Файл: Разработка технологии сборки и сварки кожухотрубчатого теплообменника этанолвода с внутренним диаметром 2390мм, длиной цилиндрической части 6450 мм, толщиной стенки 52мм из биметалла 10Х2М1 05Х20Н32Т.docx
ВУЗ: Не указан
Категория: Не указан
Дисциплина: Не указана
Добавлен: 11.04.2024
Просмотров: 186
Скачиваний: 6
ВНИМАНИЕ! Если данный файл нарушает Ваши авторские права, то обязательно сообщите нам.
4.3 Выбор сварочного оборудования и источников питания
В качестве сварочного оборудования для автоматической сварки под флюсом используем сварочную головку ESAB A2S Mini Master (таблица 4.10) и сварочный трактор А2 Multitrac с блоком РЕК (таблица 4.5). Сварочная головка расположена на сварочном центре ESAB 460M.
Таблица 4.5 – Техническая характеристика сварочной головки ESAB A2S Mini Master
Параметр | Величина |
Напряжение питания | 42 |
Допустимый ток (ПВ100%), постоянный ток, А | 800 |
Максимальная нагрузка, А | 1000 |
Макс. скорость подачи, м/мин | 9 |
Макс. масса сварочной проволоки, кг | 30 |
Таблица 4.6 – Технические характеристики сварочного трактора А2 Multitrac с блоком РЕК
Макс. ток ПВ 100%, А | 800 |
Скорость подачи проволоки, м/мин | 9 |
Скорость перемещения, м/мин | 0,1-1,7 |
Диаметр сварочной проволоки, мм | 1,-4,0 |
Масса, кг | 47 |
Габаритные размеры, ДхШхВ, мм | 750х589х937 |
Таблица 4.7 – Технические характеристики сварочного центра ESAB 460M.
Параметр | Значение |
Колонна | |
Эффективный рабочий диапазон, м | 5 |
Макс. Высота влета стрелы, мм | 5950 |
С использованием передвижной тележки мин., мм | 950 |
Макс. общая высота при использовании передвижной тележки, мм | 7275 |
Скорость подъёма | 2,0 |
Стрела | |
Вылет, макс/мин, мм | 5715/715 |
Допустимые нагрузки, общая макс/на один конец, кг | 1050/450 |
Диаметр поперечного сечения, мм | 630 |
Скорость перемещения, м/мин | 2,0 |
Выберем сварочный источник питания для атоматической сварки под флюсом: Сварочный выпрямитель Kjellberg GTH 1402 - мощный источник питания, предназначенный для автоматической и полуавтоматической сварки под слоем флюса.
Поставляет ток до 1400А. Относится к источникам тиристорного типа.
Источник питания состоит из силового трехфазного трансформатора, который подключен к трехфазному выпрямителю и сглаживающему дросселю, схемы управления тиристорами. Тиристорный выпрямительный блок является основным элементам, который используется в качестве силы тока.
Сварочный выпрямитель GTH 1402 имеет жесткую вольт-амперную характеристику. Управляющие импульсы, подаваемые на тиристорный блок, настраивают источник питания на заданный режим непрерывной работы, а также формируют заданную вольт-амперную характеристику.
Мощный источник питания предназначен для крупного промышленного производства. Он легко выполнит любые производственные и технологические процессы. Сварочный выпрямитель будет незаменим в судостроении, автомобилестроении, а также в машиностроении.
Таблица 4.8 – Технические характеристики сварочного выпрямителя Kjellberg GTH 1402
Напряжение сети | 380В |
Ток в режиме ММА: При ПВ 100% | 100 - 1400 А 1200 А |
Масса | 440 кг |
Габаритные размеры | 1100x820x1000мм |
Приварку штуцеров и люков, опоры к корпусу аппарата и сварка самой опоры выполняем полуавтоматом ESAB Warrior 500i в смеси газов. Технические характеристики полуавтомата приведены в таблице 4.9.
Таблица 4.9 – Технические данные полуавтомата ESAB Warrior 500i
Напряжение в питающей сети, В | 380 |
Частота питающей сети, Гц | 50 |
Номинальный сварочный ток, при ПВ=100%, А | 400 |
Максимальный ток, А | 500 |
Диаметр электродной проволоки, мм | 0,8-1,6 |
Расход газа, л/мин | 8-20 |
Продолжение таблицы 4.10
Напряжение холостого хода, В | 54 |
Масса, кг | 11,5 |
4.4 Сварка продольных и кольцевых стыков аппарата
Сварку продольных и кольцевых стыков корпуса аппарата и днищ будем производить автоматической сваркой под флюсом на специальной установке. В качестве сварочного оборудования используем сварочную головку ESAB A2S Mini Master установленной на сварочной колонне ESAB 460M и сварочный трактор А2 Multitrac с блоком РЕК для приварки последнего днища к корпусу аппарата. В соответствии с ГОСТ 16098-80 выбираем разделку С14. Сварка осуществляется с предварительным и сопутствующим подогревом основного и переходного слоя 200-250оС. Межваликовая температура не более 100оС. Термическая обработка не позднее 72ч после окончания сварки основного и переходного слоев, при условии проведения термического отдыха 300-350 оС.
