Файл: Вариант 1 Установка стабилизации нефтей на промысле.docx
ВУЗ: Не указан
Категория: Не указан
Дисциплина: Не указана
Добавлен: 28.04.2024
Просмотров: 101
Скачиваний: 1
ВНИМАНИЕ! Если данный файл нарушает Ваши авторские права, то обязательно сообщите нам.
11.
Колонна 11 разделена полуглухой тарелкой на две части: пары из нижней части переходят в верхнюю, а жидкость из верхней части накапливается в аккумуляторе (кармане) внутри колонны. Отсюда жидкость (легкая часть сырья) забирается насосом 9 и подается в змеевики печи 3. Ас низа колонны 11 тяжелая часть сырья забирается насосом 10 и подается в змеевики печи 2.Продукты крекинга по выходе из змеевиков печей 2 и 3 поступают в выносную реакционную камеру 4, откуда переходят в испаритель высокого давления 7. Здесь от смеси отделяется жидкий крекинг-остаток, который затем через редукционный клапан поступает в испарительную колонну низкого давления 12 (испаритель).
Газы и пары по выходе из верхней части испарителя 7 направляются в низ колонны 11, с верха которой, уходят бензиновая фракция и газ. Пары конденсируются, и смесь охлаждается в холодильнике- конденсаторе 6. Далее газожидкостная смесь разделяется в газосепараторе 5 на газ и бензиновую фракцию. Газ поступает на ГФУ, а балансовое количество бензина — на стабилизацию. Насосом 8 бензин- орошение подается на верхнюю тарелку колонны 11. В колонне 12 в результате снижения давления из крекинг-остатка выделяются газойлевые фракции; несконденсированные пары из колонны 12 направляются в холодильник-конденсатор 13, и конденсат собирается в приемнике 14. Отсюда часть конденсата насосом 15 возвращается в колонну 12 в качестве орошения, а балансовое его количество выводится с установки. Крекинг-остаток подается насосом 16 в вакуумную колонну 17. Целевой продукт —термогазойль — выводится как промежуточный продукт с 17-й тарелки вакуумной колонны 17.
Во избежание коксования крекинг-остатка и для улучшения транспортирования его разбавляют менее вязким продуктом. Крекинг-остаток можно использовать в производстве битумов, а также как связующее вещество при брикетировании углей. Выход термогазойля на сырье вакуумной колонны составляет около 72 % (масс.).
Некоторые установки термического крекинга по получению термогазойля работают по схеме, отличной от описанной. Целевой продукт отбирается из колонны 12, выход термогазойля в этом случае составляет 24—27 % (масс.). При индексе корреляции 95—100.
Режим работы основных аппаратов:
Вариант № 13
Установка замедленного коксования в необогреваемых камерах
РИС. II1-5. Технологическая схема установки замедленного коксования в необогреваемых камерах: 1, 6, 12—15 — насосы; 2, 3 — трубчатые печи; 4 — приемник; 5, 5' — камеры замедленного коксования; 7 — четырехходовые краны; 8, 19, 21 — аппараты воздушного охлаждения; 9 — ректификационная колонна; 10, 11 — отпарные колонны; 16 — холодильник; 17 — водогазо-отделитель; 18, 20 — теплообменники.
Процесс замедленного коксования в необогреваемых камерах предназначен для получения крупнокускового нефтяного кокса как основного целевого продукта, а также легкого и тяжелого газойлей, бензина и газа. Сырьем для коксования служат малосернистые атмосферные и вакуумные нефтяные остатки, сланцевая смола, тяжелые нефти из битуминозных песков, каменноугольный деготь и гильсонит. Эти виды сырья дают губчатый кокс. Для получения высококачественного игольчатого кокса используют более термически стойкое ароматизированное сырье, например смолу пиролиза, крекинг-остатки и каталитические газойли.
Основными показателями качества сырья являются плотность, коксуемость по Конрадсону и содержание серы. Выход кокса определяется коксуемостью сырья и практически линейно изменяется в зависимости от этого показателя. При коксовании в необогреваемых камерах остаточного сырья выход кокса составляет 1,5—1,6 от коксуемости сырья. При коксовании дистиллятного сырья выход кокса не соответствует коксуемости сырья, поэтому составлять материальный баланс расчетным методом для такого сырья нельзя.
