Файл: Разработка технологии сборки и сварки кожухотрубчатого теплообменника этанолвода с внутренним диаметром 2390мм, длиной цилиндрической части 6450 мм, толщиной стенки 52мм из биметалла 10Х2М1 05Х20Н32Т.docx
ВУЗ: Не указан
Категория: Не указан
Дисциплина: Не указана
Добавлен: 11.04.2024
Просмотров: 191
Скачиваний: 6
ВНИМАНИЕ! Если данный файл нарушает Ваши авторские права, то обязательно сообщите нам.
3.4 Сборка корпуса с днищем
Установим днище на ложемент и зафиксируем его при помощи 12 пневмоцилиндров, которые захватывают и удерживают его. При сборке эллиптических днищ с корпусом согласно ГОСТ 34347-2017, сварные швы днищ не должны совпадать с продольными швами корпуса и отстоять друг от друга на величину не менее трех толщин корпуса или днища, но не менее 100 мм.
Сборку первого днища будем производить по схеме, представленной на рисунке 3.5. Днище 2 устанавливается на ложемент 1, далее фиксируется с помощью пневмоцилиндров 6, затем с помощью поворотного механизма 3 стыкуется корпусом 5 установленным на роликовой опоре 4, на расстоянии равным зазору между свариваемыми кромками выбранного способа сварки по ГОСТ. Далее ставятся прихватки(5штук, с шагом , по схеме, указанной на рисунке 3.5., при этом контролируется высота превышения кромок, которая не должна быть больше 3,45 мм. После данных операций днище приваривается к цилиндрической части корпуса по той же технологии, по которой производилась сварка цилиндрической части корпуса. После приварки первого днища производится разметка и вырезка отверстий под люки и штуцера, а также их последующая сварка.
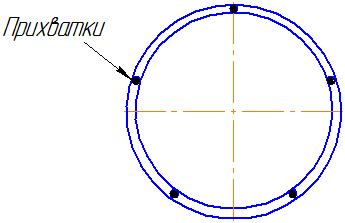
Рисунок 3.4 – Последовательность нанесения прихваток при сборке кольцевого стыка
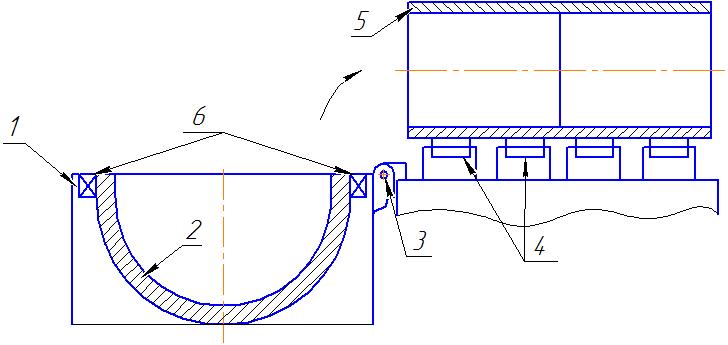
Рисунок 3.5 – Схема сборки первого днища с корпусом
3.5 Разметка и вырезка отверстий под штуцера и люки
Задачей разметки является определение координаты центра отверстия штуцера или люка. Как правило, используется два способа разметки: с помощью лазера, с помощью мелового шнура.
Будем использовать способ разметки с помощью лазера. Принцип разметки этими способами следующий. Выбирается базовая плоскость, как правило, кольцевой стык днища по оси шва или плоскость разъема корпуса и второго днища. Намечается базовая линия, за которую принимается продольная линия, на которой располагается максимальное количество штуцеров и люков, отмеряют от базовой плоскости расстояние, на котором расположена плоскость, в которой находится отверстие. После чего определяется угол, под которым располагается в этой плоскости искомый центр отверстия, относительно базовой линии. В месте найденного центра производят насечку керном и сверлят отверстие (либо вырезают, в зависимости от диаметра).
