Файл: Содержание Введение Общие вопросы выпускной работы 11.doc
Добавлен: 29.03.2024
Просмотров: 77
Скачиваний: 0
ВНИМАНИЕ! Если данный файл нарушает Ваши авторские права, то обязательно сообщите нам.
Твсп. = 2,65 мин.
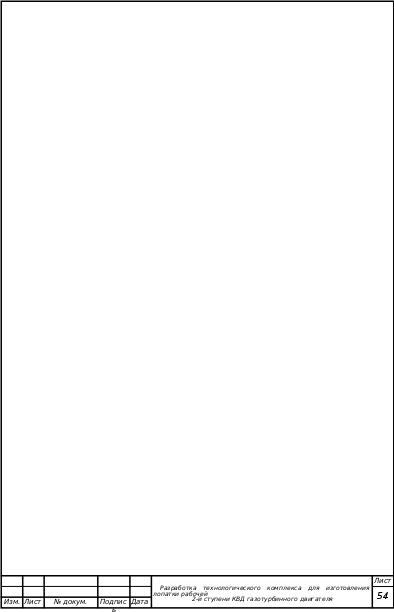


Штучное время на операцию №020 будет равно:

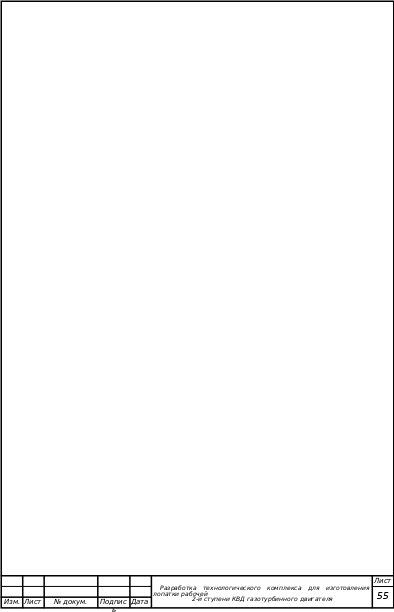
При выполнении операции фрезерования профиля пера деталь устанавливается в кассету, которая обеспечивает базирование и закрепление детали.
На рисунке 2.9 показано станочное приспособление для фрезерования профиля пера лопатки.
Приспособление состоит из плиты - 1, корпуса - 2, планки - 3, прихвата - 4, винта – 5, упора - 6, планки - 7 и пальцев - 8 и 9.
Лопатка устанавливается в кассету, которая состоит из планки 3 и прихвата 4, образуя соединение типа «ласточкин хвост» и фиксируется в этом положении гайкой 7. (см. приложение А – лист )
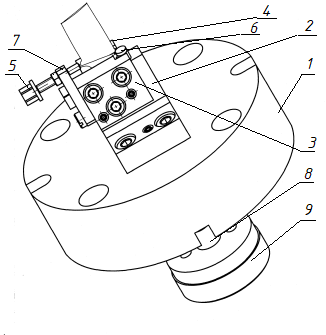
Рисунок 2.9. Станочное приспособление для фрезерования профиля пера лопатки.
1 – плита, 2 – корпус, 3 – планка, 4 – прихват, 5 – винт, 6 – упор, 7 – планка, 8;9 – пальцы.