Главным потребителем кокса является алюминиевая промышленность, где кокс служит восстановителем (анодная масса) при выплавке алюминия из алюминиевых руд. Кроме того, кокс используют в качестве сырья при изготовлении графитированных электродов для сталеплавильных печей, для получения карбидов (кальция, кремния) и сероуглерода.
Основными показателями качества кокса являются истинная плотность, содержание серы, зольность и микроструктура. Для игольчатого кокса истинная плотность должна быть не ниже 2,09 г/см3, для кокса марки КНПС (пиролизного специального), используемого в качестве конструкционного материала, она находится в пределах 2,04—-2,08 г/см3 [151.
Содержание серы в коксе почти всегда больше, чем в остаточном сырье коксования. Из остатков малосернистых нефтей получают малосернистый кокс, содержащий, как правило, до 1,5 % (масс.) серы; кокс из сернистых остатков содержит обычно 2,0—4,5% (масс.) серы, а из высокосернистых — более 4,0% (масс.).
Содержание золы в коксе в значительной мере зависит от глубины обессоливания нефти перед ее перегонкой.
В Советском Союзе проектируются и находятся в эксплуатации установки замедленного коксования мощностью 300, 600 и 1500 тыс. т сырья в год. На рис. Ш-5 приведена установка мощностью 600 тыс. т в год, которая включает реакторный блок, состоящий из четырех коксовых камер, две трубчатые нагревательные печи, блок фракционирования и систему регенерации тепла и охлаждения продуктов.
Сырье — гудрон или крекинг-остаток (или их смесь)— Подается насосом 1 двумя параллельными потоками в трубы подовых и потолочных экранов печей 2 и 3, где оно нагревается до 350—380 °С. Затем сырье поступает в нижнюю часть колонны 9 на верхнюю каскадную тарелку. Сюда же под нижнюю тарелку поступают горячие газы и пары продуктов коксования, образующиеся в двух параллельно работающих камерах 5 (или 5'). В колонне сырье встречается с восходящим потоком газов и паров и в результате контакта тяжелые фракции паров конденсируются и смешиваются с сырьем. Таким образом, в нижней части колонны образуется смесь сырья с рециркулятом, обычно называемая вторичным сырьем. Если в сырье содержались легкие фракции, то они в результате контакта с высокотемпературными парами испаряются и уходят в верхнюю часть колонны 9.
Вторичное сырье с низа колонны 9 забирается насосом 6 и возвращается в змеевики печи 2 и 3, в верхние трубы конвекционной секции и правые подовые и потолочные экраны. Эта часть труб относится к «реакционному» змеевику, здесь вторичное сырье нагревается до 490—510 °С. Во избежание закоксовывания труб этой секции в трубы потолочного экрана подают перегретый водяной пар, так называемый турбулизатор, в количестве ≈3 % (масс.) на вторичное сырье. За счет подачи турбули- затора увеличивается скорость прохождения потока через реакционный змеевик. Избыток перегретого водяного пара может подаваться в отпарные колонны
10 и 11.
Парожидкостная смесь из печей 2 и 3 вводится параллельными потоками через четырехходовые краны 7 в две работающие камеры 5; две другие камеры (5') в это время подготавливают к рабочему периоду цикла. Горячее сырье подается в камеры вниз и постепенно заполняет их. Объем камер достаточно большой (внутренний диаметр 4,6—5,5 м, высота 27—28 м), и время пребывания сырья в них значительно. Здесь в камерах сырье подвергается крекингу. Пары продуктов разложения непрерывно выводятся из камер сверху и поступают в колонну 9, а тяжелый остаток остается. Жидкий остаток постепенно превращается в кокс.
В колонне 9 продукты коксования разделяются. С верха колонны уходят пары бензина и воды, а также газ коксования. Эти продукты проходят аппарат воздушного охлаждения 8, затем водяной холодильник 16 для дополнительного охлаждения и поступают в водогазоотделитель 17, где разделяются на водный конденсат, нестабильный бензин и жирный газ.
Часть нестабильного бензина нагнетается насосом 15 в качестве орошения на верхнюю тарелку колонны 8.Балансовое количество бензина проходит теплообменник 18, где нагревается за счет тепла легкого газойля, и передается в секцию стабилизации. Водный конденсат, отводимый из водогазоотделителя 17, подается насосом 14 через теплообменник 20 в пароперегреватели, расположенные в конвекционных секциях печей 2 и 3.
