Файл: Сырьевая база и подготовка материалов к металлургическому переделу.doc
ВУЗ: Не указан
Категория: Не указан
Дисциплина: Не указана
Добавлен: 17.03.2024
Просмотров: 369
Скачиваний: 0
СОДЕРЖАНИЕ
3.1 Разжижители и шлакообразующие материалы.................................93
4.1 Цель и методы подготовки шихты.....................................................99
6.2 Обезвоживание концентратов.........................................................156
6.3 Обжиг железных руд........................................................................157
8.2 Производство кокса...........................................................................174
8.10 Качество металлургического кокса................................................202
3.1 Разжижители и шлакообразующие материалы
Шлакообразующие смеси и брикеты
4.1 Цель и методы подготовки шихты
Таблица 6.1 – Сравнительные характеристики различных сепараторов
6.2 Обезвоживание концентратов
ПОНЯТИЯ ОДНОРОДНОСТИ И УСРЕДНЕННОСТИ
Рисунок 7.1 – Усреднительный склад
Рисунок 7.2 – Устройство саморазгружающейся тележки
Таблица 8.2 – Структура запасов углей Донбасса
Таблица 8.8 – Коксуемость углей Донецкого бассейна
Рисунок 8.4 – Схема процесса коксования шихты в камере коксовой печи
Рисунок 8.5 – Поперечный разрез коксовой батареи
8.10 Качество металлургического кокса
Рисунок 8.7 – Барабаны для механического испытания кокса
Таблица 8.11 – Ситовый состав некоторых коксов
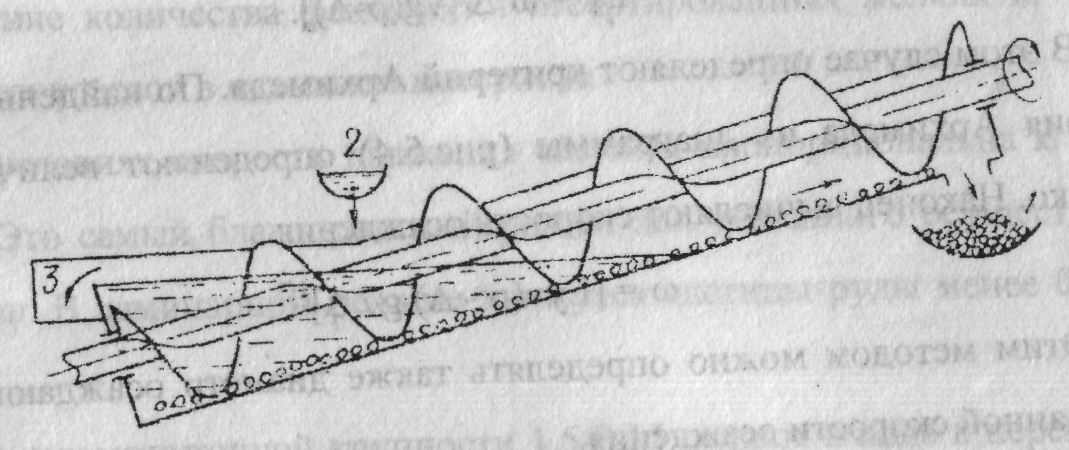
1 – пески; 2 – пульпа; 3 – слив
Рисунок 5.8 – Спиральный классификатор
Камерный классификатор (рис.5.9) состоит из нескольких (3-10) камер пирамидальной формы, в которых осаждаются крупные частички с постепенным уменьшением их размеров (от 3 до 0,2 мм).
