Файл: Отчет по учебной практике уп. 04 Учебная практика пм. 04 Выполнение работ по профессии слесарьремонтник.docx
Добавлен: 18.03.2024
Просмотров: 99
Скачиваний: 6
ВНИМАНИЕ! Если данный файл нарушает Ваши авторские права, то обязательно сообщите нам.
операций по нарезанию резьбы бывают цельными, раздвижными, круглыми и разрезными. Кроме того, резьба может нарезаться квадратными, призматическими или шестигранными плашками. Наиболее универсальны устанавливаемые в клуппах раздвижные инструменты, а разрезные и цельные не дают высокой точности резьбы. Изготавливаются инструменты из закаленной или другой специальной стали. При этом процесс нарезания резьбы и его качество во многом зависят от геометрии лезвий плашек. В процессе работы материал винта выдавливается наружу, следовательно, чтобы не произошло повреждение плашки, необходимо, чтобы стержень имел диаметр меньше наружного диаметра резьбы. Обычно при таких операциях, как нарезание резьбы, применяемая мастером плашка устанавливается в специально предназначенный для этого держатель. 10. Притирка Опиливания, зачистки и шабрения поверхностей зачастую бывает недостаточно, чтобы достигнуть достаточно плотного прилегания деталей друг к другу. Поэтому в процессе сборки механизмов слесари прибегают к притирке (доводке) поверхностей с использованием абразивных порошков и паст. В процессе притирки деталям сообщается наиболее точный размер за счет снятия очень малого припуска (около 0,05 мм). Притиркой можно достичь такого плотного прилегания поверхностей, что соединение будет гидронепроницаемым. Сразу стоит оговориться, что далее речь пойдет о ручной притирке, ибо вряд ли домашняя мастерская может быть оснащена специальными механическими притирочными станками. Притирку можно производить двумя способами: одной деталью о другую (так притирают в основном криволинейные прилегающие друг к другу поверхности - клапаны, пробки и пр.) или деталью о притир (так доводят фланцы, крышки и пр.). В качестве притиров используются плиты, бруски или другие детали, сделанные из более мягкого материала, чем сами притираемые элементы (например, для притирки стальных деталей используются чугунные притиры, для притирки деталей из цветных металлов - стеклянные притиры). Притирка, подобно шабрению, осуществляется в два этапа: предварительная притирка (предназначенные для этого притиры имеют на своей поверхности канавки, куда собирается металлическая стружка) и окончательная - доводка (она производится притирами с гладкой поверхностью). В качестве притирочных порошков используются: корундовый, карборундовый, наждачный порошки, окись железа, алюминия, хрома, толченое стекло. Зернистость абразивных порошков - от М40 до М7. В качестве смазки применяются олеиновая кислота, машинное масло, керосин, скипидар, техническое сало. При доводке вместо абразивных порошков используются пасты, в частности паста ГОИ. Нанесение притирочных порошков на притиры (или на поверхности деталей, если притирка осуществляется одной деталью о другую) называется шаржированием и осуществляется двумя способами: во-первых, абразивный порошок можно вдавить в притир стальным закаленным валиком, после чего лишний порошок удалить, а поверхность притира смазать; во-вторых, притир можно смазать и уже поверх смазки насыпать абразивный порошок и вдавить его валиком. Притирочная паста наносится на поверхность притира тонким слоем без вдавливания. Перед шаржированием поверхность притира предварительно промывают керосином и начисто протирают. По плоскому притиру с легким нажимом прокатывают стальной закаленный валик (рис. 37, в). Если шаржируется круглый притир, то притирочную массу наносят на две стальные закаленные плиты и притир прокатывают между ними (рис. 37, г). После шаржирования, когда абразивные зерна вдавлены в поверхность притира, избыточную притирочную массу убирают.
Р
ис. 37. Притиры и шаржирование притиров: а - плоский притир с канавками; б - плоский притир без канавок; в - шаржирование плоского притира; г - шаржирование круглого притира: 1 - нижняя стальная закаленная плита; 2 - притир; 3 - верхняя стальная закаленная плита.
Притирка плоских поверхностей происходит следующим образом: деталь обрабатываемой стороной накладывают на подготовленную плоскость притира (или другой притираемой детали) и производят 20-30 сложных кругообразных движений с сильным нажимом. Траектория движений должна быть действительно сложной (даже можно сказать - хаотичной), чтобы они не накладывались друг на друга. Скорость движений должна быть приблизительно 20 м/мин (рис. 38).
Р
ис. 38. Притирка плоских поверхностей: а - предварительная; б - окончательная.