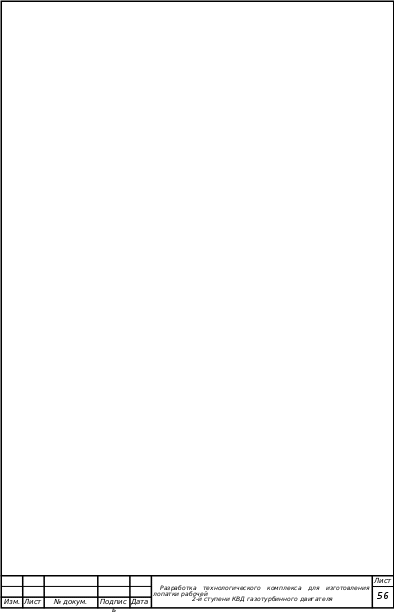
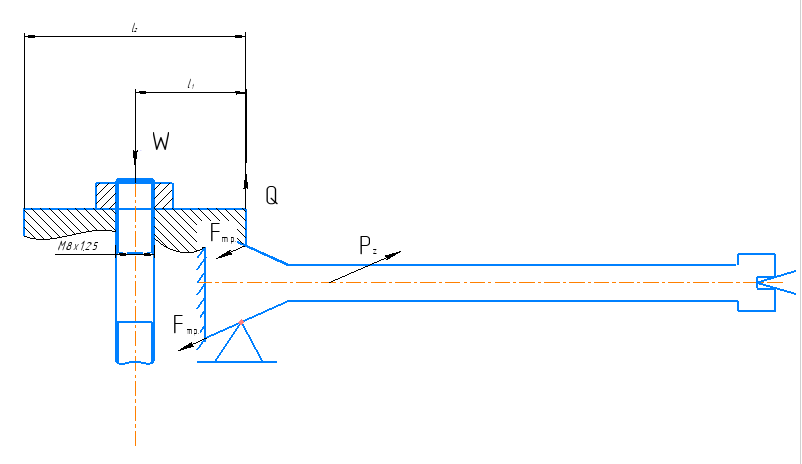
Рисунок 2.9.1. Расчетная схема закрепления лопатки на операции №090 Фрезерная с ЧПУ «Профиля пера».
Сила закрепления заготовки определяется определяется по формуле 20:
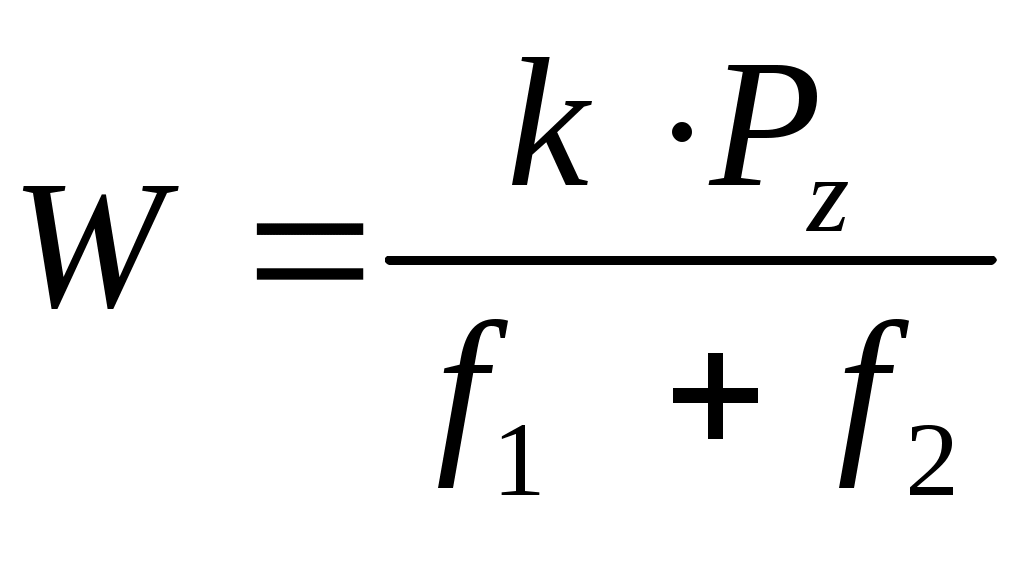
гдеk – коэффициент запаса;
Pz – сила резания, Н;
f1 и f2 – коэффициенты трения в местах контакта.
Коэффициент запаса определяется как:

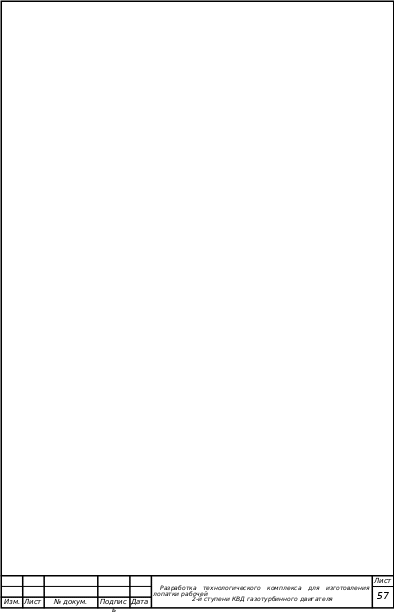
k1 – коэффициент, учитывающий увеличение силы резания из за случайных неровностей на заготовке – 1,2;
k2 – коэффициент, учитывающий увеличение силы резания вследствие притупления режущих кромок инструмента – 1,1;
k3 – коэффициент, учитывающий увеличение силы резания из- за затупления режущего инструмента – 1,2;
k4 – коэффициент, учитывающий нестабильность усилия зажима – 1,3 (для ручных зажимов);
k5 – коэффициент учитывающий удобство расположения рукоятки в ручном зажиме – 1,0;
k6 – коэффициент, учитывающий неопределенность по причине неровностей места контакта заготовки с опорным элементом – 1,5.