Легкий и тяжелый газойли, отводимые из отпарных колонн 10 и 11, направляются соответственно насосами 13 и 12 через теплообменники нагрева нестабильного бензина 18, водного конденсата 20 и аппараты воздушного охлаждения 19 и 21 в резервуары. После заполнения камер коксом, образующимся в процессе, камеры отключают и продувают водяным паром для удаления оставшихся жидких продуктов и нефтяных паров. Удаляемые продукты поступают вначале в колонну 9, а затем, когда температура кокса понизится до 400—405 °С, поток паров отдувают в приемник 4. Подачу водяного пара продолжают до снижения температуры кокса до 200 °С, далее в камеру подают воду до тех пор пока вновь подаваемые порции воды, пары которой выходят в атмосферу, не перестанут испаряться, т. е. пока в сливной трубе приемника 4 не появится вода. Кокс из камер выгружается гидравлическим способом — посредством гидрорезаков с использованием воды давлением 10—15 МПа.
Установка замедленного коксования мощностью 1,5 млн. т сырья в год аналогична описанной, но она оборудована шестью коксовыми камерами и тремя трубчатыми печами, каждая из которых обслуживает две камеры; диаметр камер 7 м, высота 30 м. Технологический режим установки:
Вариант № 14
Установка непрерывного коксования в псевдоожиженном слое кокса (термоконтактный крекинг)
Колонна 11 разделена полуглухой тарелкой на две части: пары из нижней части переходят в верхнюю, а жидкость из верхней части накапливается в аккумуляторе (кармане) внутри колонны. Отсюда жидкость (легкая часть сырья) забирается насосом 9 и подается в змеевики печи 3. Ас низа колонны 11 тяжелая часть сырья забирается насосом 10 и подается в змеевики печи 2.Продукты крекинга по выходе из змеевиков печей 2 и 3 поступают в выносную реакционную камеру 4, откуда переходят в испаритель высокого давления 7. Здесь от смеси отделяется жидкий крекинг-остаток, который затем через редукционный клапан поступает в испарительную колонну низкого давления 12 (испаритель).
Газы и пары по выходе из верхней части испарителя 7 направляются в низ колонны 11, с верха которой, уходят бензиновая фракция и газ. Пары конденсируются, и смесь охлаждается в холодильнике- конденсаторе 6. Далее газожидкостная смесь разделяется в газосепараторе 5 на газ и бензиновую фракцию. Газ поступает на ГФУ, а балансовое количество бензина — на стабилизацию. Насосом 8 бензин- орошение подается на верхнюю тарелку колонны 11. В колонне 12 в результате снижения давления из крекинг-остатка выделяются газойлевые фракции; несконденсированные пары из колонны 12 направляются в холодильник-конденсатор 13, и конденсат собирается в приемнике 14. Отсюда часть конденсата насосом 15 возвращается в колонну 12 в качестве орошения, а балансовое его количество выводится с установки. Крекинг-остаток подается насосом 16 в вакуумную колонну 17. Целевой продукт —термогазойль — выводится как промежуточный продукт с 17-й тарелки вакуумной колонны 17.
Во избежание коксования крекинг-остатка и для улучшения транспортирования его разбавляют менее вязким продуктом. Крекинг-остаток можно использовать в производстве битумов, а также как связующее вещество при брикетировании углей. Выход термогазойля на сырье вакуумной колонны составляет около 72 % (масс.).
Некоторые установки термического крекинга по получению термогазойля работают по схеме, отличной от описанной. Целевой продукт отбирается из колонны 12, выход термогазойля в этом случае составляет 24—27 % (масс.). При индексе корреляции 95—100.