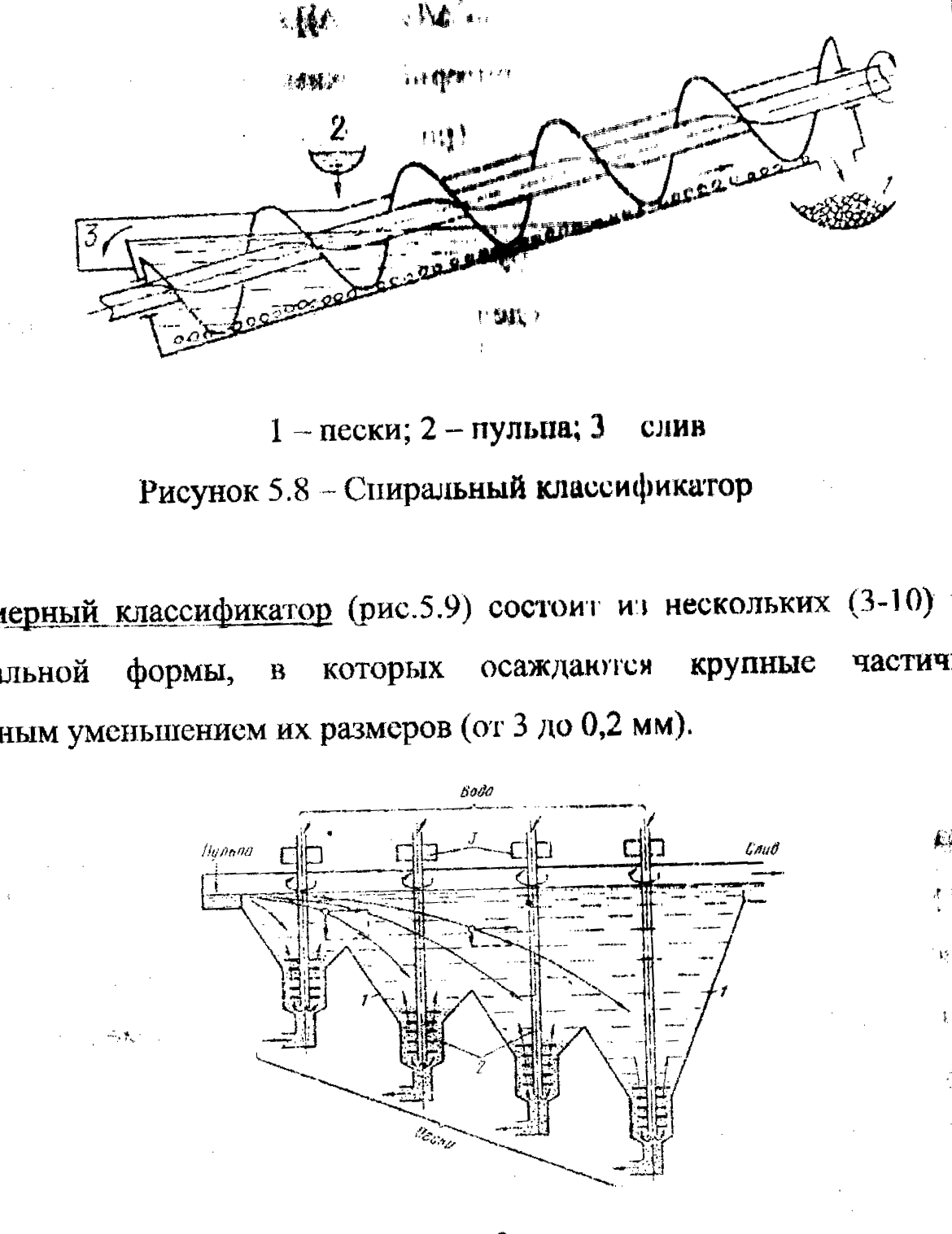
1 – камера; 2 – мешалки; 3 – привод мешалки
Рисунок 5.9 – Камерный классификатор
Уплотнению слоя осевших частиц препятствуют вращающиеся мешалки; восходящие потоки воды, подаваемой в каждую камеру через пустотелые оси мешалок, улучшают качество классификации.
Гидроциклоны используются для разделения наиболее мелких частиц материала. В результате подвода питания по касательной к корпусу (рис.5.10) поток пульпы приобретает вращательное движение.
