Файл: Разработка автоматизированного участка для детали вал.docx
ВУЗ: Не указан
Категория: Не указан
Дисциплина: Не указана
Добавлен: 26.04.2024
Просмотров: 47
Скачиваний: 0
ВНИМАНИЕ! Если данный файл нарушает Ваши авторские права, то обязательно сообщите нам.
насторону. В итоге получаем заготовку с габаритными размерами 46 x 166 мм.
Для определения нормы расхода материала необходимо определить массу заготовки. Массу заготовки рассчитывают исходя из его объема и плотности материала. Необходимо стремиться к тому, чтобы форма и размеры заготовки были близки к форме и размерам готовой детали, что уменьшает трудоемкость механической обработки, сокращает расход материала, режущего инструмента, электроэнергии и т.д.
Массу заготовки рассчитывают по формуле:
Kиm
= ????,
????з
где – масса детали по чертежу, кг; з – масса заготовки, кг. Масса детали по чертежу известна, она составляет = 1,483 кг. Масса заготовки:2,61 кг
Следовательно, подставив значение з = 4,3 . в формулу 4, получим:
Kиm
= 1,483 = 0,68. (4)
2,61
Помимо рабочего чертежа детали, необходимо также для проектирования механической обработки иметь и рабочий чертеж заготовки. Таковой необходим прежде всего для того; чтобы иметь все припуски на обработку (чтобы было их легко видеть, обычно, внутри контура заготовки дается контур готовой детали и проставляются размеры припусков па обработку).
Кроме того, этот чертеж позволяет установить, каким образом возможно и удобно закрепить данную деталь при обработке; очень часто дает указание о том, как удобнее начать обработку детали (здесь важны не только размеры припусков, по и расположение заусенца, расположение конических поверхностей для выемки из штампа — «уклоны» у поковок, а также расположение литника, выпора и плоскостей стыка форм — у отливок и т. д.).
Заготовка типа круг имеет размеры 166 мм в длину на диаметр ∅46 мм.
Чертеж заготовки представлен ниже на рисунке 1.6.
Рисунок 1.6- Чертеж заготовки
это часть производственного процесса, содержащая целенаправленные дейст вия по изменению и (или) определению состояния предмета труда. К предмет ам труда относят заготовки и изделия.
Практически любой технологический процесс можно рассматривать как часть более сложного процесса и совокупность менее сложных (в пределе
— элементарных) технологических процессов.
Технологический процесс втулки приведен в таблице 1.
Таблица 1 – технологический процесс
Режимы резания определяются глубиной резания t, мм; подачей на оборот So, мм/об и скоростью резания V, м/мин.
Режимы резания оказывают влияние на точность и качество обработанной поверхности, производительность и себестоимость обработки.
В курсовом проекте необходимо рассчитать для одной из операций:
глубину, подачу и скорость резания по формулам теории резания; суммарную силу резания и эффективную мощность электродвигателя
главного привода станка.
На все остальные операции техпроцесса режимы резания назначают по нормативам предприятий или справочникам [16, 21, 27].
Исходными данными при выборе режимов резания являются:
сведения о заготовке (вид заготовки, материал и его характеристика, величина припусков, состояние поверхностного слоя);
данные об обрабатываемой детали (форма, размеры, допуски на обработку, требования к состоянию поверхностного слоя, к шероховатости);
данные о режущем инструменте (типоразмер, материал режущей части, геометрические параметры);
паспортные данные станков (техническая характеристика).
Таким образом, режим резания устанавливают исходя из особенностей обрабатываемой детали, характеристики режущего инструмента и станка.
В первую очередь устанавливают глубину резания t. При однопроходной обработке на настроенном станке глубина резания равна припуску. При многопроходной глубина резания на первом рабочем ходе берется максимальная, на последующем – уменьшается с целью достижения заданной точности. Обычно на черновом этапе удаляется до 70 % припуска, а на чистовые этапы оставляют не более 30 %.
Подача So назначается максимально допустимой [26]. При черновой обработке ее величина ограничивается жесткостью и способом крепления
обрабатываемой детали, прочностью и жесткостью инструмента, прочностью механизма подачи станка.