Затем отработанную притирочную массу убирают с поверхности притира и детали и наносят новый слой (зернистость используемого порошка на этот раз должна быть меньше). Таким образом чередуют притирочные движения с заменой притирочного слоя до получения соответствующего вида изделия (при последних подходах абразивный порошок заменяют пастой: сначала грубой, затем средней и в последнюю очередь тонкой. Окончательную притирку (доводку) осуществляют без нанесения пасты, а лишь со смазыванием притира смесью керосина и машинного масла. Если заготовка очень тонкая в сечении и ее неудобно двигать по притиру, то ее закрепляют на деревянном бруске и перемещают по плите вместе с ним. Притирка узких граней деталей или мелких заготовок производится пакетом. Несколько заготовок с помощью струбцин соединяют в пакет и притирают как широкую поверхность. Для этой цели можно использовать стальные или чугунные направляющие бруски или призмы. Притирка криволинейных поверхностей имеет свои особенности. Чаще всего криволинейные поверхности двух деталей взаимосоприкасаемы, при этом одна из поверхностей выпуклая, а другая вогнутая (например, пробка и гнездо под нее, вместе составляющие самоварный краник), поэтому притирку этих поверхностей производят одна об другую. Пробку смазывают и присыпают абразивным порошком, вставляют в гнездо и вращают попеременно в разные стороны приблизительно на 1/4 оборота 5-6 раз, после чего делают полный оборот пробки вокруг ее оси. Чередование притирки с заменой притирающих материалов аналогично притиранию широких плоских поверхностей. Проверку точности притирки можно осуществить с помощью грифельного карандаша: наносят линию на одну из притертых поверхностей и проводят ею по другой притертой поверхности. При удовлетворительном качестве притирки карандашная линия равномерно стирается или смазывается по всей длине. В завершение операции притирки (доводки) детали при необходимости обрабатывают полировальниками - эластичными кругами из фетра или войлока. В качестве механического привода полировальника может выступать двигатель от бормашины или электрическая дрель. Полировку производят очень тонкими абразивными порошками со связкой из вазелина, говяжьего сала, воска или полировальными пастами. Механическая обработка металлов 11. Токарные работы Токарная обработка (точение) - наиболее распространенный метод изготовления деталей типа тел вращения (валов, дисков, осей, пальцев, цапф, фланцев, колец, втулок, гаек, муфт и др.) на токарных станках. На них можно производить обтачивание и растачивание цилиндрических, конических, шаровых и профильных поверхностей этих деталей, подрезание торцов, вытачивание канавок, нарезание наружных и внутренних резьб, накатывание рифлений, сверление, зенкерование, развертывание отверстий и другие виды токарных работ. Снятие стружки с поверхности вращающейся заготовки осуществляется режущим инструментом, основным элементом которого является клин, заостренный под углом. Вращательное движение заготовки называют главным движением резания, а поступательное движение режущего инструмента - движением подачи. Различают также вспомогательные движения, которые не имеют непосредственного отношения к процессу резания, но обеспечивают транспортирование и закрепление заготовки на станке, его включение и изменение частоты вращения заготовки или скорости поступательного движения инструмента и др. Для обработки заготовки необходимо установить наиболее рациональные режимы резания, т.е. скорость резания, подачу и глубину резания. Скоростью резания и (м/с или м/мин) называют путь режущей кромки инструмента относительно обрабатываемой заготовки в направлении главного движения за единицу времени. Подачей S (мм/об) называют путь, пройденный режущей кромкой инструмента относительно вращающейся заготовки в направлении движения подачи за один оборот заготовки. Подача может быть продольной, если инструмент перемещается параллельно оси вращения заготовки, и поперечной, если инструмент перемещается перпендикулярно этой оси. 12. Фрезерные работы Фрезерование (фрезерная обработка) - обработка материалов резанием с помощью фрезы. Фреза совершает вращательное, а заготовка - преимущественно поступательное движение, как правило в направлении перпендикулярном оси вращения фрезы. Фрезеровать заготовки можно при установке на столе одной заготовки или группы заготовок (множественная обработка). Кроме того, применяют позиционное фрезерование, непрерывное фрезерование, фрезерование набором фрез, одновременную обработку заготовок несколькими фрезами. Фрезерование одной заготовки применяется главным образом в единичном производстве или при обработке крупногабаритных заготовок. Фрезерование нескольких заготовок обеспечивает сокращение как машинного, так и вспомогательного времени. Различают две разновидности множественного фрезерования: последовательное и параллельное (рядами). При последовательном фрезеровании одной фрезой или набором фрез обрабатывают заготовки, установленные в один ряд (в направлении перемещения стола. При параллельном методе заготовки, установленные в два или несколько параллельных рядов, обрабатывают одновременно одной фрезой или набором фрез. Позиционное фрезерование является одним из прогрессивных методов обработки. Существуют два вида позиционного фрезерования: фрезерование с применением специальных или универсальных поворотных столов и маятниковое фрезерование с подачей в обе стороны, не требующие применения поворотных приспособлений. На столе фрезерного станка устанавливают поворотный стол с двумя одинаковыми приспособлениями для закрепления заготовок. В то время как в приспособлении заготовку фрезеруют, в приспособлении устанавливают следующую заготовку. При этом способе большая часть вспомогательного времени на установку заготовки и снятие обработанной детали совмещается с машинным временем. 13. Строгальные работы Строгальная операция эффективно применяется для снятия припуска и придания металлическим заготовкам необходимой формы, заданной гладкости и точности поверхностей. Суть процесса состоит в снятии стружки различной толщины с поверхности металлической заготовки специальными резцами. Обработке подлежат плоскости различного расположения (вертикальные, горизонтальные, параллельные, перпендикулярные, наклонные), а также криволинейные поверхности сложных геометрических форм, фасонные поверхности. Строганием также можно выполнять различные пазы и канавки. Оборудование для выполнения строгальной операции Строгальная операция выполняется на станках строгальной группы, которые классифицируются в соответствии с технологическими особенностями, характером работы и компоновкой. Для некоторых строгальных операций
используются специализированные станки, ориентированные на конкретные задачи. Конечно же, самыми распространенными считаются станки универсальной группы - на них можно выполнять практически все строгальные операции. Группа универсальных станков представлена поперечно-строгальными и продольными станками. Их технические характеристики адаптированы под обработку крупногабаритных или небольших заготовок. Заготовка закрепляется неподвижно на столе, а гидравлическая или механическая передача приводит стол в возвратно-поступательное движение. Резец, обрабатывающий плоскость снятием стружки, остается неподвижным. По качеству и точности получаемой поверхности, а также экономичности процесса продольно-строгальная обработка опережает фрезерование. Причем продольно-строгальная операция применима для некоторых задач, которые фрезерованием выполнить невозможно или невыгодно. Особенно экономичным оказывается выполнение единичных или небольших партий заказов. Ведь переналадка станка и установка заготовки не требует много времени и сил. Поверхности заготовок средних размеров и мелкие обрабатываются на поперечно-строгальных станках, где главное возвратно-поступательное движение совершает резец. Стол с закрепленной на нем заготовкой двигается в поперечном направлении горизонтально и вертикально. Вертикальные и наклонные плоскости обрабатываются при неподвижном столе. Привод, как и у продольно-строгальных станков механический или гидравлический (более точный). Поперечно-строгальная операция может использоваться не только для снятия стружки с наклонных, горизонтальных или вертикальных плоских и фасонных поверхностей, но и для вырезания канавок, уступов, пазов или выемок.