При лазерной разметке (рисунок 3.6) на горизонтальной площадке устанавливается лазерный генератор, который дает прямой жесткий луч вдоль корпуса, на пути луча ставится отражатель, который одновременно с фиксацией точки, где расположен штуцер, может фиксировать плоскость внутри корпуса, если на этой плоскости имеется штуцер или люк. Отражатель также имеет световой лимб с указателем углов, под которым располагается центр отверстия. Разметка штуцеров и люков, располагаемых на днище, как правило, производится до установки его в корпус. Перемещая отражатель на требуемое расстояние, определяют центры всех штуцеров и люков.
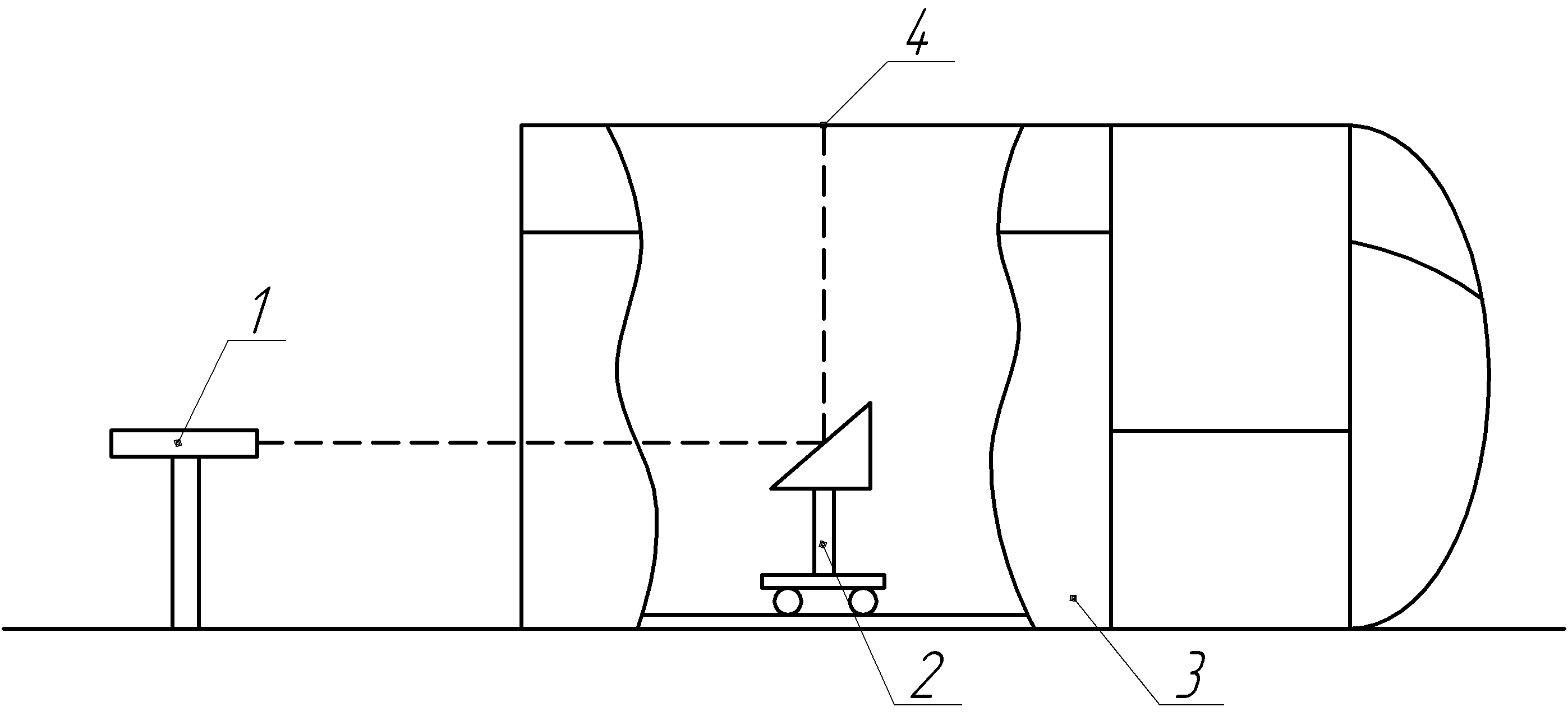
Рисунок 3.6 – Способ разметки корпуса под установку штуцеров и люков
1 – лазерный генератор; 2 – поворотный отражатель с лимбом; 3 – размечаемый корпус; 4 – центр отверстия под люк или штуцер.