Коэффициенты трения f1 и f2 выбираем по таблице 5.1; [12], f1 = 0,15, f2 = 0,1 – т.к обработанная поверхность хвостовика контактирует с плоскостью опорного элемента.
Определяем коэффициент запаса:

Тогда сила закрепления будет равна:
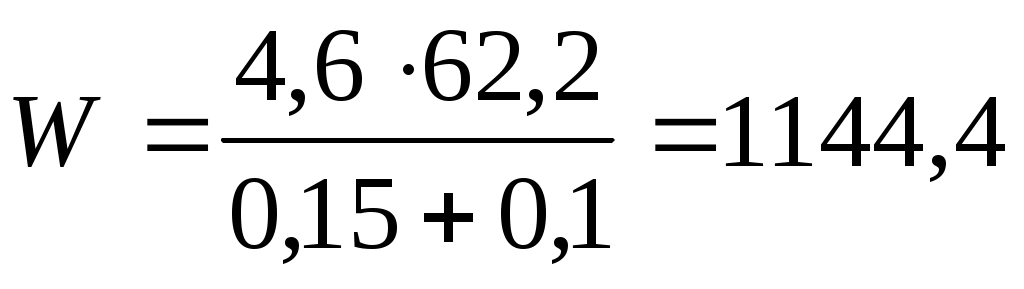
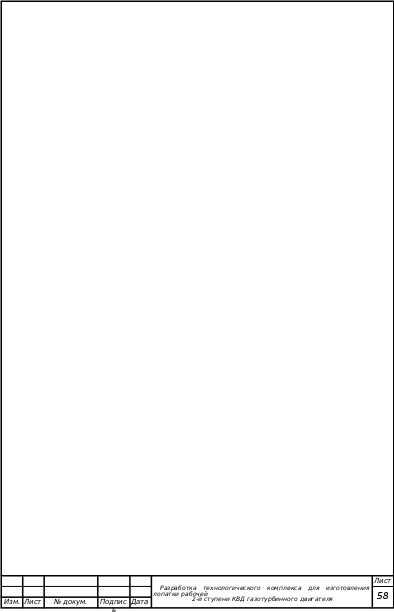
Расчету подлежит резьбовое соединение соединение в приспособлении, а конкретно шпилька М8 х 1,25 .
Исходными данными для расчета являются:
Осевое усилие на винт: W = 1144,4 , Н.
Марка стали винта: 3.6. (табл. 1.2); [13].
Допускаемое напряжение:
- на растяжение: [σ]20 = 90, МПа; (табл.1.3); [13].
- на срез: [τ]20 = 45, МПа. (табл.1.3); [13].
Номинальный диаметр резьбы винта: D = 8 мм.
Шаг резьбы : Р = 1.25, мм.
Диаметр резьбы по впадинам: d3 = 6.47, мм.
Коэффициент полноты резьбы K1 = 0.75; [13].
Коэффициент деформации витков: Km = 0.6; [13].
Коэффициенты наличия смазки:
ζ = 0.18; ζ1 = 0.37. (табл. 2.1); [13].
Крутящий момент при затяжке Мкр определяется по формуле 21:
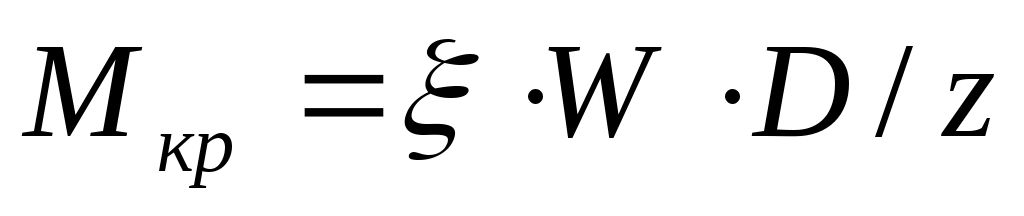

, Нм·м = 0,15 кгс·м.
