Файл: Реферат Дипломный проект 126 с., 5 рис., 28 табл.,17 источников.doc
Добавлен: 04.05.2024
Просмотров: 433
Скачиваний: 3
СОДЕРЖАНИЕ
2.1. Способы получения хлорида калия из сильвинита
2.2. Сравнение технико-экономических показателей различных способов производства хлорида калия
3. ТЕХНИКО-ЭКОНОМИЧЕСКОЕ ОБОСНОВАНИЕ
3.1. Месторождения калийного сырья
3.2. Технико-экономическое обоснование сырья, энергоресурсов, географической точки строительства
3.3. Расчет производственной мощности
4.1. Термодинамический анализ возможности элементарного акта флотации
4.2. Силовая трактовка флотации
4.3. Максимальный размер частицы, флотирующейся при пенной флотации
4.4. Необходимый размер пузырьков при пенной флотации
4.6. Кинетика процесса флотации
4.7. Расчет диаметра пузырька воздуха
4.8. Расчет скорости всплывания пузырька
4.9. Оптимизация процесса флотации
5.1. Расчет качественно – количественной схемы.
5.2. Таблица материального баланса
6. МАТЕМАТИЧЕСКОЕ МОДЕЛИРОВАНИЕ
6.2. Условия проведения эксперимента
7. ВЫБОР И РАСЧЕТ ОБОРУДОВАНИЯ
7.1. Оборудование для флотации
7.2 Оборудование отделения измельчения и классификации
7.3. Оборудование для обезвоживания
7.4. Оборудование для сгущения
7.5. Обоснование выбора насосов
8.1. Автоматизация технологических процессов
8.2. Выбор и обоснование параметров контроля, регулирования, сигнализации и блокировок
8.3. Выбор средств автоматизации и контроля отделения флотации
9. ТЕХНОЛОГИЧЕСКАЯ СХЕМА ФЛОТАЦИОННОГО ПОЛУЧЕНИЯ ХЛОРИДА КАЛИЯ ИЗ СИЛЬВИНИТА
9.2. Отделение обесшламливания
9.4. Отделение обезвоживания концентрата и хвостов
9.5. Отделение сгущения продуктов обогащения
10.1. Ежегодные нормы образования отходов производства
10.2. Обеспечение надежности охраны окружающей среды
10.3. Анализ экологической безопасности
11. БЕЗОПАСНОСТЬ ПРОИЗВОДСТВЕННОЙ ДЕЯТЕЛЬНОСТИ
11.1. Охрана труда в Российской Федерации
11.2. Свойства используемых и получаемых веществ. Опасные и вредные производственные факторы
11.3. Классификация производства
11.4. Общие правила безопасности
11.5. Санитарно-технические мероприятия
11.6. Противопожарные мероприятия
12.1. Климатические и геологические условия месторасположения производства
12.2. Описание генерального плана предприятия
12.3. Характеристика главного корпуса обогатительной фабрики БКПРУ-2
12.4. Компоновка оборудования в цехе
13.1. Расчет производственной мощности ФОФ БКПРУ-2
13.5. Расчёт себестоимости КСL на БКПРУ-2
13.6. Сравнительный анализ себестоимости KCl
13.7. Расчет основных экономических показателей производства KCl
Недостатки:
-
Большой расход электроэнергии -
Трудность быстрого запуска после аварийной остановки
а) Флотация сильвинитовой пульпы
t = 5-6 минут
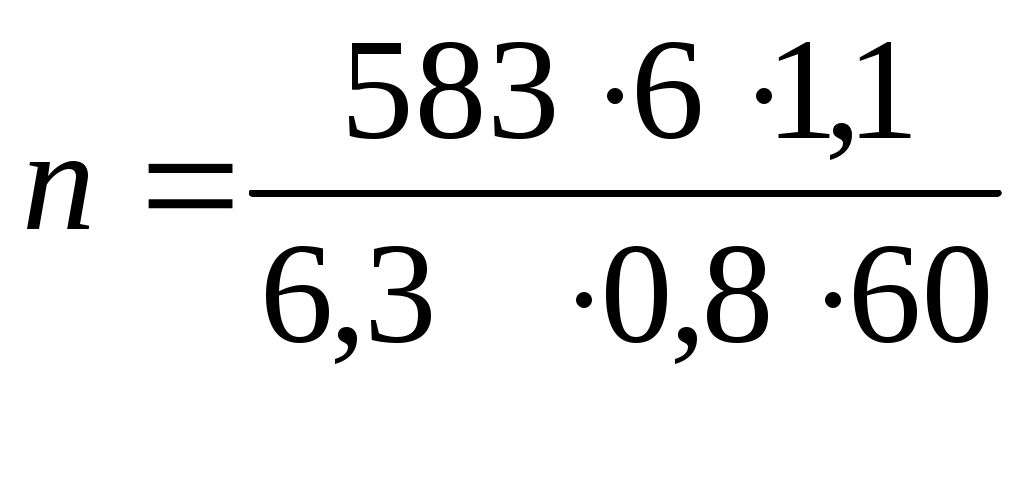
Для эффективного разделения сильвинита на сильвин и галит при данных условиях требуется 14 флотационных камер. Фактически установлены 2-а плеча по 7 камер или по 6 и 8 камер.
б) Первая перечистка
t = 4-5 минут
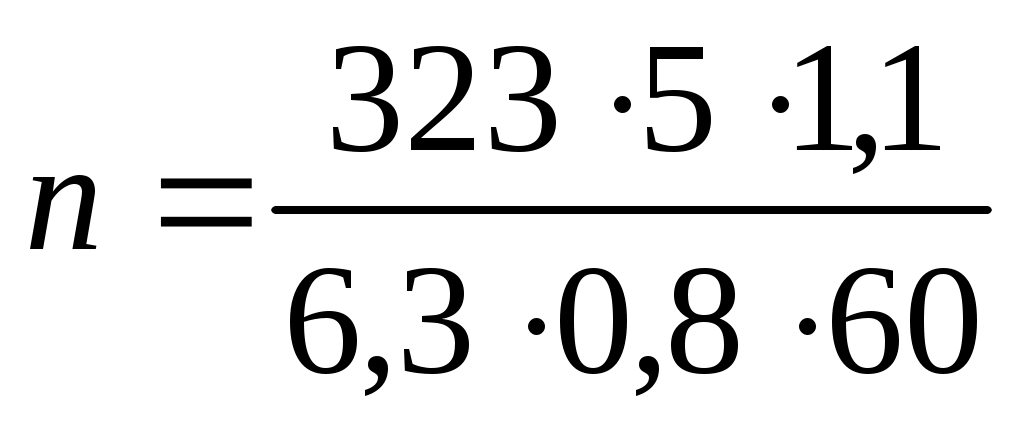
Для первой перечистной операции требуется 4 камеры.
в) Вторая перечистка
t = 4-5 минут
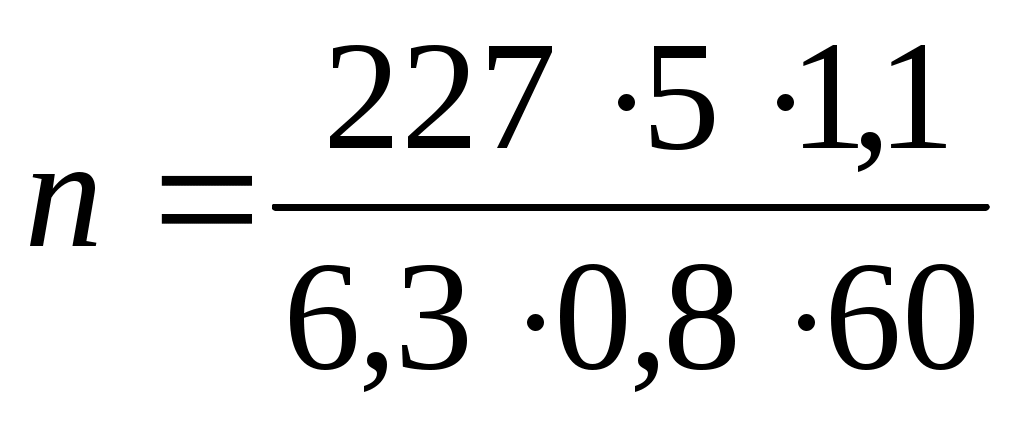
Для второй перечистной операции требуется 3 камеры.
