Файл: Реферат Дипломный проект 126 с., 5 рис., 28 табл.,17 источников.doc
Добавлен: 04.05.2024
Просмотров: 432
Скачиваний: 3
СОДЕРЖАНИЕ
2.1. Способы получения хлорида калия из сильвинита
2.2. Сравнение технико-экономических показателей различных способов производства хлорида калия
3. ТЕХНИКО-ЭКОНОМИЧЕСКОЕ ОБОСНОВАНИЕ
3.1. Месторождения калийного сырья
3.2. Технико-экономическое обоснование сырья, энергоресурсов, географической точки строительства
3.3. Расчет производственной мощности
4.1. Термодинамический анализ возможности элементарного акта флотации
4.2. Силовая трактовка флотации
4.3. Максимальный размер частицы, флотирующейся при пенной флотации
4.4. Необходимый размер пузырьков при пенной флотации
4.6. Кинетика процесса флотации
4.7. Расчет диаметра пузырька воздуха
4.8. Расчет скорости всплывания пузырька
4.9. Оптимизация процесса флотации
5.1. Расчет качественно – количественной схемы.
5.2. Таблица материального баланса
6. МАТЕМАТИЧЕСКОЕ МОДЕЛИРОВАНИЕ
6.2. Условия проведения эксперимента
7. ВЫБОР И РАСЧЕТ ОБОРУДОВАНИЯ
7.1. Оборудование для флотации
7.2 Оборудование отделения измельчения и классификации
7.3. Оборудование для обезвоживания
7.4. Оборудование для сгущения
7.5. Обоснование выбора насосов
8.1. Автоматизация технологических процессов
8.2. Выбор и обоснование параметров контроля, регулирования, сигнализации и блокировок
8.3. Выбор средств автоматизации и контроля отделения флотации
9. ТЕХНОЛОГИЧЕСКАЯ СХЕМА ФЛОТАЦИОННОГО ПОЛУЧЕНИЯ ХЛОРИДА КАЛИЯ ИЗ СИЛЬВИНИТА
9.2. Отделение обесшламливания
9.4. Отделение обезвоживания концентрата и хвостов