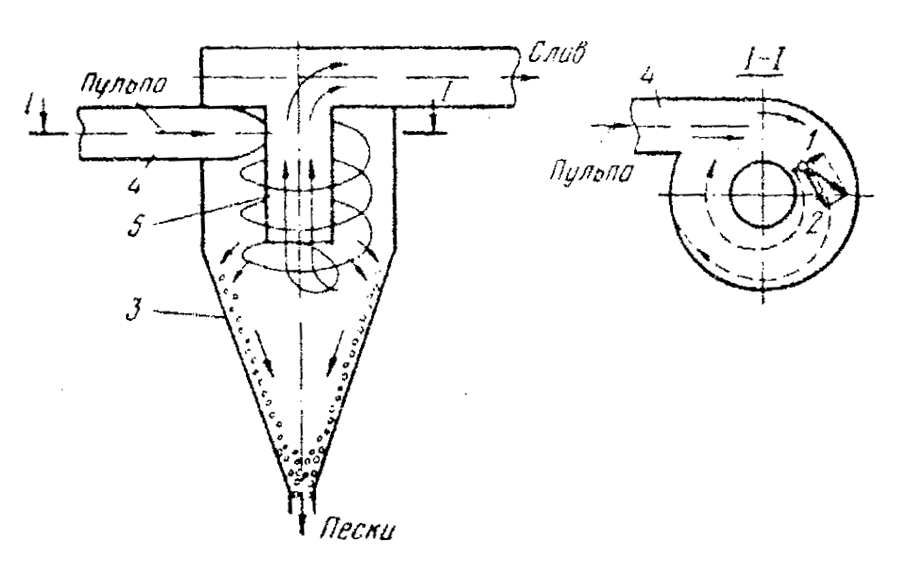
1 – центробежная сила; 2 – сила инерции; 3 – корпус; 4 – пульпопровод; 5 – центральный отводящий патрубок
Рисунок 5.10 – Схема гидроциклона
В результате вращения появляется центробежная сила mv2o/R, перпендикулярная направлению движения потока. Под действием этой силы и происходит выделение крупных частичек, траектория движения которых представляют раскручивающуюся спираль. Чем крупнее частички, тем больше центробежной силе они подвергаются, тем быстрее достигают стенок циклона, после чего частички тормозятся, спускаются вниз и удаляются через специальный затвор. Поток жидкости, содержащий во взвешенном состоянии мелкие частички, примерно на середине циклона поворачивается вверх и выходит из него через центральный патрубок. Повышая скорость движения потока и снижая радиус циклона, удается достигать высоких значений центробежного ускорения, во много раз превышающего ускорение силы тяжести. Благодаря этому интенсифицируется процесс выделения крупных частиц при одновременном уменьшении размеров аппарата.
6 ОБОГАЩЕНИЕ
Обогащением руд называется операция, увеличивающая содержание железа (марганца или любого другого элемента), или снижающая содержание вредных примесей в руде за счет удаления максимально возможного количества пустой породы. Обогащение позволяет существенно повысить содержание железа в шихте доменных печей, улучшить условия восстановления железа, уменьшить выход шлака, улучшая тем самым ход печи и снижая расход кокса при возрастающей производительности.
Установлено, что в средних условиях плавки повышение содержания железа в шихте на 1 % позволяет увеличить производительность печи на 2-2,5% при снижении удельного расхода кокса на 2-2,5 %.
В настоящее время в Украине подвергается обогащению 90-95 % всей добываемой руды. Получаемые на обогатительных фабриках концентраты содержат до 65-68 % железа.
В процессе обогащения исходная (сырая) руда разделяется на концентрат – продукт с максимально возможным для определенных условий обогащения содержанием железа, и хвосты – материал, не
содержащий железа или содержащий минимальное его количество. Иногда в ходе обогащения присутствует циркулирующая нагрузка – промежуточный продукт.