г) Третья перечистка
t = 4-5 минут
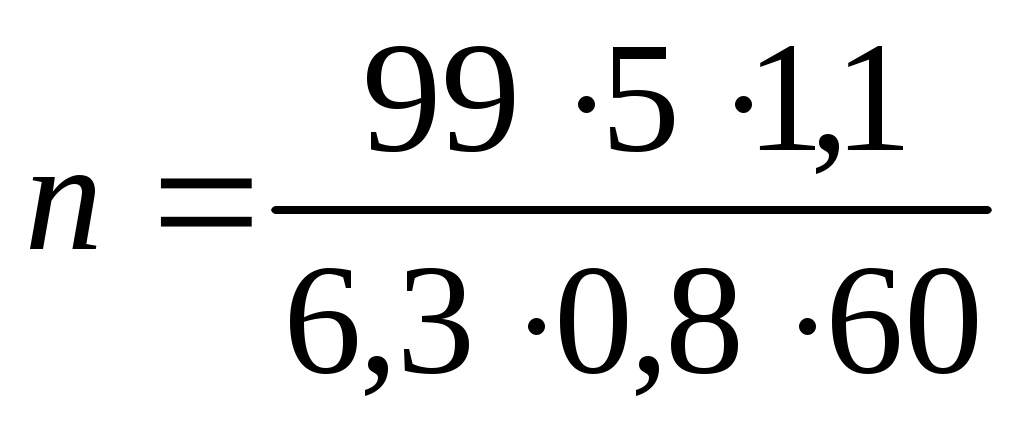
Для третьей перечистной операции требуется 3 камеры.
д) Шламовая флотация
t = 3-4 минуты
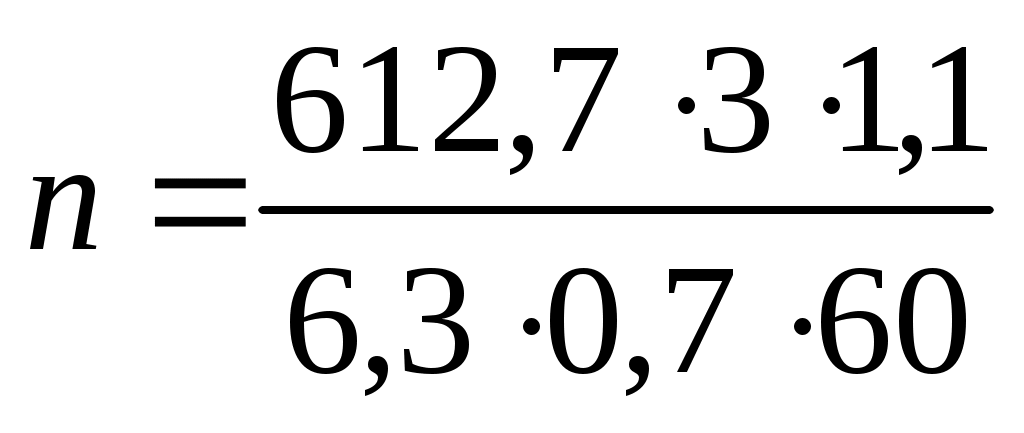
Для процесса шламовой флотации требуется 8 камер (фактически установлена 8-ми камерная флотомашина).
е) Перечистка шламов
t = 4-5 минут
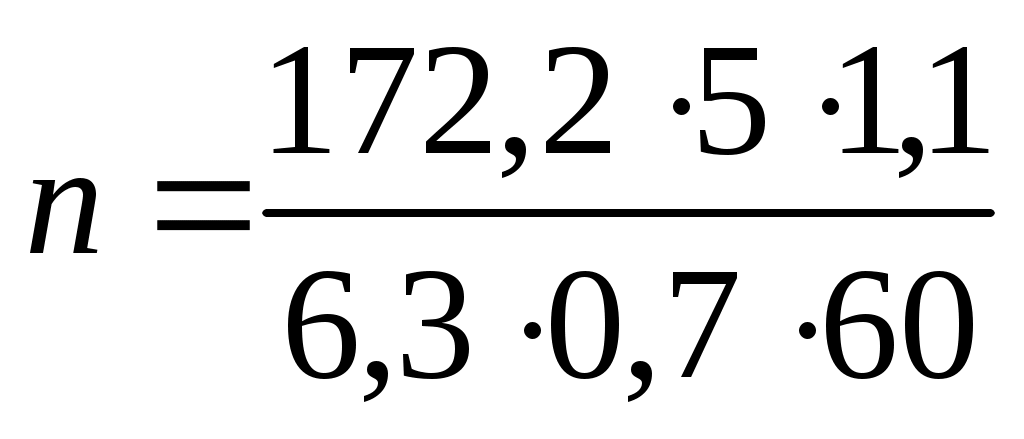
Для перечистки шламов требуется 4 камеры (фактически установлена 4-х камерная флотомашина).
ж) колонная машина
Техническая характеристика:
- производительность (по суспензии) - 1000 м3/ч;
- объем 1 камеры (полезный) - 60 м3;
Машина состоит из 3-х камер Vк = 60·3 = 180 м3
t = 10-15 минут
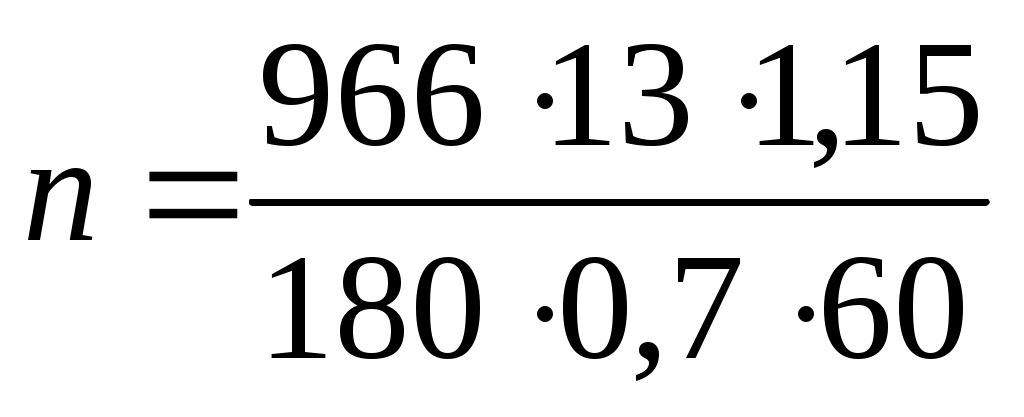
Для данного количества суспензии необходимо 2 колонные машины. Фактически установлено по 2 машины на каждой секции.
