Файл: Разработка технологии сборки и сварки кожухотрубчатого теплообменника этанолвода с внутренним диаметром 2390мм, длиной цилиндрической части 6450 мм, толщиной стенки 52мм из биметалла 10Х2М1 05Х20Н32Т.docx
ВУЗ: Не указан
Категория: Не указан
Дисциплина: Не указана
Добавлен: 11.04.2024
Просмотров: 206
Скачиваний: 6
ВНИМАНИЕ! Если данный файл нарушает Ваши авторские права, то обязательно сообщите нам.
Вальцевание листового материала может производиться как в холодном, так и в горячем состоянии в зависимости от свойств материала и возникающих при этом деформаций. При вальцевании для определения деформаций используют зависимость:

Если это условие выполняется, то деформации в растянутой зоне больше 2,5% и вальцевать следует в горячем состоянии.
Рассчитаем ожидаемую деформацию для обечаек корпуса:

Таким образом, деформации превышают допустимые и вальцевать следует в горячем состоянии при температуре 250 ˚C.
2.8 Формирование днища
Готовые к сварке части днищ получаются после вырезки их из проката и гибки. Гибку проводят двумя способами: штамповкой и фланжированием.
Штамповку применяют для гибки перлитной стали толщиной от 10-13 мм, как правило в холодном состоянии.
Фланжирование – это комбинированная операция штамповки центральной части заготовки и обкатка роликами периферийной её части для образования эллиптических или коробовых днищ. Фланжирование производится на ротационных прессах и только в горячем состоянии при температуре заготовки 1100-1200оС. Нагретая заготовка манипулятором подаётся на матрицу пресса, центрируется и с помощью пуансона штампуется центральная часть днища, затем заготовка начинает вращение и осуществляется формовка переферийной части днища.
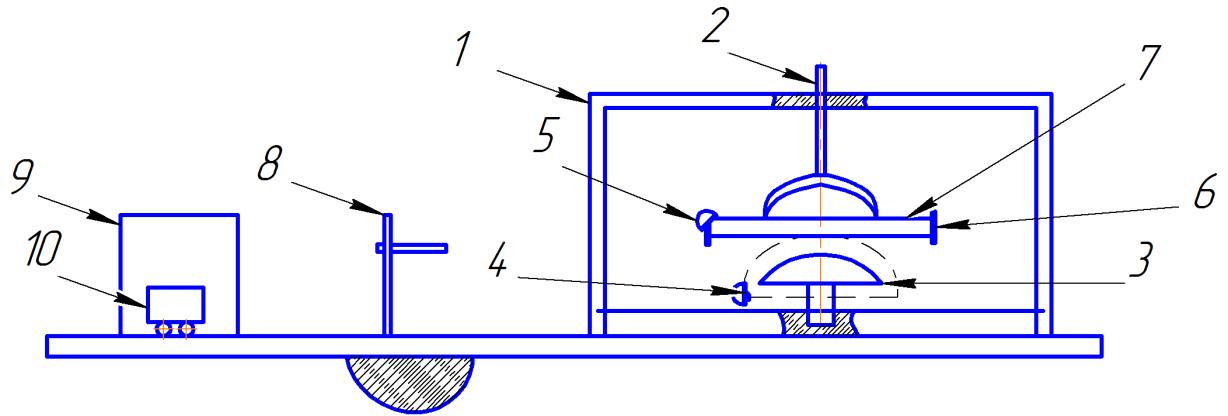
Рисунок 2.10 – Схема ротационного пресса
1 – Портал ротационного пресса 2 – Пуансон с гидроцилиндром 3 – Матрица с приводом вращения 4 – Опорный ролик 5 – Формирующий ролик. 6 – Центрирующие ролики 7 – Заготовка днища 8 – Манипулятор 9 – Печь 10 – Под печи для подачи заготовки.
2.9 Подготовка кромок под сварку
Продольные и кольцевые стыки обечаек, а также стыки днищ будут свариваться автоматической дуговой сваркой под флюсом. Для сварки толщиной 52 мм наиболее предпочтительна по ГОСТ 16098-80 разделка С14. Параметры разделки кромок с указанием допусков приведены на рисунке 13.
