Файл: Сырьевая база и подготовка материалов к металлургическому переделу.doc
ВУЗ: Не указан
Категория: Не указан
Дисциплина: Не указана
Добавлен: 17.03.2024
Просмотров: 364
Скачиваний: 0
СОДЕРЖАНИЕ
3.1 Разжижители и шлакообразующие материалы.................................93
4.1 Цель и методы подготовки шихты.....................................................99
6.2 Обезвоживание концентратов.........................................................156
6.3 Обжиг железных руд........................................................................157
8.2 Производство кокса...........................................................................174
8.10 Качество металлургического кокса................................................202
3.1 Разжижители и шлакообразующие материалы
Шлакообразующие смеси и брикеты
4.1 Цель и методы подготовки шихты
Таблица 6.1 – Сравнительные характеристики различных сепараторов
6.2 Обезвоживание концентратов
ПОНЯТИЯ ОДНОРОДНОСТИ И УСРЕДНЕННОСТИ
Рисунок 7.1 – Усреднительный склад
Рисунок 7.2 – Устройство саморазгружающейся тележки
Таблица 8.2 – Структура запасов углей Донбасса
Таблица 8.8 – Коксуемость углей Донецкого бассейна
Рисунок 8.4 – Схема процесса коксования шихты в камере коксовой печи
Рисунок 8.5 – Поперечный разрез коксовой батареи
8.10 Качество металлургического кокса
Рисунок 8.7 – Барабаны для механического испытания кокса
Таблица 8.11 – Ситовый состав некоторых коксов
Молотковые дробилки относительно просты по устройству и в эксплуатации, характеризуются высокой ( 10) степенью дробления.
Молотковая дробилка с диаметром ротора 1300 и его длиной 1600 мм весит 20 т и имеет производительность 160-300 т/ч.
Измельчение материалов является подготовительной операцией к обогащению, выполняется в барабанных мельницах. Они представляют собой вращающийся барабан, в котором пересыпаются и разрушают дробимый материал дробящие тела: шары, стержни и куски дробимого материала. Мельницы бывают шаровые, стержневые и мельницы самоизмельчения. На обогатительных фабриках наибольшее распространение имеют шаровые мельницы. Так как дробление сухого материала создает много пыли, то в подавляющем большинстве случаев в мельницы подают дробимый материал вместе с водой (пульпу), которая и уносит продукт дробления. Мельницы подобного типа имеют диаметр 900-4000 мм и длину барабана 800-5500 мм. Масса загруженных шаров изменяется от 1,5 до 140 т при скорости вращения 17-42 об/мин. Такие мельницы могут измельчать около 95 % материала до содержания фракции 0,074 мм. На рис. 4.8 приведена схема шаровой мельницы. Вращающийся барабан мельницы цапфами укреплен в двух подшипниках, установленных на фундаменте. Загрузка мельницы материалом производится через цапфу 1 с помощью комбинированного питателя, состоящего из черпака улиткообразной формы 2 и спирали 3. Разгрузка мельница осуществляется через цапфу 4 большего диаметра, благодаря чему избыток пульпы (представляющей взвесь измельченного материала в воде) свободно выливается из мельницы. Существуют и другие способы разгрузки.
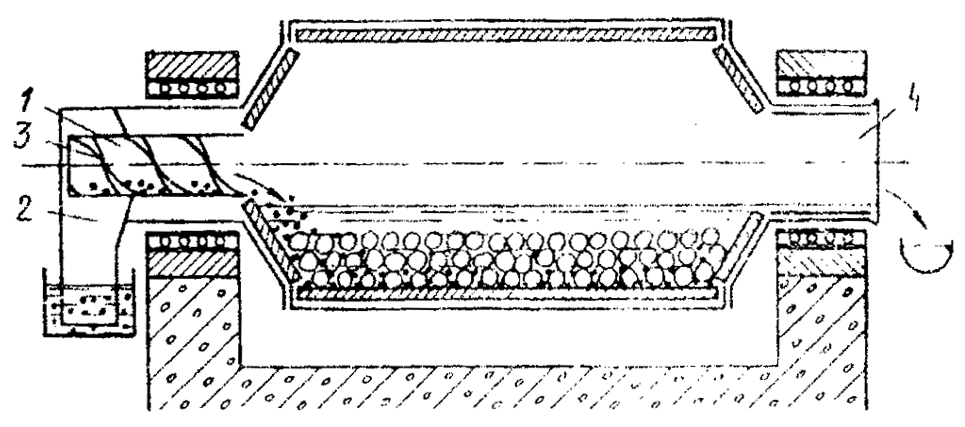
Рисунок 4.8 – Продольный разрез шаровой мельницы
С уменьшением исходного размера кусков дробимого материала существенно увеличивается производительность шаровых мельниц.