14. Шлифовальные работы слесарный металл токарный фрезерный
Шлифовка — это процесс окончательной обработки деталей путём снятия с них тонкого слоя материала вращающимся абразивным элементом. Шлифовальные работы позволяют добиться высокой точности обработки металла, снимая слои материала с крайне высокой точностью. Как правило операция шлифовки детали является окончательной в технологическом процессе механообработки деталей.
Шлифовальные станки классифицируют по принципу действия и расположению детали. Различают круглошлифовальный, плоскошлифовальный, бесцентрошлифовальный и внутришлифовальный и др. виды станков. Станки шлифовальной группы современных моделей предназначены для изготовления деталей с малыми отклонениями формы, размеров, малыми параметрами шероховатости поверхности и отличаются высокой производительностью. При шлифовании главным движением резания является движения инструмента. Различают шлифование периферией абразивного круга и торцом круга, в первом случае режущей частью является наружная поверхность круга, а во втором случае - торец круга. В зависимости от расположения и формы обрабатываемой заготовки шлифование подразделяют на следующие виды: • Наружное шлифование, когда обрабатывается наружная поверхность заготовки, • Внутреннее шлифование, когда обрабатывается внутренняя поверхность заготовки, • Плоское шлифование, когда обрабатывается плоская поверхность, • Профильное шлифование, когда обрабатывается поверхность, образующая которой представляет кривую или ломаную линию. Тепловая практика 15. Медницко-жестянные работы Обработка жести составляет предмет нескольких ремесел. Жестянщики обычно занимаются и лужением, и часто соединяют свое мастерство с лакировальным, чтобы выпускать изделия в окончательно отделанном виде. Главным инструментом для жестянщика служит молоток, стальной или деревянный, которым работают на стальной наковальне соответственной формы или на деревянном чурбане. Удар стальным молотком по металлическому листу, лежащему на стальной наковальне, плющит и производит на плоском листе шишку, вогнутую со стороны удара, потому что нетронутые ударом части листа не дают материалу возможности раздаваться по сторонам. Удар же по свесившемуся с наковальни краю листа только сгибает его; при этом вогнутая сторона претерпевает сжатие, а выпуклая растягивается. Удар между деревом и сталью тоже не расплющивает металл, а, смотря по обстоятельствам, только сгибает его, растягивает или даже утолщает, "осаживает". Эти три процесса, обуславливающие все приемы для придания формы тонкому листовому металлу, удаются только на мягком, отожженном металле; когда от самой обработки он станет упругим, "крепким", приходится или отжечь работу, или приостановить дальнейшее изменение формы под опасением получить трещины. Поэтому-то белая жесть, которую нельзя отжигать, и железо для кровельной работы, которое отжигать неудобно, должны быть из особенно хорошего, мягкого сорта железа или стали. Медницкие работы: Обработка листового материала слесарными методами. Пайка легкоплавкими и тугоплавкими припоями: котлы, трубопроводы холодильных установок, и др. Чеканка и выколотка. Лужение изделий. Профессия жестянщика в современных условиях одна из ведущих в производстве фасонных частей (отводы, утки, переходы, тройники, крестовины и т. п.) воздуховодов для промышленной вентиляции и производстве монтажа систем промышленной вентиляции. Жестянщики работают на машиностроительных предприятиях по ремонту вентиляции, а также изготовляют различного рода ограждения к станкам, машинам и т. п. 16. Кузнечные работы Горячую обработку металла, т. е. обработку металла в нагретом состоянии, производят в тех случаях, когда под действием усилий нужно изменить форму металла без разрушения. Такая обработка металла в нагретом состоянии называется ковкой. При изготовлении санитарно-технических деталей ковку используют сравнительно мало, ее применяют лишь для изготовления ручного инструмента, средств крепления трубопроводов и нагревательных приборов, а также при выполнении ремонтных работ. Существует два основных метода ковки: свободная ковка и ковка штамповкой. Свободную ковку выполняют с помощью плоских бойков и вспомогательного инструмента, под действием ударов которых металл деформируется и свободно изменяет свои размеры. Свободную ковку можно выполнять на приводных молотах и вручную. Все основные кузнечные операции при свободной ковке заключаются в обработке нагретого металла ударами бабки молота или ручного инструмента для получения поковок или изделий определенной формы и требуемых размеров. Все кузнечные операции при ручной ковке выполняют на наковальне с применением следующих инструментов: гладилки, обжимок, кувалды, ручника, кузнечных зубил, пробойников и клещей. Протяжка - операция, при которой заготовка под действием ударов удлиняется и поперечное сечение ее уменьшается. Протяжку производят на гладкой стороне наковальни с помощью обжимки или на роге наковальни. Осадка - операция, при которой увеличивается поперечное сечение заготовки за счет уменьшения ее длины. Осадка называется полной, если увеличивается все сочен не за счет всей длины, и местной, если увеличивается сечение конца заготовки или середины ее. Местную осадку называют высадкой. При высадке нагревают ту, часть заготовки, которую нужно увеличить в поперечном сечении. Осадку производят ударами кувалды. Загиб - операция, при которой часть заготовки загибают под заданным углом к другой части заготовки. Загиб производят на наковальне, с которой загибаемая часть должна свешиваться так, чтобы вершина угла изгиба совмещалась с краем наковальни. Удары кувалдой наносят по свисающей части, удерживая
