ВУЗ: Не указан
Категория: Не указан
Дисциплина: Не указана
Добавлен: 03.02.2024
Просмотров: 230
Скачиваний: 6
ВНИМАНИЕ! Если данный файл нарушает Ваши авторские права, то обязательно сообщите нам.
Ррабочие колеса с импеллерами(рисунок 2.22 г), служат для разгрузки осевого усилия или защиты уплотнений от попадания твердых частиц.
Очертания и размеры внутренней (проточной) части колеса определяются гидродинамическим расчетом. Форма и конструктивные размеры колеса должны обеспечивать его необходимую механическую прочность, а также удобство отливки и дальнейшей механической обработки.
Материал для рабочих колес выбирают с учетом его коррозионной стойкости к воздействию перекачиваемой жидкости. В большинстве случаев рабочие колеса насосов изготовляют из чугуна. Колеса крупных насосов, выдерживающие большие механические нагрузки, изготовляют из стали. В тех случаях, когда эти насосы предназначены для перекачки неагрессивной жидкости, для изготовления колес используется углеродистая сталь. В насосах, предназначенных для перекачивания жидкостей с большим содержанием абразивных веществ (пульп, шламов и т. п.), применяются рабочие колеса из марганцовистой стали повышенной твердости. Кроме того, в целях повышения долговечности рабочие колеса таких насосов иногда снабжают сменными защитными дисками из абразивно-стойких материалов.
Рабочие колеса насосов, предназначенных для перекачивания агрессивных жидкостей, изготовляют из бронзы, кислотоупорных чугунов, нержавеющей стали, керамики и различных пластмасс.
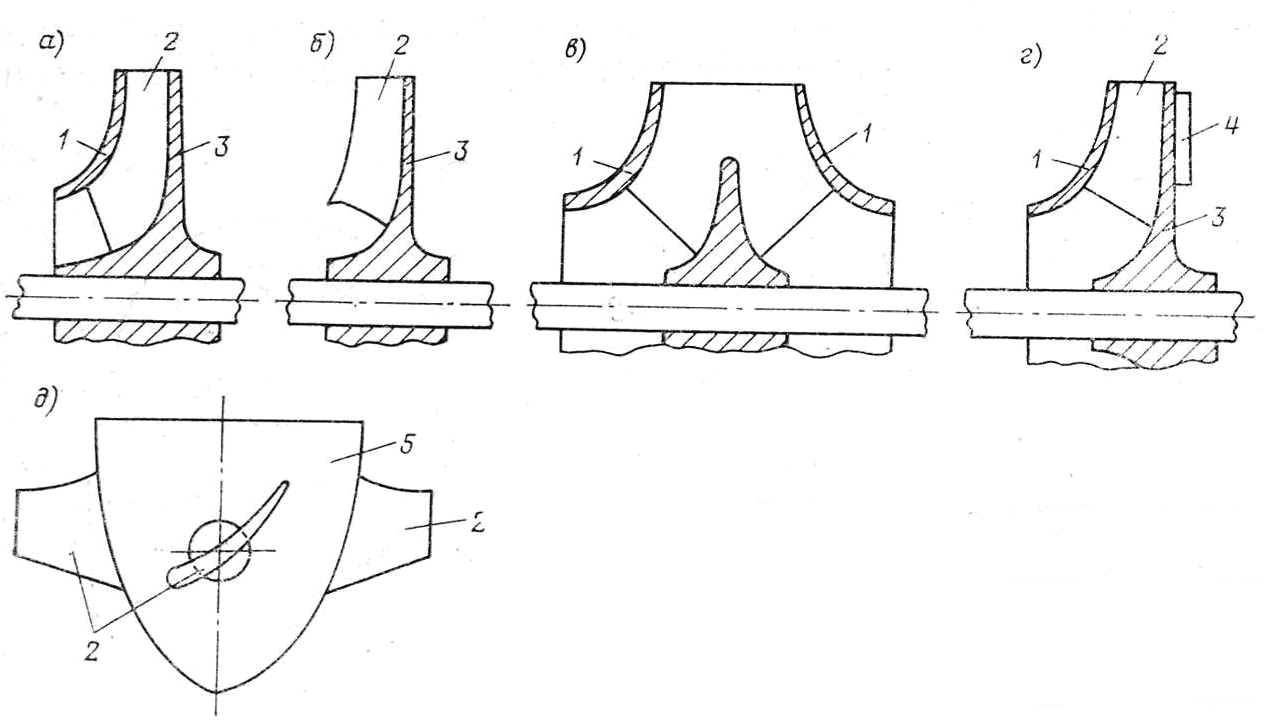
Рисунок 2.22 Рабочие колеса центробежных и осевых насосов:
а – закрытого типа с односторонним подводом жидкости;
б – полуоткрытого типа;
в – двустороннего входа (закрытого типа);
г – с импеллером;
д - колесо осевого насоса;
1 – передний диск;
2 – лопасти;
3 – основной диск;
4 – импеллер;
5 – втулка.