9.5. Отделение сгущения продуктов обогащения
10.1. Ежегодные нормы образования отходов производства
10.2. Обеспечение надежности охраны окружающей среды
10.3. Анализ экологической безопасности
11. БЕЗОПАСНОСТЬ ПРОИЗВОДСТВЕННОЙ ДЕЯТЕЛЬНОСТИ
11.1. Охрана труда в Российской Федерации
11.2. Свойства используемых и получаемых веществ. Опасные и вредные производственные факторы
11.3. Классификация производства
11.4. Общие правила безопасности
11.5. Санитарно-технические мероприятия
11.6. Противопожарные мероприятия
12.1. Климатические и геологические условия месторасположения производства
12.2. Описание генерального плана предприятия
12.3. Характеристика главного корпуса обогатительной фабрики БКПРУ-2
12.4. Компоновка оборудования в цехе
13.1. Расчет производственной мощности ФОФ БКПРУ-2
13.5. Расчёт себестоимости КСL на БКПРУ-2
13.6. Сравнительный анализ себестоимости KCl
13.7. Расчет основных экономических показателей производства KCl
6.4. Обсуждение результатов
Из результатов парного двухвыборочного t-теста для средних значений по извлечению KCL в концентрат основной сильвиновой флотации следует, что дисперсии первой и второй выборок (
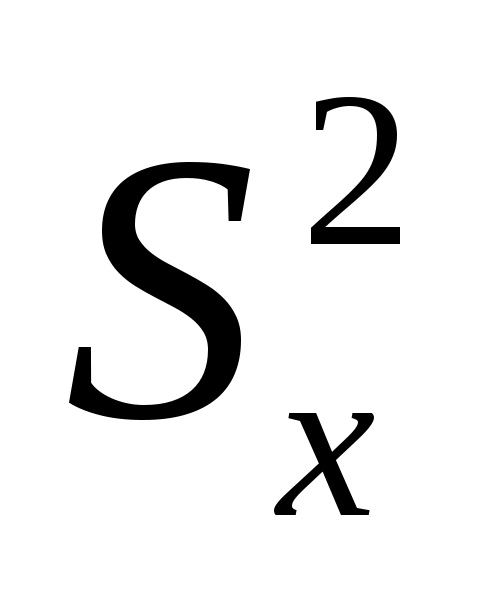
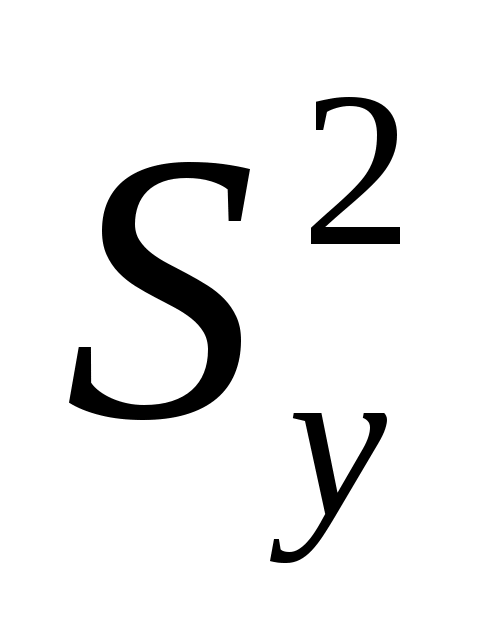
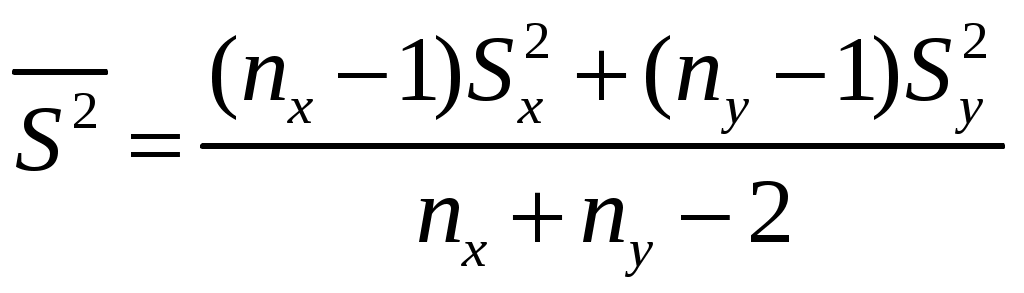
где
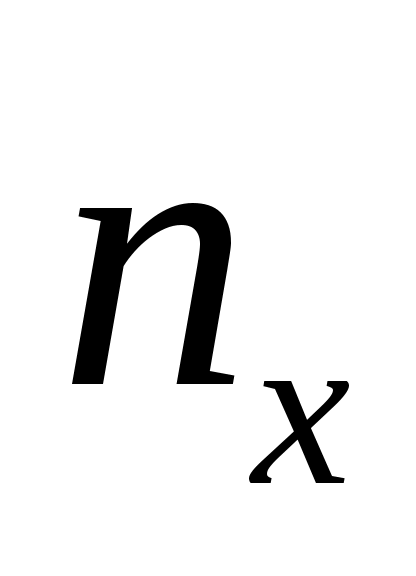
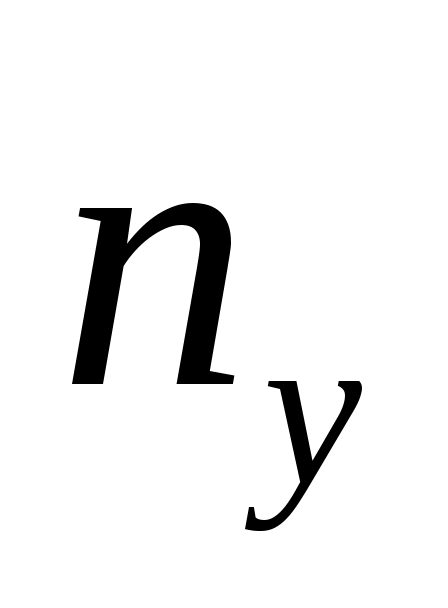
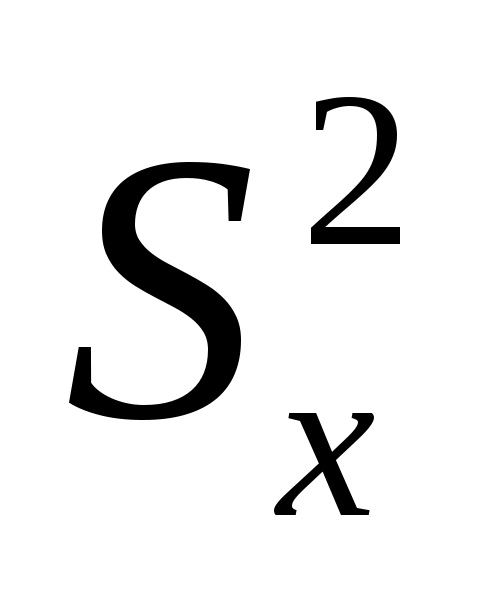
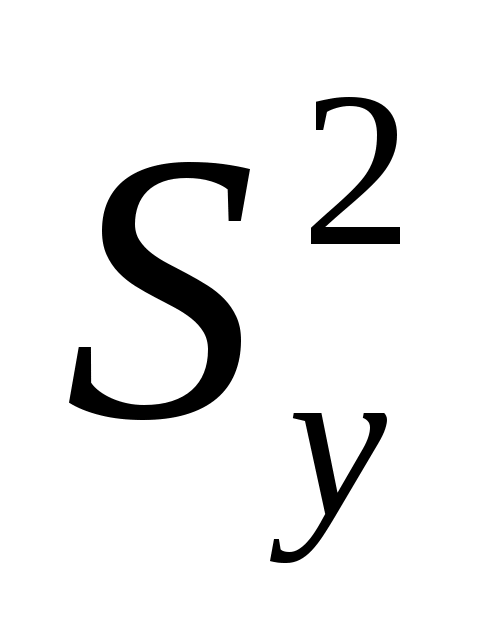



Так же найдём значение критерия Стьюдента
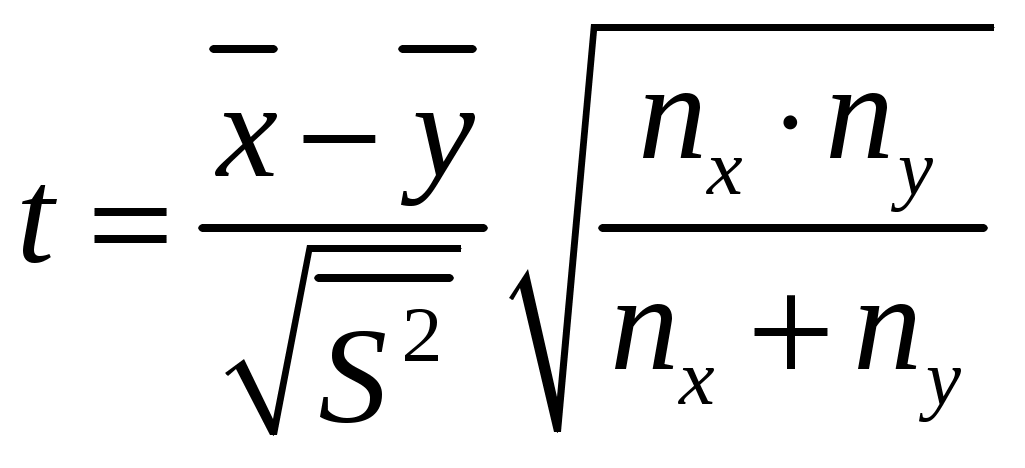
где
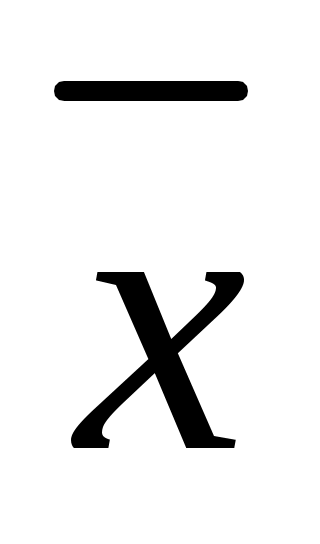