С учетом эффективности всех операций дробления-измельчения оптимальная крупность кусков материала, загружаемого в шаровые мельницы, составляет 5-20 мм. Степень заполнения мельницы шарами 40-50 %.
Производительность шаровой мельницы диаметром и длиной 3 м при питании материалом крупностью 0-20 мм составляет 55 т/ч при дроблении до 0,2 мм и 15 т/ч при дроблении до 0,075 мм. Производительность самых крупных мельниц достигает 200 т/час.
На дробильно-обогатительных фабриках наряду с шаровыми применяют стержневые мельницы, отличающиеся от первых формой дробящих тел – вместо шаров внутренняя полость цилиндрического барабана заполняется стальными стержнями. Принцип работы стержневых мельниц такой же, как и шаровых. Измельченный в стержневых мельницах материал характеризуется большей однородностью по размеру зерен. Благодаря отсутствию переизмельчения, стержневые мельницы обладают повышенной, по сравнению с шаровыми, производительностью и пониженным удельным расходом энергии.
Измельчение является одним из наиболее дорогих процессов дробления. Стоимость измельчения достигает 80 % общих расходов на дробление руды. При производительности самых крупных мельниц 200-220 т/ч расход электроэнергии на 1 т материала достигает 15- 30 кВтч. Это служит главной причиной, заставляющей работать над созданием новых, более совершенных типов мельниц.
В последние годы в практике обогащения нашли применение мельницы вибрационного действия, в которых измельчение осуществляется под действием ударов дробящих тел, которые перемещаются в результате приложения к ним вибрационных воздействий с частотой колебаний до 300 в минуту.
Таблица 4.2 – Условные обозначения и характеристики работы дробилок и мельниц
Условные обозначения | Размеры общие/щели | Производительность,т/ч | Вес,т | Мощность, кВт |
Щековые | ||||
ЩДС – 1,62,5 | 5,06,53,8/1,62,50,2 | 140,0 | | 150 |
ЩДС – 0,60,9 | 2,12,32,4/0,60,90,2 | 55,0 | | 150 |
ЩДП 46 | 4,63,82,9/0,91,20,2 | 220-310 | 59 | 210 |
ЩДП 2125 | 6,65,74,7/1,52,10,3 | 625-780 | 215 | 400 |
Конусные | ||||
ККД 500/75 | 1,751,351,6/0,6-0,075 | 180,0 | 37,0 | |
ККД 1500/300 | 5,34,07,2/3,0-0,375 | до 2000,0 | 120,0 | 650 |
КРД 500/60 | | 200,0 | | 210 |
КДД 900/100 | | 680,0 | | 400 |
КСД 3000 | | 1200,0 | | 400 |
КСД 600 | | 5,0 | 3,7 | 30 |
КМД 1200 | | 24 | | 75 |
КМД 300 | | 160 | | 400 |
ВАЛКОВЫЕ | ||||
а) двухвалковые | ||||
ДВГ – 2 | d – 0,4 м l– 0,25 | 5 - 20 | 2,1 | 25,0 |
ДВГ - 3 | d – 0,4 м l – 0,25 | 2.7-16 | | |
ДГ 400-250 | d – 0,4 м l – 0,25 | | | |
СМ – 12Б | | | | |
ДР | | | | |
Г 80 50 | | | | |
Г 150 60 | d – 1,5 м l – 0,6 | 15-17 | 32,4 | 55,0 |
Продолжение таблицы 4.2
Условные обозначения | Размеры общие/щели | Производительность,т/ч | Вес,т | Мощность, кВт |
б) зубчатые валки | ||||
ДДЗ–1м; 2м; 3м | d – 0,45-0,9 м l – 0,5-0,9 | 20-150 | 32,0 | |
Доз-м (одновалковая) | d – 0,9 м l – 0,9 | 60-80 | 6,3 | |
Роторные | ||||
СМД 85 | 400900/30900 | 55,0 | | 40,0 |
СМД 87 | 1100900/30900 | 370,0 | | 250,0 |
СМД-75; 94 - нереверсивные | | | | |
Молотковые | ||||
ДМРЭ-10-10 | | до 200,0 | | |
ДМРИЭ 15-15 | | до 800,0 | | |
ДМРИЭ 1,41,3 | | 250,0 | | |
Мельницы стержневые | ||||
МСЦ - (d)900 (l)1800 | | | | |
МСЦ - 45006000 | | | | |
МСЦ 21003000 | | | | |
МСП 21003000 | | | | |
МСП 27003600 | | | | |
Мельницы шаровые | ||||
МШЦ 9001800 | | | | |
МШЦ85008500 | | | | |
Ш12;Ш25;Ш50А | d – 3,7 м l – 8,5 | 50,0 | Масса шаров 100 т | n-17.62 об/мин |
Продолжение таблицы 4.2
Условные обозначения | Размеры общие/щели | Производительность,т/ч | Вес,т | Мощность, кВт |
Каскад | ||||
ММС-1500400 | | | | |
ММС-100005000 | | | | |
Аэрофол | ||||
МСС 57001850 | | | | |
Все шире применяются мельницы рудного самоизмельчения. Куски руды крупностью до 250-300 мм в барабане диаметром 2-10 м, вращающемся со скоростью 2,5-6 м/с, под действием центробежных сил и с помощью специальных лифтеров поднимаются на определенную высоту и, падая вниз, дробят и измельчают руду. Измельченный материал воздушным потоком выносится из барабана и улавливается в приемных камерах.
