ВУЗ: Не указан
Категория: Не указан
Дисциплина: Не указана
Добавлен: 16.10.2024
Просмотров: 60
Скачиваний: 0
СОДЕРЖАНИЕ
1 Характеристика предприятия и проектируемого цеха
1.1 Расположение и состав предприятия
2 Обоснование технических решений и направлений проектирования
2.1 Вывод о целесообразности проектирования и постановка
2.2 Обоснование предлагаемых проектных решений
3.1 Характеристика выпускаемой продукции и ее соответствие
3.2 Характеристика применяемого сырья и материалов
3.3 Установление календарного режима работы цеха
3.4 Разработка технологической схемы производства продукции,
выбор технологического оборудования и описание
3.6 Расчет производительности, количества и коэффициента загрузки
оборудования. Корректировка производственной программы
3.7 Расчет площадей складов хранения сырья и полуфабрикатов, мест
технологической выдержки, бытовых и вспомогательных помещений
3.8 Расчет потребности в инструменте и оборудовании для его заточки
3.10 Расчет количества электроэнергии
3.11 Расчет ленточного конвейера
nфакт – фактически принятое количество оборудования.
Фактически принятое количество оборудования получается путем округления nрасч до ближайшего целого числа.
В отдельных случаях допустима перегрузка оборудования на 5… 10 % (К3= 1,05… 1,10), если при расчете производительности оборудования использованы средние параметры режима обработки, например, скорости подачи, числа оборотов шпинделей, температуры при оклеивании и т. п. Целесообразно при этом сравнить расчетную производительность со средней производительностью оборудования, достигнутой наиболее передовыми промышленными предприятиями.
3.6.1 Подготовка сырья к лущению шпона
Подготовка сырья к лущению включает следующие основные операции: гидротермическую обработку сырья (ГТО), окорку и разделку по длине. Последовательность технологических операций на этом участке может быть различной, зависит от вида производства, породы и размеров используемого сырья и т. д.
Необходимо учитывать, что оборудование для окорки и разделки сырья по длине обычно располагают в одном потоке, в этом случае производительности окорочных станков и круглопильных должны быть согласованы.
3.6.2 Гидротермическая обработка сырья
Продолжительность прогрева фанерного сырья определяют по формуле

где τt– продолжительность прогрева, ч. Температуру воздуха в
Ростове-на-Дону принимаем -190С, следовательно, τt=14 ч (при среднем
диаметре исходного сырья 24 см);
Кn- коэффициент породы древесины: для березы Кп=1;
Кд– коэффициент, зависящий от способа доставки: доставленного
железной дорогой Кд = 1,0;
Кх– коэффициент, зависящий от способа хранения: дождевание,
водное хранение Кх=1,0.
τ = 14·1·1·1 = 14 ч.
Производительность секции

где L, В, Н – соответственно длина, ширина и глубина секции, м;
К3– коэффициент загрузки (в пучках К3= 0,90)
Ку– коэффициент плотности укладки сырья (Ку=0,70);
Кр– коэффициент рабочего времени (Кр=0,95);
Тсм– продолжительность смены, ч (Тсм=8);
τ– продолжительность ГТО сырья, ч.

Размеры открытых бассейнов зависят от пролета крана. Пролет крана ККУ – 10 составляет 20 м, поэтому можно принять L=18 м. Величина В=5 м (из расчета максимальной длины кряжа 4,8 м; а Н=2 м).

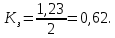
Принимаем 2 секции для гидротермической обработки древесины с коэффициентом загрузки Кз=62%.
3.6.3 Раскрой кряжей на чураки
Для раскроя кряжей на чураки чаще всего используются круглопильные однопильные станки балансирного или маятникового типов.

где Т – продолжительность смены, ч (480 ч);
m– количество чураков, получаемых из одного кряжа, шт (3);
Vч– объем чурака, м3(Vч = 0,08 м3);
Кр– коэффициент использования рабочего времени станка,
обычно принимается 0,95;
t– продолжительность одного реза или пропила (состоит из
затрат времени на продвижение кряжа, опускание пилы,
пиление и подъем пилы), с;
р – количество резов (пропилов), приходящихся на один кряж с
учетом оторцовки и возможной вырезки дефектных мест, шт (5).


Принимаем два круглопильных станка ПА-15 с коэффициентом
загрузки Кз
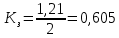
4.1.3 Окорка сырья
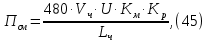
где Vч– объем чурака, м3(0,08 м3);
U– скорость подачи станка, м/мин;
Кр– коэффициент рабочего времени (0,80);
Км– коэффициент машинного времени (0,70);
Lч– длина чурака, м (1,6 м).
Принимаем окорочный станок ОК63-1Ф со скоростью подачи 8,4 м/мин.