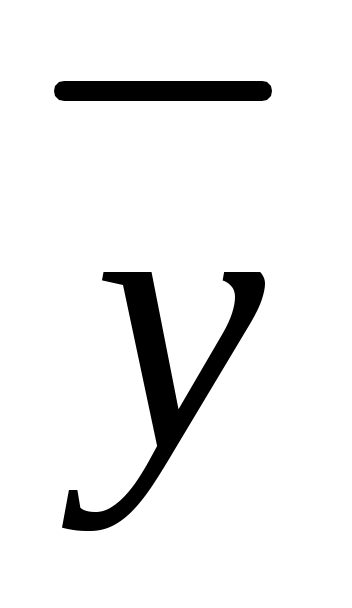
В нашем случае
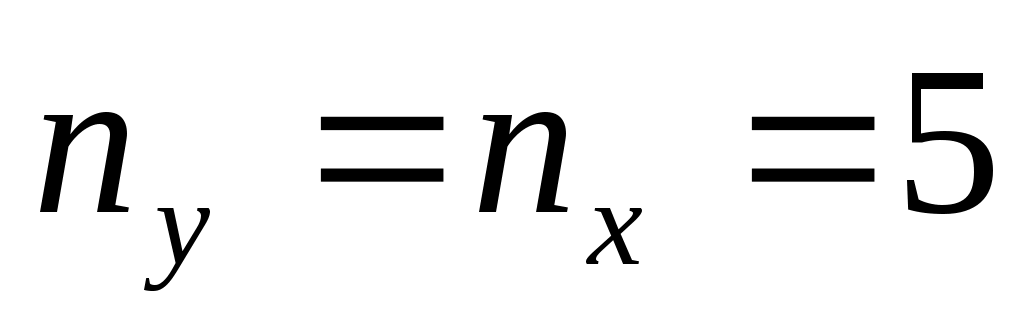
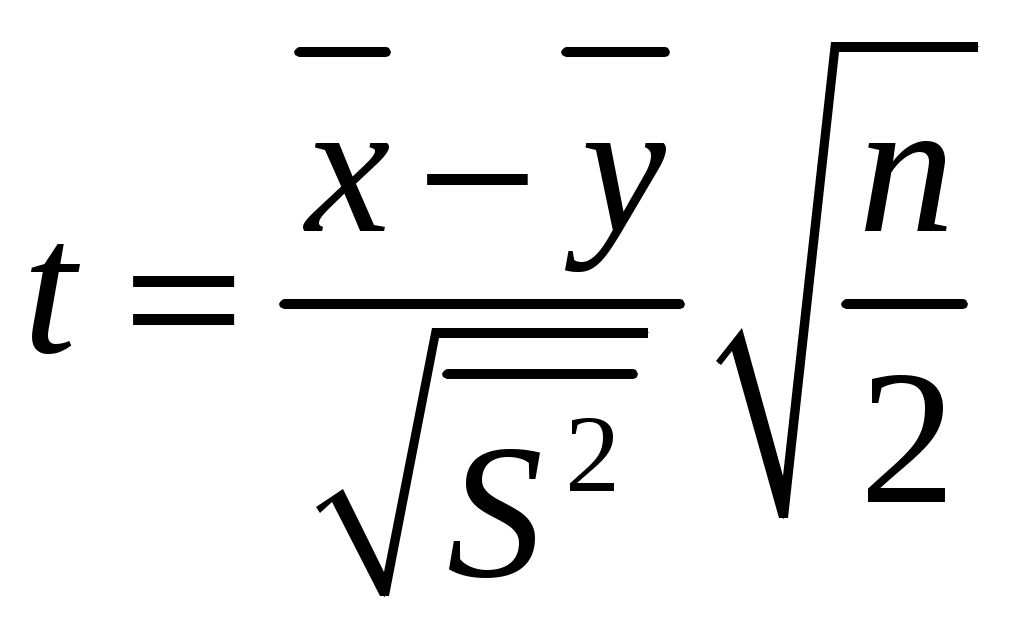

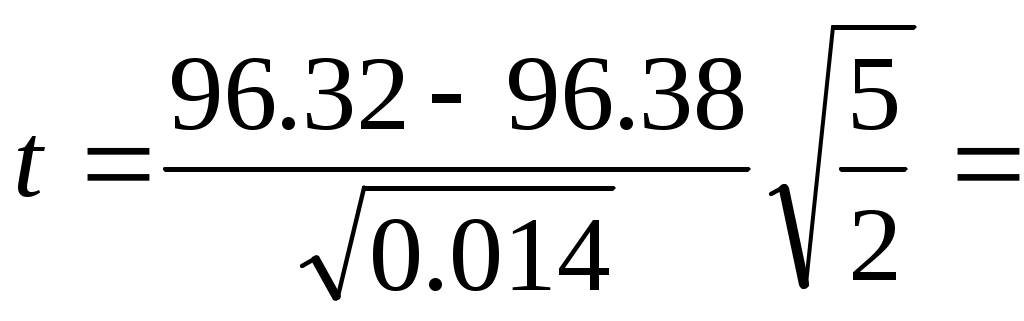
При f = 4 по таблице критерия Стьюдента находим
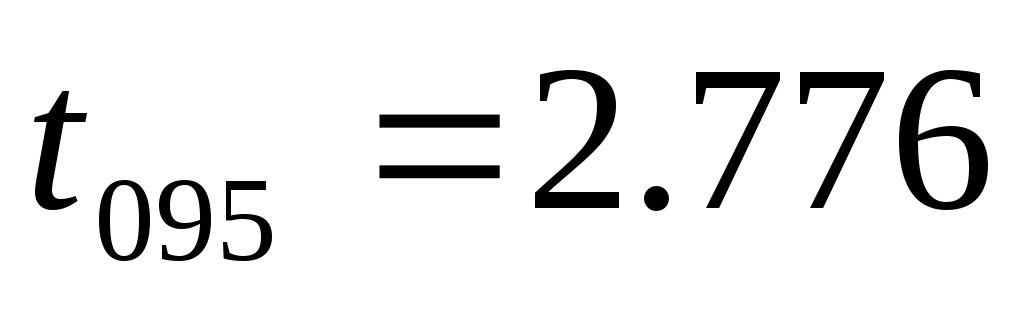
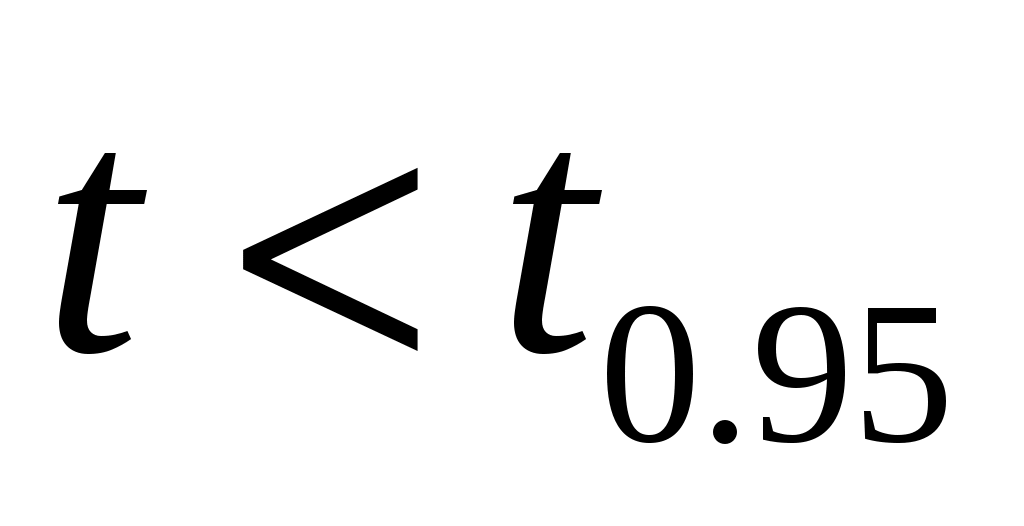
Таким образом, расхождение между извлечениями KCL в концентрат для обеих выборок можно считать не значимым.[11]
6.5. Вывод
Благодаря результатам, полученным при проведении парного двухвыборочного t-тест для средних значений, можно сделать вывод о возможности работы основной сильвиновой флотации на повышенной нагрузке на технологическую секцию используя комплексную эмульсию, так как извлечение KCL в концентрат при контрольном и испытуемом режимах не значимо отличаются друг от друга.