Режим работы основных аппаратов:
Аппарат | Температура, °С | Давление, МПа |
Печь 2 | | |
вход | 390-410 | 5,0-5,6 |
выход | 490-500 | 2,2-2,8 |
Печь 3 | | |
вход | 290-320 | 5,0-6,6 |
выход | 530-550 | 2,3-2,9 |
Реакционная камера 4 | | |
верх | 495-500 | 2,0-2,6 |
низ | 460-470 | - |
Испаритель высокого давления 7 | | |
верх | 450-460 | 1,0-1,3 |
низ | 430-440 | - |
Ректификационная колонна 11 | | |
верх | 180-220 | - |
аккумулятор | 300-330 | 0,9-1,3 |
низ | 390-410 | - |
Испарительная колонна низкого давления 12 | | |
верх | 170-200 | - |
низ | 400-415 | 0,25-0,40 |
Вакуумная колонна 17 | | |
вход | 305-345 | 0,007-0,013 |
верх | 70-92 | - |
низ | 300-320 | - |
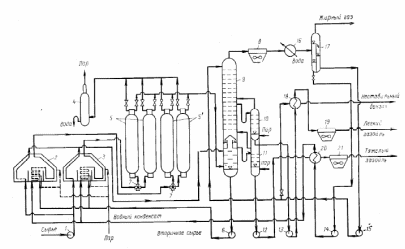
Вариант № 13
Установка замедленного коксования в необогреваемых камерах
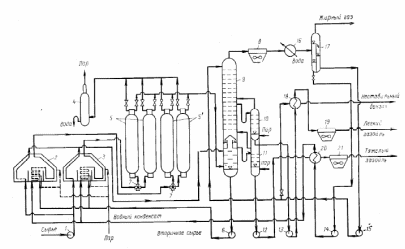
РИС. II1-5. Технологическая схема установки замедленного коксования в необогреваемых камерах: 1, 6, 12—15 — насосы; 2, 3 — трубчатые печи; 4 — приемник; 5, 5' — камеры замедленного коксования; 7 — четырехходовые краны; 8, 19, 21 — аппараты воздушного охлаждения; 9 — ректификационная колонна; 10, 11 — отпарные колонны; 16 — холодильник; 17 — водогазо-отделитель; 18, 20 — теплообменники.
Процесс замедленного коксования в необогреваемых камерах предназначен для получения крупнокускового нефтяного кокса как основного целевого продукта, а также легкого и тяжелого газойлей, бензина и газа. Сырьем для коксования служат малосернистые атмосферные и вакуумные нефтяные остатки, сланцевая смола, тяжелые нефти из битуминозных песков, каменноугольный деготь и гильсонит. Эти виды сырья дают губчатый кокс. Для получения высококачественного игольчатого кокса используют более термически стойкое ароматизированное сырье, например смолу пиролиза, крекинг-остатки и каталитические газойли.
Основными показателями качества сырья являются плотность, коксуемость по Конрадсону и содержание серы. Выход кокса определяется коксуемостью сырья и практически линейно изменяется в зависимости от этого показателя. При коксовании в необогреваемых камерах остаточного сырья выход кокса составляет 1,5—1,6 от коксуемости сырья. При коксовании дистиллятного сырья выход кокса не соответствует коксуемости сырья, поэтому составлять материальный баланс расчетным методом для такого сырья нельзя.
Главным потребителем кокса является алюминиевая промышленность, где кокс служит восстановителем (анодная масса) при выплавке алюминия из алюминиевых руд. Кроме того, кокс используют в качестве сырья при изготовлении графитированных электродов для сталеплавильных печей, для получения карбидов (кальция, кремния) и сероуглерода.
Основными показателями качества кокса являются истинная плотность, содержание серы, зольность и микроструктура. Для игольчатого кокса истинная плотность должна быть не ниже 2,09 г/см3, для кокса марки КНПС (пиролизного специального), используемого в качестве конструкционного материала, она находится в пределах 2,04—-2,08 г/см3 [151.
Содержание серы в коксе почти всегда больше, чем в остаточном сырье коксования. Из остатков малосернистых нефтей получают малосернистый кокс, содержащий, как правило, до 1,5 % (масс.) серы; кокс из сернистых остатков содержит обычно 2,0—4,5% (масс.) серы, а из высокосернистых — более 4,0% (масс.).
Содержание золы в коксе в значительной мере зависит от глубины обессоливания нефти перед ее перегонкой.
В Советском Союзе проектируются и находятся в эксплуатации установки замедленного коксования мощностью 300, 600 и 1500 тыс. т сырья в год. На рис. Ш-5 приведена установка мощностью 600 тыс. т в год, которая включает реакторный блок, состоящий из четырех коксовых камер, две трубчатые нагревательные печи, блок фракционирования и систему регенерации тепла и охлаждения продуктов.
Сырье — гудрон или крекинг-остаток (или их смесь)— Подается насосом 1 двумя параллельными потоками в трубы подовых и потолочных экранов печей 2 и 3, где оно нагревается до 350—380 °С. Затем сырье поступает в нижнюю часть колонны 9 на верхнюю каскадную тарелку. Сюда же под нижнюю тарелку поступают горячие газы и пары продуктов коксования, образующиеся в двух параллельно работающих камерах 5 (или 5'). В колонне сырье встречается с восходящим потоком газов и паров и в результате контакта тяжелые фракции паров конденсируются и смешиваются с сырьем. Таким образом, в нижней части колонны образуется смесь сырья с рециркулятом, обычно называемая вторичным сырьем. Если в сырье содержались легкие фракции, то они в результате контакта с высокотемпературными парами испаряются и уходят в верхнюю часть колонны 9.