7.2 Оборудование отделения измельчения и классификации
7.2.1 Стержневая мельница
Техническая характеристика:
- мельница стержневая МСЦ 3,2х4,5 (D = 3200 мм, L = 4500 мм);
- расчетный класс – фракция < 1 мм;
- содержание расчетного класса в исходной руде α = 33 %;
- содержание расчетного класса в измельченной руде β = 90 %
Рабочий объем барабана
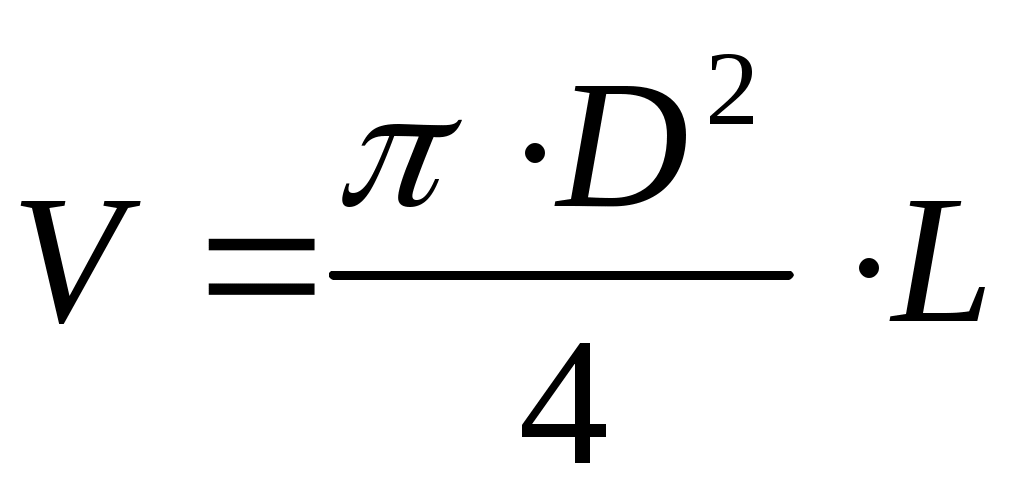
где V – объем барабана, м3;
D – диаметр барабана (без футеровки), м;
L – длина барабана, м
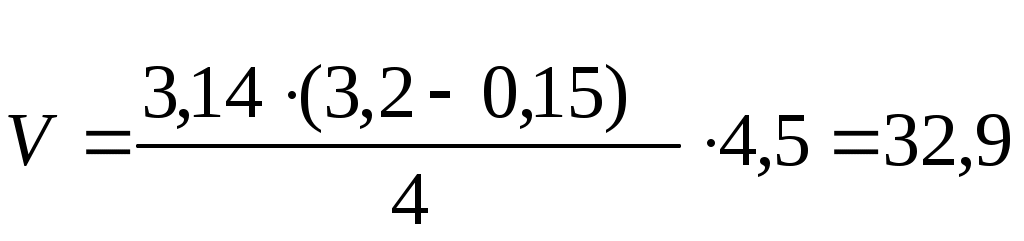
0,15 – толщина футеровки, м
Производительность мельницы

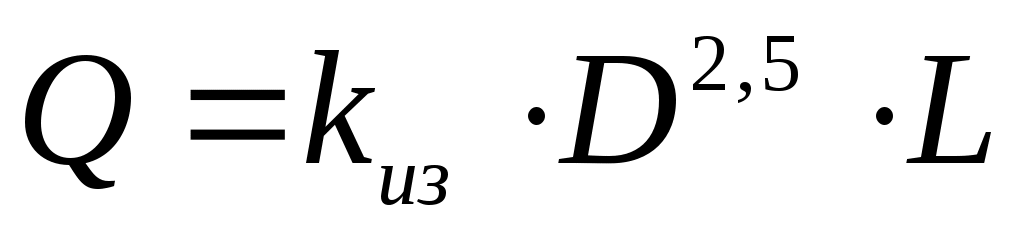
где Q – производительность мельницы, т/ч;
kиз – коэффициент измельчаемости ( для сильвинита k = 1,5÷2)

Удельная производительность по расчетному классу

Необходимое количество мельниц
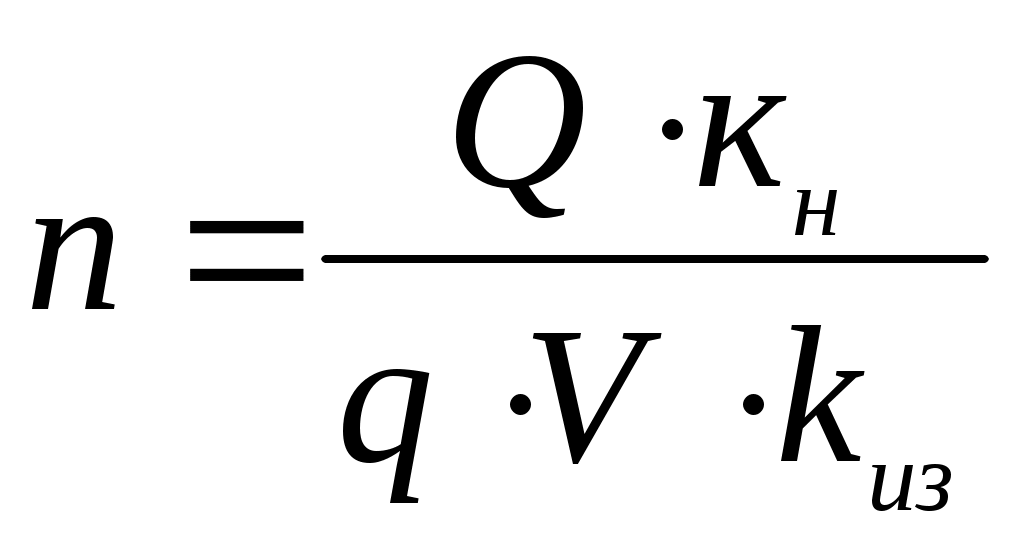
где кн – коэффициент неравномерности подачи нагрузки (1,1÷1,15)
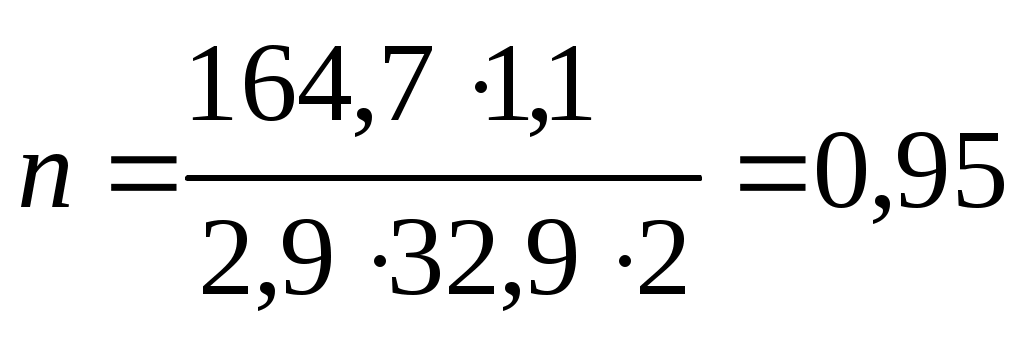
Для измельчения данного количества руды достаточно одной мельницы на каждой секции.
7.2.2 Дуговые сита
а) Предварительная классификация (поз.11)
Количество твердой фазы, поступающей на классификацию на дуговые сита, с учетом коэффициента неравномерности составляет

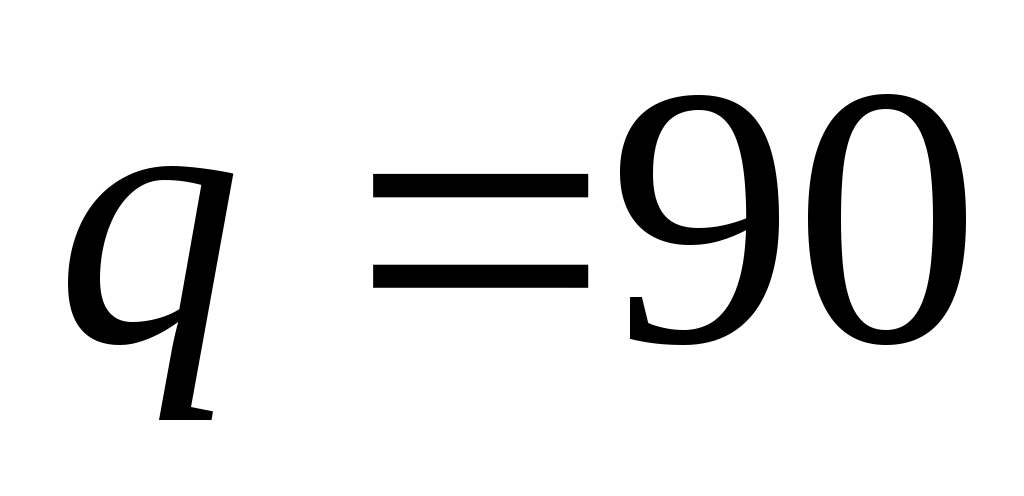
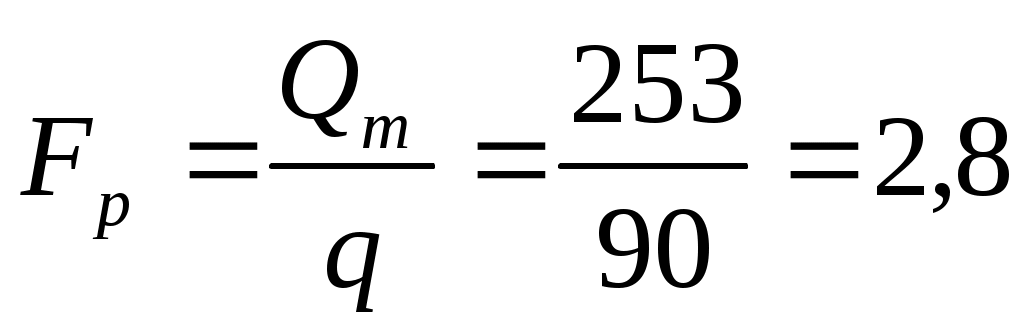
Необходимое количество сит с площадью
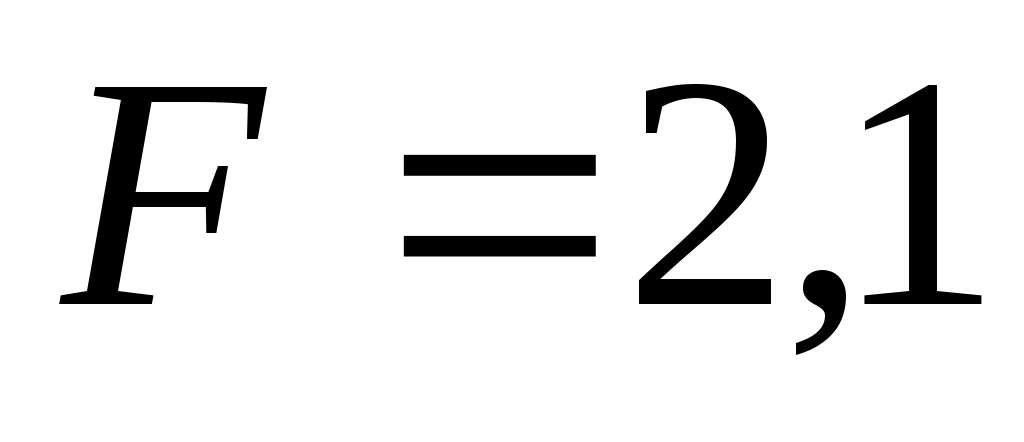
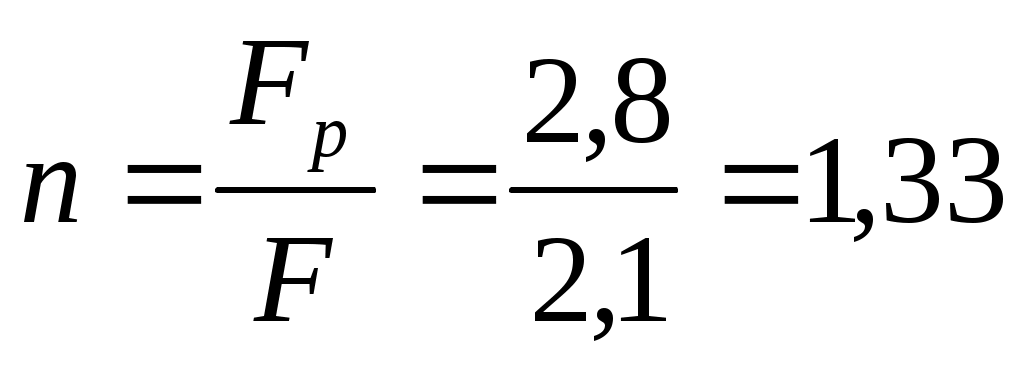
К установке принимаем 2 дуговых сита.