Количественно-качественная характеристика руд и флюсов в результате обогащения изменяется по следующим закономерностям, вытекающим из постоянства баланса металлов, (%)
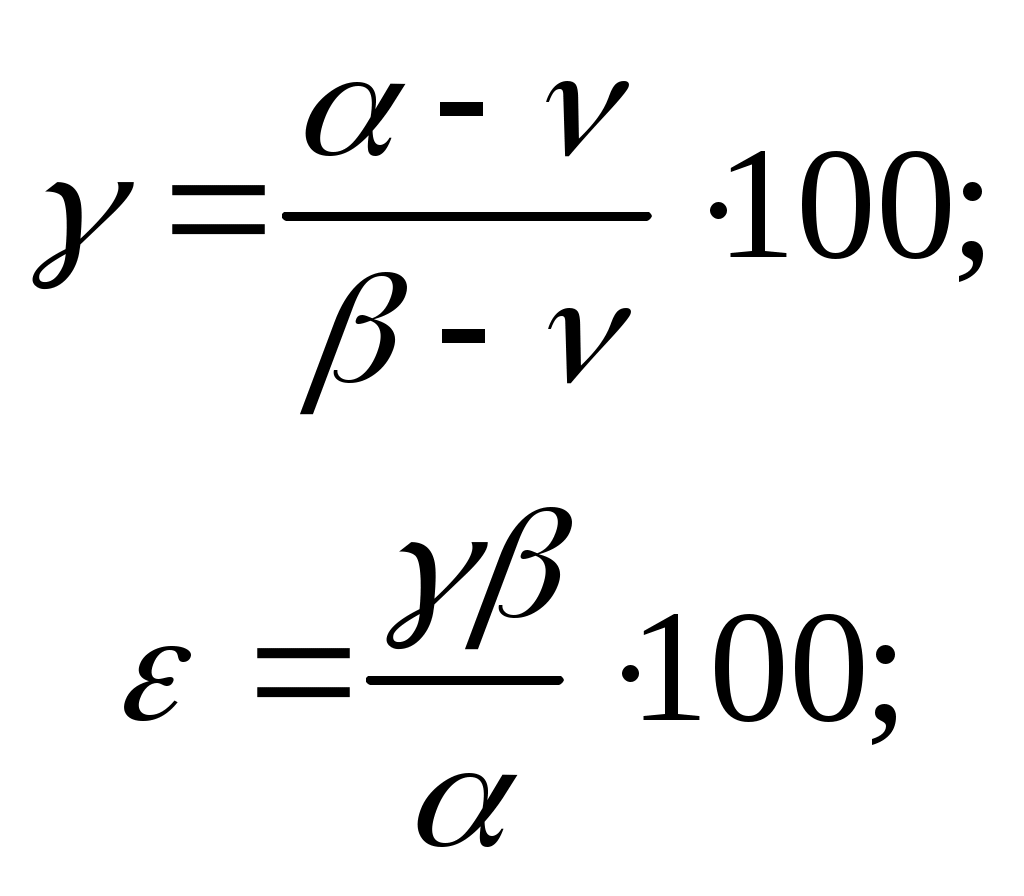
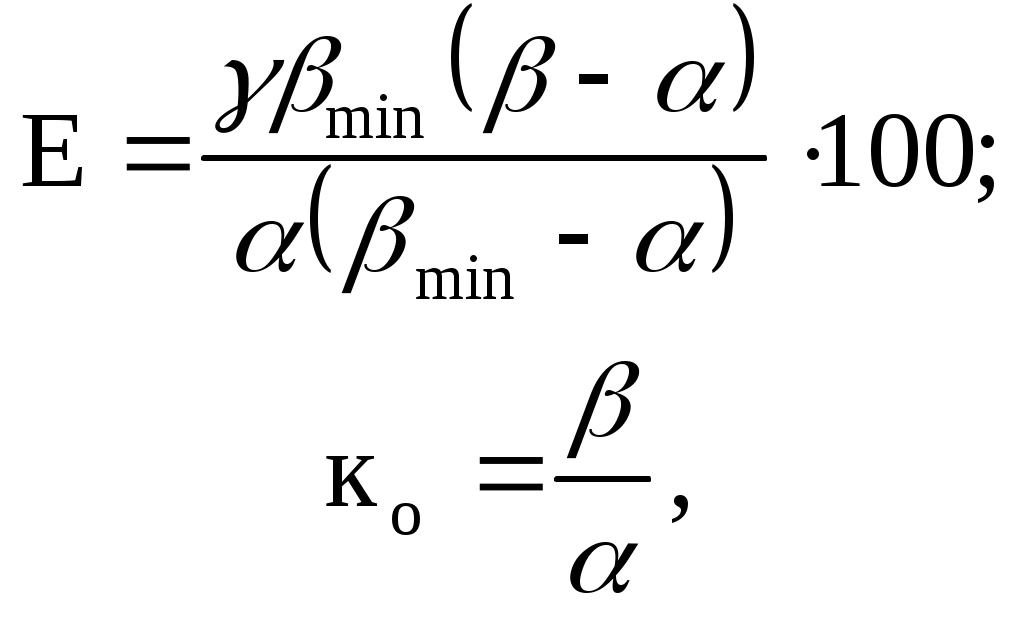
где – выход концентрата, %;
– содержание полезного компонента соответственно в исходной руде, в концентрате и хвостах;
– степень извлечения полезных компонентов в концентрат;
Е – эффективность обогащения;
– содержание полезного элемента в минерале;
ко – коэффициент обогащения, показывающий во сколько раз содержание железа в концентрате больше, чем в исходной руде.