заготовку на наковальне клещами и ручником, а большую заготовку- клещами и другой кувалдой, которую держит еще один рабочий. Угол загиба проверяют по шаблону. При ковке необходимо выполнять следующие правила техники безопасности: работать в кожаных рукавицах и брезентовых костюмах; надевать кожаные фартуки и предохранительные очки; применять исправный инструмент; клещи должны соответствовать форме материала; плотно укладывать материал на наковальню; складывать горячие поковки в определенное место; не загромождать проходы в кузнице; осторожно заливать поковки, чтобы образовавшимся паром не обжечь руки и лицо; при осадке конца трубы противоположный конец ее закрывать пробкой. Термическая обработка металлов и сплавов изменяет физические свойства металлов. Заключается она в том, что металл или сплав нагревают до определенной температуры, выдерживают при заданной температуре, а затем подвергают охлаждению. В зависимости от температуры нагрева и режима охлаждения термическая обработка делится на следующие виды: отжиг, нормализация, закалка и отпуск. Металлы и металлические изделия на производстве нагревают в специальных термических печах, ваннах и в кузнечных горнах. Отжиг стали производят для уменьшения ее твердости, затрудняющей обработку. Отжиг приводит также к уничтожению внутренних напряжений, вызывающих при механической обработке появление трещин и коробление. В результате отжига улучшается структура стали, что способствует улучшению качества ее дальнейшей термической обработки. При отжиге сталь нагревают до 740-850° (чем больше углерода содержит сталь, тем ниже температура отжига). После некоторой выдержки при этой температуре сталь в течение многих часов охлаждают. Нормализация стали отличается от отжига более быстрым ее охлаждением на воздухе. В результате нормализации сталь приобретает более высокие механические свойства, чем после отжига. Закалка придает стали высокую твердость. При закалке сталь нагревается до той же температуры, что и при отжиге, выдерживается некоторое время при этой температуре, а затем быстро охлаждается опусканием в холодную или теплую воду, машинное масло, нефть, раствор поваренной соли и другие охлаждающие жидкости. В воде производят закалку инструментов, имеющих несложную форму и изготовленных из углеродистой инструментальной стали. В воде закаливают также изделия из углеродистой конструкционной стали. В горячей воде и в масле производят закалку пружин и других изделий, которые должны обладать высокой упругостью. Мягкие стали, содержащие мало углерода, не закаливаются, то есть не изменяют механических свойств при закалке. Конструкционные и инструментальные углеродистые стали значительно увеличивают при закалке свою твердость, но становятся при этом хрупкими и обладают невысокими 'Механическими свойствами. Отпуск закаленной стали позволяет уничтожить или значительно уменьшить ее хрупкость, иными словами, придать стали вязкость. Для отпуска детали сталь нагревают до температуры от 150 до 680° (чаще всего - 220-300°), выдерживают при этой температуре и охлаждают в воде или масле (скорость охлаждения при отпуске на структуре углеродистых сталей не сказывается). Ниже в таблице приведены температуры закалки и отпуска для некоторых инструментов, изготовленных из углеродистой инструментальной стали. 18. Сварочные работы: а) электросварочные работы Сваркой называется неразъемное соединение двух или более деталей, с помощью электрического тока присадочного материала (электрод). Широкое применение получила ручная дуговая сварка из-за своей простоты и доступности применения. Электрический ток для сварки вырабатывается сварочным трансформатором, который служит для преобразования высокого напряжения эл. сети (220в - 380в) в низкое напряжение вторичной эл. цепи. Кроме трансформатора для сварки металла требуется присадочный материал или электроды. Электроды состоят из металлического стержня, предназначенного для проведения эл.тока и формирования сварочного шва, и обмазки предназначенной для защиты шва от воздействий окружающей среды, стабильного горения дуги раскисления расплавленного металла сварочной ванны, легирование металла, для связывания составляющих покрытия и образования шлака, который должен обладать определёнными физико-химическими данными. Диаметр электрода выбирают в зависимости от толщины металла, катета шва, положения шва в пространстве. б) газосварочные работы Резаки для ручной резки служат для смешения горючего газа с кислородом, образования подогревающего пламени и подачи к разрезаемому металлу струи режущего кислорода. Ручные резаки для газовой резки классифицируются по следующим признакам: по роду горючего газа, на котором они работают: для ацетилена, газов-заменителей, жидких горючих; по принципу смешения горючего газа и кислорода на инжекторные и