Момент на ключе Мкр.кл для обеспечения усилия Fw определяется по формуле 22:


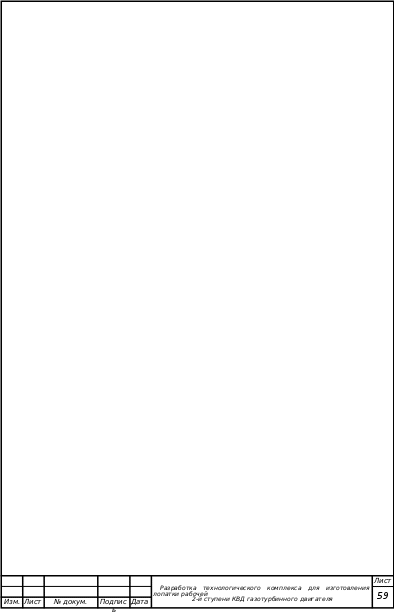
Напряжения среза резьбы на винте τр определяется по формуле 23:


Напряжения крученияна винте τкр определяется по формуле 24:


Таким образом лля закрепления заготовки в приспособлении (см. приложение А – лист) гайку М8 х 1,25 7-Н позиции 17 следует закручивать гайковертом с муфтой настроенной на величину крутящего момента 0.3 кгс· м, что обеспечивает постояноство силы закрепления. Или рожковым ключом с длиной рукоятки не более 200 мм, при норме усилия на руке исполнителя от трех до пяти кг.
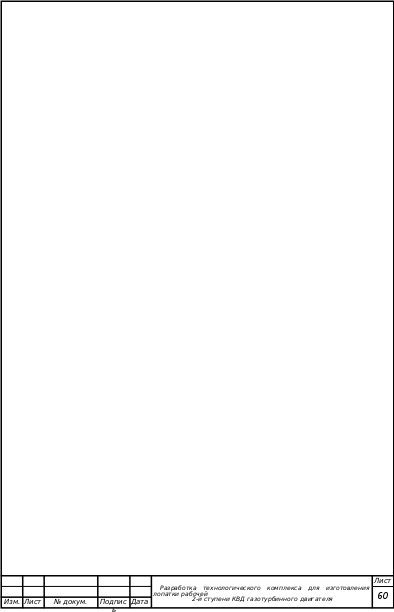
Для контроля профиля пера лопаток в условиях серийного производства применяют оптико-механический прибор ПОМКЛ – 4.
Данный прибор предназначается для контроля размеров и формы профильных сечений пера готовых лопаток. Одновременно с профилем проверяется угол закрутки профиля пера относительно хвостовика.
Принцип работы прибора ПОМКЛ-4 состоит в том, что на экране с увеличением 50:1 изображается величина перемещения контактных стержней, которые вызваны отклонениями размеров профилей сечений пера лопатки от номинальных размеров. Длина контактного стержня равна расстоянию от проверяемой точки до плоскости измерения. Приведение длины стержней к плоскости измерения осуществляется плоским шлифованием стержней, которые затем собирают в блоки по эталону.
При установке контролируемой лопатки в прибор отклонение размеров, формы профилей сечений пера от номинала вызывает смещение контактных стержней. Это смещение передается на измерительные стержни и в дальнейшем рычажки с соотношением плеч 5:1 проецируются на экран с увеличением 10:1. Таким образом достигается общее увеличение 50:1.
В зависимости от характера погрешности профиля в контролируемом сечении концы рычажков экрана могут отклоняться по отдельности от базовых прямых, или смещаться параллельно этим прямым, или располагаются на одной прямой под углом к базовым прямым. Таким образом, на приборе контролируются не только погрешностей формы профилей, но и смещение профилей пера с оси хвостовика, а также отклонения по углу закрутки профиля. На экране устанавливаются границы поля допуска, по которым определяют пригодность контролируемой лопатки.