При обогащении Криворожских руд с получением концентрата, содержащего 64-66 % железа, = 0,35-45; = 0,75-0,9; Е = 0,52-0,7; ко = 1,6-1,8.
Содержание полезных компонентов в рудах и флюсах при обогащении повышается до уровня, обеспечивающего минимальные затраты на производство чугуна. Такая глубина обогащения является оптимальной.
Для обогащения железных руд применяют преимущественно магнитные, гравитационные и флотационные методы обогащения. Они базируются на физико-химических свойствах рудных и нерудных минералов, в первую очередь учитываются магнитная восприимчивость, плотность и смачиваемость.
Плотность различных минералов (т/м3)
Магнетит - 4,9-5,2 Мартит – 4,8-5,3
Гематит – 4,9-5,3 Сидерит – 3,7-3,9
Магнезит 2,9-3,1 Кальцит – 2,6-2,8
Кварц – 2,65
Относительно простым методом обогащения, дающим вполне удовлетворительные результаты для руд с песчаной и глинистой пустой породой, является промывка. Обогащению промывкой подвергаются обычно бурые железняки, мартиты, ряд марганцевых руд, а иногда известняки. Промывку руд производят в скрубберах, корытных наклонных мойках, бичевых промывочных машинах, вибрационных мойках, бутарах.
Наиболее распространенными машинами являются бутары – вращающиеся барабанные грохоты цилиндрической, конической или пирамидальной формы с перфорированной поверхностью. Отличие их от обычных барабанных грохотов состоит в том, что внутрь бутары подается вода (5-6 т/т руды), под действием которой происходит размывание пустой породы и ее удаление через отверстия в боковой поверхности барабана. Крупные куски промытой руды удаляются через разгрузочный конец. Вследствие невысокой эффективности обогащения (содержание железа увеличивается на 2-6 %), промывка является обычно подготовительным этапом перед более совершенными методами обогащения.
Гравитационные методы обогащения основаны на различии плотности минералов пустой породы и железосодержащих минералов (плотность которых почти в два раза больше).
К статическим методам гравитационного обогащения относят обогащение в тяжелых суспензиях. Принцип этого способа заключается в том, что раздробленная до необходимой крупности руда помещается в жидкость, плотность которой имеет промежуточное значение между плотностью оксида железа и плотностью пустой породы. В такой жидкости более легкая пустая порода всплывает, а более тяжелые оксиды железа тонут. В качестве такой жидкости с плотностью около 3 г/см3 используют суспензию – взвесь тяжелого тонкоизмельченного материала в воде. В качестве суспензаторов применяют ферросилиций (6,5-6,8 г/см3), магнетит крупностью до 0,15 мм (4,6-5,2 г/см3), окалину (5,0-5,4 г/см3), гематит (4,9-5,3 г/см3).
К недостаткам обогащения в тяжелых суспензиях относят большие потери суспензатора (0,4-0,5 кг/т руды), нестабильность суспензии и невозможность обогащения мелких руд крупностью до 3 мм. Поэтому этот способ широкого распространения не нашел.
Суспензионные сепараторы бывают конусными, барабанными (для крупных руд), гидроциклонными и вихревыми гидроциклонными (для мелких руд).
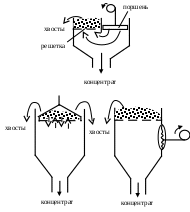
Рисунок 6.1 – Схемы отсадочных машин
Динамические методы гравитационного обогащения, как и классификация, основаны на различии скоростей движения в жидкости твердых частиц различной массы. Для успешного обогащения необходимо, чтобы измельченная руда была разделена на ряд фракций с определенным соотношением максимальных и минимальных частичек в каждой (крупностью от 3 до 35 мм). Широкое распространение получили методы гравитационного обогащения на сотрясательных столах и отсадкой.
