
Обрабатываемую заготовку устанавливают на шариковые центры. Корпус задней бабки смещают относительно её основания в направлении, перпендикулярном к линии центров станка. При этом ось вращения заготовки располагается под углом к линии центров станка, а образующая конической поверхности — параллельно линии центров станка. Таким образом обтачивают длинные конические поверхности с небольшим углом конуса (2a < 8°) с продольной подачей резца.
4. С помощью конусной линейки.
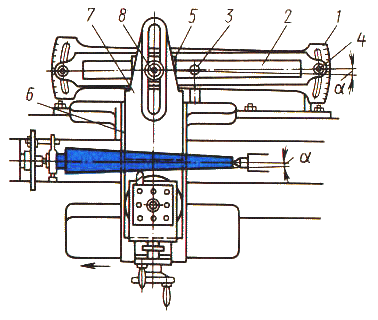
Рисунок 20
Коническую поверхность обтачивают с продольной подачей. Скорость продольной подачи складывается со скоростью поперечной подачи, получаемой от ползуна, скользящего по направляющей линейке. Сложение двух движений обеспечивает перемещение резца под углом к линии центров станка. Таким способом обтачивают длинные конические поверхности с углом при вершине конуса до 30—40°.
Обтачивание внутренних конических поверхностей выполняют так же как и наружных, но в основном используют специальные конические зенкеры или развёртки.
Обтачивание фасонных поверхностей с длиной образующей до 40 мм выполняют токарными фасонными резцами. Обтачивают только с поперечной подачей Sп.
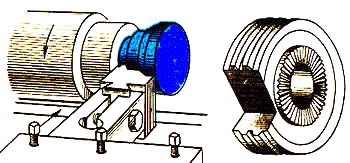
Рисунок 21
Для обработки на токарно-винторезных станках применяют, как правило, стержневые, призматические или круглые фасонные резцы; резцами остальных видов обтачивают фасонные поверхности на токарных полуавтоматах и автоматах.
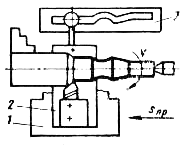
Рисунок 22
Длинные фасонные поверхности обрабатывают проходными резцами с продольной подачей с помощью фасонного копира, устанавливаемого вместо конусной линейки.
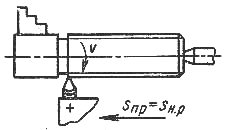
Рисунок 23
Нарезание резьбы на токарно-винторезных станках выполняют резцами, метчиками и плашками. Форма режущих кромок резцов определяется профилем и размерами поперечного сечения нарезаемых резьб. Резец устанавливают на станке по шаблону. Резьбу нарезают с продольной подачей резца Sпр. При нарезании резьбы продольный суппорт получает поступательное движение от ходового винта. Это необходимо для того, чтобы резец получал равномерное поступательное движение, что обеспечивает постоянство шага нарезаемой резьбы.
11 ИНСТРУКТАЖ ПО ТБ ПРИ ВЫПОЛНЕНИИ РАБОТ НА ФРЕЗЕРНЫХ СТАНКАХ. РАЗНОВИДНОСТИИ НАЗЧЕНИЕ ФРЕЗЕРНЫХ СТАНКОВ (ЭНГФ)
Фрезерный станок содержит ряд элементов с острыми кромками (прежде всего саму фрезу), случайное касание которых незащищёнными участками тела и конечностей (в том числе при неработающем станке — при установке/замене/закреплении режущего инструмента) может привести к порезам!
Электрические узлы станка представляют опасность поражения током! Корпусные детали также могут оказаться под напряжением — в случае неисправности/нарушения схемы заземления. Источником статического электричества (в том числе заряда на корпусе) может быть стружа и мелкая пыль, образующаяся при фрезеровании ряда органических материалов (дерева, пластика, оргстекла и пр.). При работе фрезерного станка движущиеся/вращающиеся части (инструментальный портал, шпиндель, фреза), представляют опасность для соприкосновения, вплоть до потери конечностей!
Заготовки из ряда материалов при фрезеровании дают обильную стружку и мелкую пыль, представляющую опасность при вдыхании и попадании на слизистые оболочки тела!
Скопление стружки на самом оборудовании и вблизи него (в производственном помещении) также представляют опасность возгорания!
Гидравлические (и/или пневматические) системы под давлением могут представлять опасность разрыва. Кроме того, некоторые эксплуатационные материалы (в их числе смазка, СОЖ, другие жидкости) обладают токсическим действием!
Ряд узлов станка (а также элементов корпуса) в процессе работы подвержены сильному нагреву и могут представлять опасность ожогов!
Меры безопасности при эксплуатации фрезерного оборудования
Подготовка к работе
Перед началом эксплуатации оборудования необходимо правильно организовать рабочее место