При чистовой обработке S определяется заданной точностью
-
Коэффициент использования материала
Для определения нормы расхода материала необходимо определить массу заготовки. Массу заготовки рассчитывают исходя из его объема и плотности материала. Необходимо стремиться к тому, чтобы форма и размеры заготовки были близки к форме и размерам готовой детали, что уменьшает трудоемкость механической обработки, сокращает расход материала, режущего инструмента, электроэнергии и т.д.
Массу заготовки рассчитывают по формуле:
Kиm
= ????,
????з
где – масса детали по чертежу, кг; з – масса заготовки, кг. Масса детали по чертежу известна, она составляет = 1,483 кг. Масса заготовки:2,61 кг
Следовательно, подставив значение з = 4,3 . в формулу 4, получим:
Kиm
= 1,483 = 0,68. (4)

-
Чертеж заготовки
Помимо рабочего чертежа детали, необходимо также для проектирования механической обработки иметь и рабочий чертеж заготовки. Таковой необходим прежде всего для того; чтобы иметь все припуски на обработку (чтобы было их легко видеть, обычно, внутри контура заготовки дается контур готовой детали и проставляются размеры припусков па обработку).
Кроме того, этот чертеж позволяет установить, каким образом возможно и удобно закрепить данную деталь при обработке; очень часто дает указание о том, как удобнее начать обработку детали (здесь важны не только размеры припусков, по и расположение заусенца, расположение конических поверхностей для выемки из штампа — «уклоны» у поковок, а также расположение литника, выпора и плоскостей стыка форм — у отливок и т. д.).
Заготовка типа круг имеет размеры 166 мм в длину на диаметр ∅46 мм.
Чертеж заготовки представлен ниже на рисунке 1.6.
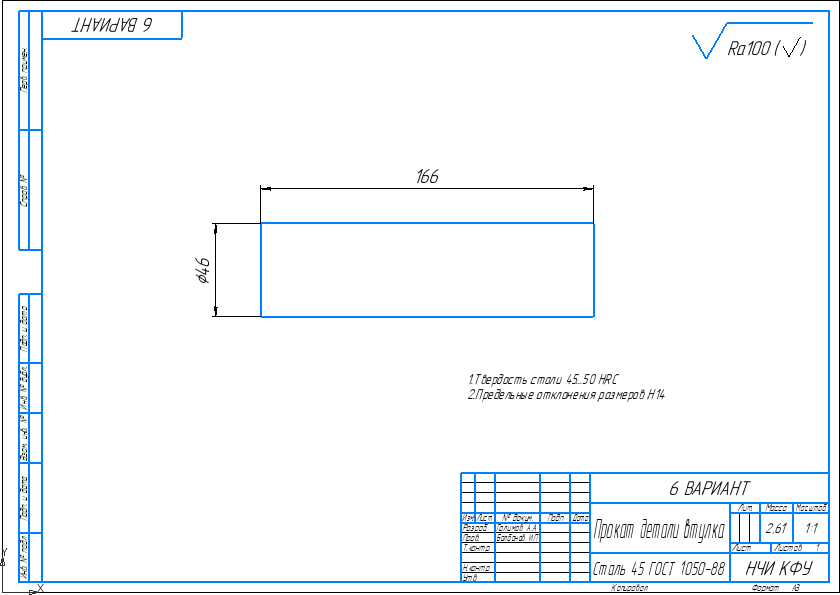
Рисунок 1.6- Чертеж заготовки
-
Разработка технологического процесса Технологический процесс —
это часть производственного процесса, содержащая целенаправленные дейст вия по изменению и (или) определению состояния предмета труда. К предмет ам труда относят заготовки и изделия.
Практически любой технологический процесс можно рассматривать как часть более сложного процесса и совокупность менее сложных (в пределе
— элементарных) технологических процессов.
Технологический процесс втулки приведен в таблице 1.