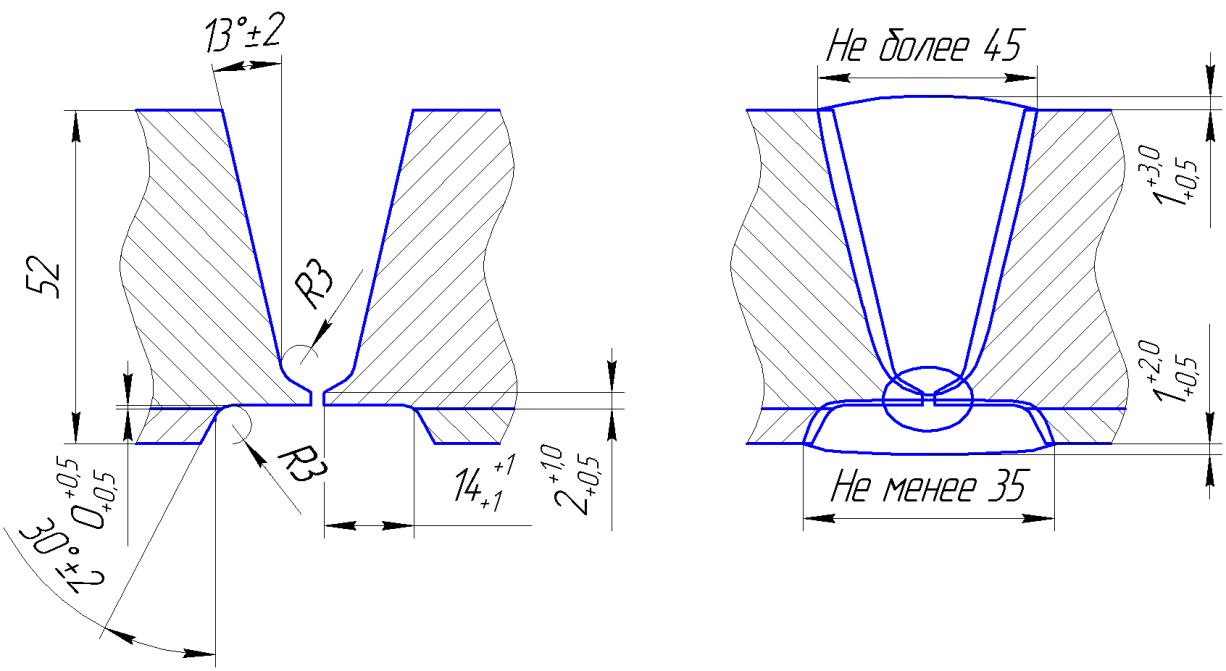
Рисунок 2.11 – Конструктивные элементы подготовленных кромок свариваемых деталей и сварного шва.
Разделка кромок позволяет вести сварку отдельными слоями небольшого сечения, что улучшает структуру сварного соединения и уменьшает возникновение сварочных напряжений и деформаций.
Зазор, правильно установленный перед сваркой, позволяет обеспечить полный провар по сечению соединения при наложении первого (корневого) слоя шва, если подобран соответствующий режим сварки.
Длиной скоса листа регулируется плавный переход от толстой свариваемой детали к более тонкой, устраняются концентраторы напряжений в сварных конструкциях.
Притупление кромок выполняется для обеспечения устойчивого ведения процесса сварки при выполнении корневого слоя шва. Отсутствие притупления способствует образованию прожогов при сварке.
2.10 Требования к изготовлению
Основные требования к изготовлению по ГОСТ 31842-2012 «Нефтяная и газовая промышленность. Теплообменники кожухотрубчатые» и ГОСТ 34347-2017 «Сосуды и аппараты стальные сварные»
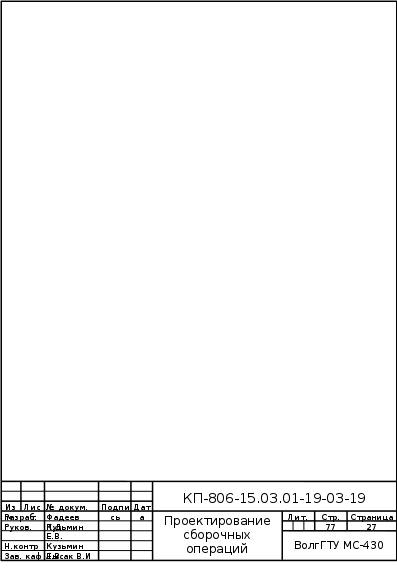
Сборочная операция – это операция для обеспечения точного сопряжения собираемых деталей перед сваркой, исключающая появление изгибающих моментов, не учитываемых расчетом. Для сосудов, работающих под давлением, имеющих эллиптические днища, ответственными за прочность конструкции являются продольные стыки обечаек и швы заготовок днищ.