б) Поверочная классификация (поз.14)
Количество твердой фазы, поступающей на классификацию на дуговые сита, с учетом коэффициента неравномерности составляет

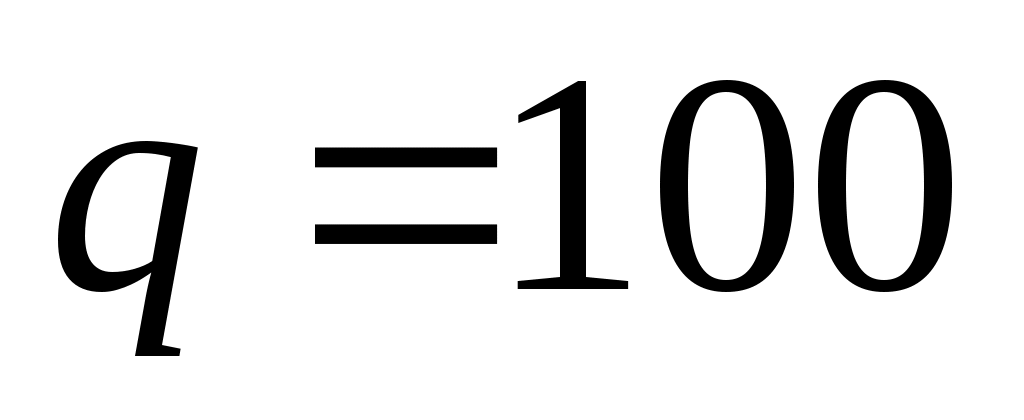
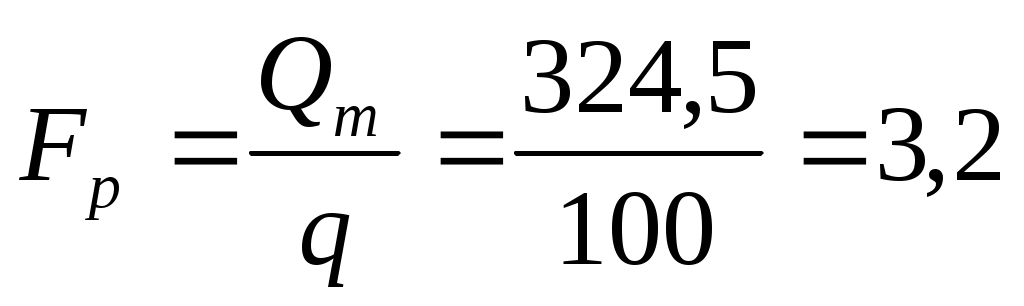
Необходимое количество сит с площадью
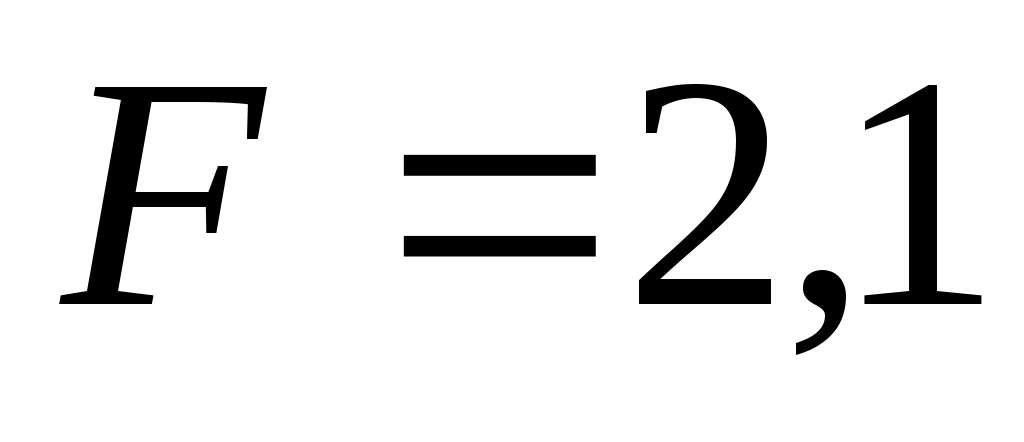
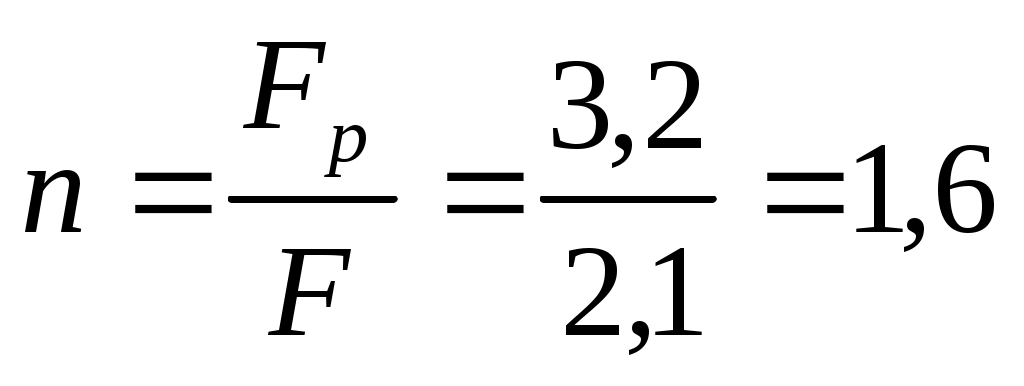
К установке принимаем 2 дуговых сита.
7.3. Оборудование для обезвоживания
7.3.1. Обезвоживание галитовых отходов (ГЦ-500)
Техническая характеристика:
- диаметр корпуса – 500 мм;
- угол конусности – 20º;
- диаметр песковой насадки – 35 мм;
- диаметр сливного патрубка – 150 мм;
- давление на входе – 0,4÷1,2 кг/см2
Расчетная производительность гидроциклона:

Поправка на диаметр

dn – эквивалентный диаметр питающего отверстия (для ГЦ-500 dn =6,5÷15 см);

Объемная производительность одного гидроциклона:

Количество гидроциклонов:
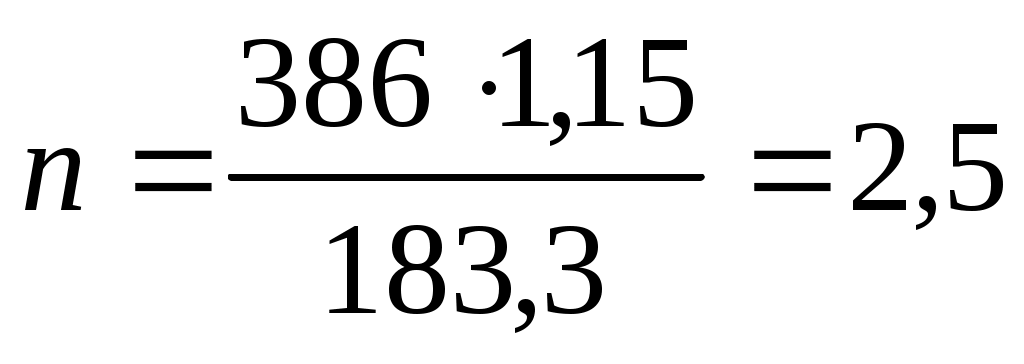
Для обезвоживания данного количества суспензии необходимы 3 гидроциклона (марки ГЦ-500). Фактически установлено 6 гидроциклонов (3 – в работе, 3 – в резерве).