7. ВЫБОР И РАСЧЕТ ОБОРУДОВАНИЯ
Расчет и выбор оборудования произведем для варианта непрерывной работы фабрики 297 дней в году, 7113часов.
Большая часть оборудования главного корпуса поделена на четыре секции. Расчётпроизведем на одну технологическую секцию, так как оборудование по секциям идентично,нагрузки одинаковы.
Данные для расчета возьмем из качественно - количественной схемы.
7.1. Оборудование для флотации
7.1.1 Гидроциклоны
1. Первая стадия обесшламливания ( ГЦ-750)
Техническая характеристика:
- диаметр корпуса – 750мм;
- угол конусности – 20º;
- диаметр песковой насадки – 90-120 мм;
- диаметр сливного патрубка – 200 мм;
- давление на входе – 0,7÷0,9 кг/см2
Объемная производительность одного гидроциклона:
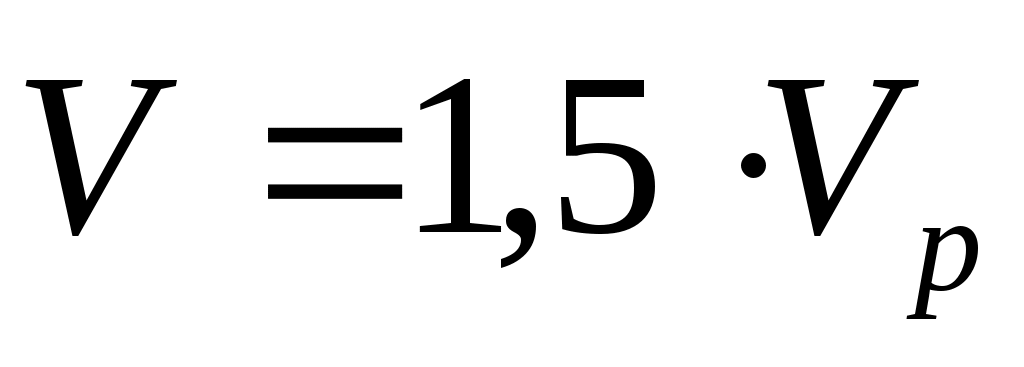
гдеVр – расчетная производительность гидроциклона,

где КД – поправка на диаметр
Кα – поправка на угол конусности (при α = 20º, где α – угол конусности, Кα = 1,0);
dn – эквивалентный диаметр питающего отверстия (для ГЦ – 750 dn =12÷20 см);
dc – диметр сливного патрубка, см;
P – давление на входе в гидроциклон, кг/см2



Количество гидроциклонов:
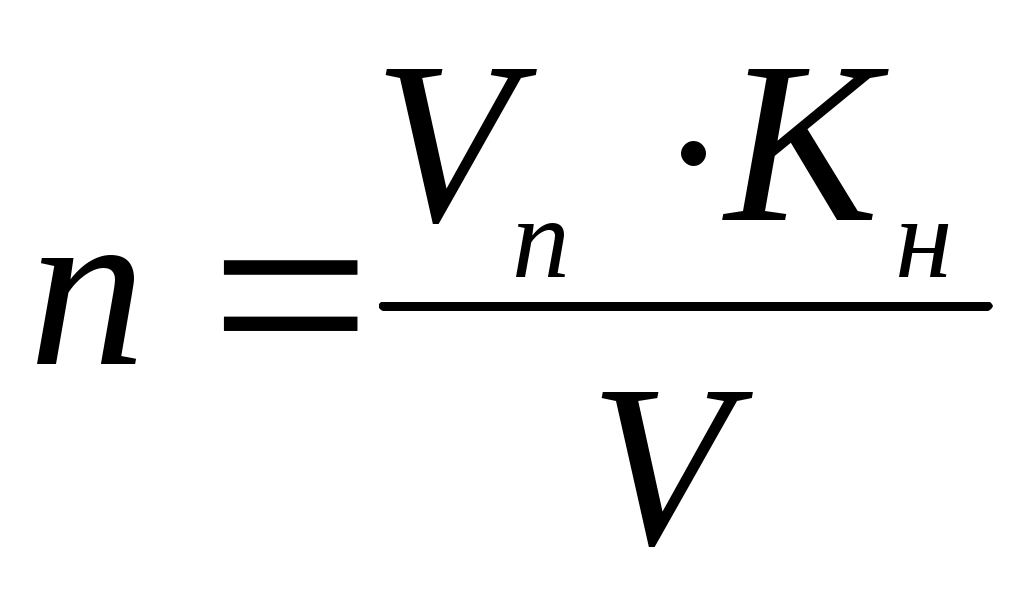
,
где Кн – коэффициент, учитывающий неравномерность подачи питания (1,15)

На I стадии обесшламливания для данного количества суспензии необходимы 3 гидроциклона (марки ГЦ-750). Фактически установлено 6 гидроциклонов (3 – в работе, 3 – в резерве).