Вторичное сырье с низа колонны 9 забирается насосом 6 и возвращается в змеевики печи 2 и 3, в верхние трубы конвекционной секции и правые подовые и потолочные экраны. Эта часть труб относится к «реакционному» змеевику, здесь вторичное сырье нагревается до 490—510 °С. Во избежание закоксовывания труб этой секции в трубы потолочного экрана подают перегретый водяной пар, так называемый турбулизатор, в количестве ≈3 % (масс.) на вторичное сырье. За счет подачи турбули- затора увеличивается скорость прохождения потока через реакционный змеевик. Избыток перегретого водяного пара может подаваться в отпарные колонны
10 и 11.
Парожидкостная смесь из печей 2 и 3 вводится параллельными потоками через четырехходовые краны 7 в две работающие камеры 5; две другие камеры (5') в это время подготавливают к рабочему периоду цикла. Горячее сырье подается в камеры вниз и постепенно заполняет их. Объем камер достаточно большой (внутренний диаметр 4,6—5,5 м, высота 27—28 м), и время пребывания сырья в них значительно. Здесь в камерах сырье подвергается крекингу. Пары продуктов разложения непрерывно выводятся из камер сверху и поступают в колонну 9, а тяжелый остаток остается. Жидкий остаток постепенно превращается в кокс.
В колонне 9 продукты коксования разделяются. С верха колонны уходят пары бензина и воды, а также газ коксования. Эти продукты проходят аппарат воздушного охлаждения 8, затем водяной холодильник 16 для дополнительного охлаждения и поступают в водогазоотделитель 17, где разделяются на водный конденсат, нестабильный бензин и жирный газ.
Часть нестабильного бензина нагнетается насосом 15 в качестве орошения на верхнюю тарелку колонны 8.Балансовое количество бензина проходит теплообменник 18, где нагревается за счет тепла легкого газойля, и передается в секцию стабилизации. Водный конденсат, отводимый из водогазоотделителя 17, подается насосом 14 через теплообменник 20 в пароперегреватели, расположенные в конвекционных секциях печей 2 и 3.
Легкий и тяжелый газойли, отводимые из отпарных колонн 10 и 11, направляются соответственно насосами 13 и 12 через теплообменники нагрева нестабильного бензина 18, водного конденсата 20 и аппараты воздушного охлаждения 19 и 21 в резервуары. После заполнения камер коксом, образующимся в процессе, камеры отключают и продувают водяным паром для удаления оставшихся жидких продуктов и нефтяных паров. Удаляемые продукты поступают вначале в колонну 9, а затем, когда температура кокса понизится до 400—405 °С, поток паров отдувают в приемник 4. Подачу водяного пара продолжают до снижения температуры кокса до 200 °С, далее в камеру подают воду до тех пор пока вновь подаваемые порции воды, пары которой выходят в атмосферу, не перестанут испаряться, т. е. пока в сливной трубе приемника 4 не появится вода. Кокс из камер выгружается гидравлическим способом — посредством гидрорезаков с использованием воды давлением 10—15 МПа.
Установка замедленного коксования мощностью 1,5 млн. т сырья в год аналогична описанной, но она оборудована шестью коксовыми камерами и тремя трубчатыми печами, каждая из которых обслуживает две камеры; диаметр камер 7 м, высота 30 м. Технологический режим установки:
Температура, °С | |
входа сырья в камеры | 490-510 |
выхода паров из камеры | 440-460 |
Давление в камерах, МПа | 0,18-0,60 |
Кратность циркуляции (на сырье) | 0,1-1,1 |
Время заполнения камеры коксом, ч | ≈24 |
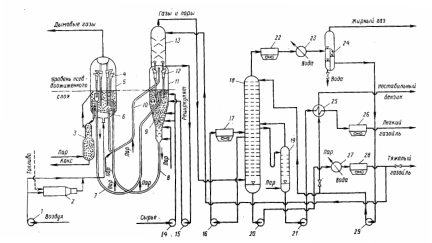
Вариант № 14
Установка непрерывного коксования в псевдоожиженном слое кокса (термоконтактный крекинг)