безинжекторные; по назначению - на универсальные и специальные; по виду резки для разделительной, поверхностной, кислородно-флюсовой, копьевой. В настоящее время широкое применение получили универсальные резаки. К универсальным резакам предъявляются следующие основные требования: возможность резки стали толщиной от 3 до 300 мм в любом направлении, устойчивость против обратных ударов, малая масса и удобство в обращении. Как и сварочные горелки, резаки имеют инжекторное устройство, обеспечивающее нормальную работу горючего газа в диапазоне давлений 0,03-1,5 кгс/см2. Инжекторный резак отличается от инжекторной горелки тем, что имеет отдельный канал для подачи режущего кислорода и специальную головку, которая включает в себя два сменных мундштука - внутренний и наружный. Источником теплоты является газовый факел, образующийся при сгорании смеси кислорода и горючего газа. В качестве горючего газа могут быть использованы: ацетилен, МАФ, пропан, бутан, блаугаз, водород, керосин, бензин, бензол и их смеси. Тепло, выделяющееся при горении смеси кислорода и горючего газа, расплавляет свариваемые поверхности и присадочный материал с образованием сварочной ванны. Пламя может быть окислительным, "нейтральным" или восстановительным.
Р
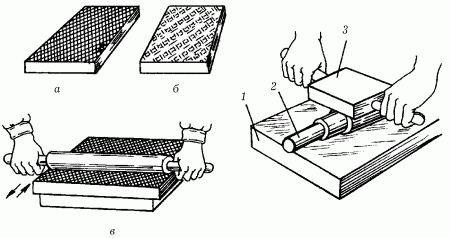
ис. 37. Притиры и шаржирование притиров: а - плоский притир с канавками; б - плоский притир без канавок; в - шаржирование плоского притира; г - шаржирование круглого притира: 1 - нижняя стальная закаленная плита; 2 - притир; 3 - верхняя стальная закаленная плита.
Притирка плоских поверхностей происходит следующим образом: деталь обрабатываемой стороной накладывают на подготовленную плоскость притира (или другой притираемой детали) и производят 20-30 сложных кругообразных движений с сильным нажимом. Траектория движений должна быть действительно сложной (даже можно сказать - хаотичной), чтобы они не накладывались друг на друга. Скорость движений должна быть приблизительно 20 м/мин (рис. 38).
Р
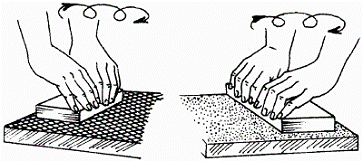
ис. 38. Притирка плоских поверхностей: а - предварительная; б - окончательная.
Затем отработанную притирочную массу убирают с поверхности притира и детали и наносят новый слой (зернистость используемого порошка на этот раз должна быть меньше). Таким образом чередуют притирочные движения с заменой притирочного слоя до получения соответствующего вида изделия (при последних подходах абразивный порошок заменяют пастой: сначала грубой, затем средней и в последнюю очередь тонкой. Окончательную притирку (доводку) осуществляют без нанесения пасты, а лишь со смазыванием притира смесью керосина и машинного масла. Если заготовка очень тонкая в сечении и ее неудобно двигать по притиру, то ее закрепляют на деревянном бруске и перемещают по плите вместе с ним. Притирка узких граней деталей или мелких заготовок производится пакетом. Несколько заготовок с помощью струбцин соединяют в пакет и притирают как широкую поверхность. Для этой цели можно использовать стальные или чугунные направляющие бруски или призмы. Притирка криволинейных поверхностей имеет свои особенности. Чаще всего криволинейные поверхности двух деталей взаимосоприкасаемы, при этом одна из поверхностей выпуклая, а другая вогнутая (например, пробка и гнездо под нее, вместе составляющие самоварный краник), поэтому притирку этих поверхностей производят одна об другую. Пробку смазывают и присыпают абразивным порошком, вставляют в гнездо и вращают попеременно в разные стороны приблизительно на 1/4 оборота 5-6 раз, после чего делают полный оборот пробки вокруг ее оси. Чередование притирки с заменой притирающих материалов аналогично притиранию широких плоских поверхностей. Проверку точности притирки можно осуществить с помощью грифельного карандаша: наносят линию на одну из притертых поверхностей и проводят ею по другой притертой поверхности. При удовлетворительном качестве притирки карандашная линия равномерно стирается или смазывается по всей длине. В завершение операции притирки (доводки) детали при необходимости обрабатывают полировальниками - эластичными кругами из фетра или войлока. В качестве механического привода полировальника может выступать двигатель от бормашины или электрическая дрель. Полировку производят очень тонкими абразивными порошками со связкой из вазелина, говяжьего сала, воска или полировальными пастами. Механическая обработка металлов 11. Токарные работы Токарная обработка (точение) - наиболее распространенный метод изготовления деталей типа тел вращения (валов, дисков, осей, пальцев, цапф, фланцев, колец, втулок, гаек, муфт и др.) на токарных станках. На них можно производить обтачивание и растачивание цилиндрических, конических, шаровых и профильных поверхностей этих деталей, подрезание торцов, вытачивание канавок, нарезание наружных и внутренних резьб, накатывание рифлений, сверление, зенкерование, развертывание отверстий и другие виды токарных работ. Снятие стружки с поверхности вращающейся заготовки осуществляется режущим инструментом, основным элементом которого является клин, заостренный под углом. Вращательное движение заготовки называют главным движением резания, а поступательное движение режущего инструмента - движением подачи. Различают также вспомогательные движения, которые не имеют непосредственного отношения к процессу резания, но обеспечивают транспортирование и закрепление заготовки на станке, его включение и изменение частоты вращения заготовки или скорости поступательного движения инструмента и др. Для обработки заготовки необходимо установить наиболее рациональные режимы резания, т.