Файл: Разработка технологии сборки и сварки кожухотрубчатого теплообменника этанолвода с внутренним диаметром 2390мм, длиной цилиндрической части 6450 мм, толщиной стенки 52мм из биметалла 10Х2М1 05Х20Н32Т.docx
ВУЗ: Не указан
Категория: Не указан
Дисциплина: Не указана
Добавлен: 11.04.2024
Просмотров: 189
Скачиваний: 6
ВНИМАНИЕ! Если данный файл нарушает Ваши авторские права, то обязательно сообщите нам.
Примем А=20000А·м/ч, тогда:

5) Определим величину погонной энергии, вносимой в шов:

где ηи = 0,95 – эффективный к.п.д. нагрева.
6) Коэффициент формы провара:

где

при

При обратной полярности:

Для механизированной сварки

0.8 – 4. При меньшем значении будут получаться швы, склонные к образованию ГТ, при больших – слишком широкие швы с малой глубиной провара, что нерационально с точки зрения использования теплоты дуги и приводит к увеличенным деформациям.
7) Определим глубину провара Н:

8) Ширина шва е:

9) Примем вылет электрода:

10) Определим коэффициент наплавки:

При сварке под флюсом ввиду незначительных потерь электродного металла с достаточной для практических расчётов степенью точности можно принять, что коэффициент наплавки αн равен коэффициенту расплавления αр.



При сварке постоянным током обратной полярности принимаем:


Тогда:

12) Определим площадь наплавленного металла:

Удельный вес металла принимаем:

13) Высота валика:

14) Общая высота шва С:

15) Коэффициент формы усиления:
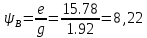
Для хорошо сформированных швов

Далее графически определяем количество заполняющих проходов. Для этого чертим, форму корневого валика используя значения, полученные выше и помещаем его на разделку, затем замеряем, заштрихованную площадь и с помощью формулы количество заполняющих проходов n округляя до целого числа в большую сторону

где F - площадь наплавленного металла наплавленного для разделки
Fн - площадь наплавленного металла рассчитанного по формуле
Подставив числовые значения в формулу, получим:
Для корневого валика – 1; для заполняющего слоя – 24; для переходного слоя – 5; для плакирующего слоя – 6.
После получения количества проходов, чертим форму заполняющего валика, используя значения полученные выше. И располагаем 27 валиков так, чтобы обеспечивать перекрытие предыдущих не менее 60%.
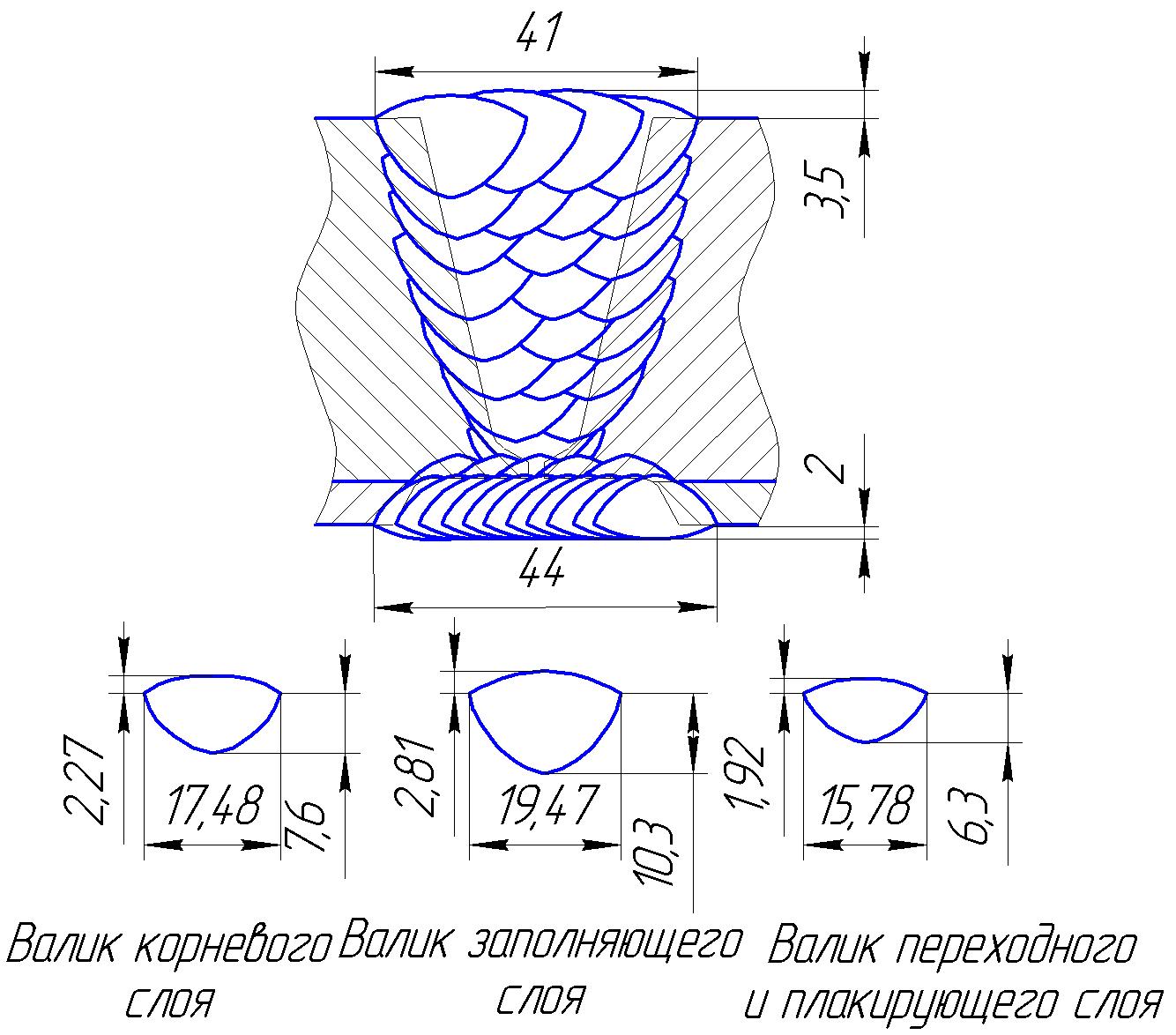
Рисунок 4.2 – количество проходов при сварке
Определим химический состав металла шва.
Содержание рассматриваемого элемента в металле шва определяется на основании правила смешения по формуле:

где |х|ш, |х|ом, |х|э – концентрация рассматриваемого элемента в металле шва, основном и электродном металле; γо – доля участия основного металла в формировании шва, определяется по формуле:

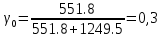
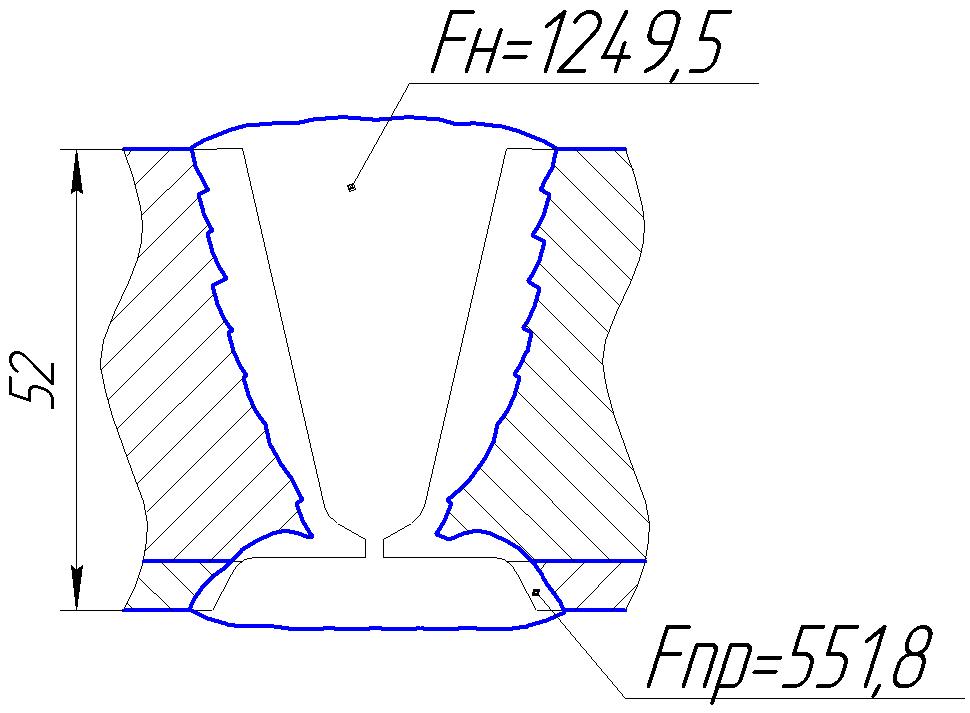
Рисунок 4.3 – наплавленный и проплавленный металл шва.
где Fн – площадь наплавленного металла,
Fпр – площадь провара.










Шов переходного слоя
Fом=75 мм2-площадь основного металла;
Fш=39,48 мм2-площадь шва основного металла;
Fпл=12 мм2- площадь плакирующего металла в переходном шве;

Fпл2=57,94 площадь плакирующего слоя в плакирующем шве.
γом=

γш=

γпл=

γэ.п.=1-γом-- γш- γпл =0,51.









Шов плакирующего слоя
γпер=

=0,56
γпл2=

γэ.п.=1- γпер - γпл2=0,33.









Финальным этапом является определение скорости охлаждения металла ωохл (˚С/с) при выбранном режиме сварки по формуле (4.18).