Корпус насоса объединяет узлы и детали, служащие для подвода жидкости к рабочему колесу и отвода ее в напорный трубопровод. На корпусе монтируют подшипники, сальники и другие детали насоса.
Корпус насосов может быть с торцевым или осевым разъемом. В насосах с торцевым разъемом корпуса (рисунок 2.23) плоскость разъема перпендикулярна оси насоса, а в насосах с осевым разъемом (рисунок 2.24) она проходит через ось насоса.
Корпус насоса включает в себя подводящее и отводящее устройства.
![]() Рисунок 2.23 Многоступенчатый насос с торцевым разъемом | ![]() Рисунок 2.24 Насос с осевым разъемом и колесом двустороннего входа |
Подводящее устройство (подвод)- участок проточной полости насоса от входного патрубка до входа в рабочее колесо, а у многоступенчатых насосов – до входа в рабочее колесо первой ступени. Подводы необходимы для подачи перекачиваемой жидкости к рабочему колесу с минимальными потерями, создания равномерного поля скоростей и обеспечения необходимого момента скорости на входе в рабочее колесо.
Конструктивно насосы изготовляют с осевым (рисунок 2.25, а), боковым в виде колена (рисунок 2.25, б), боковым кольцевым (рисунок 2.25, в) и боковым полуспиральным (рисунок 2.25, г) входом.
Осевой вход характеризуется наименьшими гидравлическими потерями, однако при изготовлении насосов с таким входом увеличиваются размеры насосов в осевом направлении, что не всегда удобно конструктивно. Боковой кольцевой вход создает наибольшие гидравлические потери, но обеспечивает компактность насоса и удобное взаимное расположение всасывающего и напорного патрубков.
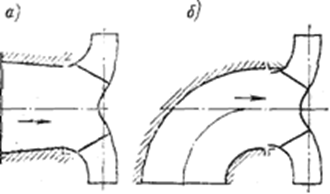
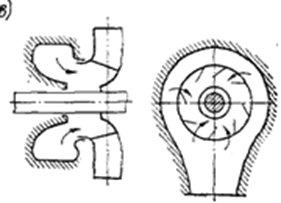
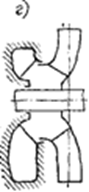
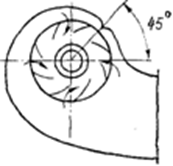
Рисунок 2.25Схемы ввода жидкости в рабочие колеса центробежных насосов
В насосах с двусторонним входом рабочие колеса разгружены от осевого давления, возникающего при работе насоса. В этих насосах применяют, как правило, боковой полуспиральный вход, который обеспечивает равномерное поступление жидкости в рабочее колесо.