е. скорость резания, подачу и глубину резания. Скоростью резания и (м/с или м/мин) называют путь режущей кромки инструмента относительно обрабатываемой заготовки в направлении главного движения за единицу времени. Подачей S (мм/об) называют путь, пройденный режущей кромкой инструмента относительно вращающейся заготовки в направлении движения подачи за один оборот заготовки. Подача может быть продольной, если инструмент перемещается параллельно оси вращения заготовки, и поперечной, если инструмент перемещается перпендикулярно этой оси. 12. Фрезерные работы Фрезерование (фрезерная обработка) - обработка материалов резанием с помощью фрезы. Фреза совершает вращательное, а заготовка - преимущественно поступательное движение, как правило в направлении перпендикулярном оси вращения фрезы. Фрезеровать заготовки можно при установке на столе одной заготовки или группы заготовок (множественная обработка). Кроме того, применяют позиционное фрезерование, непрерывное фрезерование, фрезерование набором фрез, одновременную обработку заготовок несколькими фрезами. Фрезерование одной заготовки применяется главным образом в единичном производстве или при обработке крупногабаритных заготовок. Фрезерование нескольких заготовок обеспечивает сокращение как машинного, так и вспомогательного времени. Различают две разновидности множественного фрезерования: последовательное и параллельное (рядами). При последовательном фрезеровании одной фрезой или набором фрез обрабатывают заготовки, установленные в один ряд (в направлении перемещения стола. При параллельном методе заготовки, установленные в два или несколько параллельных рядов, обрабатывают одновременно одной фрезой или набором фрез. Позиционное фрезерование является одним из прогрессивных методов обработки. Существуют два вида позиционного фрезерования: фрезерование с применением специальных или универсальных поворотных столов и маятниковое фрезерование с подачей в обе стороны, не требующие применения поворотных приспособлений. На столе фрезерного станка устанавливают поворотный стол с двумя одинаковыми приспособлениями для закрепления заготовок. В то время как в приспособлении заготовку фрезеруют, в приспособлении устанавливают следующую заготовку. При этом способе большая часть вспомогательного времени на установку заготовки и снятие обработанной детали совмещается с машинным временем. 13. Строгальные работы Строгальная операция эффективно применяется для снятия припуска и придания металлическим заготовкам необходимой формы, заданной гладкости и точности поверхностей. Суть процесса состоит в снятии стружки различной толщины с поверхности металлической заготовки специальными резцами. Обработке подлежат плоскости различного расположения (вертикальные, горизонтальные, параллельные, перпендикулярные, наклонные), а также криволинейные поверхности сложных геометрических форм, фасонные поверхности. Строганием также можно выполнять различные пазы и канавки. Оборудование для выполнения строгальной операции Строгальная операция выполняется на станках строгальной группы, которые классифицируются в соответствии с технологическими особенностями, характером работы и компоновкой. Для некоторых строгальных операций
используются специализированные станки, ориентированные на конкретные задачи. Конечно же, самыми распространенными считаются станки универсальной группы - на них можно выполнять практически все строгальные операции. Группа универсальных станков представлена поперечно-строгальными и продольными станками. Их технические характеристики адаптированы под обработку крупногабаритных или небольших заготовок. Заготовка закрепляется неподвижно на столе, а гидравлическая или механическая передача приводит стол в возвратно-поступательное движение. Резец, обрабатывающий плоскость снятием стружки, остается неподвижным. По качеству и точности получаемой поверхности, а также экономичности процесса продольно-строгальная обработка опережает фрезерование. Причем продольно-строгальная операция применима для некоторых задач, которые фрезерованием выполнить невозможно или невыгодно. Особенно экономичным оказывается выполнение единичных или небольших партий заказов. Ведь переналадка станка и установка заготовки не требует много времени и сил. Поверхности заготовок средних размеров и мелкие обрабатываются на поперечно-строгальных станках, где главное возвратно-поступательное движение совершает резец. Стол с закрепленной на нем заготовкой двигается в поперечном направлении горизонтально и вертикально. Вертикальные и наклонные плоскости обрабатываются при неподвижном столе. Привод, как и у продольно-строгальных станков механический или гидравлический (более точный). Поперечно-строгальная операция может использоваться не только для снятия стружки с наклонных, горизонтальных или вертикальных плоских и фасонных поверхностей, но и для вырезания канавок, уступов, пазов или выемок.