7.3.2. Вакуум – фильтры
Обезвоживание концентрата и галитовых отходов осуществляется на вакуум-фильтрах BF-10 с шириной ленты 1,2 м и площадью фильтрования 10 м2.
а) Обезвоживание концентрата
Количество работающих фильтров определяется по формуле:
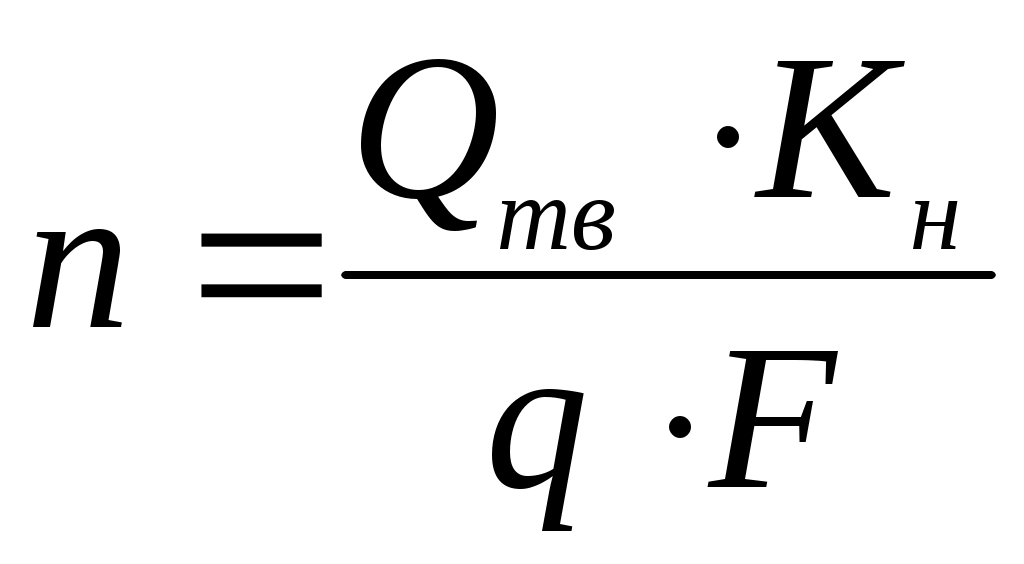
гдеQтв – нагрузка на фильтр по твердому, т/ч;
q – удельная нагрузка на вакуум-фильтр, принимаемая по практическим данным (1,5 т/ м2 ·ч);
F – площадь фильтрования, м2
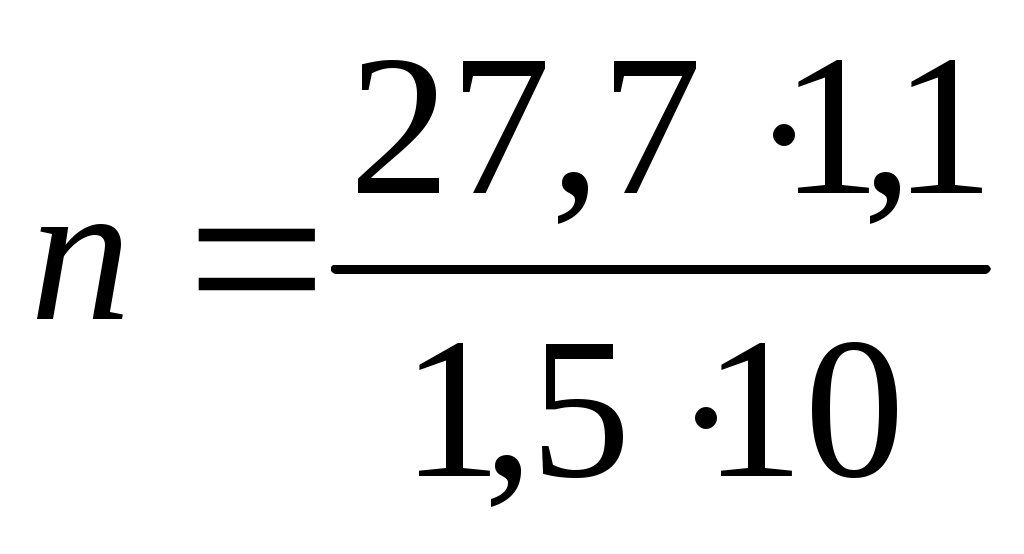
Принимаем к установке 2 ленточных вакуум-фильтра на секцию.
б) Обезвоживание хвостов
q = 12 т/ м2 ·ч
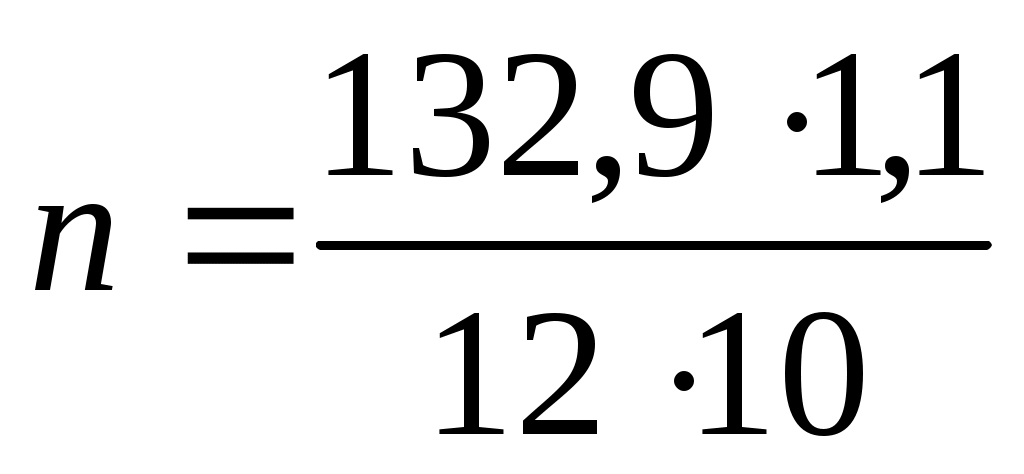
Принимаем к установке 2 ленточных вакуум-фильтра на секцию.
7.3.3. Центрифуги
Для обезвоживания концентрата используются центрифуги SVS 1400*1800 (Гумбольдт) – фактор разделения 124, производительность – 30 т/ч.
Количество центрифуг рассчитывается по формуле:
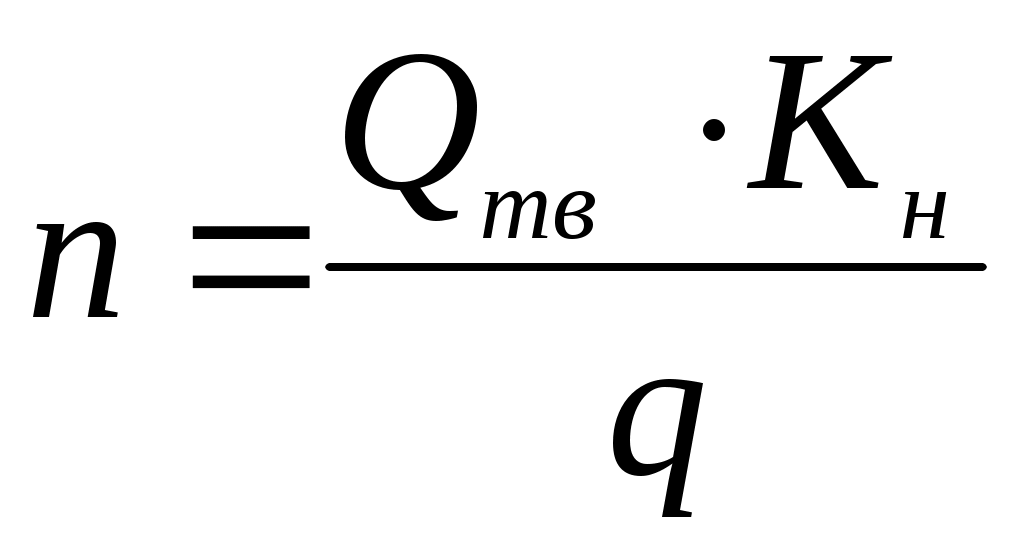
гдеQтв – нагрузка на центрифугу по твердому, т/ч;
q – производительность центрифуги, т/ч
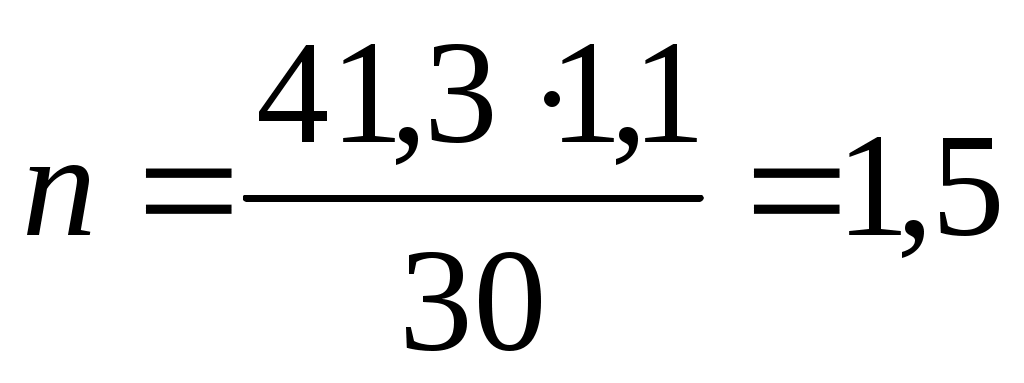
Принимаем к установке 2 центрифуги на секцию.