Отводящее устройство (отвод) - это участок, предназначенный для отвода жидкости от рабочего колеса в напорный патрубок насоса. Жидкость выходит из рабочего колеса с большой скоростью. При этом поток обладает высокой кинетической энергией, а движение жидкости сопровождается большими гидравлическими потерями. Для уменьшения скорости движения жидкости, выходящей из рабочего колеса, преобразования кинетической энергии в потенциальную (увеличения давления) и уменьшения гидравлических сопротивлений применяют отводящие устройства, а также направляющие аппараты.
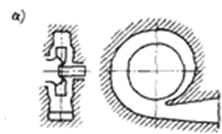
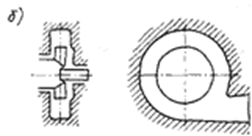
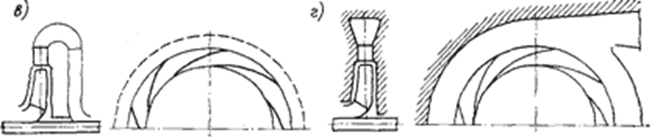
Рисунок 2.26 Схемы отводов центробежных насосов
Различают спиральный, полуспиральный, двухзавитковый и кольцевой отводы, а также отводы с направляющими аппаратами.
Спиральный отвод — это канал в корпусе насоса, охватывающий рабочее колесо по окружности (рисунок 2.26, а). Поперечное сечение этого канала увеличивается соответственно расходу жидкости, поступающей в него из рабочего колеса, а средняя скорость движения жидкости в нем уменьшается по мере приближения к выходу или остается примерно постоянной. Спиральный канал оканчивается выходным диффузором, в котором происходит дальнейшее уменьшение скорости и преобразование кинетической энергии жидкости в потенциальную.
Кольцевой отвод - это канал постоянного сечения, который охватывает рабочее колесо так же, как и спиральный отвод (рисунок 2.26,б). Кольцевой отвод применяют обычно в насосах, предназначенных для перекачивания загрязненных жидкостей. Гидравлические потери в кольцевых отводах значительно больше, чем в спиральных.
Полуспиральный отвод - это кольцевой канал, переходящий в спиральный расширяющийся отвод.
Направляющий аппарат (рисунок 2.26, в). В центробежных насосах направляющий аппарат предназначен для того, чтобы поток жидкости, поступающий из рабочего колеса, отвести в определенном направлении и одновременно преобразовать кинетическую энергию потока в потенциальную энергию давления.
Напрвляющий аппарат представляет собой два кольцевых диска, между которыми размещены направляющие лопасти, изогнутые в сторону, противоположную направлению изгиба лопастей рабочего колеса. Направляющие аппараты — более сложные устройства, чем спиральные отводы, гидравлические потери в них больше и потому их применяют только в некоторых конструкциях многоступенчатых насосов.
В крупных насосах иногда применяются составные отводы (рисунок 2.26, г), представляющие собой сочетание направляющего аппарата и спирального отвода.
Вал насосапредназначен для передачи момента вращения от электродвигателя к рабочим колесам, неподвижно закрепленным на валу при помощи шпонок и установочных гаек или неподвижной (горячей, глухой, прессовкой и т.д.) посадки. Часть вала, которая непосредственно лежит на опоре, называется цапфой, причем концевые цапфы принято называть шипами, а промежуточные – шейками. Если цапфа передает опоре осевую нагрузку вала, ее называют пятой.
Максимальный диаметр вала насоса обычно выбирается в месте посадки рабочих колес, а к концам диаметр вала ступенчато уменьшается. Уступ вала для упора рабочих колес выполняется строго перпендикулярно е оси, а оси шпоночных пазов лежат в плоскости, проходящей через ось ротора. Посадочные размеры вала обрабатываются по второму классу точности.
Валы нефтяных насосов изготавливают из сталей 40Х (ГОСТ 4543-71).
Вращающийся вал насоса своей шейкой (шипом) соприкасается с неподвижной опорой – подшипником.
Подшипники воспринимают усилия передаваемые валом насоса на опору (при неуравновешенных осевых силах). Следовательно, подшипники насоса можно подразделить на две группы: радиальные, воспринимающие перпендикулярные к оси вала усилия, и упорные, воспринимающие осевые усилия, действующие на ротор.