14. Шлифовальные работы слесарный металл токарный фрезерный
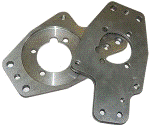
Шлифовальные станки классифицируют по принципу действия и расположению детали. Различают круглошлифовальный, плоскошлифовальный, бесцентрошлифовальный и внутришлифовальный и др. виды станков. Станки шлифовальной группы современных моделей предназначены для изготовления деталей с малыми отклонениями формы, размеров, малыми параметрами шероховатости поверхности и отличаются высокой производительностью. При шлифовании главным движением резания является движения инструмента. Различают шлифование периферией абразивного круга и торцом круга, в первом случае режущей частью является наружная поверхность круга, а во втором случае - торец круга. В зависимости от расположения и формы обрабатываемой заготовки шлифование подразделяют на следующие виды: • Наружное шлифование, когда обрабатывается наружная поверхность заготовки, • Внутреннее шлифование, когда обрабатывается внутренняя поверхность заготовки, • Плоское шлифование, когда обрабатывается плоская поверхность, • Профильное шлифование, когда обрабатывается поверхность, образующая которой представляет кривую или ломаную линию. Тепловая практика 15. Медницко-жестянные работы Обработка жести составляет предмет нескольких ремесел. Жестянщики обычно занимаются и лужением, и часто соединяют свое мастерство с лакировальным, чтобы выпускать изделия в окончательно отделанном виде. Главным инструментом для жестянщика служит молоток, стальной или деревянный, которым работают на стальной наковальне соответственной формы или на деревянном чурбане. Удар стальным молотком по металлическому листу, лежащему на стальной наковальне, плющит и производит на плоском листе шишку, вогнутую со стороны удара, потому что нетронутые ударом части листа не дают материалу возможности раздаваться по сторонам. Удар же по свесившемуся с наковальни краю листа только сгибает его; при этом вогнутая сторона претерпевает сжатие, а выпуклая растягивается. Удар между деревом и сталью тоже не расплющивает металл, а, смотря по обстоятельствам, только сгибает его, растягивает или даже утолщает, "осаживает". Эти три процесса, обуславливающие все приемы для придания формы тонкому листовому металлу, удаются только на мягком, отожженном металле; когда от самой обработки он станет упругим, "крепким", приходится или отжечь работу, или приостановить дальнейшее изменение формы под опасением получить трещины. Поэтому-то белая жесть, которую нельзя отжигать, и железо для кровельной работы, которое отжигать неудобно, должны быть из особенно хорошего, мягкого сорта железа или стали. Медницкие работы: Обработка листового материала слесарными методами. Пайка легкоплавкими и тугоплавкими припоями: котлы, трубопроводы холодильных установок, и др. Чеканка и выколотка. Лужение изделий. Профессия жестянщика в современных условиях одна из ведущих в производстве фасонных частей (отводы, утки, переходы, тройники, крестовины и т. п.) воздуховодов для промышленной вентиляции и производстве монтажа систем промышленной вентиляции. Жестянщики работают на машиностроительных предприятиях по ремонту вентиляции, а также изготовляют различного рода ограждения к станкам, машинам и т. п. 16. Кузнечные работы Горячую обработку металла, т. е. обработку металла в нагретом состоянии, производят в тех случаях, когда под действием усилий нужно изменить форму металла без разрушения. Такая обработка металла в нагретом состоянии называется ковкой. При изготовлении санитарно-технических деталей ковку используют сравнительно мало, ее применяют лишь для изготовления ручного инструмента, средств крепления трубопроводов и нагревательных приборов, а также при выполнении ремонтных работ. Существует два основных метода ковки: свободная ковка и ковка штамповкой. Свободную ковку выполняют с помощью плоских бойков и вспомогательного инструмента, под действием ударов которых металл деформируется и свободно изменяет свои размеры. Свободную ковку можно выполнять на приводных молотах и вручную. Все основные кузнечные операции при свободной ковке заключаются в обработке нагретого металла ударами бабки молота или ручного инструмента для получения поковок или изделий определенной формы и требуемых размеров. Все кузнечные операции при ручной ковке выполняют на наковальне с применением следующих инструментов: гладилки, обжимок, кувалды, ручника, кузнечных зубил, пробойников и клещей. Протяжка - операция, при которой заготовка под действием ударов удлиняется и поперечное сечение ее уменьшается. Протяжку производят на гладкой стороне наковальни с помощью обжимки или на роге наковальни. Осадка - операция, при которой увеличивается поперечное сечение заготовки за счет уменьшения ее длины. Осадка называется полной, если увеличивается все сочен не за счет всей длины, и местной, если увеличивается сечение конца заготовки или середины ее. Местную осадку называют высадкой. При высадке нагревают ту, часть заготовки, которую нужно увеличить в поперечном сечении. Осадку производят ударами кувалды. Загиб - операция, при которой часть заготовки загибают под заданным углом к другой части заготовки. Загиб производят на наковальне, с которой загибаемая часть должна свешиваться так, чтобы вершина угла изгиба совмещалась с краем наковальни. Удары кувалдой наносят по свисающей части, удерживая