7.4. Оборудование для сгущения
7.4.1. Сгустители
Площадь сгущения, м2
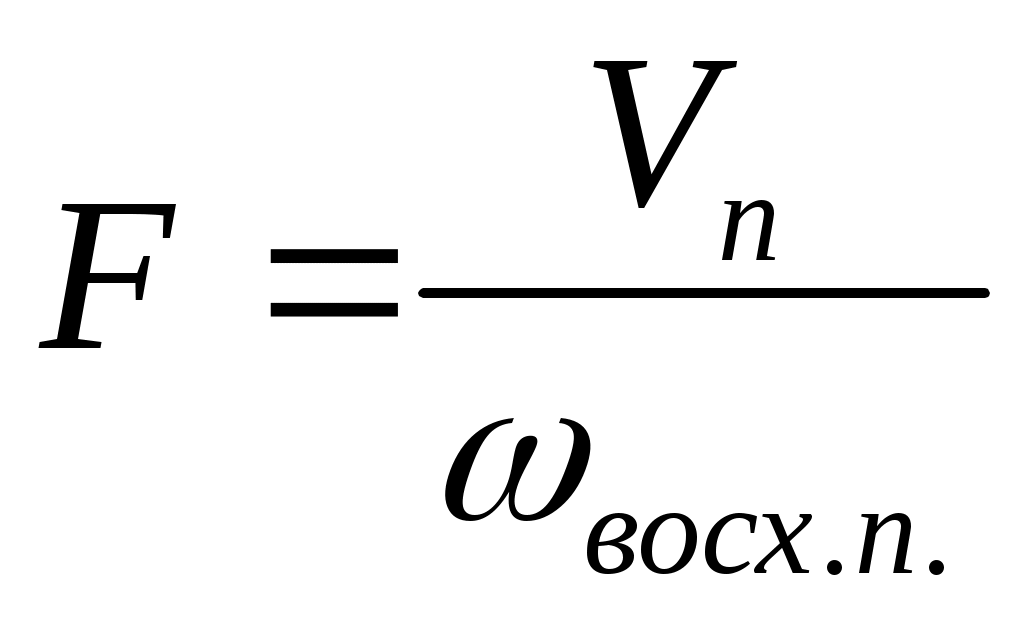
где Vn – объем суспензии, идущей на сгущение, м3/ч;
ωвосх.п. – скорость восходящих потоков, м/ч
Диаметр сгустителя, м
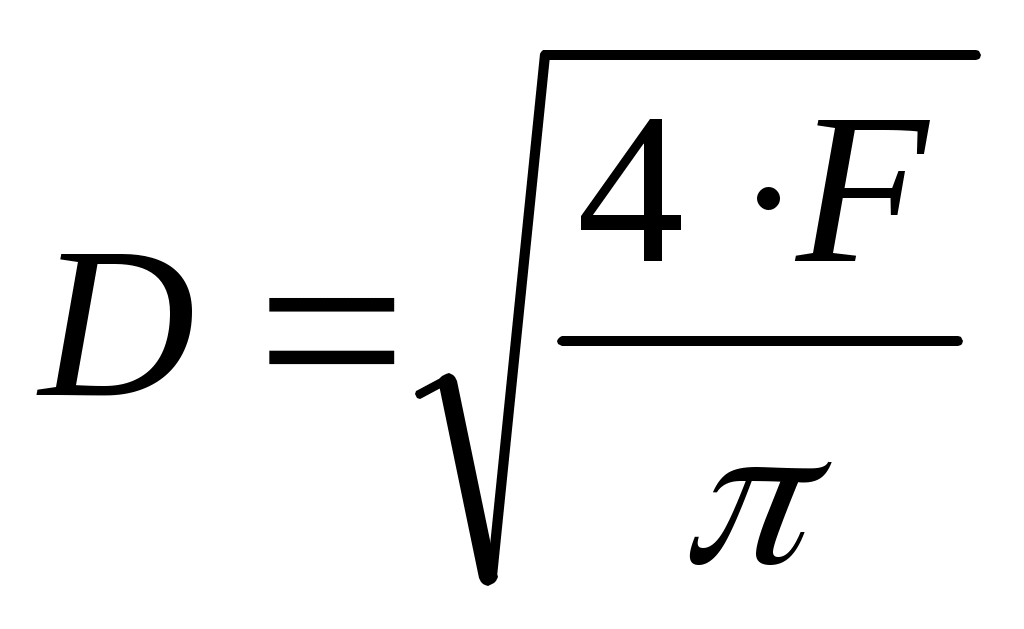
Площадь зеркала сгущения, м2
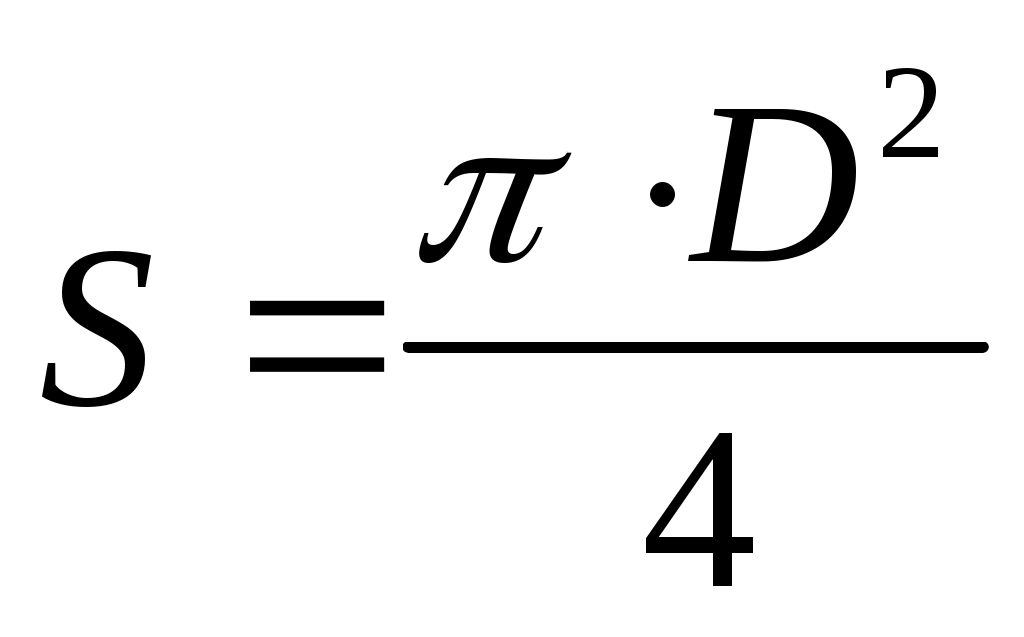
Количество сгустителей, шт