2. Вторая стадия обесшламливания ( ГЦ-500)
Техническая характеристика:
- диаметр корпуса – 500 мм;
- угол конусности – 20º;
- диаметр песковой насадки – 70-75 мм;
- диаметр сливного патрубка – 120-150 мм;
- давление на входе – 0,8÷1,0 кг/см2
Расчетная производительность гидроциклона:

Поправка на диаметр

dn – эквивалентный диаметр питающего отверстия (для ГЦ-500 dn =6,5÷15 см);

Объемная производительность одного гидроциклона:

Количество гидроциклонов:
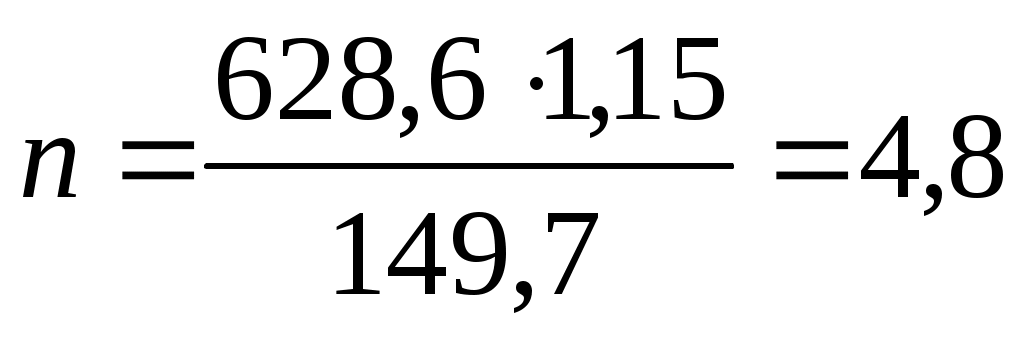
На II стадии обесшламливания для данного количества суспензии необходимы 5 гидроциклона (марки ГЦ-500). Фактически установлено 10 гидроциклонов (5 – в работе, 5 – в резерве).[9]
7.1.2 Флотомашины
Основным оборудованием отделения флотации являются флотомашины. В данное время на сильвинитовой обогатительной фабрике в основном используются флотомашины типа ФМ - 6,3 КС.
Технологический расчет любой флотомашины сводится к нахождению числа камер необходимых для вычислительной нагрузки.
Производительность машины определяется временем флотации, которое зависит от состава руды. Оно определяется экспериментально и обычно характеризуется временем пребывания суспензии во флотационной машине для получения необходимого извлечения.