заготовку на наковальне клещами и ручником, а большую заготовку- клещами и другой кувалдой, которую держит еще один рабочий. Угол загиба проверяют по шаблону. При ковке необходимо выполнять следующие правила техники безопасности: работать в кожаных рукавицах и брезентовых костюмах; надевать кожаные фартуки и предохранительные очки; применять исправный инструмент; клещи должны соответствовать форме материала; плотно укладывать материал на наковальню; складывать горячие поковки в определенное место; не загромождать проходы в кузнице; осторожно заливать поковки, чтобы образовавшимся паром не обжечь руки и лицо; при осадке конца трубы противоположный конец ее закрывать пробкой. Термическая обработка металлов и сплавов изменяет физические свойства металлов. Заключается она в том, что металл или сплав нагревают до определенной температуры, выдерживают при заданной температуре, а затем подвергают охлаждению. В зависимости от температуры нагрева и режима охлаждения термическая обработка делится на следующие виды: отжиг, нормализация, закалка и отпуск. Металлы и металлические изделия на производстве нагревают в специальных термических печах, ваннах и в кузнечных горнах. Отжиг стали производят для уменьшения ее твердости, затрудняющей обработку. Отжиг приводит также к уничтожению внутренних напряжений, вызывающих при механической обработке появление трещин и коробление. В результате отжига улучшается структура стали, что способствует улучшению качества ее дальнейшей термической обработки. При отжиге сталь нагревают до 740-850° (чем больше углерода содержит сталь, тем ниже температура отжига). После некоторой выдержки при этой температуре сталь в течение многих часов охлаждают. Нормализация стали отличается от отжига более быстрым ее охлаждением на воздухе. В результате нормализации сталь приобретает более высокие механические свойства, чем после отжига. Закалка придает стали высокую твердость. При закалке сталь нагревается до той же температуры, что и при отжиге, выдерживается некоторое время при этой температуре, а затем быстро охлаждается опусканием в холодную или теплую воду, машинное масло, нефть, раствор поваренной соли и другие охлаждающие жидкости. В воде производят закалку инструментов, имеющих несложную форму и изготовленных из углеродистой инструментальной стали. В воде закаливают также изделия из углеродистой конструкционной стали. В горячей воде и в масле производят закалку пружин и других изделий, которые должны обладать высокой упругостью. Мягкие стали, содержащие мало углерода, не закаливаются, то есть не изменяют механических свойств при закалке. Конструкционные и инструментальные углеродистые стали значительно увеличивают при закалке свою твердость, но становятся при этом хрупкими и обладают невысокими 'Механическими свойствами. Отпуск закаленной стали позволяет уничтожить или значительно уменьшить ее хрупкость, иными словами, придать стали вязкость. Для отпуска детали сталь нагревают до температуры от 150 до 680° (чаще всего - 220-300°), выдерживают при этой температуре и охлаждают в воде или масле (скорость охлаждения при отпуске на структуре углеродистых сталей не сказывается). Ниже в таблице приведены температуры закалки и отпуска для некоторых инструментов, изготовленных из углеродистой инструментальной стали. 18. Сварочные работы: а) электросварочные работы Сваркой называется неразъемное соединение двух или более деталей, с помощью электрического тока присадочного материала (электрод). Широкое применение получила ручная дуговая сварка из-за своей простоты и доступности применения. Электрический ток для сварки вырабатывается сварочным трансформатором, который служит для преобразования высокого напряжения эл. сети (220в - 380в) в низкое напряжение вторичной эл. цепи. Кроме трансформатора для сварки металла требуется присадочный материал или электроды. Электроды состоят из металлического стержня, предназначенного для проведения эл.тока и формирования сварочного шва, и обмазки предназначенной для защиты шва от воздействий окружающей среды, стабильного горения дуги раскисления расплавленного металла сварочной ванны, легирование металла, для связывания составляющих покрытия и образования шлака, который должен обладать определёнными физико-химическими данными. Диаметр электрода выбирают в зависимости от толщины металла, катета шва, положения шва в пространстве. б) газосварочные работы Резаки для ручной резки служат для смешения горючего газа с кислородом, образования подогревающего пламени и подачи к разрезаемому металлу струи режущего кислорода. Ручные резаки для газовой резки классифицируются по следующим признакам: по роду горючего газа, на котором они работают: для ацетилена, газов-заменителей, жидких горючих; по принципу смешения горючего газа и кислорода на инжекторные и безинжекторные; по назначению - на универсальные и специальные; по виду резки для разделительной, поверхностной, кислородно-флюсовой, копьевой. В настоящее время широкое применение получили универсальные резаки. К универсальным резакам предъявляются следующие основные требования: возможность резки стали толщиной от 3 до 300 мм в любом направлении, устойчивость против обратных ударов, малая масса и удобство в обращении. Как и сварочные горелки, резаки имеют инжекторное устройство, обеспечивающее нормальную работу горючего газа в диапазоне давлений 0,03-1,5 кгс/см2. Инжекторный резак отличается от инжекторной горелки тем, что имеет отдельный канал для подачи режущего кислорода и специальную головку, которая включает в себя два сменных мундштука - внутренний и наружный. Источником теплоты является газовый факел, образующийся при сгорании смеси кислорода и горючего газа. В качестве горючего газа могут быть использованы: ацетилен, МАФ, пропан, бутан, блаугаз, водород, керосин, бензин, бензол и их смеси. Тепло, выделяющееся при горении смеси кислорода и горючего газа, расплавляет свариваемые поверхности и присадочный материал с образованием сварочной ванны. Пламя может быть окислительным, "нейтральным" или восстановительным.
- 1 2 3