Ведется разработка и опробование струйных мельниц, в которых самоизмельчение руд достигается при соударении частиц в момент встречи двух движущихся со скоростями 100-150 м/с потоков.
В настоящее время для измельчения применяют мельницы самоизмельчения – «Каскад», «Аэрофол».
В технических схемах дробление и измельчение почти всегда комбинируется с сортировкой и классификацией материалов.
Любая дробилка или мельница должна удовлетворять следующим основным требованиям:
-
быть простой по устройству и механически прочной; -
обеспечивать заданную производительность; -
потреблять минимум энергии; -
полностью принимать сырье, подлежащее дроблению; -
свободно разгружать продукты дробления; -
не давать много пыли.
Эффективность работы дробилок и мельниц оценивается производительностью в т/кВтч или м3/кВтч.
Средние нормы расхода мощности на 1 м3/ч дробленого материала (для щековых дробилок)
для дробилок крупного размола – 0,37-0,74 кВт
среднего – 0,74-1,1
малого – 1,1-2,2
Дробилки и мельницы производят машиностроительные заводы: им. Котлякова (г. Одесса), Выксунский (г. Выкса), Южуралмашзавод (г. Орск), Уралмашзавод (г. Екатеринобург), Электросталь, Строймашина (г. Электросталь), Ясиноватский.
Украина имеет развитую горно-рудную, металлургическую, строительную и химическую промышленность, которые используют большое количество дробильно-измельчительной техники. Износ оборудования, реконструкция и создание новых предприятий требуют постоянного возобновления дробильно-измельчительной техники с широким диапазоном технологических показателей.
Основные разработчики и производители дробильного оборудования сосредоточены в России. В этих условиях создание новых машин у нас является актуальным.
Эффективность машин дробления и измельчения зависит от способа передачи энергии дробильному материалу. Наиболее благоприятными являются условия, при которых частицам сообщается энергия, уровень которой достаточный для разрушения и при этом не происходит ее рассеивание в слое. Следовательно, в процессе дробления необходимо непрерывно выводить готовые по размеру частицы из рабочей зоны. Такой процесс реализуется в установках самоизмельчения, у которых энергия передается слою материала с двух противоположных сторон. При этом частицы сталкиваются и разрушаются. Готовые по размеру частицы эвакуируются из зоны разрушения под действием центробежных сил через подвижные щели, образованные рабочими органами и корпусом рабочей камеры.
Учитывая большие успехи ДонГТУ в области разработки оборудования для контроля химического состава сырья и дробления, и измельчения в частности, правительство Украины открыло при ДонГТУ научно-исследовательский институт «Параметр»
НИИПКИ «Параметр» разработал ряд машин, предназначенных для среднего и мелкого измельчения.
-
Роторно-ударная дробилка (РУД) – для среднего и мелкого дробления. -
Установка самоизмельчения (УС-1) – для среднего и мелкого дробления (рис. 4.9). -
Установка пробоприготовления (БИП-1; БИП-2; УП-1) предназначена для выполнения в автоматическом или ручном режиме всех операций пробоприготовления по рекомендациям стандарта. Помол: железная руда, известняк, агломерат – содержание класса менее 0,07 мм более 95%, до 60-70% классов не менее 0,05 мм.
Дробилку можно использовать в режиме среднего и мелкого дробления. Крупность готового продукта 15 мм и менее с содержанием 30-40% фракции менее 1 мм. Крупность готового продукта 6-7 мм и менее с содержанием 30-60% фракции менее 1 мм. Принципиально в замкнутом цикле можно получать 100% фракции менее 1 мм. Главными отличительными свойствами являются низкая металлоемкость (в 5-6 раз в сравнении с конусными дробилками), простота конструкции и низкая энергоемкость.
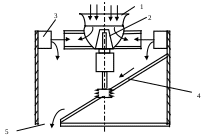