После определения всех центров, осуществляется их сверление насквозь сверлом диаметром 6…12 мм.
Одновременно с вырезкой отверстий возможна подготовка кромок под сварку с обязательным припуском на механическую обработку.
Отклонения по диаметрам отверстий для штуцеров и люков не должны быть более: +1,5-0,5 для отверстий Ø до 150 мм; +2,0-0,5 для Ø 150 – 300 мм и +3,0-0,5 мм для Ø > 300 мм.
После вырезки отверстий под штуцера и люки необходимо произвести подготовку кромок.
3.6 Установка штуцеров и люков
Для установки штуцеров будем использовать схему с заглублением штуцера в корпус аппарата
Последовательность установки следующая:
1. Устанавливаем штуцер или люк согласно принятой для него схеме (рисунок 3.7).
2. Выверяем перпендикулярность оси люка или штуцера относительно корпуса при помощи угольника.
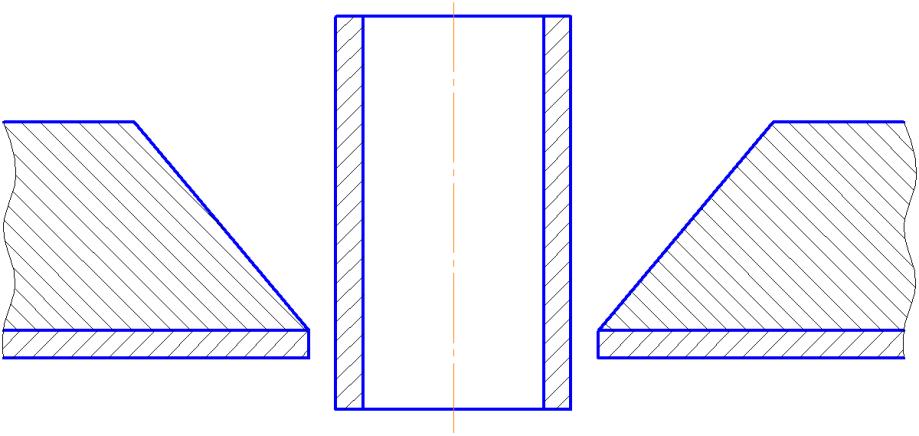
Рисунок 3.7 – Способ установки штуцеров в корпус аппарата (разделка кромок Т2 по 16098-80)
В соответствии с требованиями ГОСТ 34347-2017 выверяем позиционное отклонение осей штуцеров и люков (допускается не более ±10 мм) и отклонение по высоте (вылету) штуцеров (не должно быть более ±5 мм).
3. Производим прихватку штуцера или люка полуавтоматом ESAB Warrior 500i в смеси 80% Ar + 20% СО2 проволокой
Cв-04ХМА диаметром 1,6 мм с основным слоем на постоянном токе обратной полярности.
3.7 Сборка корпуса со вторым днищем
Сборку второго днища с корпусом осуществляют после установки всех штуцеров и люков. Сборка производится на том же оборудовании и в той же последовательности что и при сборке первого днища с корпусом.
3.8 Сборка опоры корпуса аппарата
Сборка опорных частей теплообменного аппарата производится на сборочно-сварочной плите с применением универсальных сборочно-сварочных приспособлений.
На сборочно-сварочную плиту устанавливается основание опоры. На основание устанавливается гнутая стойка опоры. Данные элементы закрепляются на сборочно-сварочной плите с помощью рычажных прижимов. Затем устанавливается и прихватывается к гнутой стойке подкладное кольцо. Далее устанавливаем и прихватываем ребра жесткости.
Производим прихватку основания со стойкой опоры, отводим рычажные прижимы и после проверки операции сборки, сборочная опора отправляется на сварку.