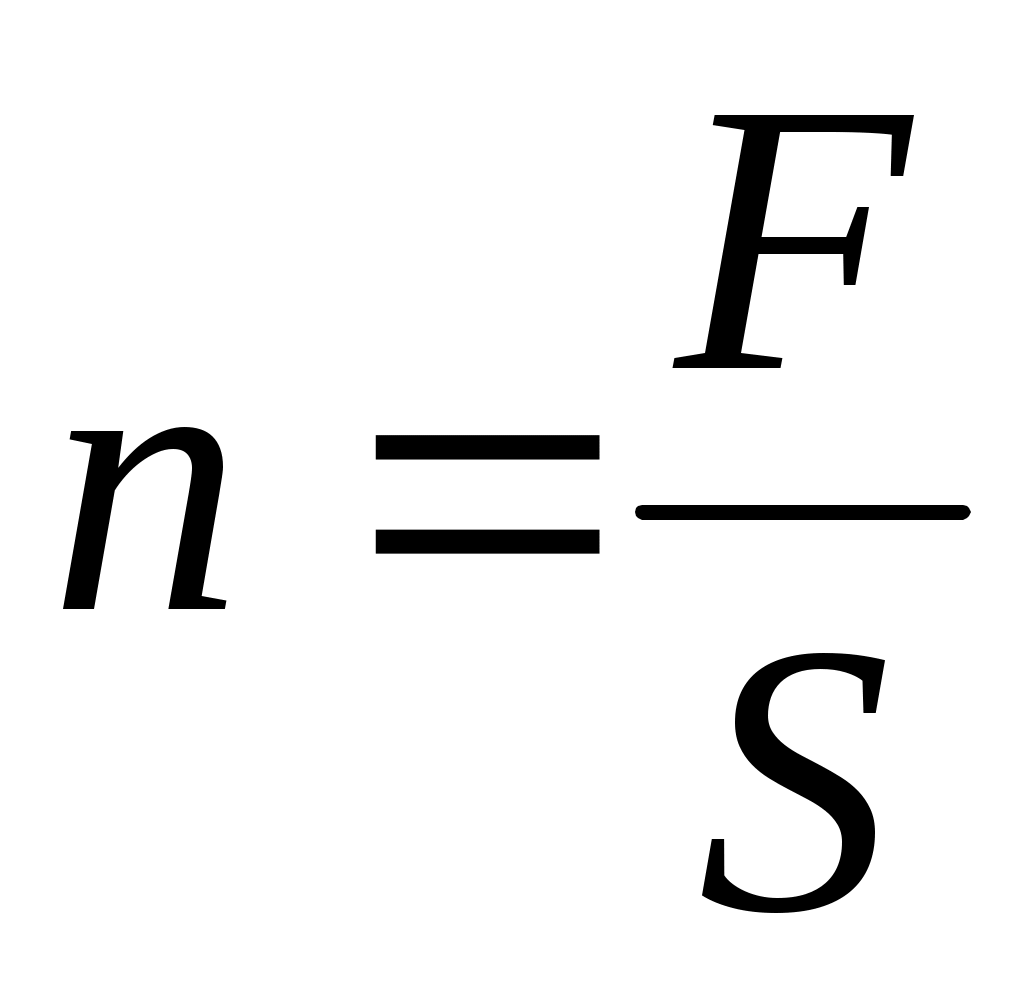
а) Сгуститель для шламов
ωвосх.п. = 0,25-0,5 м/ч
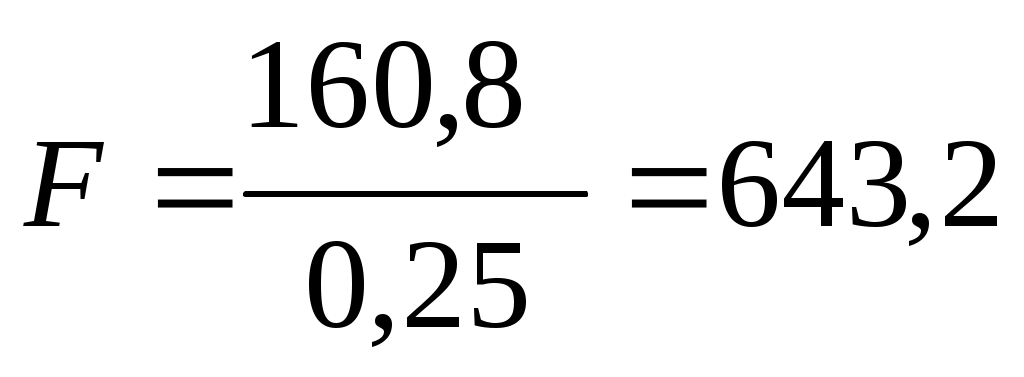
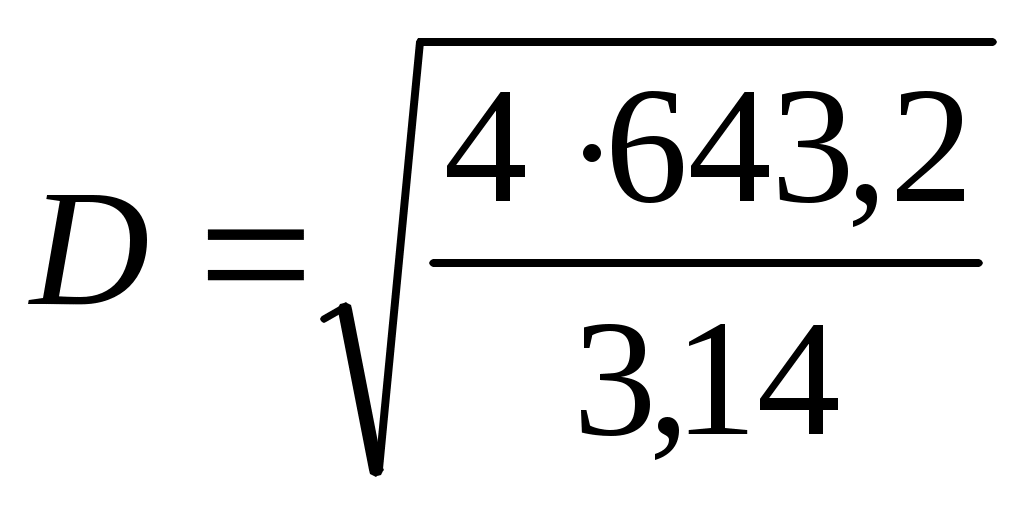
Выбираем стандартный сгуститель диаметром 30 метров.
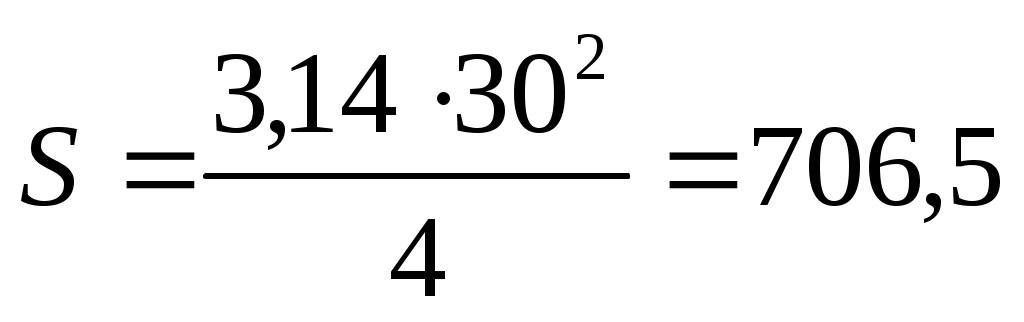
Количество сгустителей
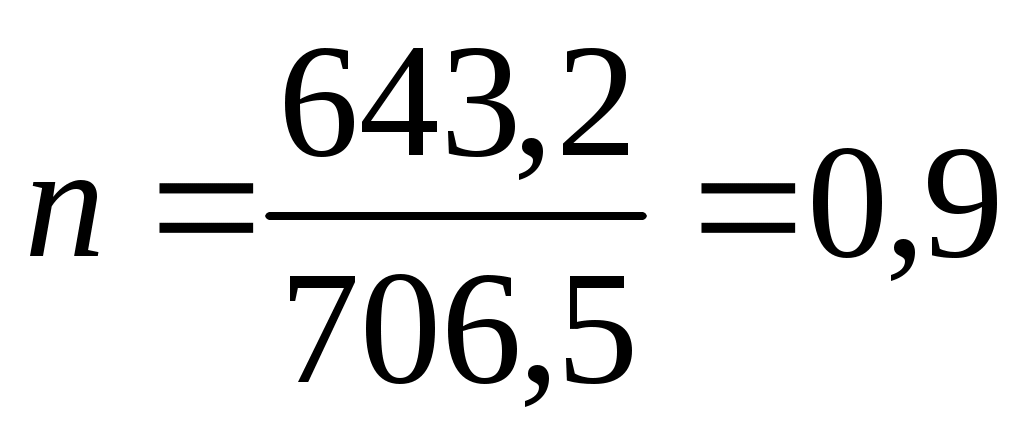
Принимаем к установке 1 сгуститель для шламов.