Прибор состоит из: корпуса 1 в котором расположено специальное приспособление для закрепления лопатки 2, корпуса контактных стержней
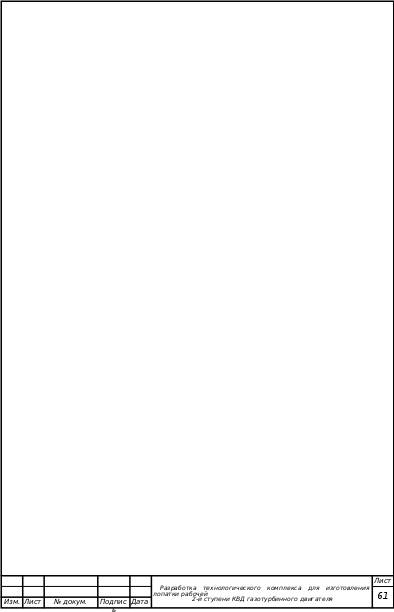
После проведения контроля позиция загрузки и выгрузки детали 11 выезжает из прибора и происходит замена детали.
В таблице 2.8 приведены технические характеристики прибора ПОМЛК-4, а на рисунке 2.9.2 показана принципиальная схема прибора ПОМКЛ-4.
Таблица 2.8 – Технические характеристики прибора ПОМКЛ-4.
Размеры контролируемых лопаток, мм Длина Ширина | До 250 До 100 |
Шаг между стержнями, мм | 5 |
Увеличение прибора | 50 - кратное |
Погрешность измерения, мм | 0,02 |
Производительность, шт/час | 120 ; 250 |
Габаритные размеры, мм | 900 х 480 х 620 |
Масса, кг | 115 |
Напряжение питания, В | 220 |
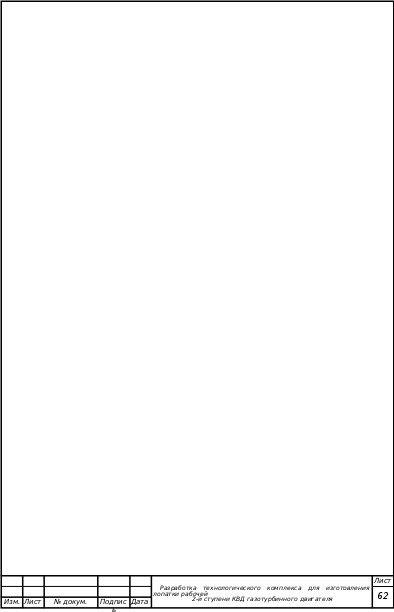
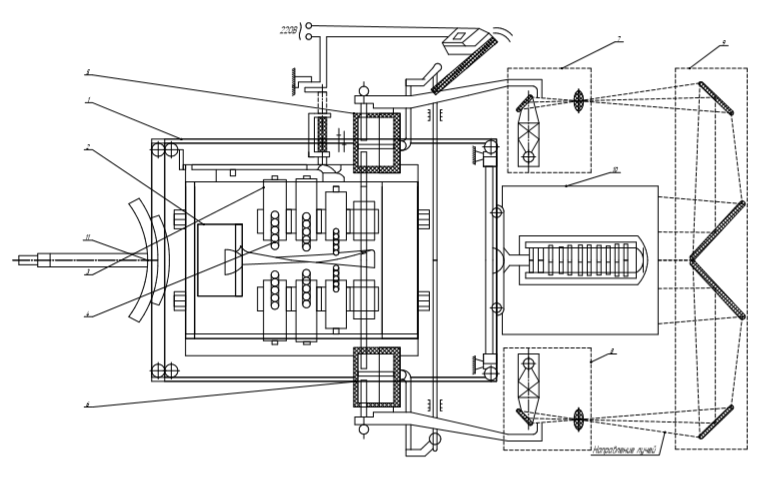
Рисунок 2.9.2. Принципиальная схема прибора ПОМКЛ – 4.
1 – корпус, 2 – приспособление для закрепления лопатки, 3 – корпус контактного стержня, 4 – контактный стержень, 5; 6 – блоки преобразования линейных перемещений; 7; 8 – преобразователи линейных перемещений в перемещения оптического луча; 9 – преобразователь оптических перемещений; 10 – приемник отраженных лучей; 11 – позиция загрузки – выгрузки детали.
Принципиальная схема представлена на листе № 8 приложения А
Чертеж приспособления для закрепления лопатки представлен на листе № 9 приложения А.