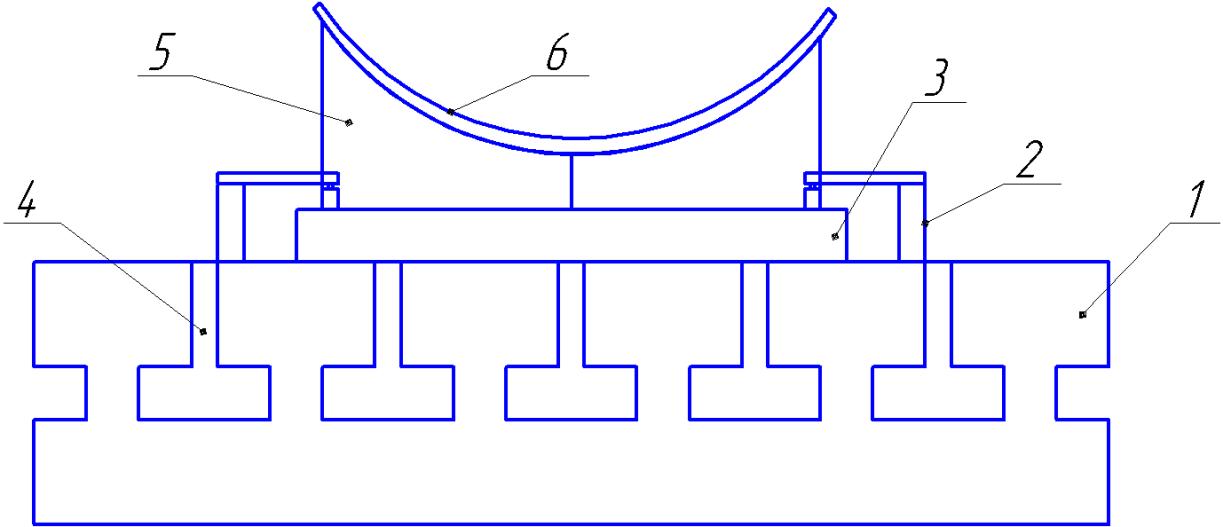
Рисунок 3.8 – Схема сборки опоры. 1 – сборочно-сварочная плита; 2 – рычажный прижим; 3 – основание опоры; 4 – ребра жесткости; 5 – гнутая стойка; 6 – подкладное кольцо
4. Проектирование сварочных операций
4.1 Выбор сварочных материалов
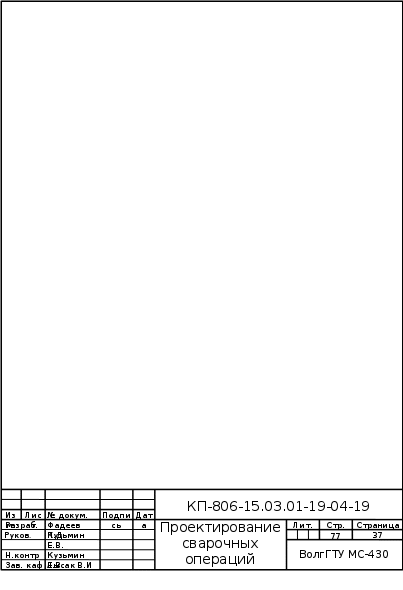
Сварочная проволока для автоматической сварки под слоем флюса– Cв-04ХМА Ø4мм;
Сварочная проволока для полуавтоматической сварки в смеси защитных газов – Cв-04ХМА Ø1,2;
Сварочная проволока для автоматической сварки под слоем флюса – OK Autrod 309L Ø4мм;
Сварочная проволока для полуавтоматической сварки в смеси защитных газов – OK Autrod 309L Ø1,2мм;
Сварочная проволока для автоматической сварки под слоем флюса – OK Autrod 385 Ø4мм;
Сварочная проволока для полуавтоматической сварки в смеси защитных газов – OK Autrod 385 Ø1,2мм;
Сварочный флюс для автоматической сварки – ОК 10.71;
Сварочный флюс для автоматической сварки – ОК 10.93.