б) Сгуститель для хвостов
ωвосх.п. = 1,2-1,8 м/ч
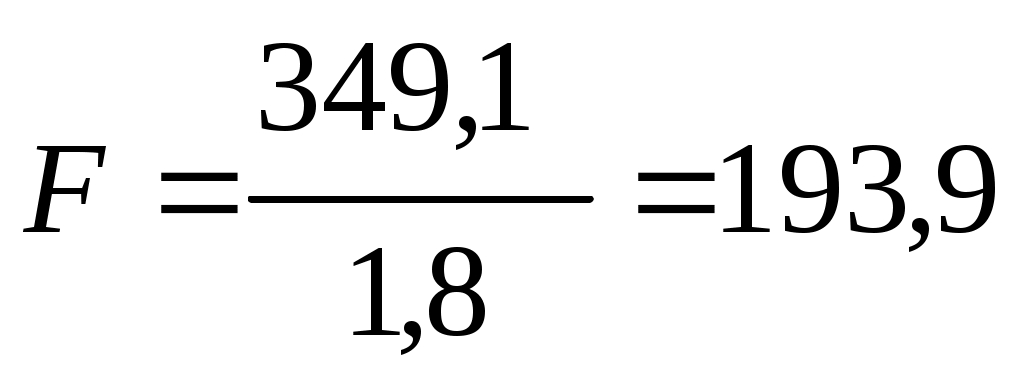
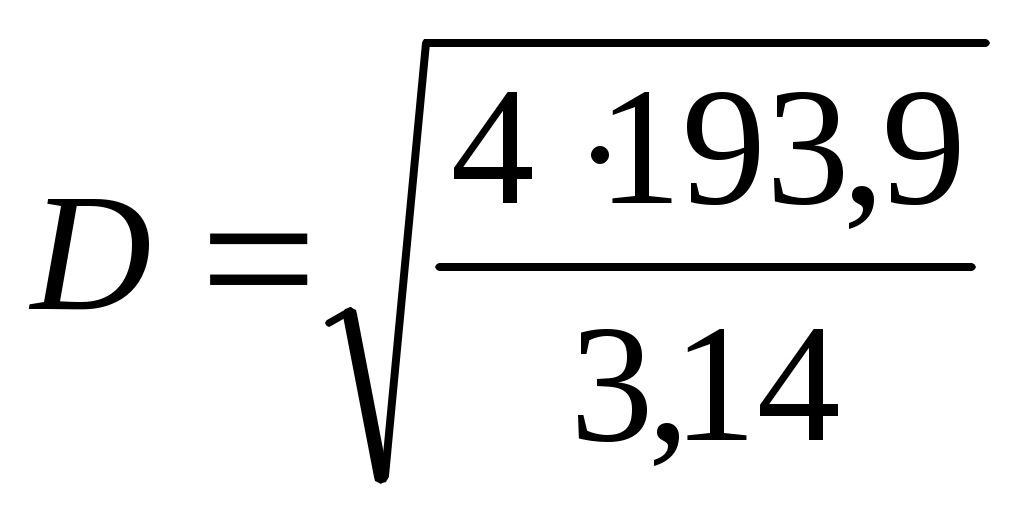
Выбираем стандартный сгуститель диаметром 15 метров.
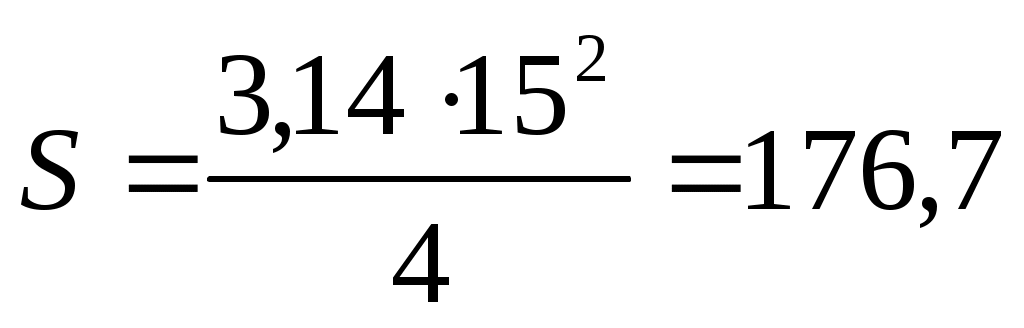
Количество сгустителей
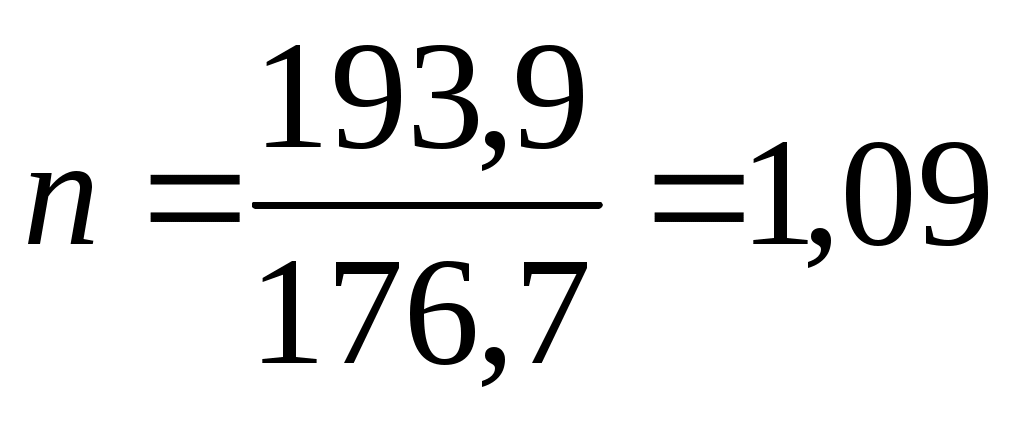
Принимаем к установке 1 сгуститель для хвостов на секцию.
в) Сгуститель для промпродуктов
ωвосх.п. = 1,8-2 м/ч

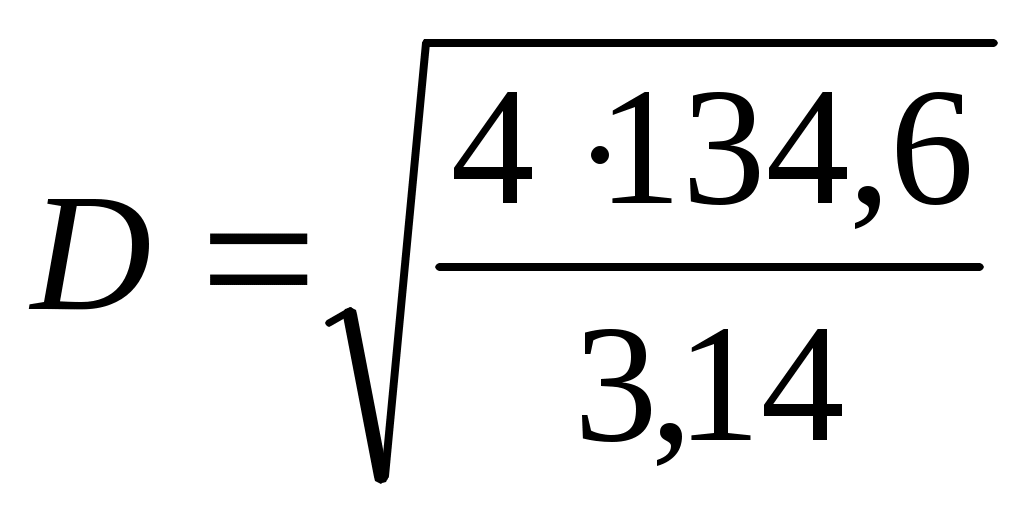
Выбираем стандартный сгуститель диаметром 18 метров.

Количество сгустителей
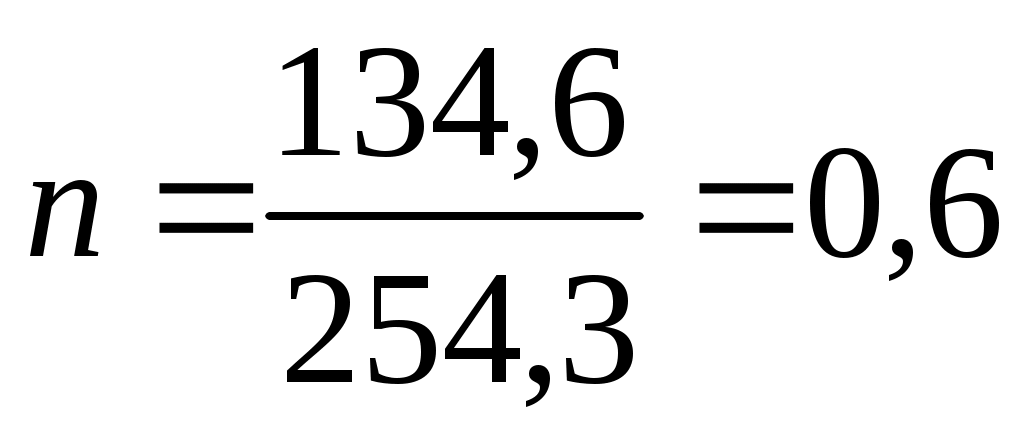