Таблица 1 – технологический процесс
Операц ия | Устан ов | Позиция | Содержание перехода | Эскиз |
1. | 1.1 | 1.1.1 | Установить и | ![]() |
Загот- | | | зажать сортамент | |
ая | | | с двух сторон. | |
| | | Отрезать | |
| | | заготовку, | |
| | | выдерживая | |
| | | размер 167х467 |
2.Тока рная с ЧПУ | 2.1 | 2.1.1 | Подрезать торец, выдерживая размер 1 | |
2.1.2 | Точить поверхность на длину 2 и диаметр 3 | | ||
2.1.3 | Точить фаску, выдерживая размер 8 | | ||
| 2.1.3 | Точить проточку на диаметр 5 , на длину 6 | | |
2.2 | 2.2.4 | Переустановить и закрепить заготовку. Точить поверхность на диаметр 7, выдерживая длину 8 | | |
2.2.5 | Точить фаску 9 | ![]() |
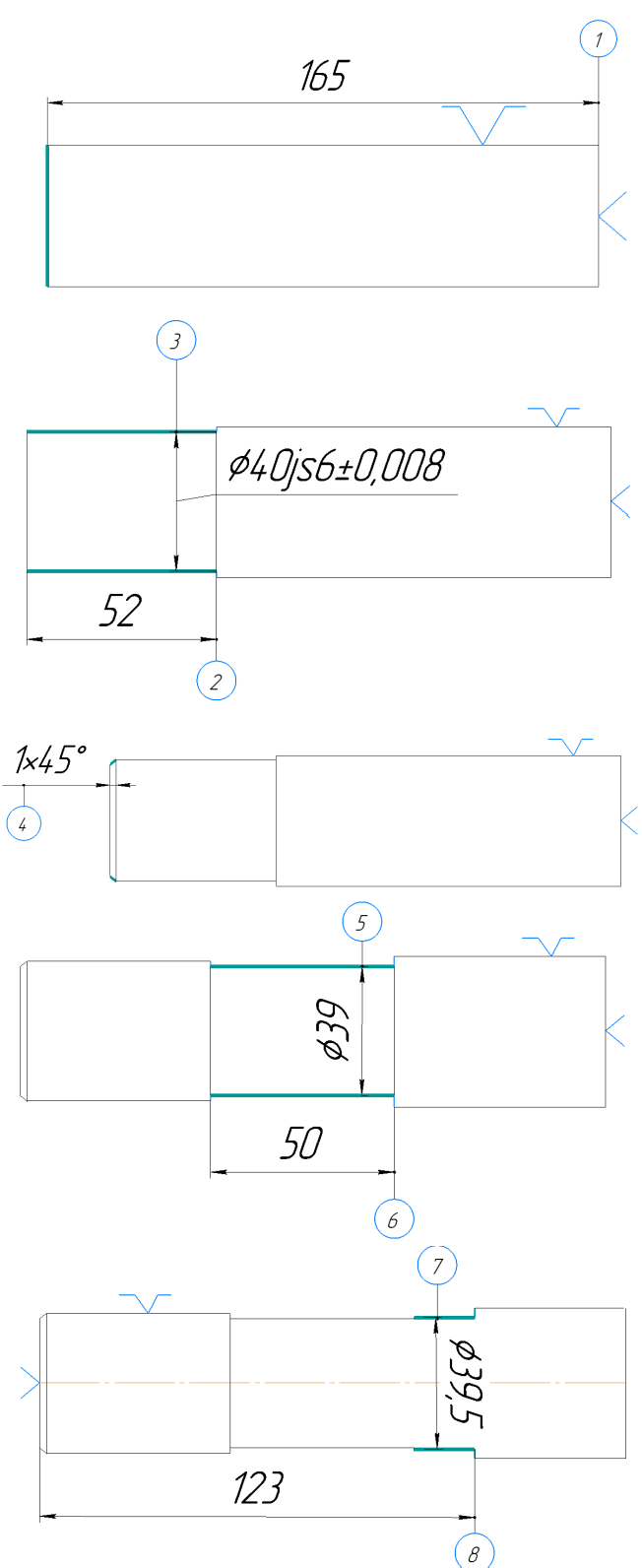
| | 2.2.6 | Точить поверхность на диаметр 10, выдерживая размер 11 | |
2.2.7 | Точить канавку, выдерживая размеры 12,13 | | ||
3. Фрез- я с ЧПУ | 3.1 | 3.1.1 | Фрезеровать шпоночный паз, выдерживая размеры 14,15 На глубину 16, ширину 17 (Вид Б-Б) С 18 (Вид В) | ![]() |
| | | | |
3.2 | 3.2.1 | Переустановить и закрепить деталь. Сверлить отверстие на длину 19 Диаметром 20 | |
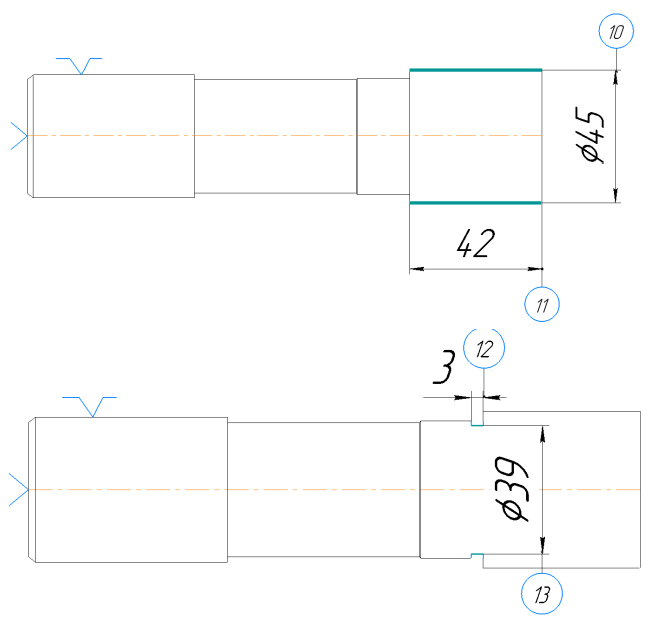
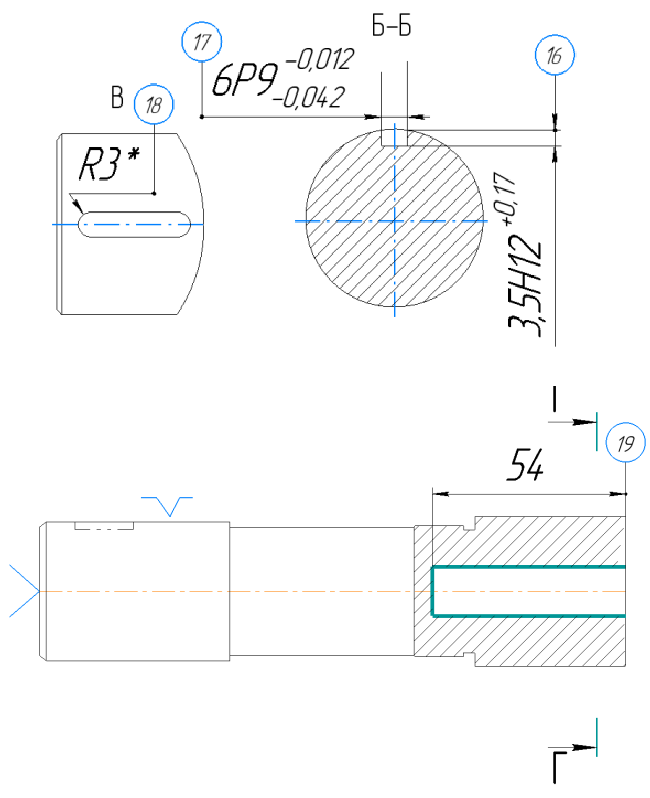