Принимаем один окорочный станок с коэффициентом загрузки К3 = 0,79.
3.6.4 Лущение и рубка шпона
Лущение шпона.
Производительность лущильного станка.
В чураках, разлущиваемых за смену
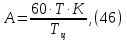
В куб. метрах сырого шпона за смену

где Т – продолжительность смены, мин;
Тц– продолжительность полного цикла обработки одного чурака, с;
К – коэффициент использования рабочего времени (К=0,94…0,95);
Vш.ср.– объем сырого шпона (полноформатного и деловых кусков),
полученного из одного чурака, м3 (определяется при расчете расхода
сырья).
Продолжительность полного цикла обработки одного чурака (Тц) включает следующие затраты
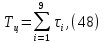
где T1– продолжительность установки чурака, зависит от диаметра и
формы чурака, конструкции станка и центровочно-загрузочного
приспособления, с.
Т1=3-6 с.
Принимаем Т1= 3с.
Т2– продолжительность зажима чурака роликами
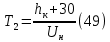
где hk– глубина внедрения центра кулачка в торец чурака, равна в среднем
30-60 мм (принимаем hk = 30 мм);
UH– скорость осевого перемещения наружных шпинделей, мм/с (по
технической характеристике лущильного станка UH = 70 мм/с);

T3–продолжительность подвода суппорта на ускоренной подаче, с,

гдеLc– путь, проходимый суппортом на ускоренной подаче, (30мм);
Uc– скорость ускоренной подачи суппорта, мм/с; (50… 100мм/с);
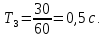
Т4– продолжительность оцилиндровкичурака
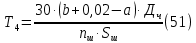
где b– коэффициент формы чурака, определяется по формулам для
березовых чураков
b=0,935+0,165Lч;
а – коэффициент оцилиндровки, определяемый по формулам для
березовых чураков.
а=0,818+0,067 Lч;
Lч– длина чурака, м(Lч = 1,6 м);
Дч– диаметр чурака, мм (Дч = 240 мм);
nш– число оборотов шпинделей, мин-1 (принимаем nш=63,69 мин-1);
Sш– толщина шпона, мм.



Т5– продолжительность лущения оцилиндрованного чурака
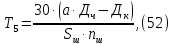
где Дк– диаметр карандаша, мм;

Т6
– продолжительность отвода суппорта, с.


Т7– продолжительность отвода шпинделя
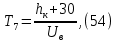
UB– скорость осевого перемещения внутреннего шпинделя, мм/с
(принимаем Uв = 35 мм/с);
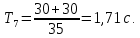
Т8– продолжительность удаления карандаша, 2-3 с (принимаем Т8 = 2с);
Т9– продолжительность прочистки просвета между ножом и
прижимной линейкой, (1-2 с, принимаем Т9 = 1с.).



Определяем потребное количество станков:

Принимаем 5 лущильных станка с коэффициентом загрузки:
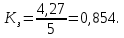
Рубка шпона
Производительность ножниц для рубки ленты шпона определяется по формуле

где Т – продолжительность смены, ч;
Ки– коэффициент использования рабочего времени ножниц (0,93-0,95;
принимаем Ки = 0,93);
Vл– объем одного листа сырого шпона, м3;
V(1,5) = 1,6·1,6·0,0015 = 0,00384 м3
Кр– коэффициент продолжительности рубки листов, % от
продолжительности полного цикла получения шпона от одного чурака;
t – затраты времени на прохождение одного листа шпона через
ножницыи отрезку его от ленты (1,5-5 с) или из технической
характеристикиножниц (принимаем t= 2 с).
При отводе шпона от ножниц (без перекладки) Кр=0,6-0,8, при перекладывании шпона вручную со стола ножниц на подстопное место Кр= 0,4-0,6. Принимаем Кр= 0,6.

Определяем расчетное количество ножниц:

Принимаем 5 ножниц для рубки шпона APL 68 с коэффициентом загрузки
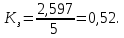
По технологическим соображением устанавливаем 5 ножниц по количеству лущильных станков, т.к. они работают в линии.
3.6.5 Сушка шпона
Средняя температура в сушилках выбирается как среднеарифметическая величина температур на входе и выходе сушилок. Для газовых сушилок средняя расчетная температура ориентировочно 160-165 °С, для паровых - 120-125 °С.
При использовании однокомпонентных фенолоформальдегидных клеев для склеивания требуется сушка шпона после нанесения смолы на шпон или пропитки шпона смолами. С этой целью применяют конвейерные сушилки.
Расчет производительности роликовых (ленточных) сушилок.
Производительность сушилок за смену по сухому шпону

где Т - время работы сушилки за смену, мин;
n - число листов шпона по ширине этажа, умноженное на число этажей
(для полноформатного шпона принимаем n=16;
S - толщина листа шпона, м;
b - ширина листа после сушки, м (1,6 м);
L - полная рабочая длина сушилки, м;
τ1 - время прохождения шпона через сушилку, мин;
K1 - коэффициент учета времени при переходе от сушки шпона
одного вида к другому и равен 0,9... 1 (принимаем K1 = 0,9);
K2 - коэффициент использования времени работы сушилки,
К2=0,9...0,95(принимаем К2 = 0,9 );
K3 - коэффициент заполнения шпоном рабочей длины сушилки равен
0,98.
Продолжительность прохождения шпона по всей роликовой сушилки
(по зонам сушки и охлаждения) определяется по формуле

где τ - продолжительность сушки шпона в сушильной зоне, мин;
L - полная рабочая длина сушилки, м (СУР-6 – 14,26 м, СРГ-25М –
16,36 м);
l - длина сушильной зоны, м ( СУР-6 – 12,5 м, СРГ-25М – 14,2).
Продолжительность сушки шпона в роликовых сушилках определяется по формуле

где Wн, WK - начальная и конечная влажность шпона, % (принимаем 70 и
8% соответственно);
30 - влажность шпона, соответствующая переходу от периода постоян
ной скорости сушки к периоду убывающей скорости;
Np - скорость сушки в период постоянного ее значения %/мин;
Кр - коэффициент продолжительности сушки в период убывающей
скорости сушки;
Кп