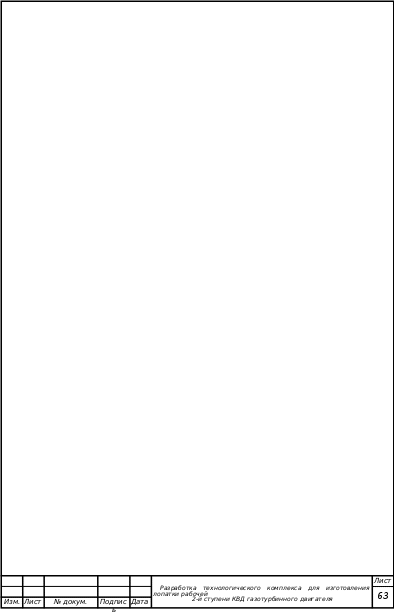
Количество оборудования расчитаем для условия массового производства.
Количество оборудования определяется по формуле 25:

Где Тшт. – штучное время операци выполняемой на i-м оборудовании, мин;
τ – такт выпуска, τ = 8,4, мин/шт (см.страницу).
Коэффициент загрузки оборудования Кз.о определяется по формуле 26:
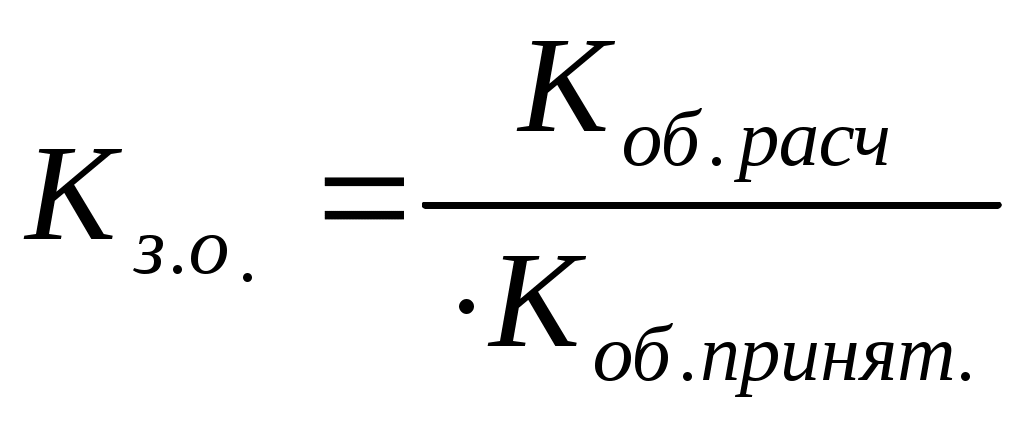
где Коб. расч. – количество оборудования расчетное, шт;
Коб.прин. – количсество оборудования принятое, шт.
Количество станков Коб.расч. для операции №020 «Протяжная»:
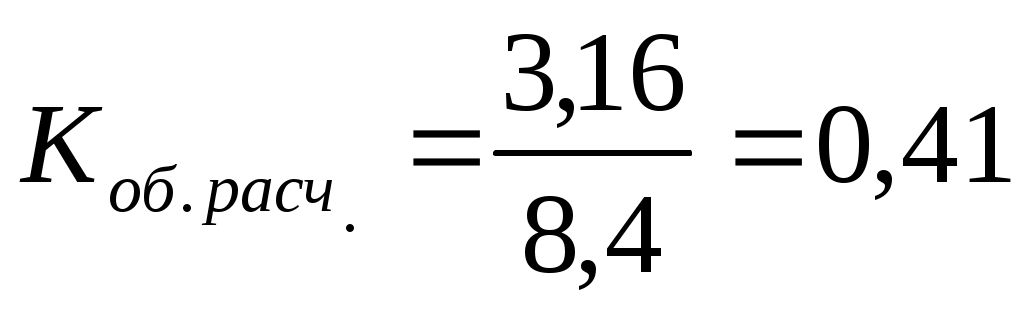
округляем полученное значение до целого числа и принимаем Kоб.пр = 1 шт.