Найдём число камер:
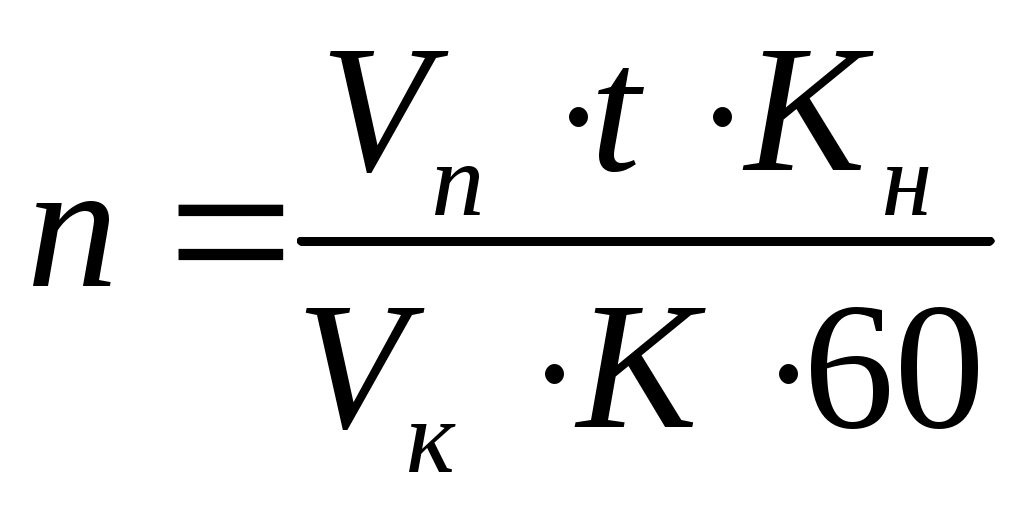
гдеVп – объем пульпы, поступающей во флотомашину, м3/ч;
Vк – геометрический объем камеры (6,3 м3);
К – коэффициент, учитывающий аэрированность суспензии (для шламовой флотации
К=0,7; для сильвиновой К=0,8);
t – продолжительность флотации, мин;
Кн – коэффициент, учитывающий неравномерность подачи питания (1,1÷1,15)
Для флотации используется флотомашина ФМ – 6,3 КСМ, которая имеет следующие технические характеристики:
- производительность камеры по твердому – 20–25 т/час;
- объем камеры – 6,3 м3;
- размеры камеры: длина – 2200 мм;
ширина – 2200 мм;
высота – 1200 мм;
- диаметр импеллера – 750 мм;
- число оборотов всасывающей камеры – 270 об/мин;
- прямоточной камеры – 240 об/мин;
- эл. двигатель импеллера: мощность – 30 кВт;
число оборотов – 730 об/мин;
- тип ремней – Г – 4000.
Флотационная механическая машина ФМ – 6,3 КСМ (Перемешивание и подача воздуха осуществляется импеллером) предназначена для обогащения сильвинитовой пульпы. Все камеры оборудованы горизонтальными решетками и циркуляционными карманами для создания направленного вверх потока пульпы через решетку. Машина состоит из всасывающей и прямоточных камер. Камера представляет собой сварную ванну прямоугольного сечения. Каждая камера имеет импеллер, приводимый во вращение электродвигателем. Внутри камеры помещается разъемная решетка из уголков с шириной щели 6 – 8 мм. Решетка устанавливается на высоте 450 мм от дна камеры и делит ее на два отделения: подрешетное – область аэрации и диспергации пульпы, надрешетное – минерализации и флотации минерала.
Аэрация пульпы осуществляется воздухом, засасываемым из атмосферы. Уровень пульпы в камерах регулируется шиберами. Гашение вращательного движения пульпы производится успокоителями, расположенными радиально вокруг блок импеллера в нижней части камеры, а также вертикальной перегородкой вдоль передней стенки камеры.
Для создания внутренней циркуляции пульпы в камере на передней стенке нижнего сливного порога имеется циркуляционная щель. Циркуляция пульпы осуществляется по циркуляционному карману и циркуляционной трубе. Пенный продукт пеногонами удаляется в желоб машины. Разгрузка производится в последней камере через разгрузочное устройство. Выпуск пульпы из машины во время ремонта и остановок осуществляется через дренажные клапана.[2;9]
Достоинства механической флотомашины:
-
Непрерывность процесса -
Оптимальная крупность воздушных пузырьков и их равномерное распределение по всему объему пульпы -
Полный перевод минерализованных пузырьков в пенный слой -
Быстрое и полное удаление минерализованной пены из машины -
Удобная и простая разгрузка хвостов -
Простая регулировка уровня пульпы