Сварочная проволока для полуавтоматической сварки в смеси защитных газов – Св-08Г2С Ø1,2мм.
Защитный газ – газовая смесь, содержащая в качестве основного газа Ar80%, в качестве компонента 20%СО2.
Таблица 4.1 – Химический состав проволок по ГОСТ 2246-70
Проволока | Содержание в % | |||||||||
C | N | Mn | Si | Cr | Ni | Мо | Nb | S | P | |
Cв-04ХМА | 0,15-0,22 | До 0,012 | 0,4-0,7 | 0,12-0,35 | 0,8-1,1 | До 0,3 | 0,15-0,3 | - | До 0,025 | До 0,025 |
OK Autrod 309L | До 0,03 | 0,11 | 1,4-2,2 | 0,3-0,65 | 23-25 | 12-14 | 0,1 | - | До 0,02 | До 0,03 |
OK Autrod 385 | До 0,025 | - | 1,4-2,2 | До 0,5 | 19,5-21,5 | 24,0-26,0 | 4,2-5,2 | - | До 0,02 | До 0,02 |
Таблица 4.2 – Химический состав флюсов по ГОСТ 9087-81
Флюс | Содержание в % | ||||||||
C | Cr | Cu | Mn | Mo | Ni | N | Nb | Si | |
OK Flux 10.71 | 0,04-0,09 | 0,3-1,3 | 0,5 | 0,9-2,0 | 0,2-0,5 | 0,7-2,2 | - | - | 0,3-0,5 |
OK Flux 10.93 | 0,0-0,1 | 16,2-29 | 1,5 | 0,2-6,3 | 2,1-4 | 8-25 | 0.12-0.25 | 0.3-0.5 | 0,1-1,2 |
Содержание S до 0,02; P до 0,03
Выбор сварочных флюса:
Флюс при автоматической дуговой сварке выполняет важную функцию. Слой флюса защищает жидкий металл в зоне плавления от атмосферного влияния. Флюс легирует наплавляемый металл, рафинирует его и оказывает влияние на химический состав и структуру шва. От физических свойств флюса зависит формирование сварного шва и наличие в нем дефектов.
Сварочный флюс OK Flux 10.71 - керамический сварочный флюс алюминатно-основного типа, предназначен для одно- и многопроходной электродуговой сварки на постоянном и переменном токе углеродистых и низколегированных конструкционных сталей перлитного класса с нормативным временным сопротивлением разрыву до 600 МПа. Флюс OK Flux 10.71 соответствует общим техническим условиям ГОСТ 28555, ЕN 13479, имеет маркировку «СЕ» Европейской ассоциации торговли и широко применяется в производстве строительных металлоконструкций, в том числе мостов, в судостроении, строительстве трубопроводов и в ряде отраслей машиностроения.
Флюс OK 10.71 предназначен для одно- и многодуговых видов сварок, таких как двухдуговая сварка, сварка расщепленной дугой, а также двухдуговая сварка расщепленными дугами и многие другие способы сварки стыковых, нахлесточных и угловых швов. Он одинаково хорошо работает как на постоянном, так и переменном токе. Хорошая отделяемость шлака и незначительное легирование Si и Mn делает его отличным флюсом для многопроходной сварки толстостенных изделий. Незначительная чешуйчатость наплавленного металла позволяет выполнять сварку на высоких скоростях, и все это в сочетании с очень хорошими значениями ударной вязкости. Высокая скорость кристаллизации шлака позволяет выполнять сварку в положении Г(PC).
Применение сварочного флюса OK FLUX 10.71
Флюс OK Flux 10.71 обладает высокими для основного флюса технологическими свойствами, сохраняя при этом низкое содержание О2 в наплавленном металле, что обеспечивает получение высокой ударной вязкости при температурах до -40 °С. Требуемый уровень механических свойств металла шва достигается за счет правильного подбора сварочной проволоки, так как легирование шва преимущественно происходит через нее. Флюс OK Flux 10.71 обладает определенными преимуществами при сварке в узкую разделку, так как обеспечивает плавный переход от наплавленного к основному металлу, а также хорошую отделяемость шлаковой корки.