Коэффициент загрузки оборудования Кз.о на операции №020 «Протяжная»:
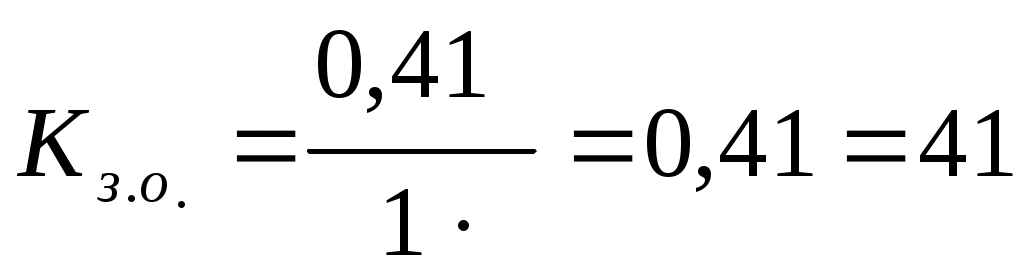
Количество станков Коб.расч. для операции №030 «Протяжная»:
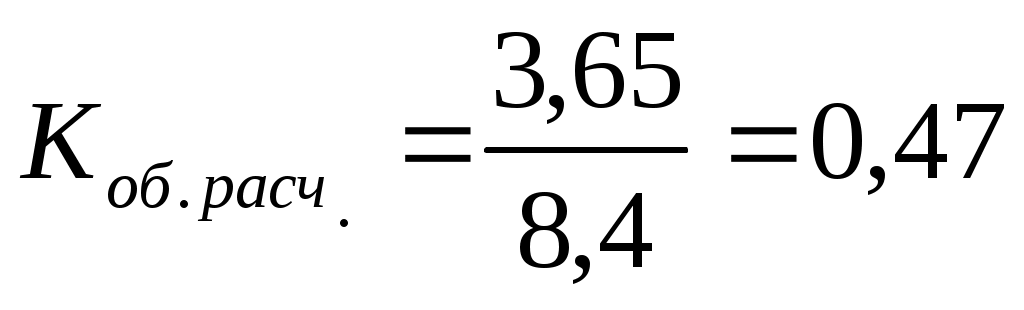
округляем полученное значение до целого числа и принимаем Kоб.пр = 1 шт.
Коэффициент загрузки оборудования Кз.о на операции №030 «Протяжная»:
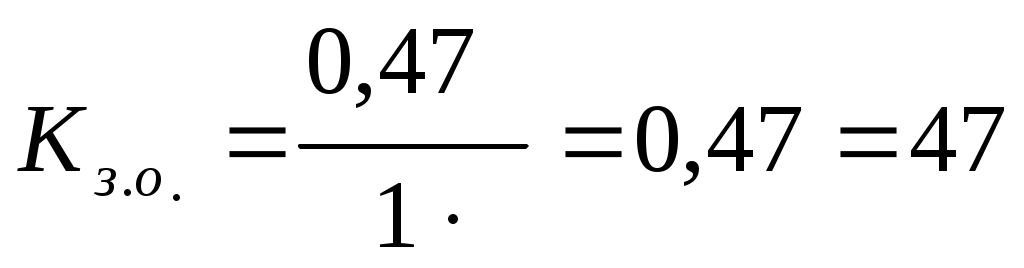
Количество станков Коб.расч. для операции №040 «Протяжная»:
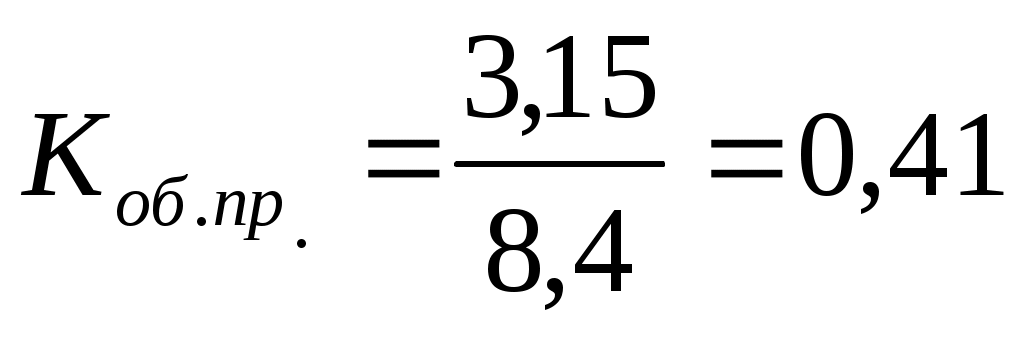