Загрузка в печь при температуре не более 350 оС. Скорость нагрева от 420°С до 620±15 °С - 65±10 °С/час. Температура выдержки - 620±15 °С. Время выдержки при 620±15 °С - 2 часа 30 мин. Скорость охлаждения от 620±15 до 420 °С - 65±10 °С/час, далее на воздухе.
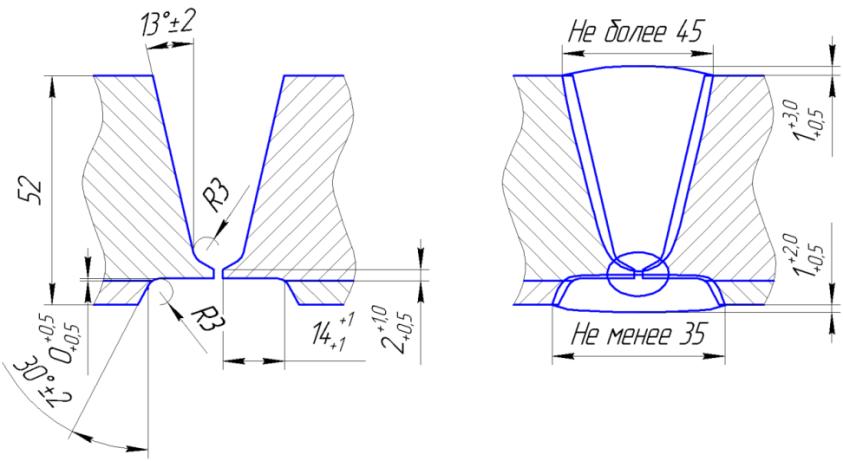
Рисунок 4.5 – форма подготовки кромок и сварного соединения С14 по ГОСТ 16098-80.
4.5 Приварка штуцеров и люков к корпусу аппарата
Для приварки штуцеров и люков используем сварочный полуавтомат ESAB Warrior 500i . Для приварки данных изделий выбран способ сварки в среде инертных газов плавящимся электродом. В соответствии с ГОСТ 16098-80 разделка кромок Т2, рисунок 4.6. Диаметр сварочной проволоки – 1,2 мм. Сварочный ток в диапазоне от 230 до 330 А. Напряжение на дуге в диапазоне от 29 до 34 В. Сварка осуществляется с предварительным и сопутствующим подогревом основного и переходного слоя 200-250оС. Межваликовая температура не более 100оС. Термическая обработка не позднее 72ч после окончания сварки основного и переходного слоев, при условии проведения термического отдыха 300-350 оС.
Загрузка в печь при температуре не более 350 оС. Скорость нагрева от 420°С до 620±15 °С - 65±10 °С/час. Температура выдержки - 620±15 °С. Время выдержки при 620±15 °С - 2 часа 30 мин. Скорость охлаждения от 620±15 до 420 °С - 65±10 °С/час, далее на воздухе.
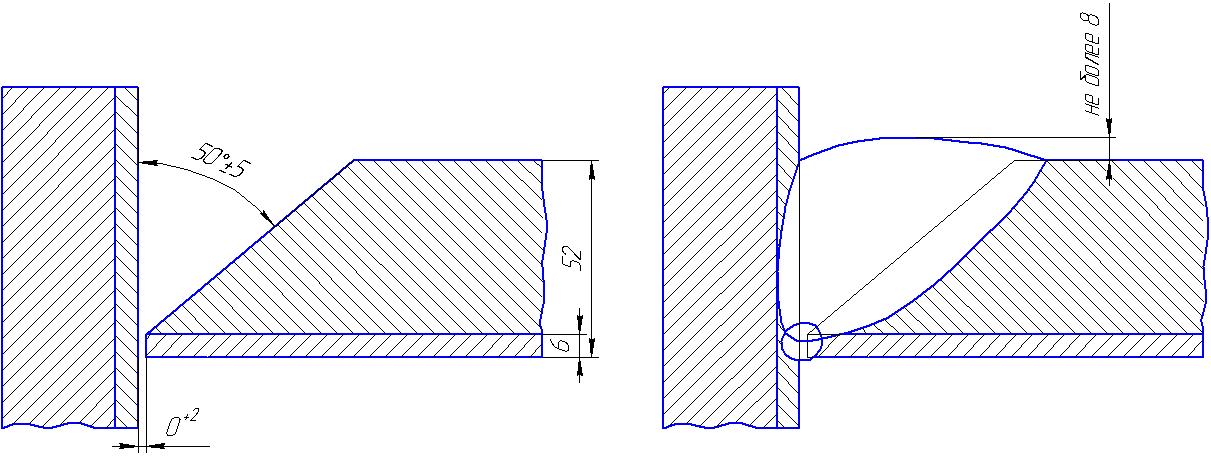
Рисунок 4.6 – Форма подготовки кромок и сварного соединения Т2 по ГОСТ 16098-80, где S1 – толщина стенки штуцера
4.6 Приварка опор к корпусу аппарата
Для приварки аппарата к опоре используем ESAB Warrior 500i . Для данной операции выбран способ сварки в среде инертных газов плавящимся электродом, в связи с необходимостью получения высокого качества сварного соединения при сварке на монтаже. Выбор разделки выбираем по ГОСТ 14771-76 H1. Диаметр сварочной проволоки – 1,2 мм. Сварочный ток в диапазоне от 250 до 350 А. Напряжение на дуге в диапазоне от 29 до 37 В. Сварка осуществляется с предварительным и сопутствующим подогревом основного и переходного слоя 200-250оС. Межваликовая температура не более 100оС. Термическая обработка не позднее 72ч после окончания сварки основного и переходного слоев, при условии проведения термического отдыха 300-350 оС.