При обогащении отсадкой слой руды, расположенный на решетке, пронизывается выходящим потоком воды, скорость которого должна быть больше скорости падения частиц. Через некоторое время происходит расслоение руды: внизу сосредоточиваются тяжелые (богатые железом) частички, а вверху - легкие (хвосты). Наиболее распространенным типом отсадочных машин является диафрагмовая машина с неподвижным решетом.
Обогащение на сотрясательных столах происходит за счет различной кинетической энергии частиц различной плотности.
На наклонную поверхность стола размерами – шириной 1,5- 2,5 м, длиной 4-6 м, покрытую волнистой резиной, с боку поступает руда. За счет возвратно-поступательного движения стола происходит перераспределение материала по плотности (содержанию железа).
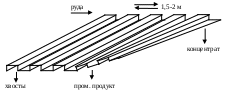
Рисунок 6.2 – Схема работы сотрясательных столов
Гравитационными способами обогащаются немагнитные или слабомагнитные руды крупностью 2-6 мм.
Обогащение методом флотации основано на различии в поверхностных свойствах. В частности способности смачиваться жидкостью зерен полезных минералов и частиц пустой породы.
М
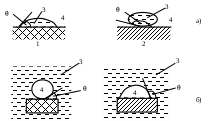
Рисунок 6.3 – Схема взаимодействия гидрофильных (1) и гидрофобных (2) материалов с водой (3) и
воздухом (4)
Количественно мера смачиваемости может характеризоваться величиной краевого угла – угла, образованного плоской поверхностью твердой фазы и плоскостью, касательной к поверхности жидкости на границе существования всех трех фаз. К гидрофильным принято относить такие материалы, для которых 90о; для гидрофобных материалов 90о. Способность тел смачиваться водой определяется в первую очередь природой материала или точнее – типом кристаллической решетки минерала.
Принципиально процесс флотации – разделение хорошо и плохо смачиваемых жидкостью частиц – осуществляется следующим образом. В емкость с водой, через которую непрерывно пропускают мелкие пузырьки воздуха, загружают дробленную руду. Во время осаждения частички руды сталкиваются с поднимающимися пузырьками воздуха. В соответствии с характером взаимодействия фаз (см. рис. 6.3, б) воздушные пузырьки «прилипают» к гидрофобным частичками и поднимают их на поверхность жидкости. Частички же, хорошо смачиваемые водой, не взаимодействуют с пузырьками воздуха и осаждаются на дно бака-сепаратора.
С целью усиления различия смачиваемости отдельных минералов и для улучшения других условий процесса обогащения флотацией производят не в чистой воде, а в воде со специальными веществами-реагентами.
В качестве флотационных реагентов применяют галловые, олеиновые или ветлужное масло, остатки жирных кислот, окисленный керосин и др.
Флотационная механическая машина (рис. 6.4) представляет собой камеру 1 объемом 2 м3. При вращении импеллера 2 происходит интенсивное перемешивание в жидкости минеральных частичек и пузырьков воздуха; кроме того, в зоне вращения мешалки создается разрежение, под действием которого в машину засасываются воздух 3 и пульпа 4. Разделение минералов руды происходит в средней части камеры, где гидрофобные частички соединяются с пузырьками воздуха и поднимаются вверх. Минерализованная пена вращающимися лопастями 5 перебрасывается через сливную перегородку в желоб. Осевшие частички удаляются из машины через отверстие в стенке камеры 6.
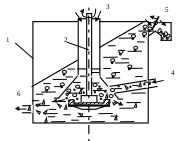
Рисунок 6.4 – Схема флотационной машины с механическим перемешиванием
Как видно из рассмотренного, удаление пустой породы из руд и получение концентратов глубокого обогащения (с высоким содержанием железа) требует применения разнообразных устройств (дробилок, мельниц, грохотов, классификаторов, обогатительных установок, устройств для обезвоживания) и значительного расхода энергии на эти процессы. Схемы современных дробильно-обогатительных фабрик весьма сложны и определяются в основном свойствами перерабатываемой конкретной руды.