| | | | ![]() |
3.2.2 | Фрезеровать отверстие на длину 21 Диаметром 22 | ![]() | ||
| | | | |
3.2.3 | Фрезеровать канавку, выдерживая размеры 23,24 | |
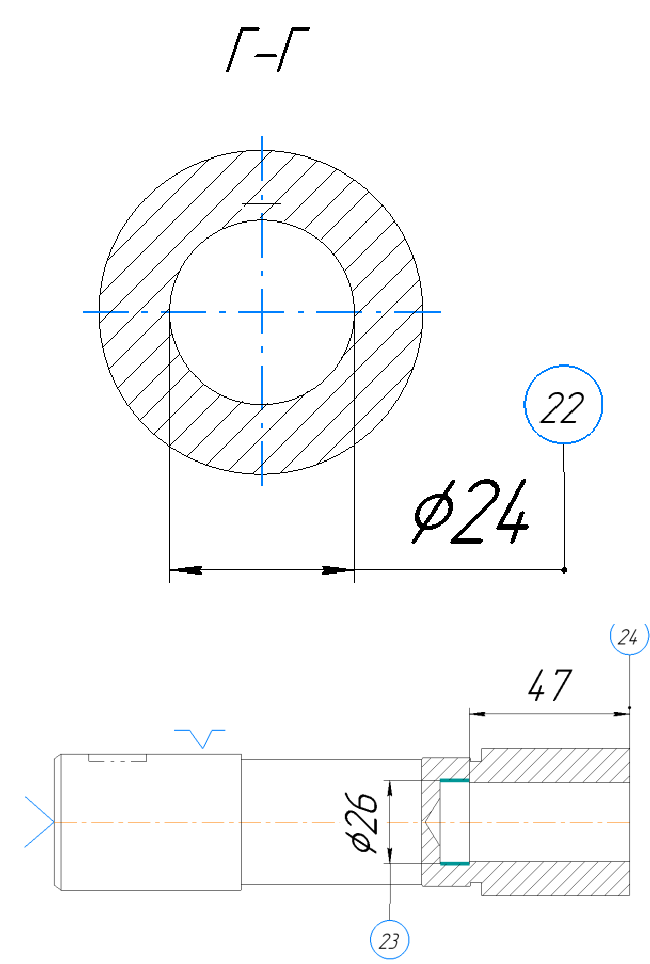
| | 3.2.4 | Зенковать фаску, выдерживая размер 25 | |
3.2.5 | Сверлить отверстие на диаметр 26, выдерживая размер 27 | | ||
3.2.6 | Фрезеровать поверхность на диаметр 28, выдерживая размеры 29,30,31 | ![]() |
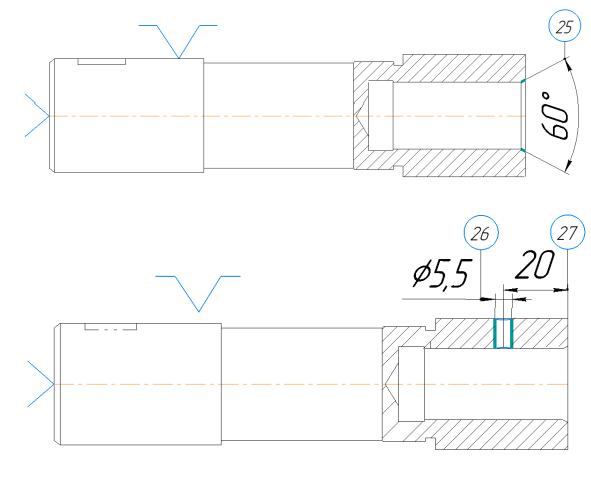
-
Подготовка производства-
Расчет и назначение режимов резания
-
Режимы резания определяются глубиной резания t, мм; подачей на оборот So, мм/об и скоростью резания V, м/мин.
Режимы резания оказывают влияние на точность и качество обработанной поверхности, производительность и себестоимость обработки.
В курсовом проекте необходимо рассчитать для одной из операций:
глубину, подачу и скорость резания по формулам теории резания; суммарную силу резания и эффективную мощность электродвигателя
главного привода станка.
На все остальные операции техпроцесса режимы резания назначают по нормативам предприятий или справочникам [16, 21, 27].
Исходными данными при выборе режимов резания являются:
сведения о заготовке (вид заготовки, материал и его характеристика, величина припусков, состояние поверхностного слоя);
данные об обрабатываемой детали (форма, размеры, допуски на обработку, требования к состоянию поверхностного слоя, к шероховатости);
данные о режущем инструменте (типоразмер, материал режущей части, геометрические параметры);
паспортные данные станков (техническая характеристика).
Таким образом, режим резания устанавливают исходя из особенностей обрабатываемой детали, характеристики режущего инструмента и станка.
В первую очередь устанавливают глубину резания t. При однопроходной обработке на настроенном станке глубина резания равна припуску. При многопроходной глубина резания на первом рабочем ходе берется максимальная, на последующем – уменьшается с целью достижения заданной точности. Обычно на черновом этапе удаляется до 70 % припуска, а на чистовые этапы оставляют не более 30 %.
Подача So назначается максимально допустимой [26]. При черновой обработке ее величина ограничивается жесткостью и способом крепления
обрабатываемой детали, прочностью и жесткостью инструмента, прочностью механизма подачи станка.
При чистовой обработке S определяется заданной точностью