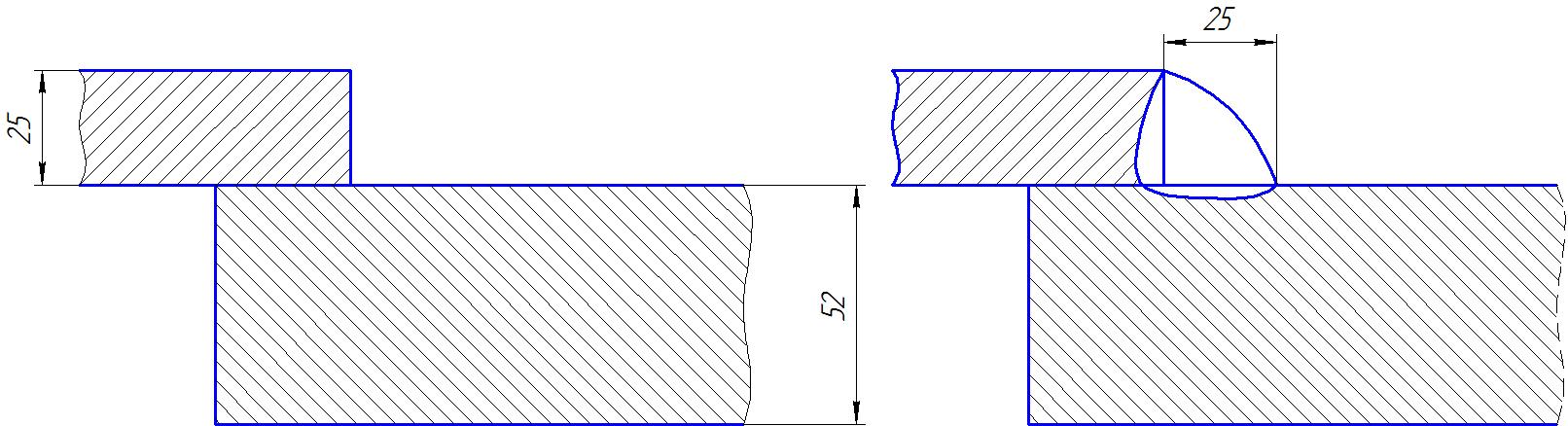
Рисунок 4.7 – Конструктивные элементы подготовленных кромок и шва сварного соединения типа H1 по ГОСТ 14771-76 (Приварка подкладных колец к корпусу аппарата)
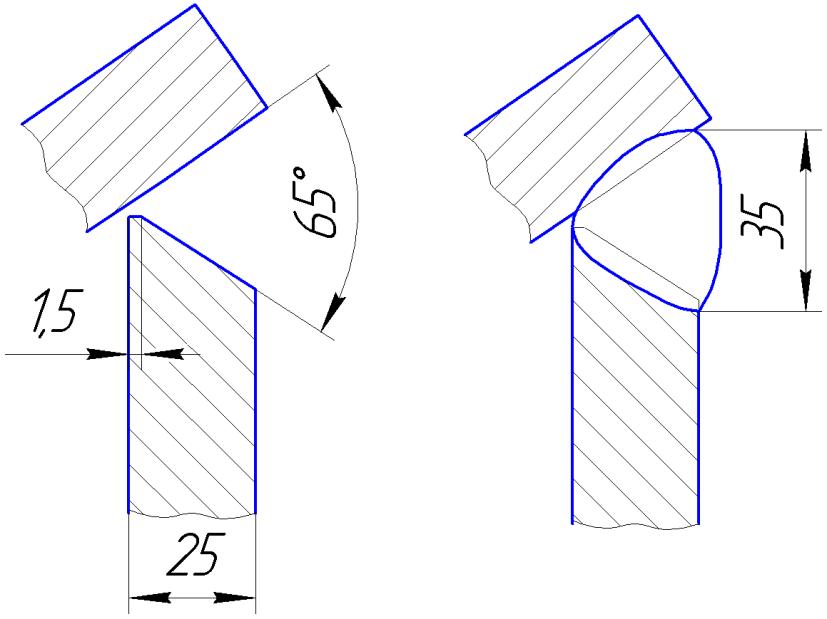
Рисунок 4.8 – Конструктивные элементы подготовленных кромок и шва сварного соединения (Приварка подкладных колец к ребрам опоры)
Термическая обработка аппарата после приварки опоры к корпусу:
Загрузка в печь при температуре не более 350 оС. Скорость нагрева от 420°С до 620±15 °С - 65±10 °С/час. Температура выдержки - 620±15 °С. Время выдержки при 620±15 °С - 2 часа 30 мин. Скорость охлаждения от 620±15 до 420 °С - 65±10 °С/час, далее на воздухе.