3,6 < 15, следовательно закалочные структуры не образуются.
ωохл – мгновенная скорость охлаждения при температуре Тm, ˚С/с;
λ = 18 – коэффициент теплопроводности, Вт/м2∙˚С;
Т0 – начальная температура изделия, ˚С;
qn – погонная энергия (Дж/м).
Рассчитанные режимы сварки обеспечивают необходимую скорость охлаждения, которая попадает в допустимый интервал скоростей охлаждения.
Расчет эквивалента Ni и эквивалента Cr
Рассчитаем эквивалентное содержание никеля и хрома плакирующего слоя:



Рассчитаем эквивалентное содержание никеля и хрома для электродной проволоки OK Autrod 385 для сварки плакирующего слоя:
Crэкв=21,5+2+1,5·0,5 =24,25;
Niэкв=26+30·0,025+0,5·2=27,75;


По диаграмме Шеффлера определяем предположительную структуру металла шва:
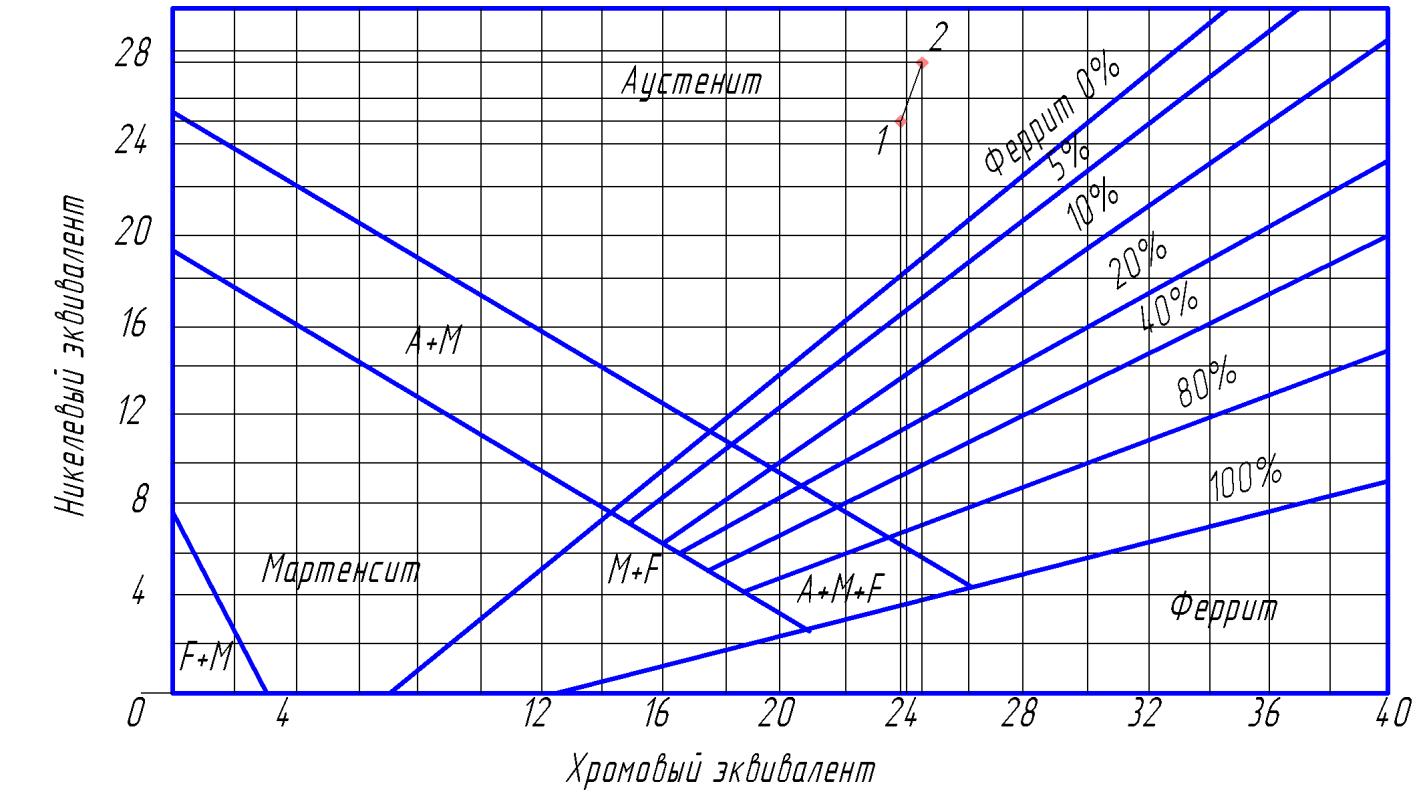
1 – эквивалентное содержание Ni и Cr для плакирующего слоя, 2 - эквивалентное содержание Ni и Cr электродной проволоки
Рисунок 4.4 – Диаграмма Шеффлера