По виду трения подшипники разделяются: на подшипники скольжения и подшипники качения (шарикоподшипники и роликоподшипники).
Подшипники скольжения – это опоры вращающихся деталей, которые работают в условиях скольжения поверхности цапфы по поверхности подшипника.
Форма рабочей поверхности подшипника скольжения так же, как и форма цапфы вала, может быть
• цилиндрической,
• плоской,
• конической,
• сферической.
Опору, передающую осевую нагрузку, называют подпятником. Подпятники работают, как правило, в паре с радиальными подшипниками. Большая часть радиальных подшипников может воспринимать небольшие осевые нагрузки. Основным элементом подшипника является вкладыш из антифрикционного материала. Вкладыш устанавливается в специальном корпусе подшипника или непосредственно в корпусе.
Условия работы и виды разрушения подшипников скольжения
Вращению цапфы в подшипнике противодействует момент сил трения. При этом нагревается подшипник и цапфа. Теплота выделяется через корпус подшипника и вал, переносится со смазывающей жидкостью. Повышение температуры снижает вязкость смазки, увеличивая вероятность заедания цапфы в подшипнике, что приводит к выплавлению вкладыша. Основной причиной его выхода из строя подшипника является перегрев.
При работе подшипника наблюдаются износ вкладыша и цапфы, что нарушает правильную работу механизма и самого подшипника. Интенсивность износа определяет долговечность подшипника.
При переменных нагрузках на поверхности вкладыша может наблюдаться усталостноевыкрашивание. При больших кратковременных перегрузках ударного характера вкладыши могут хрупко разрушаться.
Достоинства подшипников скольжения:
- надежно работают в высокоскоростных приводах;
- способны воспринимать большие ударные и вибрационные нагрузки;
- бесшумность работы;
- сравнительно малые радиальные размеры;
- разъемные подшипники допускают установку на шейки коленчатых валов;
- простота конструкции;
- для тихоходных машин могут иметь весьма простую конструкцию.
Недостатки подшипников скольжения:
- в процессе работы требуют постоянного надзора из-за высоких требований к смазыванию и опасности перегрева. Перерыв в подаче смазочного материала ведет к выходу из строя подшипника;
- имеют сравнительно большие осевые размеры;
- значительные потери на трение в период пуска и при несовершенной смазке;
- большой расход смазочного материала.
Подшипники качения представляют собой готовый узел, основным элементом которого являются тела качения - шарики или ролики, установленные между кольцами и удерживаемые на определенном расстоянии друг от друга обоймой, называемой сепаратором. В процессе работы тела качения катятся по дорожкам качения колец, одно из которых в большинстве случаев неподвижно. Распределение нагрузки между несущими телами качения неравномерно и зависит от величины радиального зазора в подшипнике и от точности геометрической формы его деталей.
В зависимости от типа нагрузки (радиальной или осевой) подшипники качения делятся на три группы:
- радиальные, которые могут воспринимать нагрузки направленные радиально;
- упорные, предназначенные для восприятия нагрузки, действующей вдоль оси вала;
- радиально-упорные, воспринимающие комбинированную нагрузку – радиальную и осевую.
Достоинства подшипников качения:
- сравнительно малая стоимость вследствие массового производства подшипников;
- малые потери на трение и незначительный нагрев (потери на трение при пуске и установившемся режиме работы практически одинаковы);
- высокая степень взаимозаменяемости, что облегчает монтаж и ремонт машин;
- малый расход смазочного материала;
- не требуют особого внимания и ухода;
- малые осевые размеры.
Недостатки подшипников качения:
- высокая чувствительность к ударным и вибрационным нагрузкам вследствие большой жесткости конструкции подшипника;
- малонадежны в высокоскоростных приводах из-за чрезмерного нагрева и опасности разрушения сепаратора от действия центробежных сил;