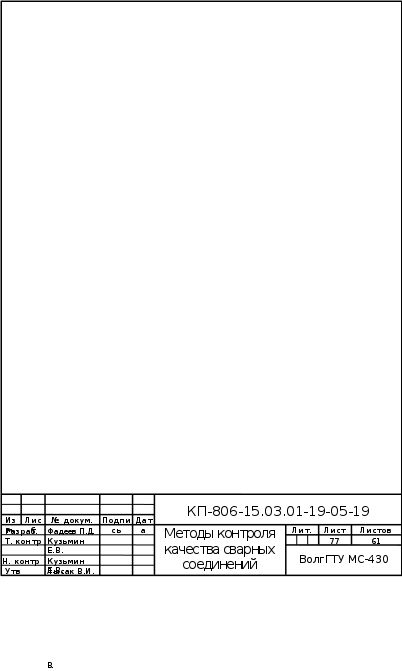
После сварки всего аппарата необходимо произвести полный контроль сварных швов на выявление дефектов для этого необходимо назначить: визуальный контроль и измерение сварных швов; механические испытания; металлографические испытания; стилоскопирование сварных соединений; ультразвуковой контроль; гидравлические испытания на прочность и герметичность.
5.1. Визуальный контроль и измерение сварных швов
Визуально и измерительным контролем проверяют качество подготовки и сборки заготовок под наплавку, качество выполнения швов в процессе наплавки и качество готовых сварных швов. Обычно внешним осмотром контролируют все сварные изделия независимо от применения других видов контроля. Порядок проведения визуального и измерительного контроля согласно РД 03-606-03.
Проводят на следующих стадиях:
–входного контроля;
–изготовления деталей, сборочных единиц и изделий;
–подготовки деталей и сборочных единиц к сборке;
–подготовки деталей и сборочных единиц к сварке;
–сборки деталей и сборочных единиц под сварку;
–процесса сварки;
–контроля готовых сварных соединений и наплавок;
–исправления дефектных участков в материале и сварных соединениях (наплавках);
–оценки состояния материала и сварных соединений в процессе эксплуатации технических устройств и сооружений, в том числе по истечении установленного срока их эксплуатации.
5.2 Механические испытания
Механические испытания определяют прочность и надежность работы сварной конструкции. Механическим испытаниям в сосудах должны подвергаться стыковые сварные соединения.
Прочность соединения слоев двухслойных листов проверяют испытанием на срез с определением сопротивления срезу по плоскости соприкосновения основного и коррозионно-стойкого слоев.
Механические испытания предусматривают статические и динамические (ударные) испытания при нормальной температуре (20̊С).
Основными методами определения характеристик механических свойств сварного соединения в целом и его отдельных участков, а также наплавленного металла являются:
–испытание металла различных участков сварного соединения и наплавленного металла на статическое растяжение;
–испытание металла различных участков сварного соединения и наплавленного металла на ударный изгиб (на надрезанных образцах);
–испытание сварного соединения и наплавленного металла на (технологическая проба с наплавленным валиком) статический изгиб (загиб);
–измерение твердости различных участков сварного соединения и наплавленного металла.
Испытания на растяжение, изгиб, ударный изгиб из сварного соединения толщиной 50 мм и более должны проводиться согласно требованиям РД 26-11-08.
Проведение испытаний на статическое растяжение
Испытание на статическое растяжение при пониженной, комнатной и повышенной температурах проводится для определения следующих характеристик механических свойств материалов:
–предела текучести (физического) sТ, кгс/мм2