Технологический процесс сборки независимо от способа производства должен удовлетворять требованиям: соблюдение требуемой последовательности сборки и сварки; применение необходимого инструмента и приспособлений, повышающих производительность труда; проведение пооперационного контроля качества сборки; соблюдение допусков на размеры конструкции; соблюдение правил техники безопасности.
3.1 Сборка продольных стыков обечаек
Сборку продольных стыков обечаек будем производить на роликовом стенде HGZ 20(Рисунок 3.2). При сварочных работах на изделиях цилиндрической формы, часто возникает необходимость создания сварного шва вдоль всей окружности. При больших размерах подобных изделий (например, цистерны или котлы), появляется необходимость их вращения в процессе обработки. Роликовые опоры с плавной регулировкой решают эту проблему, позволяя придавать плавное вращательное движение с постоянной скоростью цилиндрическим изделиям практически любого размера.
При использовании роликов изделие будет надежно закреплено и, вместе с тем, оно будет вращаться с удобной для работы скоростью без усилий со стороны работника. Плавное регулирование скорости позволяет совершать различные работы без остановки и перенастройки роликов. Также это устройство способно работать в паре с автоматической сваркой, так как обеспечивает скорость вращения, которая подойдет для автоматического сварочного аппарата любого типа. Технические данные стенда приведены в таблице 3.1.
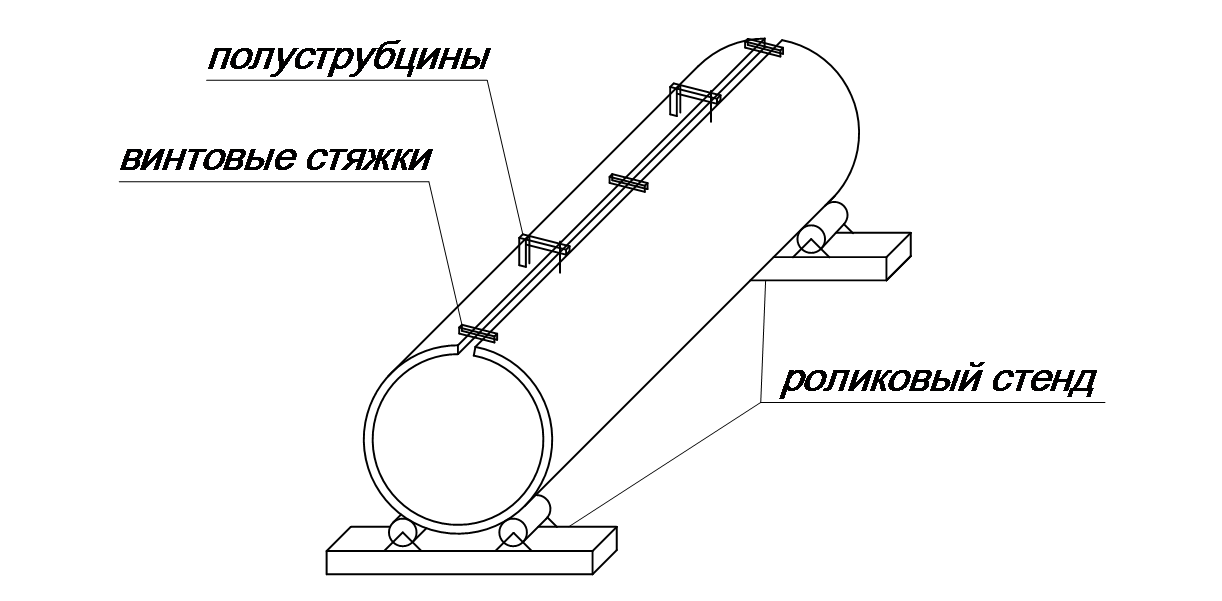
Рисунок 3.1 – Схема сборки обечайки по продольному стыку
1 – Собираемая обечайка 2 – Стяжка 3 – Полуструбцина
Таблица 3.1 – Техническая характеристика роликового стенда HGZ 20
Максимальная грузоподъемность, кг | 20000 |
Диаметр свариваемых изделий, мм | 700-5000 |
Скорость вращения, м/час | 6-60 |
Напряжение питания, В | 380 |
Сборку производим в следующей последовательности:
Обечайка устанавливается на роликовый стенд
Установим требуемый зазор в стыке при помощи винтовых стяжек. Стяжки разместим по обеим сторонам обечайки и по центру с шагом 450 мм между стяжкой и полуструбциной, зазор в стыке b=0+2 мм. Величину зазора в стыке будем контролировать с помощью специальных щупов или калиброванной закаленной стальной проволоки.
Выставив минимальное превышение кромок в стыке, не более допустимого при помощи полуструбцин, расположенных в местах, где превышение кромок максимально. Максимально допустимое превышение кромок составляет 2,2 мм.
Произведем прихватку стыка ESAB Warrior 500i .
Приварим вводные, выводные планки и контрольную пластину.
Удаляем полуструбцины и винтовые стяжки пневмозубилом, места их установки зачищаем. Далее заготовку подаем на сварку продольного стыка.
3.2 Сборка продольных стыков заготовок эллиптического днища
Сборка и сварка заготовок под эллиптические днища происходит на сборочных плитах. Сборочная плита (рисунок 3.2) представляет собой ровную площадку определённого размера, на которой сделаны продольные и поперечные пазы на расстоянии от 100 до 500 мм. В пазах перемещаются специальные сборочные приспособления, которые могут быть закреплены в определённом месте сборочной плиты винтовыми зажимами, предотвращающими самопроизвольное перемещение приспособлений на плите. В качестве универсальных сборочных приспособлений применяются упоры струбцины, прижимы, призмы и т.д. Данные приспособления устанавливаются на плите согласно геометрической схеме собираемого изделия, затем осуществляется сборка изделия и после этого осуществляется сварка изделия с помощью выбранного способа сварки.
В данной работе сборку и сварку днища аппарата будем производить на сборочной плите с применением струбцин по следующей схеме (рисунок 3.3).
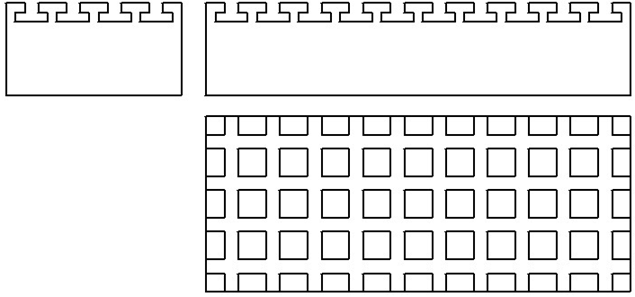
Рисунок 3.2 – Сборочная плита
Вырезанные части заготовки днища 1 с техническими планками 2 собираются на сборочной плите 3 и прижимаются к ней струбцинами 4 после чего происходит простановка прихваток каждые 300 мм. Прихватки проставляются аппаратом для сварки плавящимся электродом в среде защитных газов ESAB Warrior 500i. Конструкция корпуса с улучшенным охлаждением силовых элементов и надёжной защитой электронных компонентов от загрязнения. Технические характеристики которого приведены в таблице 3.2, дальнейшее заполнение разделки шва указано в главе 4 данной работы. После сварки и удаления технических планок заготовка днища перемещается для операции штамповки.
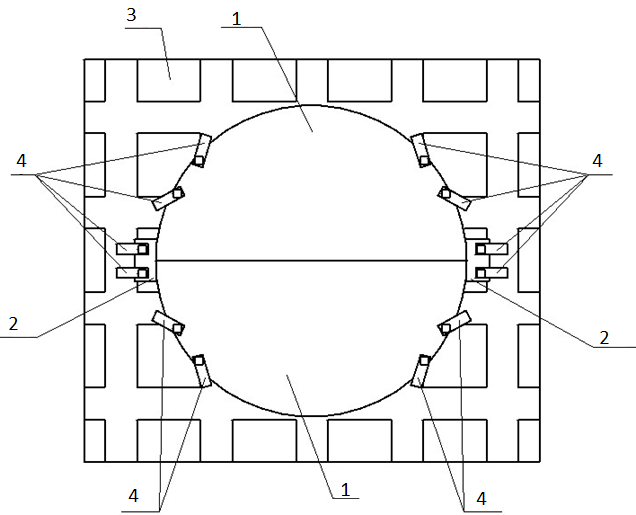
Рисунок 3.3 – Схема сборки заготовки днища
3.3 Сборка обечаек между собой в корпус
Для сборки обечаек в первый корпус воспользуемся роликовой опорой HGZ 20, технические характеристики которой приведены выше. Благодаря использованию данной опоры отсутствует необходимость перемещения собранных, но не сваренных корпусов по цеху, что существенно экономит пространство, а также повышает производительность. Данная опора имеет ролики для выравнивания двух собираемых секций между собой, что повышает точность и качество сборки. После выравнивания обечаек между собой происходит их сближение на расстояние, которое равно величине зазора по ГОСТ на выбранный способ сварки. Далее для закрепления сборки ставятся прихватки каждые 300 мм с помощью аппарата ESAB Warrior 500i. После постановки прихваток на том же стенде происходит сварка кольцевого шва.